
Bien está lo que bien acaba
Empleando tecnología punta de KHS, una subsidiaria de AB InBev en Mozambique está construyendo la fábrica de cerveza más grande y más moderna de África. El núcleo de la planta es la línea de vidrio retornable más rápida del continente, cuya instalación y puesta en marcha exitosas no pudieron impedir ni un huracán catastrófico ni la propagación de la pandemia de Coronavirus.
En gran parte de África la cerveza se ha elaborado durante mucho tiempo a partir de la mandioca de cultivo doméstico. Elaborada de forma casera, adopta características muy diferentes, en su mayoría es turbia, sin espuma digna de mención y de una consistencia espesa, casi como muesli líquido y, por lo tanto, no goza de buena acogida entre la la mayoría de la gente. La primera fábrica de cerveza en asumir el desafío de hacer una cerveza sabrosa a partir de la planta Cassava, también conocida como mandioca, es Cervejas de Moçambique, CDM para abreviar: En 2011, bajo la marca Impala la empresa lanza al mercado una de las primeras cervezas comerciales de mandioca en África. En lugar de malta de trigo o de cebada, un 70% del almidón empleado procede de los tubérculos. Después de un largo proceso de desarrollo, finalmente se obtiene una bebida, que en un vaso se presenta de color amarillo afrutado y ligeramente turbio. Con su corona de espuma blanca, parece una cerveza lager normal y sorprende con su sabor fresco.
Para CDM, Impala es un éxito en varios sentidos: Mediante la compra de materias primas regionales, la fábrica de cerveza asegura la existencia económica de los pequeños agricultores locales y crea numerosos puestos de trabajo en la agricultura. El estado honra este compromiso, así como el hecho de que la cerveza hecha profesionalmente toma el lugar de las producciones caseras de sus ciudadanos, que son peligrosas para la salud: Gracias a una menor carga impositiva, la nueva cerveza puede ofrecerse a alrededor de un 30% por debajo del precio normal. Esto ayuda a que Impala sea un gran éxito con más de un millón de botellas vendidas cada año, copiadas hace mucho tiempo en varios países africanos y por varias fábricas de cerveza.
Junto a su fuerza innovadora, CDM también apuesta a las tradiciones. Privatizada en 2005 como parte de la reestructuración de economía de mercado del país anteriormente gobernado por socialistas, la compañía ahora combina en su cartera todas las marcas de cerveza consolidadas desde hace mucho tiempo en Mozambique. Entre ellas se cuenta sobre todo la cerveza 2M elaborada desde 1950, cuyo nombre es un recuerdo del presidente francés Patrice de Mac-Mahon: En 1875 medió en el conflicto entre Portugal e Inglaterra por la actual capital Maputo, y en consecuencia es venerado en el país del sudoeste africano. Una de las mejores marcas continúa siendo la cerveza Laurentina, que fue la primera que se elaboró en Mozambique en 1932 y ha recibido numerosos premios. Con una facturación de alrededor de 300 millones de euros (2021), la fábrica de cerveza, que ahora es de propiedad mayoritaria del grupo AB InBev, es, con diferencia, el mayor productor nacional de cerveza y líder del mercado.
Nuevo emplazamiento con potencial
Esta condición es posible gracias a la estrategia consecuente de crecimiento constante y a un aumento continuo de la capacidad. Recién en 2010 se inauguró una tercera fábrica en Nampula, en el norte del país, que se suma a los emplazamientos anteriores en la capital Maputo y en Beira, más al norte en la costa. Apenas ocho años después, se colocó la primera piedra de otro proyecto greenfield en Marracuene, a pocos kilómetros de las puertas de Maputo. Aquí se comenzará con una producción de 1,6 millones de hectolitros por año. En vista de una población en rápido crecimiento y al aumento de la demanda de cerveza de alta calidad, aún no se ha llegado al final del rápido desarrollo: La planta de producción fue diseñada de tal forma que, en los próximos años, pueda ampliarse sin problemas a una capacidad de 6 millones de hectolitros.
El núcleo de la nueva planta es una línea de vidrio retornable de KHS, que puede envasar por hora hasta 80.000 botellas de 550 mililitros, que es el formato con el cual se alcanzará hasta un 95% de la facturación (ver el recuadro “Tecnología punta en Mozambique”). Para el continente africano, esta capacidad de línea es extremadamente alta, explica Tobias Zeimentz, gerente de cuentas clave de KHS con responsabilidad global para el cliente AB InBev: “En esta región es poco frecuente el procesamiento de más de 40.000 botellas por hora”.
