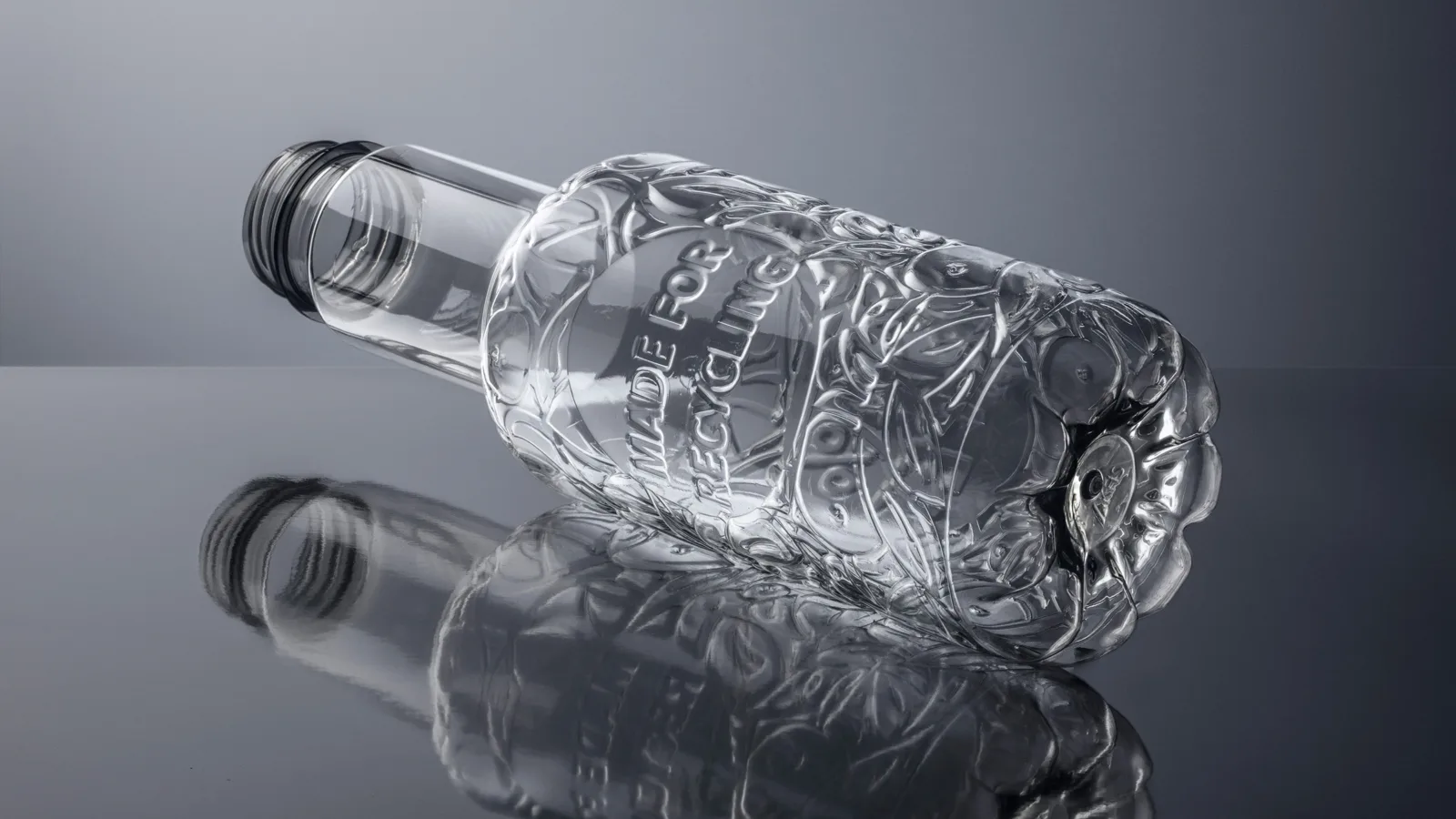
Closed loop
With its Beyond Juice project and example juice bottle KHS shows what one possible solution to the urgent problem of preventing, reusing and recycling waste could look like. Recycling specialist Interseroh has issued a special Made for Recycling seal for this exact purpose.
Developing and manufacturing sustainable packaging is one of KHS’ main lines of business. Besides the various technical challenges which have to be met there’s also the question of how to reach out to consumers and convince them of such sustainable solutions. In order to better understand how this can be achieved, KHS filling and packaging specialists recently joined forces with the recycling experts at environmental service provider Interseroh. In an attempt to improve input materials and widen the approach to recycling, the specific aim of the cooperation is to explore how those areas and materials which at the moment are still outside the sustainable circular economy can also be integrated into it. This pertains in particular to sensitive foods whose product protection at the time of writing usually consists of non-sustainable materials and is thus excluded from the recycling process. Another objective is to communicate positive results to consumers so that they can also act responsibly.
