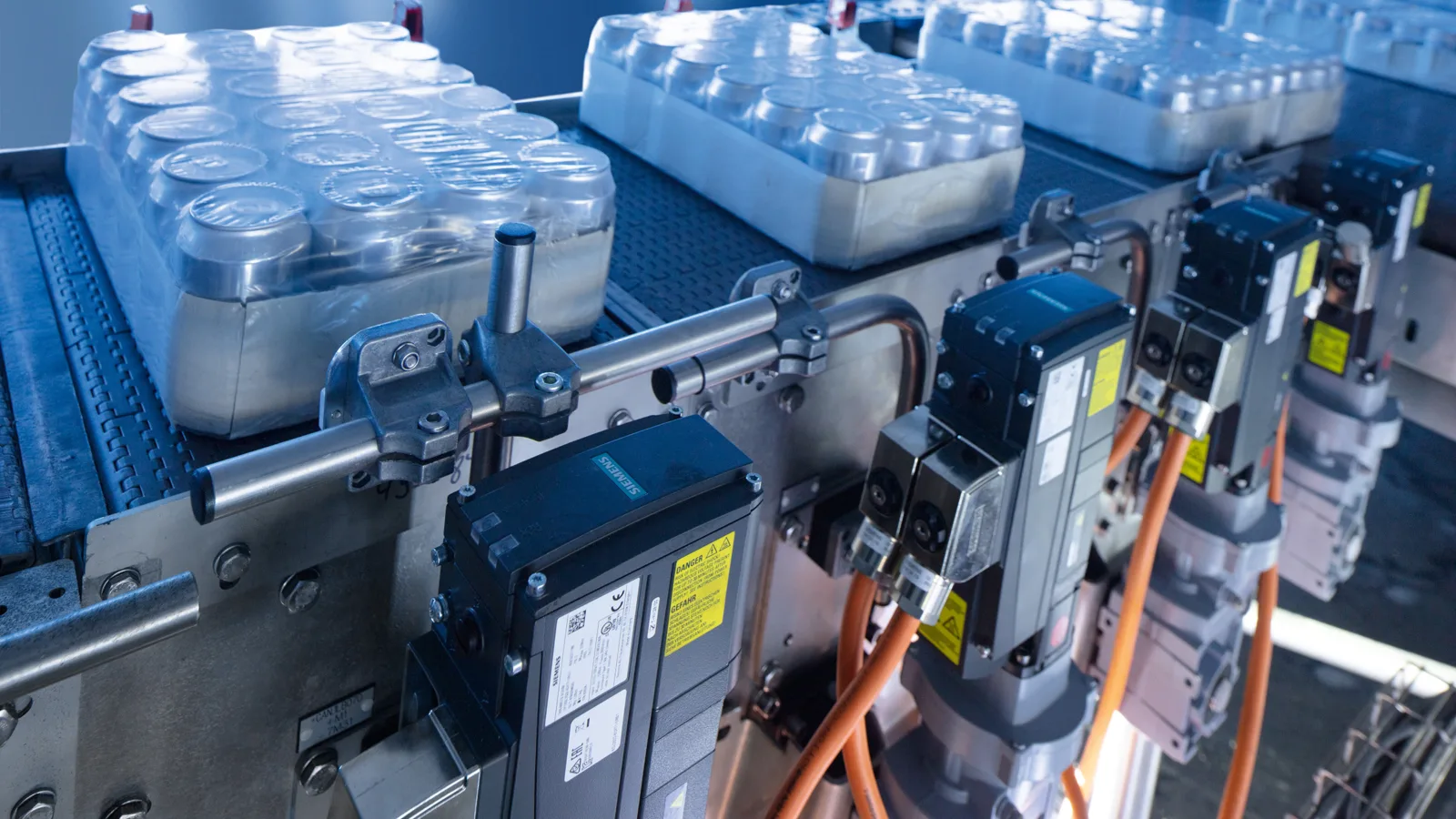
Der Quattro für den Palettierer
Mehr Schub in der Verpackung – aber ganz ohne Staudruck: Dank eines mit Hilfe von optischen Sensoren intelligent gesteuerten Palettierers sparen Getränkehersteller Zeit und Manpower. Obendrein werden sie noch mit hoher Prozesssicherheit belohnt.
Mit dem InnoDry Block von KHS steht seit zwei Jahren eine Pack- und Palettierlösung bereit, die ganz auf Führungen im Gebindetransport verzichtet. Möglich wird das zum einen durch einen flexiblen Puffer hinter der Verpackungsmaschine, der seine Größe laufend der Menge an Gebinden anpasst. Zum anderen erkennt ein optischer Sensor die im geländerlosen Transport fehlerhaft ausgerichteten Gebinde und stellt den Robotern diese Information zur Verfügung. Die Roboter passen daraufhin ihre Zugriffsposition entsprechend an. Ohne die Pakete aufstauen zu müssen, stellen sie die Gebinde zu präzisen Lagenbildern zusammen. Das erhöht die Stabilität der Palette, sodass die Packs sicher im Supermarkt ankommen.
