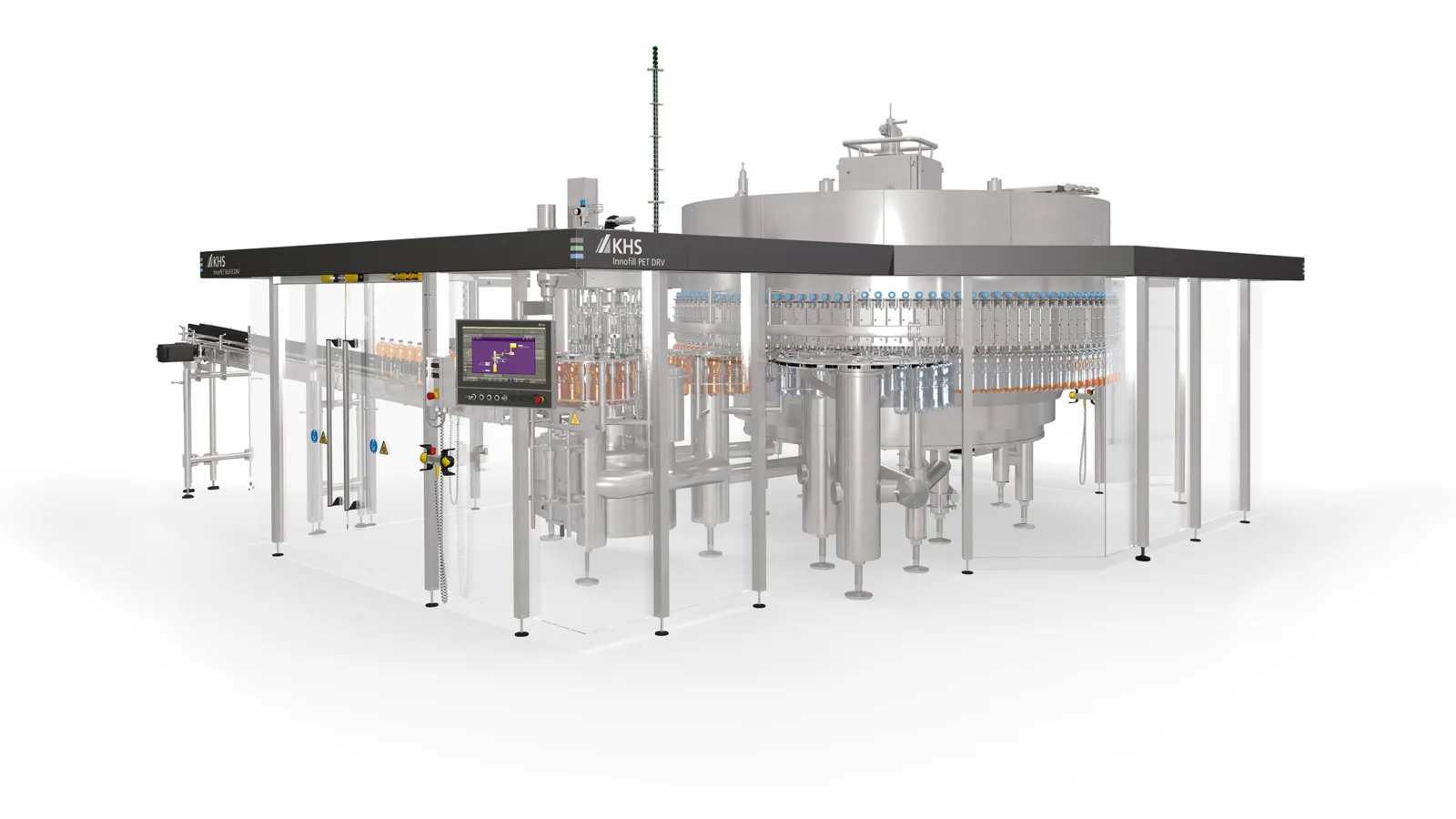
All options open
The new PET filler platform from KHS is distinguished by its level of standardization and a multitude of technological improvements. There’s very little that gives beverage producers more flexibility and security for the future when filling their increasing variety of products.
Bottlers today face a number of economic and ecological challenges regarding the packaging of their products. On the one hand, they are under a great deal of pressure in relation to time and cost: new and ever more powerful packaging systems and technologies need to be developed and commissioned as quickly as possible; the consumption of materials, media and energy has to be constantly reduced and efficiency and productivity boosted in the process. On the other, the beverage industry – like so many other sectors – has become the focus of legislation: the increased regulation of recycling quotas and CO2 emissions or the introduction of tethered caps stipulated by the EU as part of its Single-Use Plastics Directive are just a few of the measures manufacturers are obliged to adopt in order to do their bit for the protection of the climate. This is also increasingly expected of them by environmentally-aware consumers who, in the same breath, neither wish to do without a high variety of products nor packaging that’s both practical and affordable.
