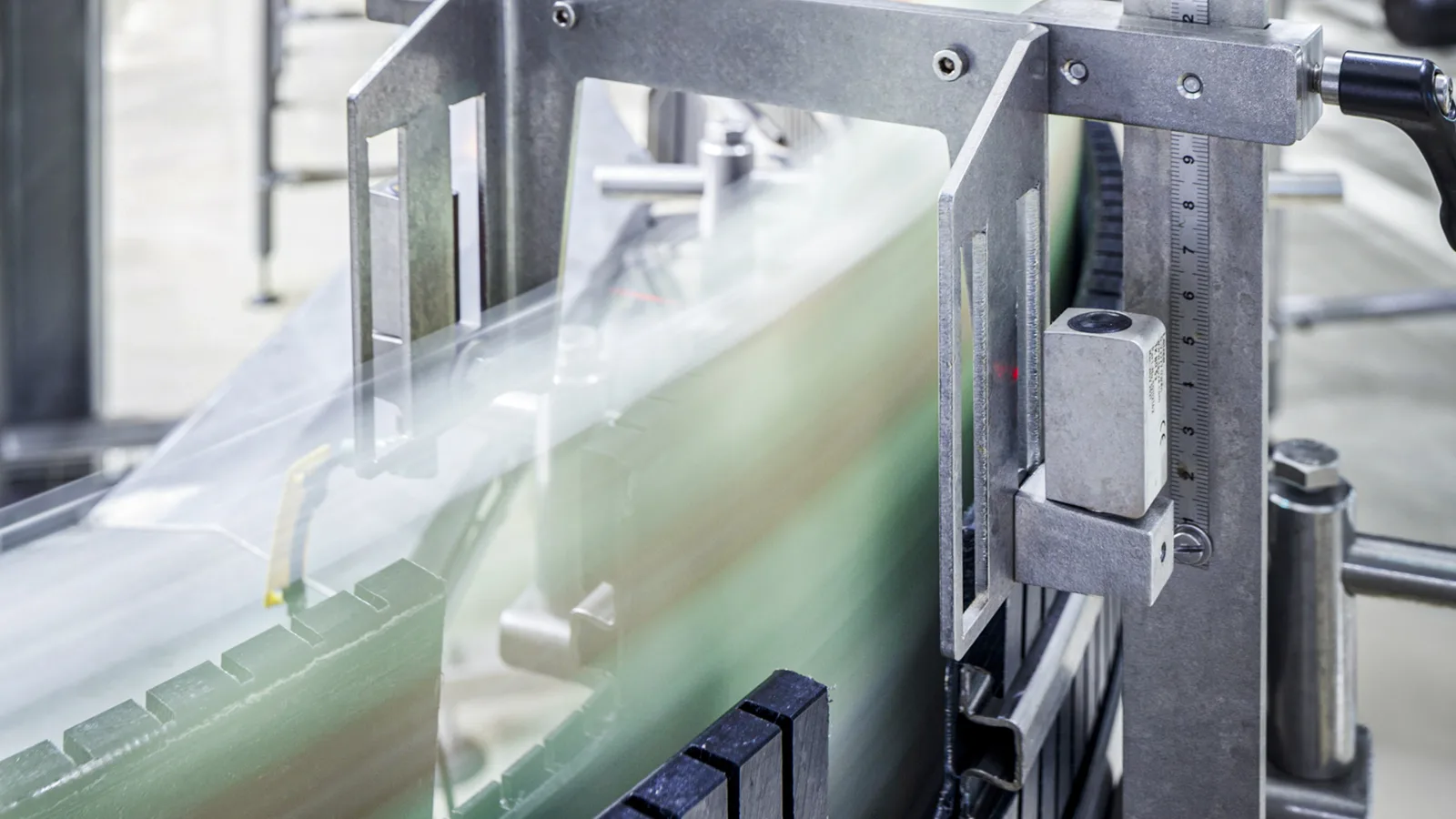
… it’s better to check!
With continuously further developed and modernized KHS inspection technology, bottlers benefit from increased efficiency, greater production reliability and cost-effective integration into existing lines.
The KHS Innocheck product family stands for effective inspection technology at attractive prices. It enables best product quality, provides operators with extensive information and can be flexibly retrofitted on existing equipment at any time. KHS offers a broad portfolio specifically tailored to the canning segment that covers the entire line.
One example in this product range is the intelligent Innocheck MMS machine management system. It localizes faulty filling valves and closure elements and evaluates these. “The Innocheck MMS allows entire parameters to be precisely read out,” explains Henrik Kahrmann, who is responsible for labeling and inspection technology product support at KHS. “Through the evaluation thereof, canners and bottlers can trace faulty fillings back to individual valves and intervene in good time.”