Erfolgte die Ausrichtung im InnoDry Block bisher für jedes Pack einzeln, kann das Manipulationssystem dank einer Neuentwicklung der KHS-Palettierexperten aus Worms jetzt auch im Hochleistungsbereich eingesetzt werden: Bei der drucklosen Gebindezuführung ohne Geländer können erstmals zwei oder mehr Gebinde gleichzeitig vom Robotergreifarm manipuliert und platziert werden. Christoph Wiesenack, Product Manager Palletizing, beschreibt, was dafür die wichtigste Voraussetzung ist: „Wir haben am Ende der Transporteure zusätzlich vier aufeinanderfolgende, jeweils nur rund 30 Zentimeter lange, glatte Förderbänder zwischen gummierter Mattenkette und Gruppiertisch eingebaut. Ihre Geschwindigkeit wird individuell auf Basis der Informationen gesteuert, die ein optischer Sensor bereitstellt. Die Kamera funktioniert bei jeder Art von Lichtverhältnissen und bei unterschiedlichsten optischen Eigenschaften, Farben oder Materialien der Verpackung beziehungsweise des Behälters. Es werden 3D-Informationen erstellt, die ein zuvor programmierter Algorithmus in einen Steuerimpuls umwandelt. Dieser beschleunigt oder verlangsamt die Gebinde – je nachdem, wie es das Robotersystem zur Erfüllung seiner Aufgabe benötigt. Dadurch werden die Packs entweder zusammengeschoben oder auseinandergezogen. So werden sie in einem optimalen Abstand zueinander transportiert und der Roboter kann zugreifen, wie es der Produktionsprozess gerade erfordert.”
»Der Verzicht auf Geländer erleichtert den Formatwechsel ganz ungemein, weil wir eine potenzielle Fehlerquelle ausgeschaltet haben.«
![]()
Product Manager Palletizing, KHS
Vier Bänder, vier Geschwindigkeiten
Das Prinzip mag einfach sein, betont Wiesenack, die Programmierung der entsprechenden Algorithmen war jedoch mit einigem Aufwand verbunden. Auch wenn er und seine Kollegen damit die Palettierung vielleicht nicht gerade neu erfunden hätten, wie er lachend einräumt, findet Wiesenack, dass sie auf ihre Leistung stolz sein dürfen. In der Industrie bereits bestehende Elemente hat das Team so in einen ganz neuen Zusammenhang gesetzt, dass diese jetzt durch dynamische Algorithmen von vier Servomotoren intelligent angetrieben werden.Der Weg zu diesem Ergebnis war dabei, wie es bei Neuentwicklungen eben oft üblich ist, nicht frei von Herausforderungen und kleineren Rückschlägen: „Bei der Programmierung haben wir davon ausgehend, dass wir uns die Arbeit erleichtern und trotzdem einen stabilen Lauf sicherstellen können, die Randbedingungen zunächst zu stark eingeschränkt. Das war zu optimistisch.“