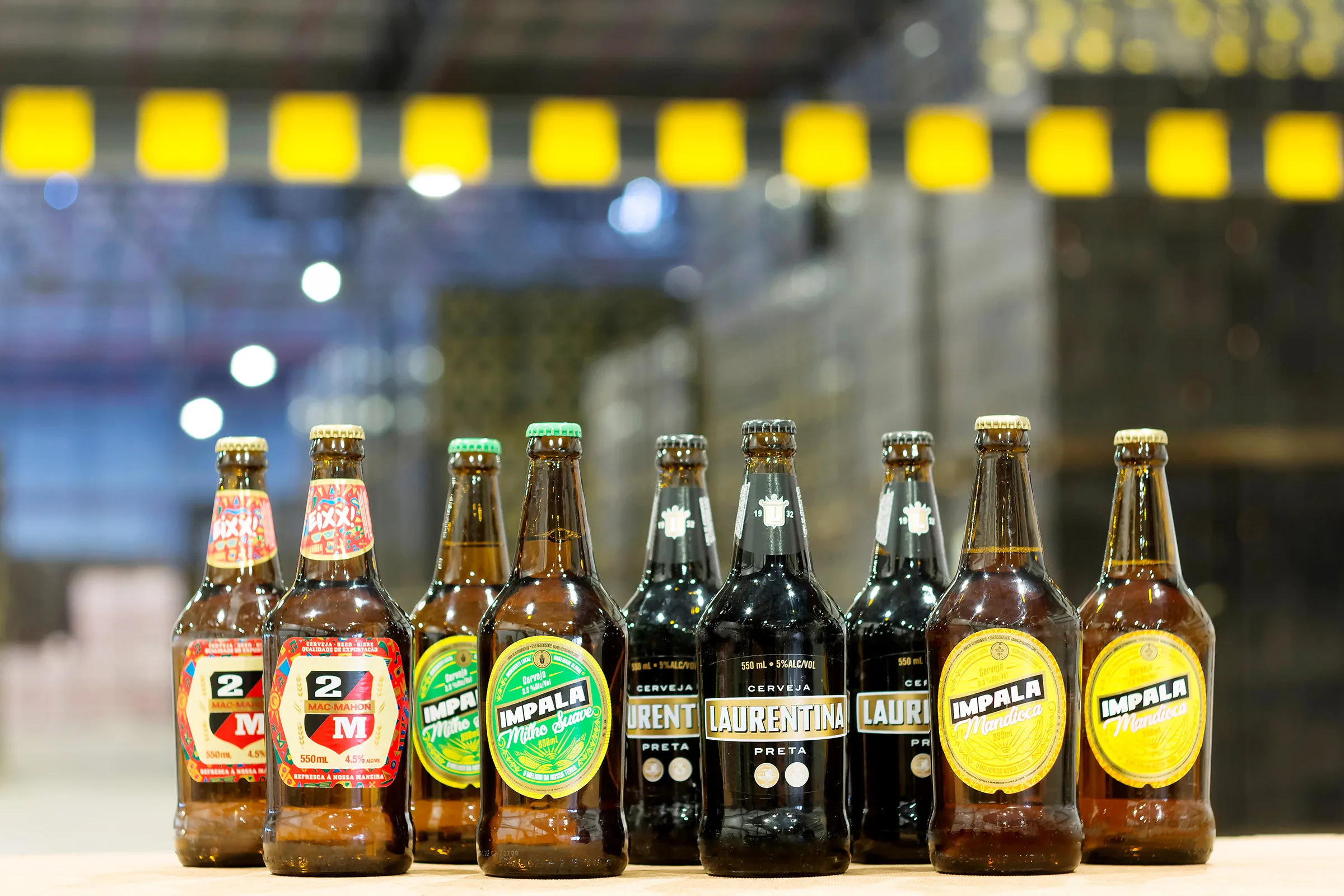
Junto a las marcas tradicionales 2M y Laurentina, desde 2011, con Impala CDM elabora una cerveza comercial a partir de la mandioca, de cultivo doméstico.