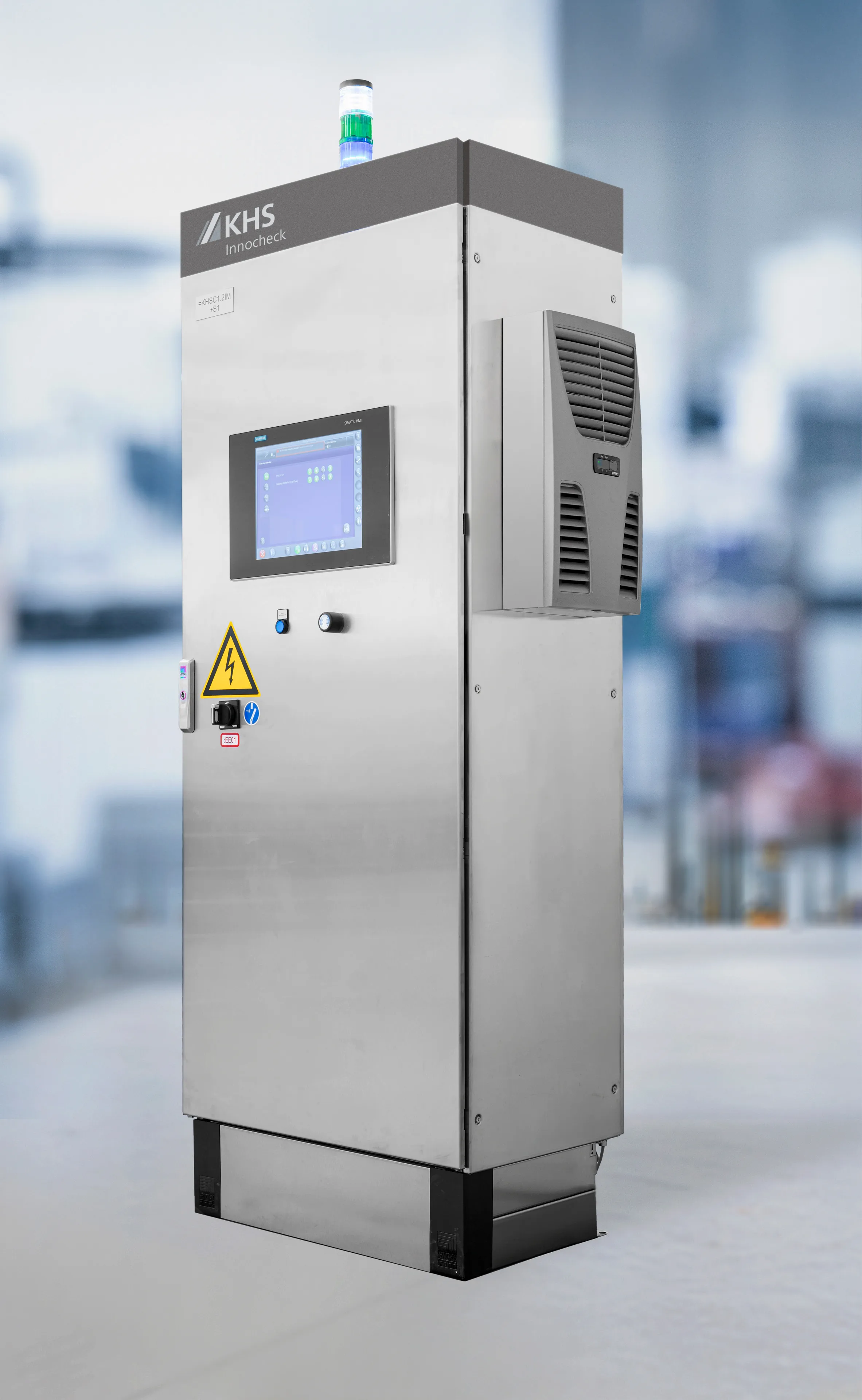
The Innocheck CUB control unit big is a central controller that monitors and operates all control systems and enables the MMS machine management system software to be run.
Perfect in the high-capacity range
With the help of cutting-edge cameras, the Innocheck ECI empty can inspector identifies the tiniest foreign bodies and damage in the millimeter range. The system quickly and thoroughly examines the inner wall, base and top edge of the can, with the machine capable of processing up to 135,000 cans per hour.
“The use of our inspection technology noticeably reduces downtime while increasing line efficiency.”
![]()
Labeling and Inspection Technology Product Support at KHS
Soiled or defective containers are correctly rejected. “By doing so, the system prevents faulty containers from reaching the filler or seamer and causing problems that hold up the entire production process,” states Kahrmann.
One new addition to the portfolio is the Innocheck ECI+ that additionally monitors the inner shoulder area of the empty can, previously a blind spot in inspection. It also takes up so little installation space that it can be easily integrated into existing machinery.