Mit dem Resultat sind nun aber alle hochzufrieden. Anders als bei sonst üblichen Anlagen können die Gebinde jetzt staudrucklos dem Palettierer zugeführt werden. Das bietet gleich zwei große Vorteile für Getränkehersteller, wie Wiesenack erklärt: „Einerseits sind die Behälter und Gebinde durch die schonende Behandlung ohne häufiges Beschleunigen und Abbremsen natürlich deutlich weniger mechanischer Beanspruchung ausgesetzt. Andererseits brauchen wir keine Geländer mehr, die die Gebinde beim Aufstauen vor dem seitlichen Herabfallen schützen müssen.“ Gerade der zweite Aspekt lässt Kunden aufhorchen und sorgt dafür, dass sie das neue Produkt mit Spannung erwarten: „Der Verzicht auf Geländer erleichtert den Formatwechsel natürlich ganz ungemein“, stellt Wiesenack fest. „Wenn man bei einem Transporteur von 20 oder 30 Meter Länge etwa alle vier Meter ein Geländer verstellen muss, nimmt das schon einige Zeit in Anspruch. Man muss Klemmhebel lösen, die Führungsschienen justieren und die Hebel wieder feststellen.“ Das spart je zehn Meter Transportstrecke zwischen rund vier und sieben Minuten Zeit ein. Darüber hinaus wird eine potenzielle Fehlerquelle ausgeschaltet, wie Wiesenack betont: „Wenn man nichts verstellen muss, kann man auch nichts falsch machen.“
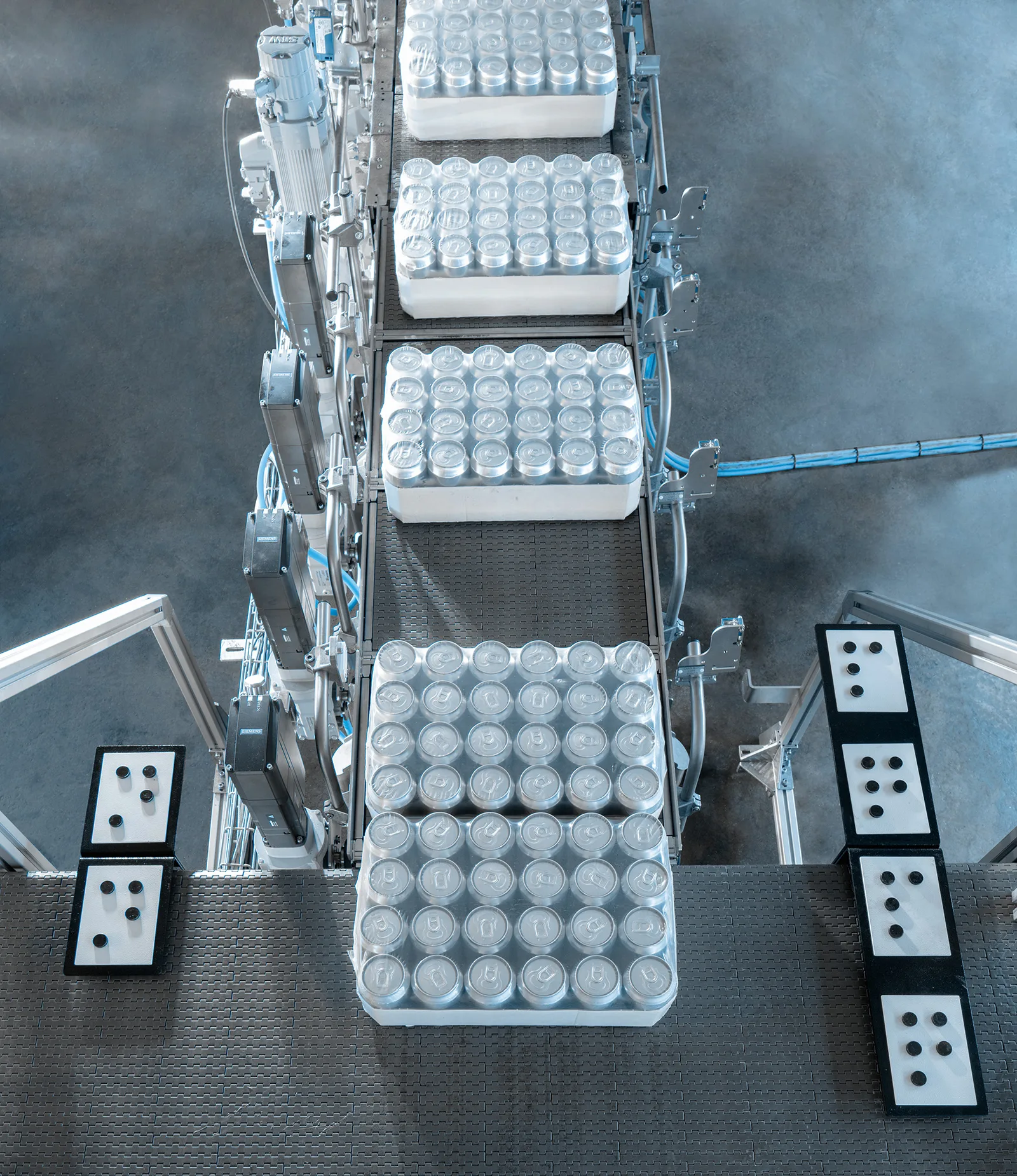
Mit Hilfe von vier kurzen, einzeln elektronisch gesteuerten Förderbändern werden Packs in den richtigen Abstand für den Zugriff durch den Roboter gebracht.
Für Einweg und Mehrweg
Zunehmend interessanter dürfte das neue System für Kunden werden, die – abhängig von der Linienleistung und der Gebindegröße – immer häufiger im Wechsel eine ein-, zwei- oder auch dreibahnige Gebindezuführung einsetzen. Und auch wenn die neue Technologie in erster Linie auf die Einwegpalettierung von Packs und Kartons zielt – hier gibt es viele verschiedene Formate und entsprechend häufige Formatwechsel – soll sie selbstverständlich auch im Mehrwegbereich eingesetzt werden können.
Zusammenfassend stellt Wiesenack zufrieden fest: „Die neue Technik basiert auf dem bewährten Prinzip des InnoDry Blocks und macht dieses – in weiterentwickelter Form – erstmals auch für den Hochleistungsbereich verfügbar.“