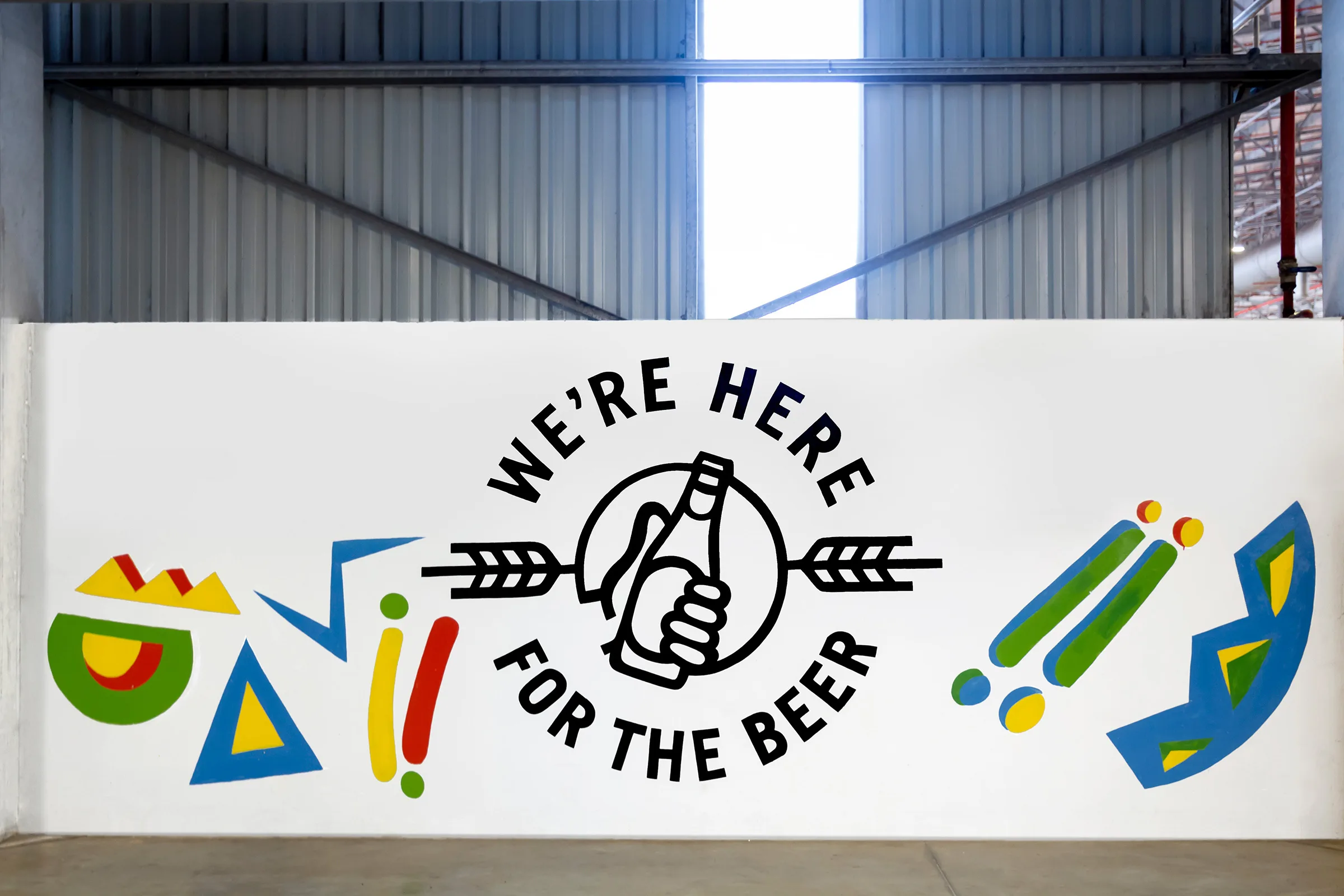
Al comprar materias primas regionales, la empresa cervecera se compromete a ayudar a los pequeños agricultores locales y a crear empleos en la agricultura.
IRed KHS internacional
CDM tiene prisa para la construcción de su nuevo emplazamiento. Con el objetivo de implementar los exigentes cronogramas y suministrar los diversos componentes lo más rápido posible, KHS confía en su red internacional: Por ejemplo, los transportadores provienen de México y los tanques de sedimentación de Sudáfrica. La línea será instalada por técnicos de Ucrania, Turquía, México y Alemania. Finalmente, los colegas de Brasil serán los responsables de la capacitación, ya que pueden comunicarse con los mozambiqueños en su lengua materna portuguesa, sin problemas de comunicación. El trabajo en equipo funciona de forma excelente desde la fase de oferta: La coordinación interna y externa necesaria se inicia tempranamente, y todos confían en poder cumplir con el desafiante cronograma.
No obstante, no todo resulta de la forma pensada: En marzo de 2019 el huracán Idai devastó el país: Más de mil personas murieron, y casi un millón perdió sus hogares. Según estimaciones del Banco Mundial, los daños en Mozambique y los países vecinos, Zimbabue y Malawi, menos afectados, ascendieron a unos 1.700 millones de euros.
La región de la capital también se vio afectada por la catástrofe natural, lo que provocó retrasos en la programación de CDM. El edificio de producción no se completó a tiempo para albergar las máquinas listas para su montaje. KHS reaccionó de forma espontánea y flexible con entregas parciales, siempre que era posible. La instalación comenzó en octubre de 2019, aunque la nave solo contaba con la estructura. A partir de ahora, todos los plazos pueden ser cumplidos, y todos los participantes están felices. Al fin y al cabo, tenían motivo para festejar, pues en febrero de 2020 se llenó la primera botella en la línea.
