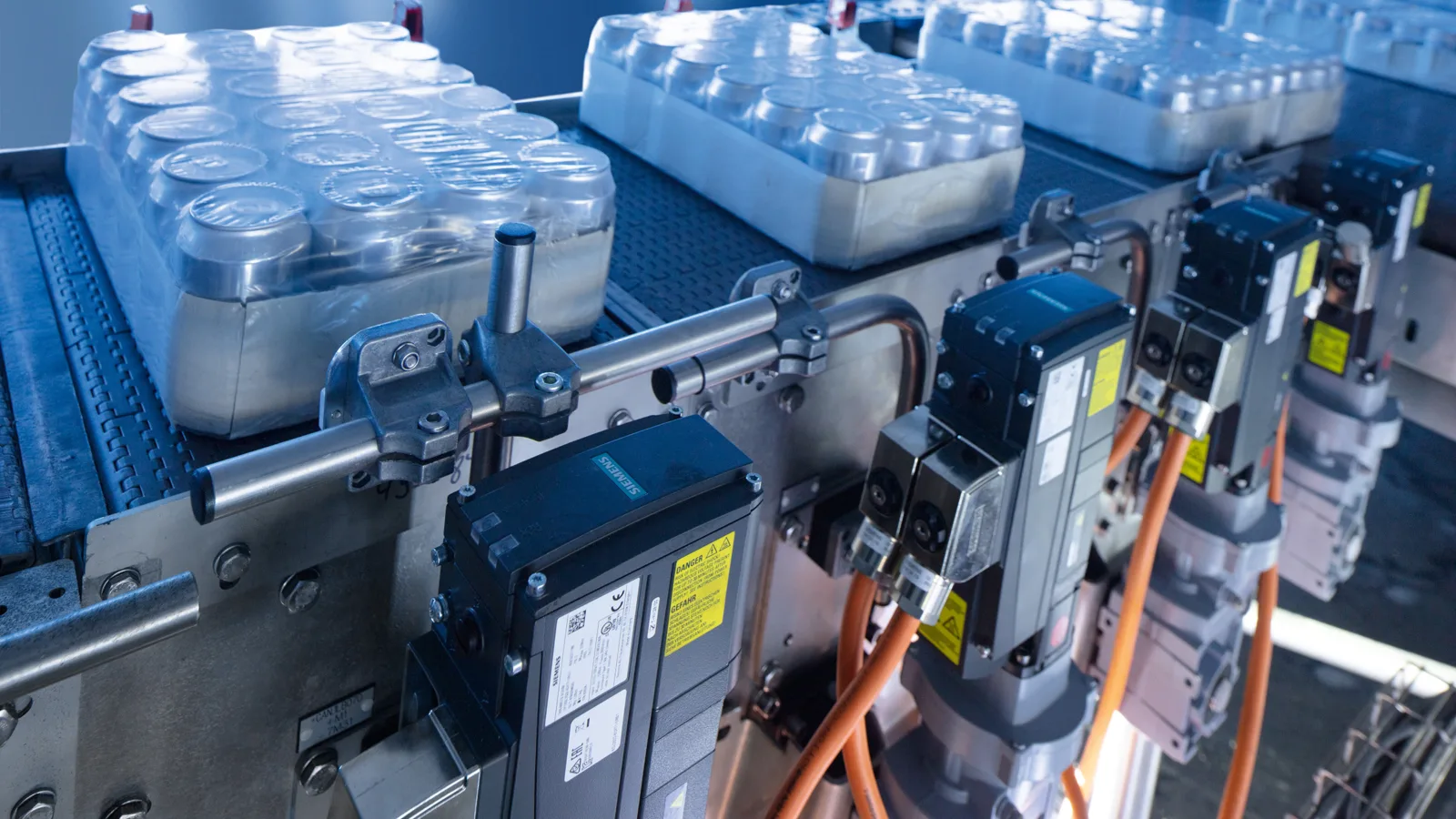
New quartet for the palletizer
More boost for your packaging – albeit with no accumulation pressure: thanks to a new palletizer that’s intelligently controlled by sensors beverage producers can now save time and manpower. They also benefit from high process reliability.