»I’m convinced that consumers are looking for a seal of quality which gives them real added value.«
![]()
Product manager for barrier technology, KHS
Special requirements
In order to show what’s already possible in this field, a project entitled Beyond Juice was launched. Juice was chosen as beverages of this nature in particular call for a number of special requirements to be met.
To protect sensitive beverages and foods against oxygen pickup and the loss of freshness and quality associated with this, PET bottles need to be protected against permeation*. To date, this barrier coating on plastics has normally comprised blended or multilayer materials which make later bottle-to-bottle recycling to produce pure PET recyclate difficult to impossible. The material blends or composite materials are very hard to separate from one another and form a jumble of secondary raw materials and chemical compounds. Approximately 10% of all PET bottles in Germany are excluded from the deposit system. Legislators have also now taken note of this ‘recycling gap’ of around 44,200 metric tons of PET a year and at the beginning of 2019 began rewarding environmentally friendly packaging systems under the new German Packaging Law. The aim is to reduce the impact of unused packaging waste on the environment by avoiding or usefully recycling it in as far as this is possible. The topic is also gaining significance beyond Germany’s national boundaries. This is illustrated by the plastics strategy presented by the EU Commission at the start of 2018 which aspires to make all packaging waste in Europe recyclable by 2030.
*Permeation: a process whereby a substance penetrates or permeates a solid through molecular interstices..
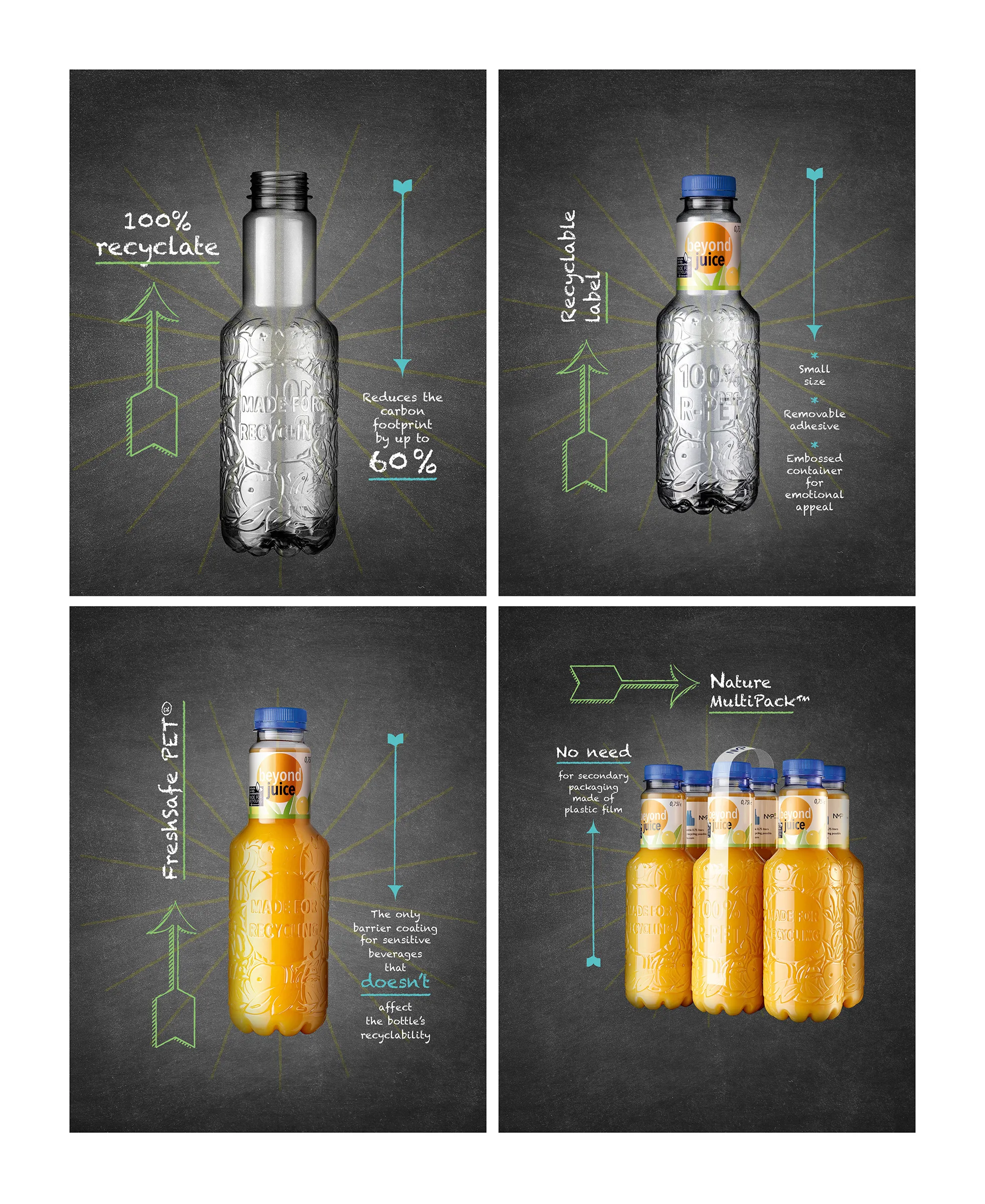
The experts in KHS’ Bottles & Shapes™ program don’t want to wait that long, however; they’ve been pursuing this idea for some time, as Arne Wiese, Bottles & Shapes™ product manager, explains. “A bottle filled with fruit juice, for example, must of course first fulfill its task of providing optimum protection for its sensitive content. Our primary aim was to develop a container which had the lowest possible impact on the environment irrespective of its sensitive content.”