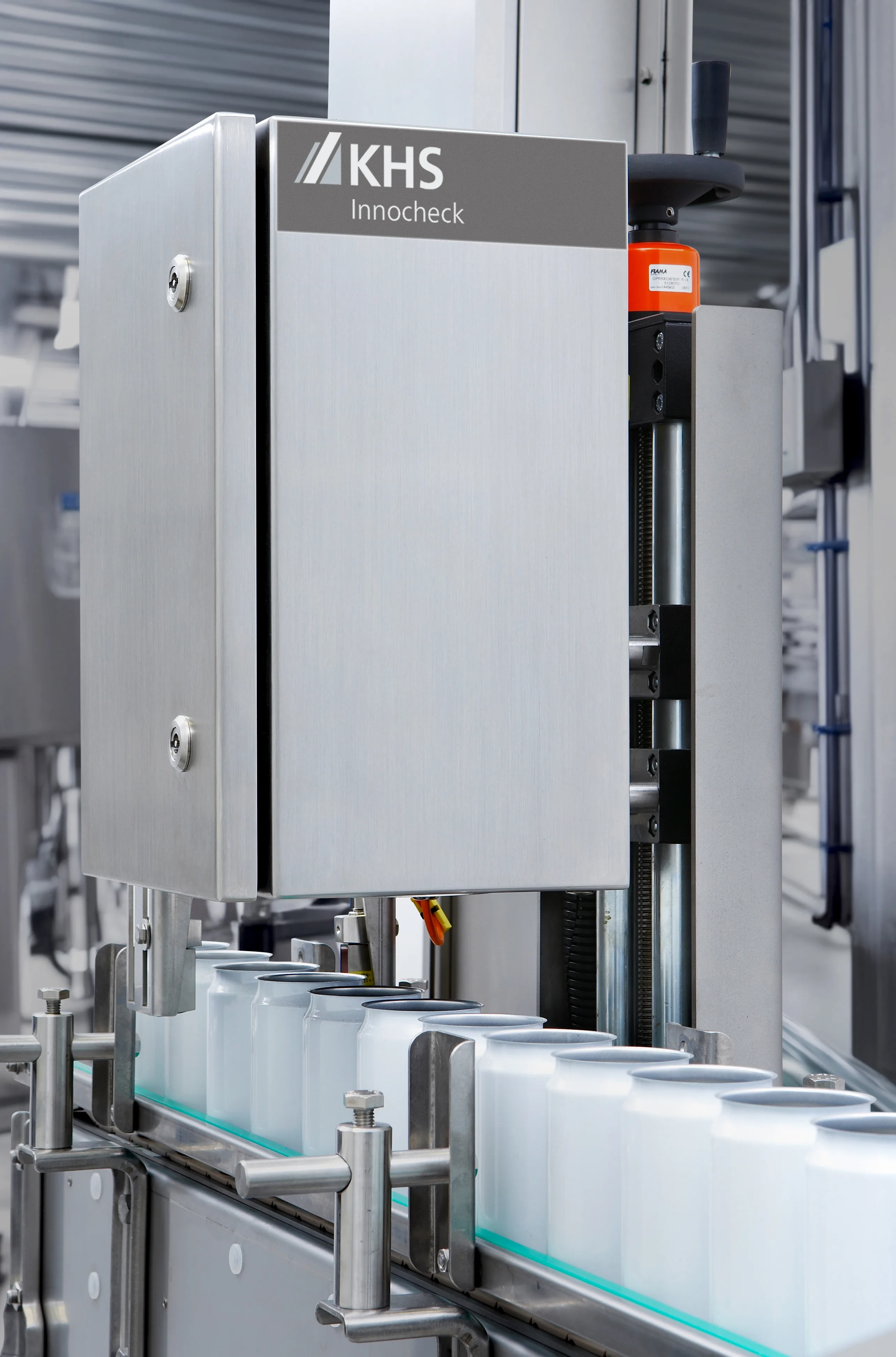
Cutting-edge cameras on the Innocheck ECI thoroughly examine empty cans for foreign bodies and damage.
Precise fill height control
Moreover, KHS has expanded its range of fill height control equipment. To date, the modular Innocheck FHC fill height control needed two systems – one to check for overfilling and a second to scan for underfilling using X-rays. “Up to now, we could only make spot checks of the fill height,” says Kahrmann. “Our new spatial-resolution system instead measures an entire fill height area using just one unit. This simplifies inspection and gives us more precise results.”

The new, spatial-resolution system Innocheck FHC not only detects over- and underfilling; it also provides absolute values that reveal whether filling valves may be starting to show a drop in performance.
Another key advantage, according to Kahrmann, is that “besides information as to whether the can is over- or underfilled, our new FHC system also gives us the fill height as an absolute value. This is calculated by an algorithm that excludes interference such as sloshing liquids. This allows our customers to see whether their filling valves may be starting to show a drop in performance.” This makes it possible to maintain the individual valves affected in good time.
KHS inspection technology also includes the Innocheck CIC-R code inspection can reader. This system examines printing and production codes on the can base with the help of artificial intelligence. Incomplete or incorrect codes are immediately signaled. Affected containers can thus be ejected before they are processed further.