For two years now KHS’ InnoDry Block has provided beverage producers with a packaging and palletizing system that manages without guides on the pack conveyor. This is made possible by two special features: firstly, a flexible buffer behind the packaging machine that constantly adjusts its capacity to match the number of packs in circulation. Secondly, an optical sensor detects any misaligned packs on the conveyor without railings and sends this information to the robots which then adapt their gripping position accordingly. Without having to accumulate the packs, the robots then form these into precise layer patterns. This boosts pallet stability, ensuring that the packs arrive at the supermarket safe and sound.
Whereas to date each pack was aligned separately on the InnoDry Block, thanks to a new development by KHS’ palletizing experts in Worms the handling system can now also be used in the high-performance range. Pressureless container infeed without railings means that for the first time two or more packs can be handled and positioned simultaneously by the robot gripper arm. Christoph Wiesenack, palletizing product manager, describes the essential prerequisite here. “We’ve installed four extra, smooth conveyor belts in succession, each around 30 centimeters long, at the end of the main conveyors between the rubberized mat-top chain and grouping table. Their speed is controlled separately on the basis of information provided by an optical sensor. The camera works in all lighting conditions and with a full range of optical properties, colors or materials specific to the packaging or container. 3D information is generated which a pre-programmed algorithm converts into a control pulse. This accelerates or decelerates the packs, depending on what the robot system needs to complete its task. The packs are then either pushed closer together or pulled apart. In this way they’re conveyed at a perfect distance to one another and the robot can access them as the production process requires at that particular moment.”
»Doing away with the railings naturally makes format changeovers so much easier as we’ve eliminated a possible source of error.«
![]()
Palletizing product manager, KHS
Four belts, four speeds
The principle may seem simple, Wiesenack points out, yet programming the respective algorithms was quite an elaborate procedure. Even if he and his colleagues perhaps haven’t exactly reinvented the palletizer, he adds, laughing, Wiesenack believes that they can be proud of their achievements. What the team did was to completely rearrange certain elements already established in the industry so that these are now intelligently driven by dynamic algorithms from four servomotors.As is often the case with new developments, however, before the results proved positive the project members had to overcome a number of challenges and suffer several minor setbacks. “At first we made the general programming conditions too restrictive, assuming that in doing so we could make our work easier and still ensure a steady process. That was too optimistic.”
Everyone’s now extremely pleased with the result, however. Unlike on other standard systems the packs can now be fed to the palletizer without accumulation pressure. This gives beverage producers not one but two major advantages, explains Wiesenack. “On the one hand, the containers and packs are of course subjected to much less mechanical stress thanks to gentle handling without frequent acceleration and deceleration. On the other, we don’t need railings any more to stop the packs from falling off the side when they accumulate.” The second aspect in particular has caught the attention of prospective customers who now eagerly await the new product. “Doing away with the railings naturally makes format changeovers so much easier,” states Wiesenack. “If, on a conveyor 20 or 30 meters long, you have to adjust a railing every four meters or so, this takes up quite a lot of time. You have to release the clamping levers, adjust the guide rails and then retighten the levers.” The new setup saves between four and seven minutes for every ten meters of conveyor belt. It also eliminates a possible source of error, Wiesenack stresses. “If you don’t have to adjust anything, you can’t do anything wrong.”