This is also expressed in the name of the project. On the one hand, ‘Beyond Juice’ stands for the fact that ideas are being developed above and beyond the demands made on packaging by oxygen-sensitive juice. On the other, the name also infers that the principle can also be equally applied to all other sensitive applications which require protection.
In 2018 Interseroh introduced its Made for Recycling seal to indicate this kind of packaging and communicate this to consumers. Based on scientific criteria this certifies the very good recyclability of packaging and helps increasingly environmentally aware customers to purchase sustainable products.
»Recyclability will become just as important as the aspects of product protection, convenience and attractiveness.«
![]()
Project manager for packing optimization, Interseroh
Many unanswered questions
In the current debate on plastics practical systems are becoming more and more important for the beverage industry, too. Many producers now have entire departments considering which type of packaging is the most ecologically sound and what end customers want. In view of the complexity of this subject and the resulting confusion among consumers, these two factors don’t always correspond, Wiese emphasizes. His colleague Philipp Langhammer, product manager for barrier technology at KHS, specifies what this means for KHS. “Our customers ask themselves what consumers are asking and we ask ourselves what our customers are asking: what technologies can KHS supply to reduce the amount of packaging material? What can we do to increase the percentage of recyclate in our PET packaging? And what are we doing to improve recyclability?”
These and many other questions were the focus of the exchange with Interseroh. The goal was to solve this important problem in the market segment for oxygen-sensitive and barrier-relevant beverages. A bottle was to be found which provided optimum product protection and at the same time closed the PET materials cycle, i.e. was as gentle on the environment as possible.
“At a number of joint workshops we looked at how materials are sorted and what has to be taken into account when designing a type of packaging so that it can be perfectly recycled,” Langhammer reports. Packaging engineer Julian Thielen, project manager for packaging optimization at Interseroh, adds, “Together with designers, engineers and sales employees we discussed what the optimum eco-friendly bottle could look like, how large the label must be and which materials it’s made of. And we looked at what happens to the individual components in the sorting and recycling chain.”
Unique barrier protection
The first requirement was to ensure functional, effective barrier protection which has no negative impact on its ability to be recycled. The only marketable system for this apparent dilemma is the FreshSafe PET® technology developed by KHS. Langhammer outlines the principle behind this. “A wafer-thin coating of silicon oxide (SiOx) applied to the inside wall of the bottle significantly reduces the permeation of gas in both directions. This means that the product quality, taste, vitamins and product color are retained for up to ten times longer than in a standard PET container.” As the SiOx coating is simply washed off during the recycling process by the caustic present in the machine in any case, pure, fully reusable PET is produced which can be used in bottle-to-bottle recycling.
As the barrier coating is also suitable for containers made of recyclate, it quickly became clear that the Beyond Juice bottle must consist of 100% recycled PET.
»We wanted to develop a container which had the lowest possible impact on the environment irrespective of the product protection.«
![]()
Product manager for Bottles & Shapes™ at KHS Corpoplast
Another limiting factor is that the demand for PET recyclate exceeds the supply. In some countries there are no collection and sorting systems and the necessary approval is lacking for the use of recyclate previously utilized for other purposes to package foods, for instance. For Thielen this is a clear argument in favor of product-related collection systems. “Only these make the food-grade application of recyclate at all possible as they clearly indicate that a bottle has never left the cycle. Accordingly, the risk of contamination is low.” FreshSafe PET® offers a solution here, too, Langhammer states. “Our coating even permits recyclate formerly used in the non-food segment to be used for food products under certain conditions.”
