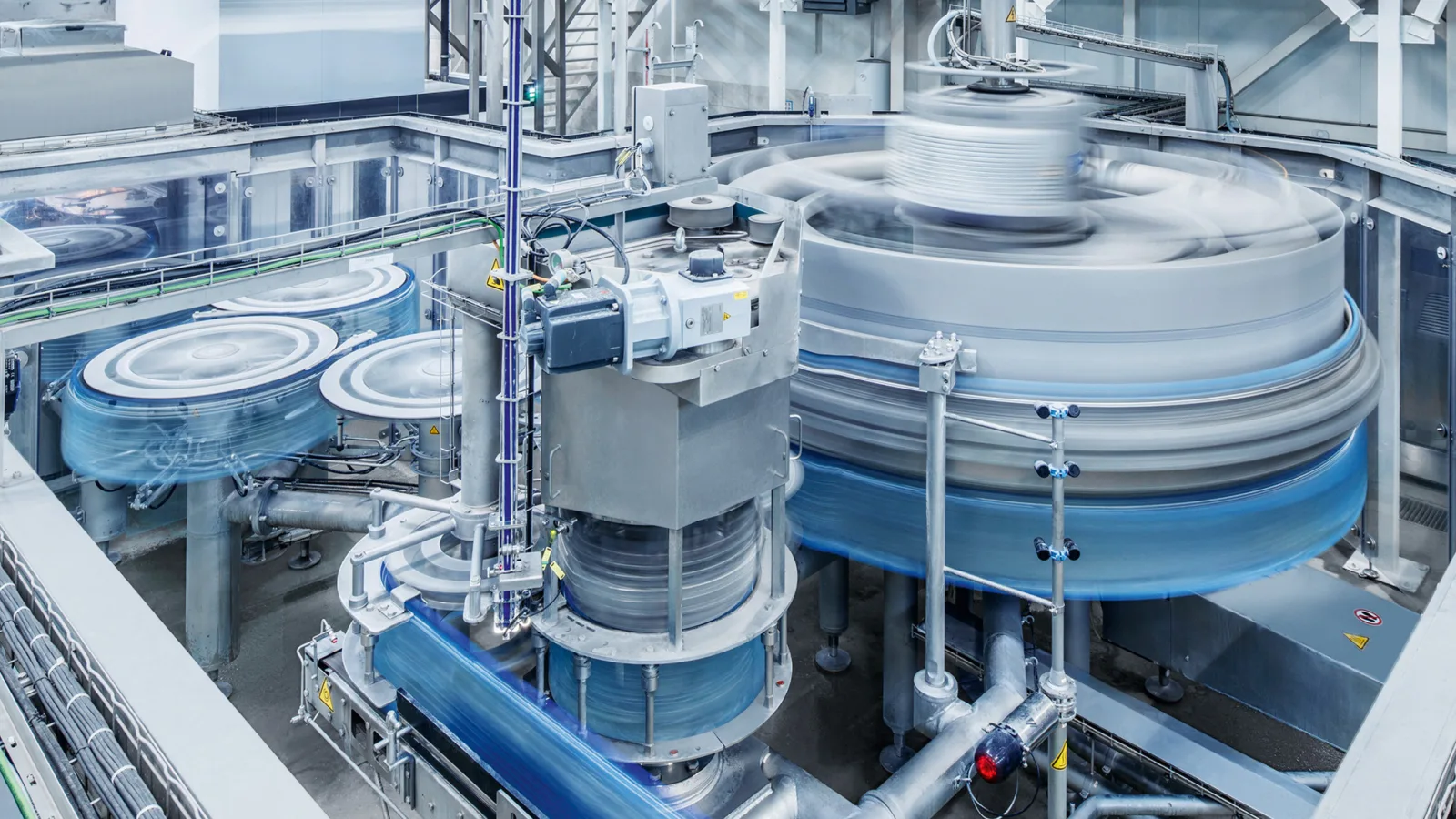
Keeping it calm
If, at high filling capacities, beverages slosh out of the bottle, levels of efficiency and hygiene suffer. KHS prevents this by drawing up extensive calculations.
If beverage filling is to be safe with little loss, physics comes into play: given the rotation speed and change in direction, especially at the transition from the transfer star to the closure system, high levels of centrifugal force act on the content of the containers. This can cause liquid to slosh out of the bottle. This may only comprise a few drops of spillage at a time – but with up to 90,000 fills an hour, the amount of product lost soon mounts up. Another aspect is hygiene. It’s not hard to imagine that on the one hand, sloshed sugary beverages soil container necks and closures, with mold even being formed in some cases. On the other, the machine is also contaminated. This in turn increases the cleaning requirements and takes up valuable production time.
“Ever higher filling outputs mean that we also have to take liquid sloshing into account when designing the machine.”
development engineer, KHS
![]()
KHS development engineer Dominik Weirich has been carrying out fluid dynamic measurements in Bad Kreuznach, Germany, since 2013.
Two groups of parameters
In order to counter this, Dominik Weirich has been drawing up CFD1 calculations since 2013. “Ever higher filling outputs mean that the technology’s reaching its physical limits, so that we also have to take liquid sloshing into account when designing the machine,” says the KHS development engineer. Data collected from the simulations he carries out form the basis here. “First, we take a look at the geometric parameters of the beverage containers themselves: here, we investigate the impact the bottle shape, fill height and neck diameter have. This is done in close consultation with our Bottles & Shapes experts, especially in the course of new line projects, when changes are made to the geometry or the bottle weight is reduced, for example. Second, we have the physical parameters of the machines. These depend on the capacity, machine pitch and diameter of the stars and can all be relatively easily adjusted. Adapting the containers, however, is usually an iterative and more extensive process.”
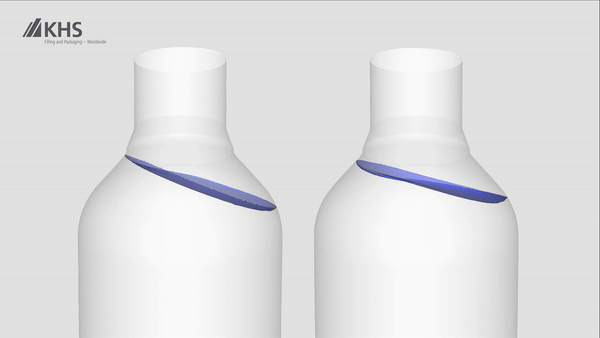
The comparison shows how the amount of product loss is reduced by optimizations based on extensive calculations (in the animation on the right).
Increasing number of simulations
As a rule, it can be said that the larger the product surface and the closer the beverage is to the bottle mouth, the more likely the liquid is to slosh. This interaction of the various factors requires calculations to be made that are then included in both the design engineering and the offers for the machinery. Weirich has already performed about 850 of these simulations – with this number continuing to rise.
Summary
Your benefits in brief
Reliable performance, quick commissioning | |
Optimum bottle geometry | |
Low microbiological risk in the filling of sugary beverages | |
Low product loss, consistent filling volumes, constant quality | |
No sticking of screw caps, no product in the thread | |
Low contamination of the bottle guides, less cleaning effort, higher availability |
Any further questions?
1. CFD = Computational Fluid Dynamics or the calculation and simulation of gas and liquid flows.