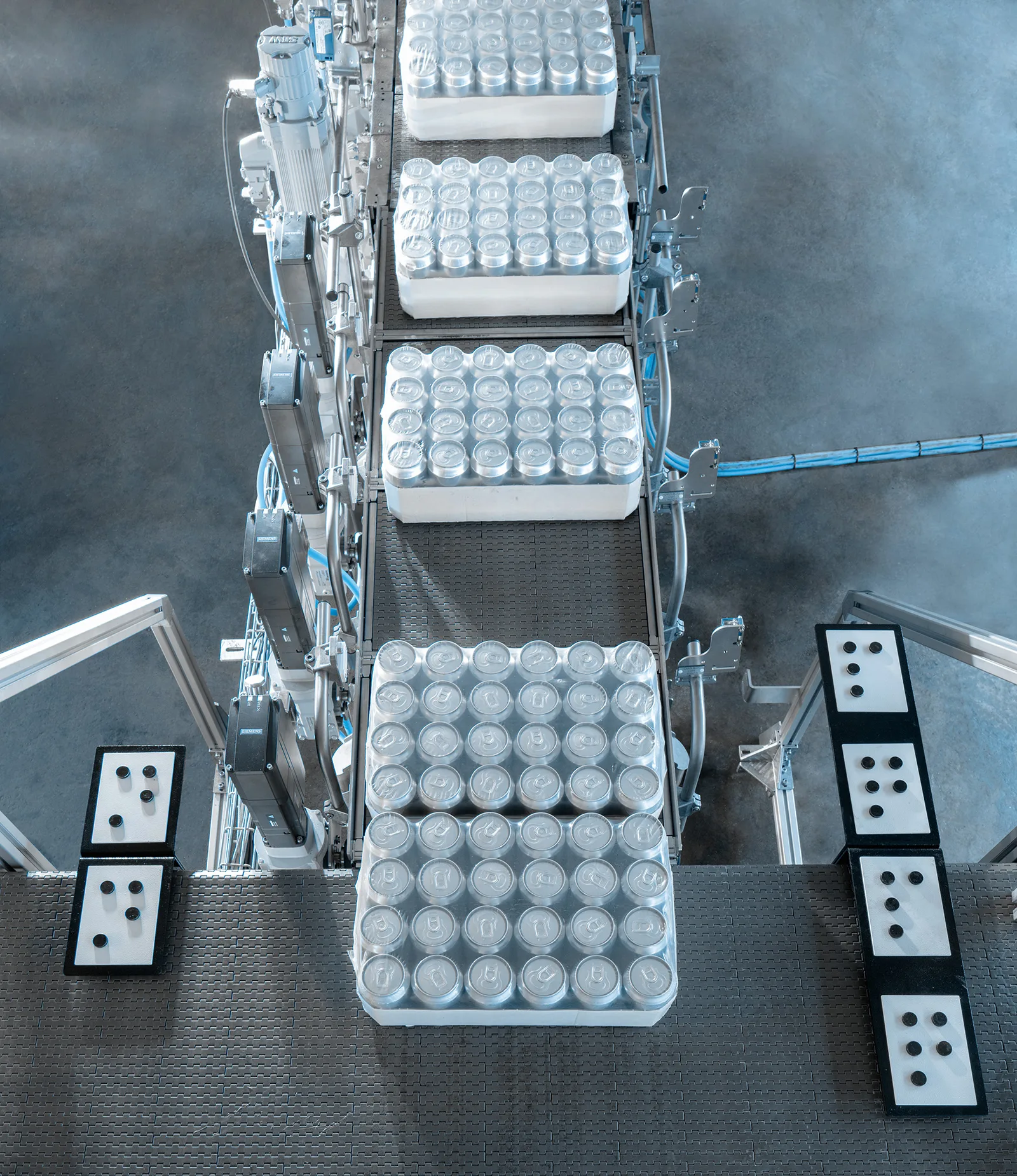
With the help of four short conveyor belts, each with a separate electronic control, the packs are brought into position for access by the robot.
For returnable and non-returnable containers
The new system could be of growing interest to customers who increasingly have to switch between pack infeed on one, two or three lanes, depending on the line capacity and pack size. Even though the new technology is primarily geared towards the palletizing of non-returnable packs and cartons – with all the many different formats and frequent format changeovers this entails – it can of course also be primed for use with returnable containers.
Wiesenack concludes happily, “Our new technology is based on the tried-and-tested InnoDry Block principle; in its redeveloped form, it’s now available for the high-capacity range for the very first time.”