The Beyond Juice team also paid great attention to the bottle label. “Its size is the deciding factor,” says Langhammer. “It mustn’t cover the entire bottle otherwise the NIR scanner won’t recognize this as a reusable PET bottle in the sorting process.” According to Interseroh’s principle of assessment the upper label limit for a type of packaging which is very easy to sort and thus recycle is 25% of the entire bottle surface. The Bottles & Shapes™ experts have found a solution to this which, despite the relatively small label format, satisfies all marketing requirements when it comes to appealing to the emotions of the consumer: they’ve embossed the container, giving it an attractive, all-round surface structure. With its relief print the Beyond Juice will also be a real eye-catcher on the shelves.
Scientifically based seal
Das „Made for Recycling“-Siegel wurde 2018 von dem Umweltspezialisten Interseroh, Tochter der europaweit und in China tätigen ALBA GroThe Made for Recycling seal was developed in 2018 by environmental specialist Interseroh, a member of the ALBA Group which operates throughout Europe and in China. It shows the consumer that a product package has been optimized for recycling. The seal criteria have been defined in cooperation with the bifa environmental institute and the scientific method confirmed by the Fraunhofer Institute for Process Engineering and Packaging (IVV) in Freising. During analysis a maximum of 20 points can be obtained – only companies whose packaging scores 18 points or more are granted use of the seal. Consumers first came into contact with the seal at the beginning of 2019: it was first presented to Bio-Zentrale Naturprodukte GmbH in Germany in February. This is an organic food company which aims to have the packaging of its entire product range successively tested, optimized and approved for seal use.
Recyclable label
There are other criteria which have to be considered besides the size of the label. For example, it’s important to select the right adhesive so that the label can be separated from the plastic in the recycling process and there’s no unintentional soiling during the washing process. Only when the label can be completely removed in an alkaline solution at a temperature of 60°C to 80°C is pure PET produced. In this context the idea was also discussed of doing away with the label altogether. “Printing brand messages and other information directly onto the bottle means that the printing inks used for this purpose have to be suitable for the recycling process,” explains Langhammer. The cap was also the focus of special attention from the expert team. In the future German legislation would like it to be fixed to the PET bottle in such a way that it can’t be removed once opened – as with the closures on many energy drinks. This is to ensure that the bottle caps are also recycled.
In an attempt to leave the smallest possible ecological footprint KHS has also thought beyond the actual bottle itself. In addition to the recyclable barrier coating, use of 100% recyclate and the smallest possible label attached with the right adhesive, the Beyond Juice project was enhanced by the Nature MultiPack™ as the fourth plus point. This joins several bottles together with dots of adhesive to form a stable pack with easy-to-remove containers, making all secondary shrink film packaging superfluous – a KHS innovation already successfully launched to market.
After the first bottles had been produced last summer, they were sent to Interseroh for inspection. “To confirm that absolutely no other barriers had been used, we tested the material in the lab using various methods and compared it,” recycling expert Thielen reports. As is usual in this analysis, the KHS Beyond Juice bottle samples were repeatedly sent through a scanner on a sorting conveyor to ensure that they were correctly segregated. The final score was a full 20 out of 20 – an absolute first in the segment for PET bottles with barriers. The Made for Recycling seal now proves that KHS has reached its ambitious target: the company has managed to develop a container which is as gentle as possible on resources yet also provides effective barrier protection.
Lots learned
At the end of the joint development project everyone was convinced by the results. Arne Wiese sums things up for us. “We’ve learned a lot about recyclability – not just concerning beverage and food packaging but also about the collection of materials, storage and the challenges posed by processing for all types of packaging.” His colleague Philipp Langhammer looks to the future. “We’re going to present this bottle at the major upcoming trade shows and with it want to show people what’s possible at the moment. In doing so we wish to suggest that consumers can opt for a sustainable form of packaging without having to forgo outstanding product protection. We first have to see how the market receives this and later how the end customer accepts the seal. I’m convinced that consumers are looking for a scientifically based seal of quality which gives them real added value.” Julian Thielen is certain that the seal will also prove to be a success among beverage producers. “In the medium term, for packaging the criterion of recyclability will become just as important as the aspects of product protection, convenience and attractiveness – also on an international scale.”
All sensitive beverages and foods filled into PET bottles can therefore be recycled in the long term and their materials reused for the same application – with immediate effect. There’s therefore really no reason to wait until 2030 for the container that perfectly satisfies all recycling requirements. On the contrary: until then we can look forward to plenty more exciting developments from Bottles & Shapes™.