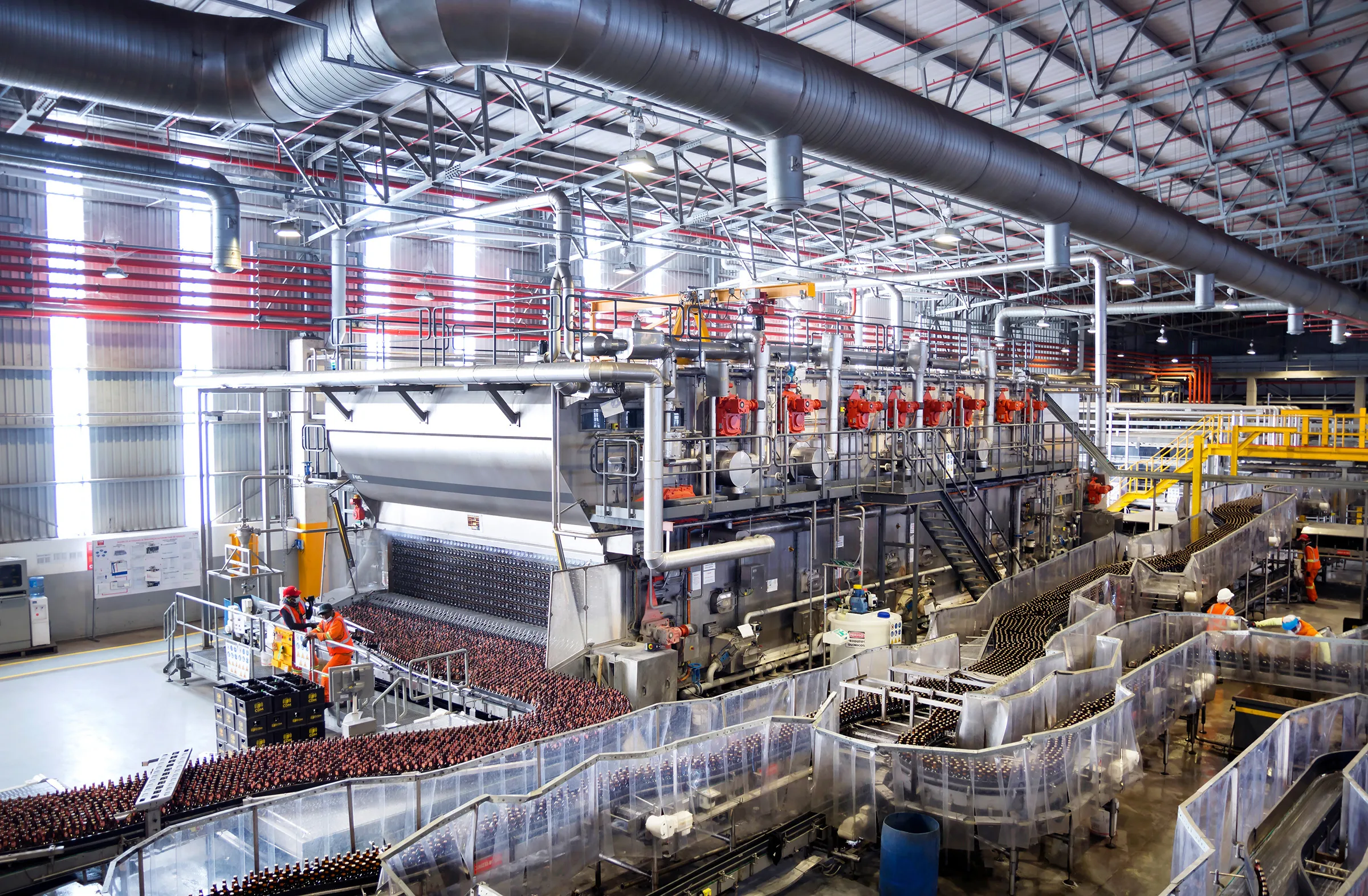
Máquina gigantesca con bajo consumo de energía y de recursos: La máquina lavadora de botellas de KHS Innoline DM puede ser vista sobre todo como un equipo de bajo consumo de agua.
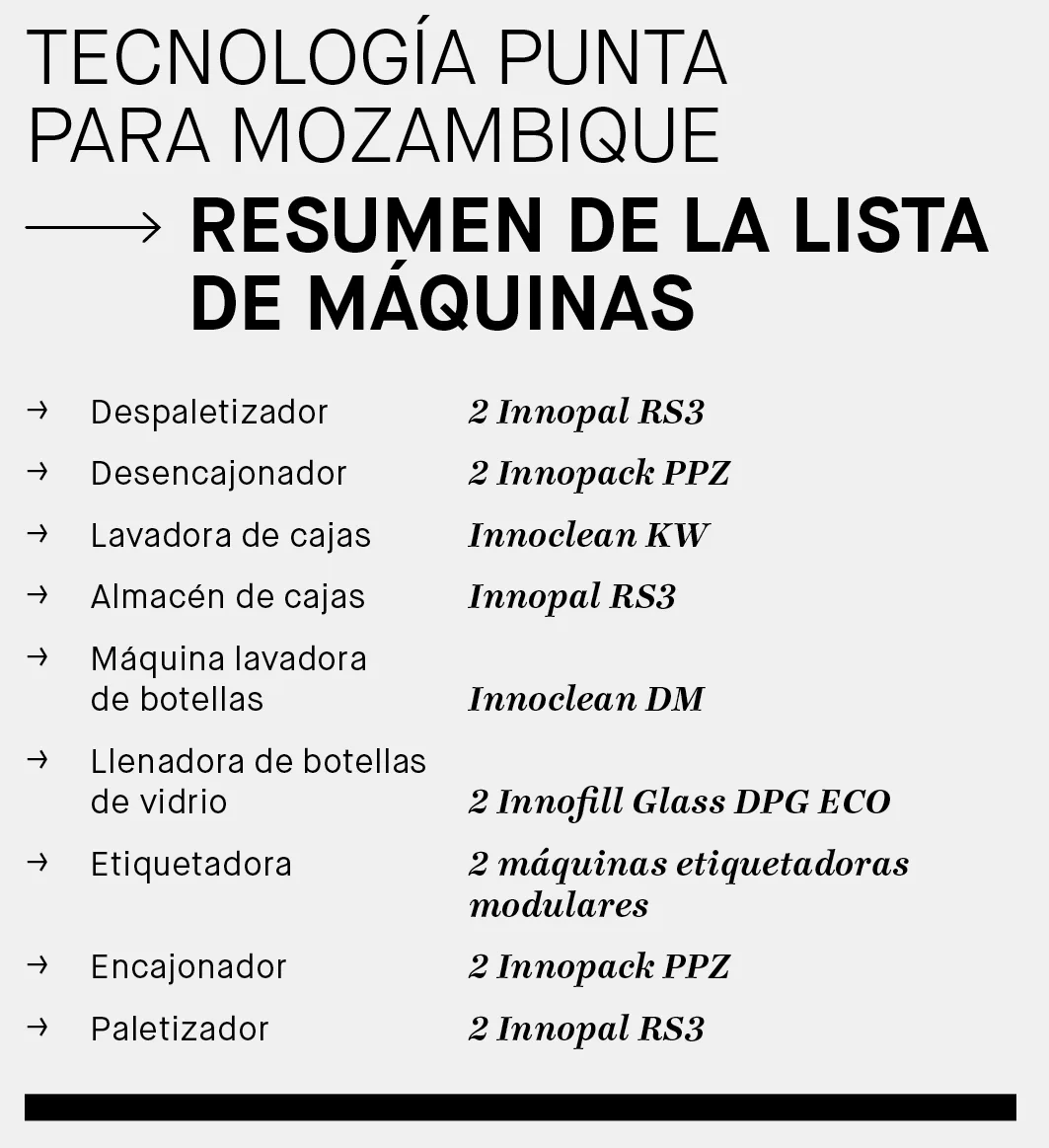
Confinamiento por Coronavirus con consecuencias
No obstante, la alegría no duró mucho tiempo. En unas pocas semanas, el Covid 19 se expande y provoca una pandemia global: Los países afectados determinan el confinamiento, las conexiones de vuelos se suspenden y los viajes se vuelven en gran medida imposibles. Mozambique anuncia el cierre de sus fronteras al cabo de un día y que el aeropuerto de Maputo dejaba de funcionar. “Nuestro equipo no tuvo más remedio que irse, literalmente, de la noche a la mañana”, recuerda Zeimentz. “Para no quedar varados en el sitio por un período de tiempo indefinido, los colegas emprendieron inmediatamente el viaje a casa, a veces difícil, manteniendo nuestro deber de protección. En ese momento, la optimización de la línea solo estaba completa en tres cuartas partes y todavía teníamos dos meses de trabajo por delante”. Sin embargo, la decisión fue la correcta en interés de los empleados: Hasta que se pudo viajar nuevamente, pasaron seis meses.
Mientras tanto, sin embargo, en el sitio las cosas debían continuar, como enfatizó Franz Schepping, Director Técnico de CDM. “Nuestro equipo local en Marracuene se enfrentaba ahora al desafío de poner en marcha esta línea de 80.000 botellas a través de reuniones en línea, llamadas telefónicas, videollamadas y el servicio de mantenimiento remoto ReDiS de KHS, sin que se pudiera realizar ninguna capacitación previa”, dice. “Por supuesto, esto inicialmente puso patas arriba nuestro plan de puesta a punto de la línea. Con mucho sudor, horas extra y algunas noches sin dormir, finalmente logramos llevar nuestro formato más importante, la botella de 550 mililitros, al punto en que pudimos suministrar nuestra cerveza a los consumidores locales”. En resumen, todos contentos de haber mantenido la línea en funcionamiento. “Una parada de varios meses hubiese sido naturalmente una catástrofe”, afirma Zeimentz.
Por el lado de la distribución, además del cuello de botella en la producción, en 2020 se suma que el gobierno restringió la venta de alcohol a ciertos horarios comerciales e impuso toques de queda en la primavera, con un impacto notable en el consumo de cerveza y en el negocio de CDM. Sin embargo, la fábrica de cerveza no se desanima por la pérdida temporal, y durante este tiempo introdujo el producto 2M Flow. Fue todo un éxito desde el principio y desde entonces goza de gran popularidad.
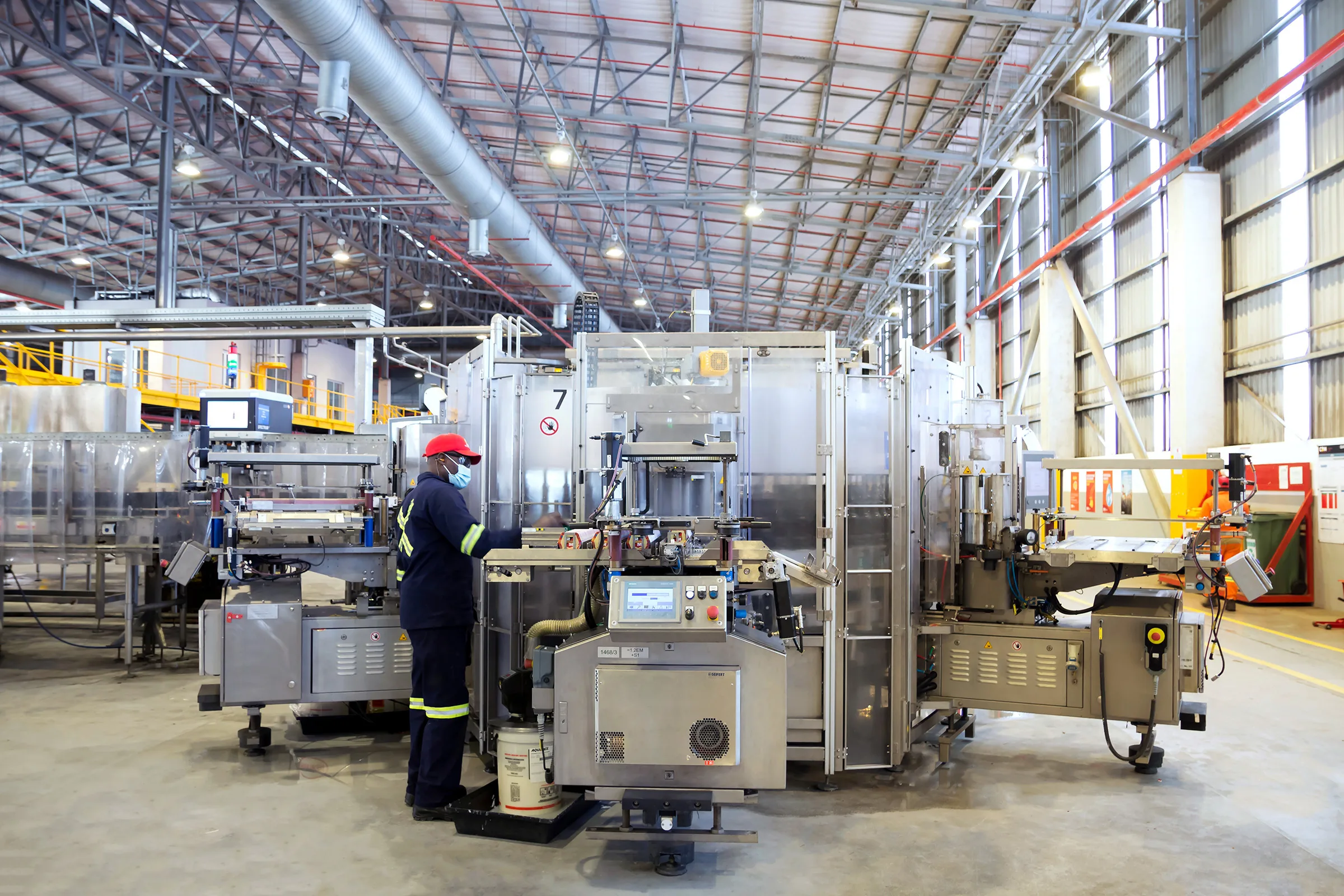
Las máquinas etiquetadoras modulares de KHS son altamente eficientes, con sus estaciones con cambio de formato en muy corto tiempo.
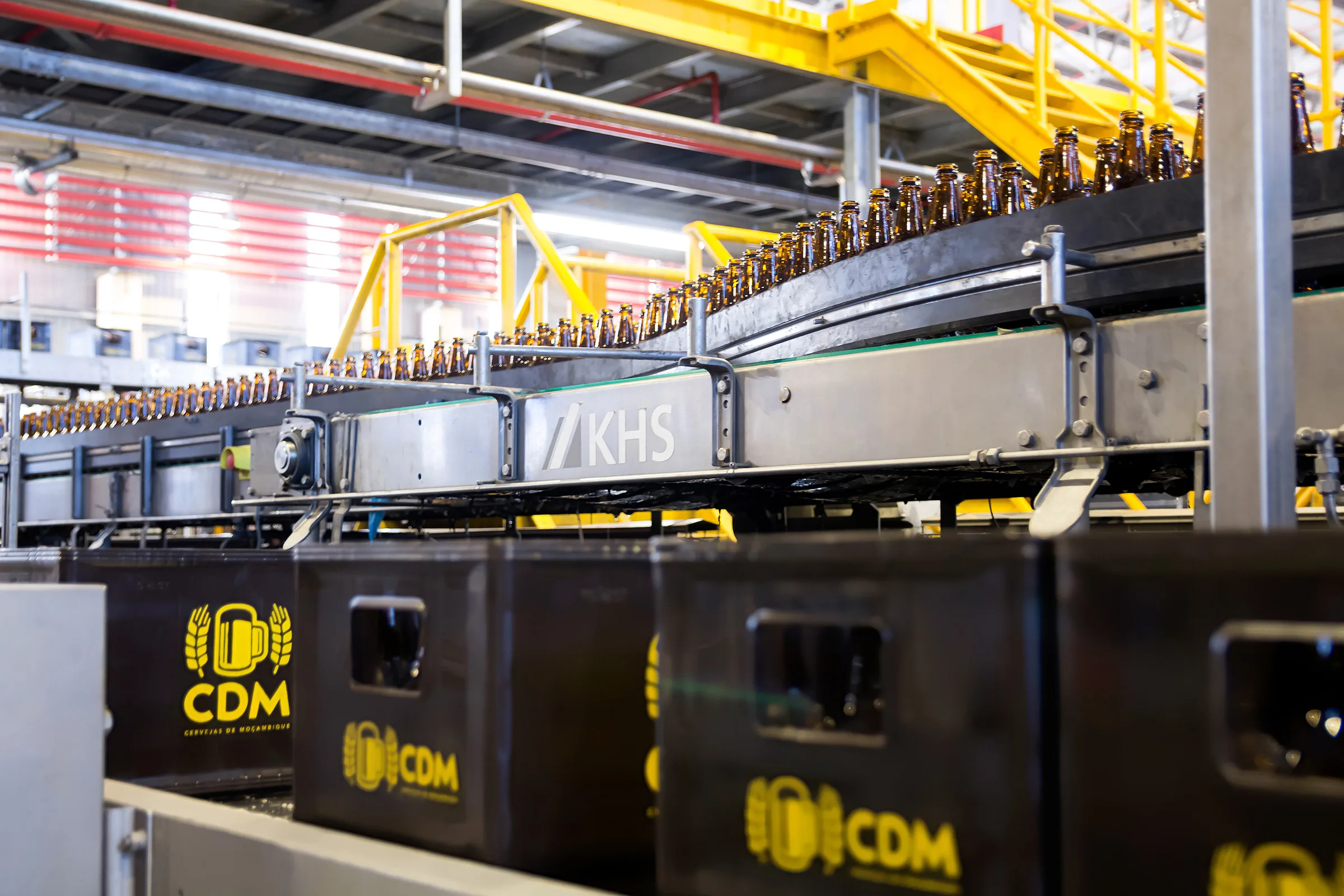
Con su rendimiento de línea extremadamente alto para la región, CDM es la fábrica de cerveza mayor y más moderna en Mozambique y toda África.
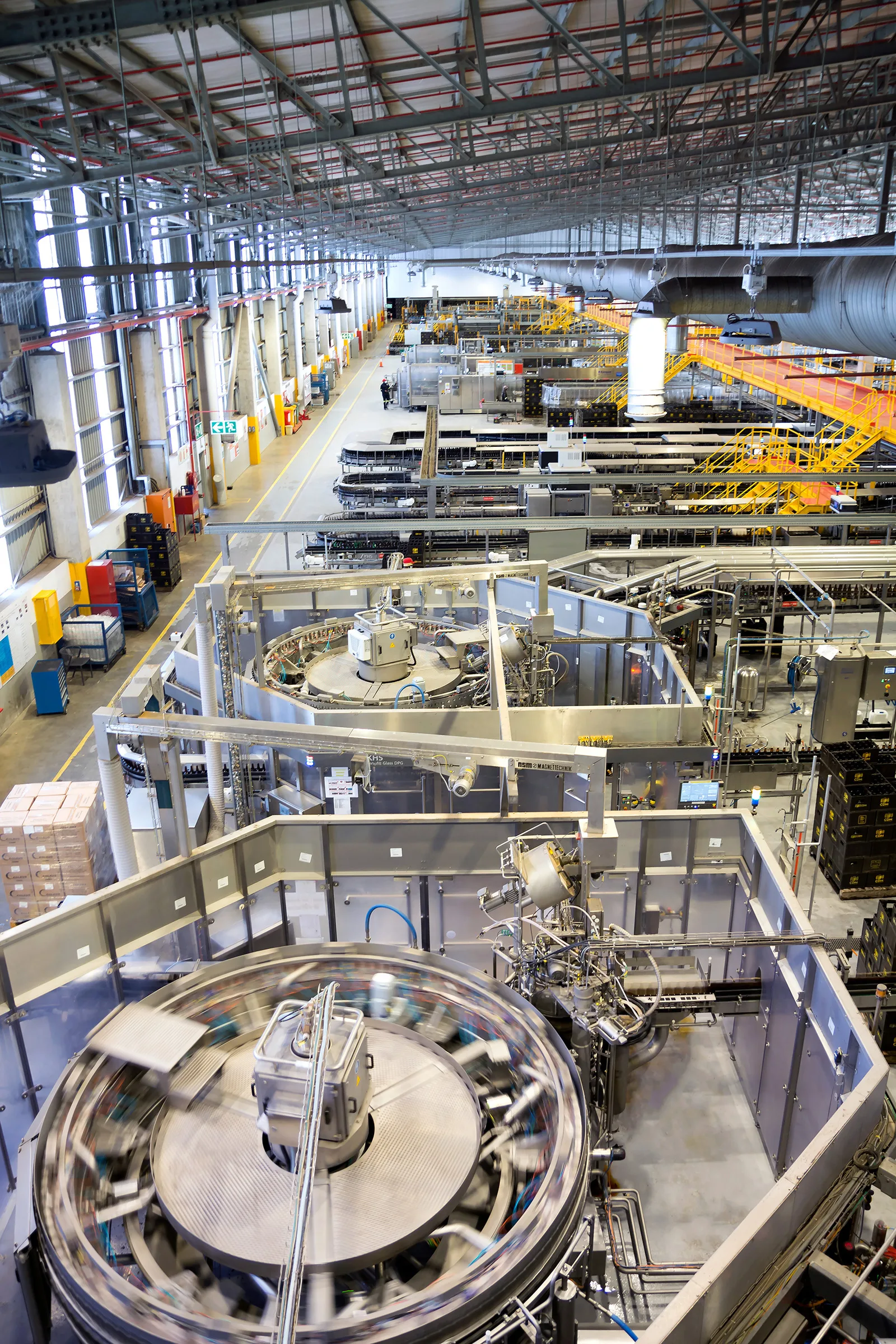
En el núcleo de la impresionante línea en el nuevo emplazamiento en Marracuene se encuentran las dos llenadoras KHS Innofill Glass DPG ECO.
Etiquetadora modular: Versátil y flexible
Por primera vez en el mundo, AB InBev está utilizando dos de las etiquetadoras modulares KHS en CDM en Mozambique. La máquina se puede equipar con varias estaciones, que se pueden convertir en muy poco tiempo simplemente mediante un acople y desacople con un carro de transporte. La flexibilidad inherente garantiza que CDM esté más preparado para el futuro: Esto permite reaccionar rápida y fácilmente a las nuevas tendencias y avances dinámicos del mercado. Los impresionantes valores de rendimiento de solo el 0,054 % de etiquetas incorrectas y una eficiencia de más del 99 % convencen doblemente de la alta calidad de la tecnología de etiquetado de KHS.
Finalmente listo para la prueba de aceptación
Recién en septiembre de 2020 la mayoría de los colegas de KHS pudieron regresar, en parte bajo condiciones difíciles, para finalizar su trabajo. En primer lugar, se llevó a cabo una auditoría exhaustiva con medidas de revisión, mantenimiento y limpieza antes de que el sistema se ajustara para su aceptación, todo teniendo en cuenta los requisitos de producción en curso. El hecho de que la pandemia no había terminado se pudo ver porque a pesar de las estrictas precauciones de seguridad, los contagios siguieron produciéndose por todos lados, lo que a su vez provocó más retrasos.
En el verano de 2021 se cumplió el objetivo: Después de una prueba de eficiencia, que con más de un 95% de eficiencia finalizó exitosamente, la línea pudo ser puesta en operación oficialmente. Junto a las dos etiquetadoras modulares de KHS, dicho sea de paso una novedad para AB InBev (ver recuadro “Versátil y flexible”), sobre todo las dos llenadoras del tipo Innofill Glass DPG-ECO convencieron a los técnicos: Los valores de absorción de TPO* muy bajos de 19 microgramos por litro y un bajo consumo de CO2 de solo 150 gramos por hectolitro, subrayan el estatus de KHS como líder en tecnología de llenado.
* TPO = Total Packaging Oxygen (oxígeno total en el envase) Absorción total de oxígeno en la llenadora.
Con una inversión de aproximadamente 150 millones de euros, se podrá inaugurar “la mayor y más moderna fábrica de cerveza de Mozambique y de toda África”, como destaca Tomaz Salomão, presidente de la junta ejecutiva de CDM. Los obstáculos imprevisibles que hubo que superar para lograr este objetivo ya están (casi) olvidados en vista de la alegría por la línea de envasado que actualmente funciona sin problemas.
¿Más preguntas?
Leroy Thangamuthu
KHS Manufacturing (Sudáfrica) Pty Ltd., Sandton
+27 11 2621 117 leroy.thangamuthu@khs.com