Future-proof PET block systems
In light of these developments KHS offers its customers a wide range of future-proof block systems, particularly for the filling of products into PET bottles. These include its latest stretch blow molding technology (also see the box on the KHS InnoPET Blomax Series V), with or without fully recyclable barrier protection, and a powerful labeler. The filler is naturally a core component of these systems. Here, KHS provides innovative plant engineering for carbonated and still beverages and for filling all kinds of sensitive products in a capacity range of up to 90,000 bottles per hour.
What’s new and absolutely revolutionary about the Dortmund systems supplier’s PET filling equipment is the modular, configurable and expandable platform. Consistently implemented on its glass fillers in 2020, its machines for plastic bottles now also satisfy the most demanding customer requirements for maximum adaptability and future viability. “The beverage market is undergoing an extremely dynamic process of change as regards its products,” says Manfred Härtel, filling product manager for KHS in Bad Kreuznach. “Where possible, bottlers want to and must therefore now keep all options open when investing in their production technology so that they can tailor their portfolio to consumer demands at any time.” The aspects of flexibility, sustainability, product quality and efficiency are thus very much in focus – in combination with smart technology that ensures trouble-free production monitoring and control. The new PET filler platform from KHS provides not one but several answers to each and every one of these issues.
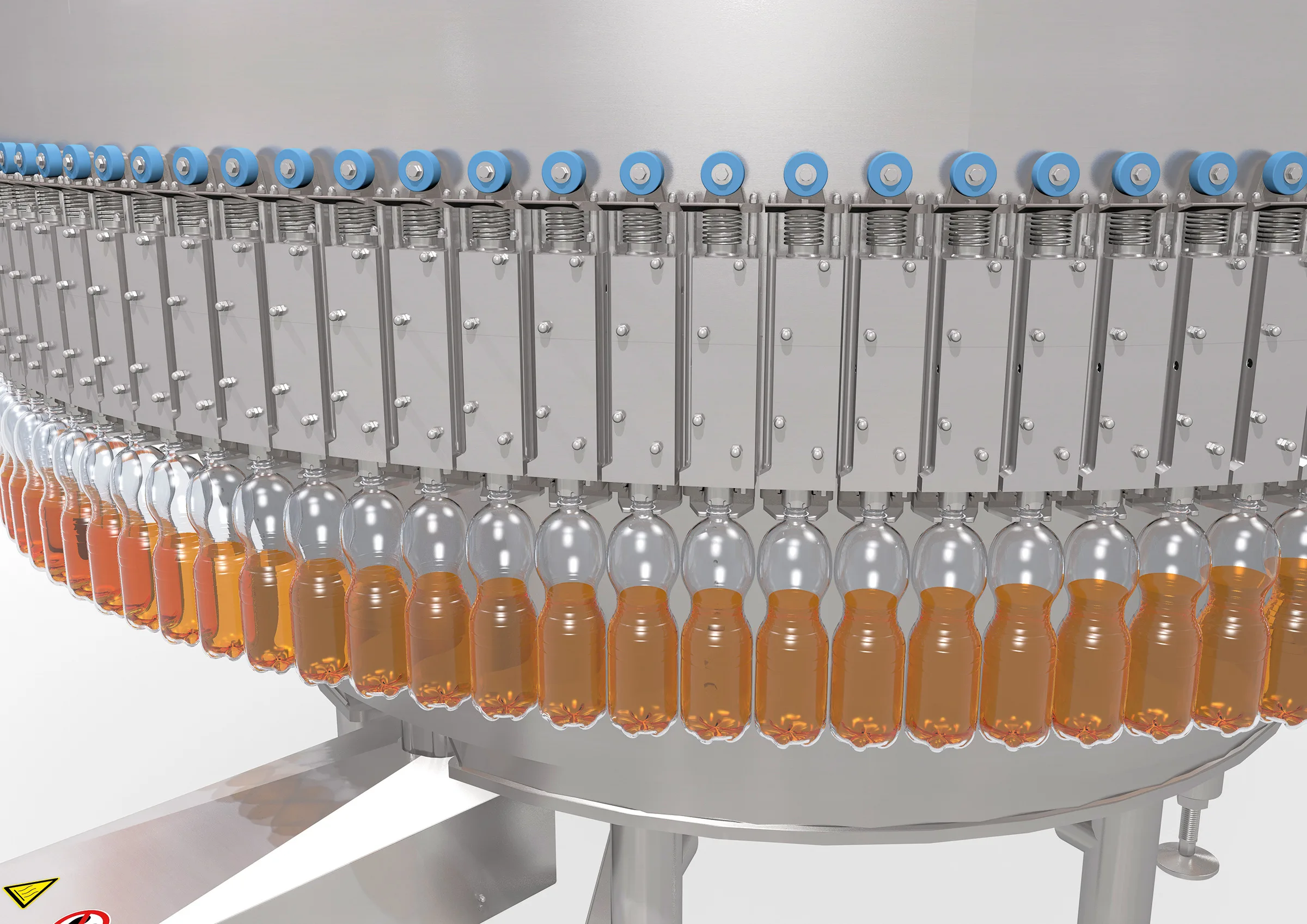
The clear, straightforward design with its smooth, mostly enclosed surfaces increases hygiene and makes cleaning and disinfection easier.
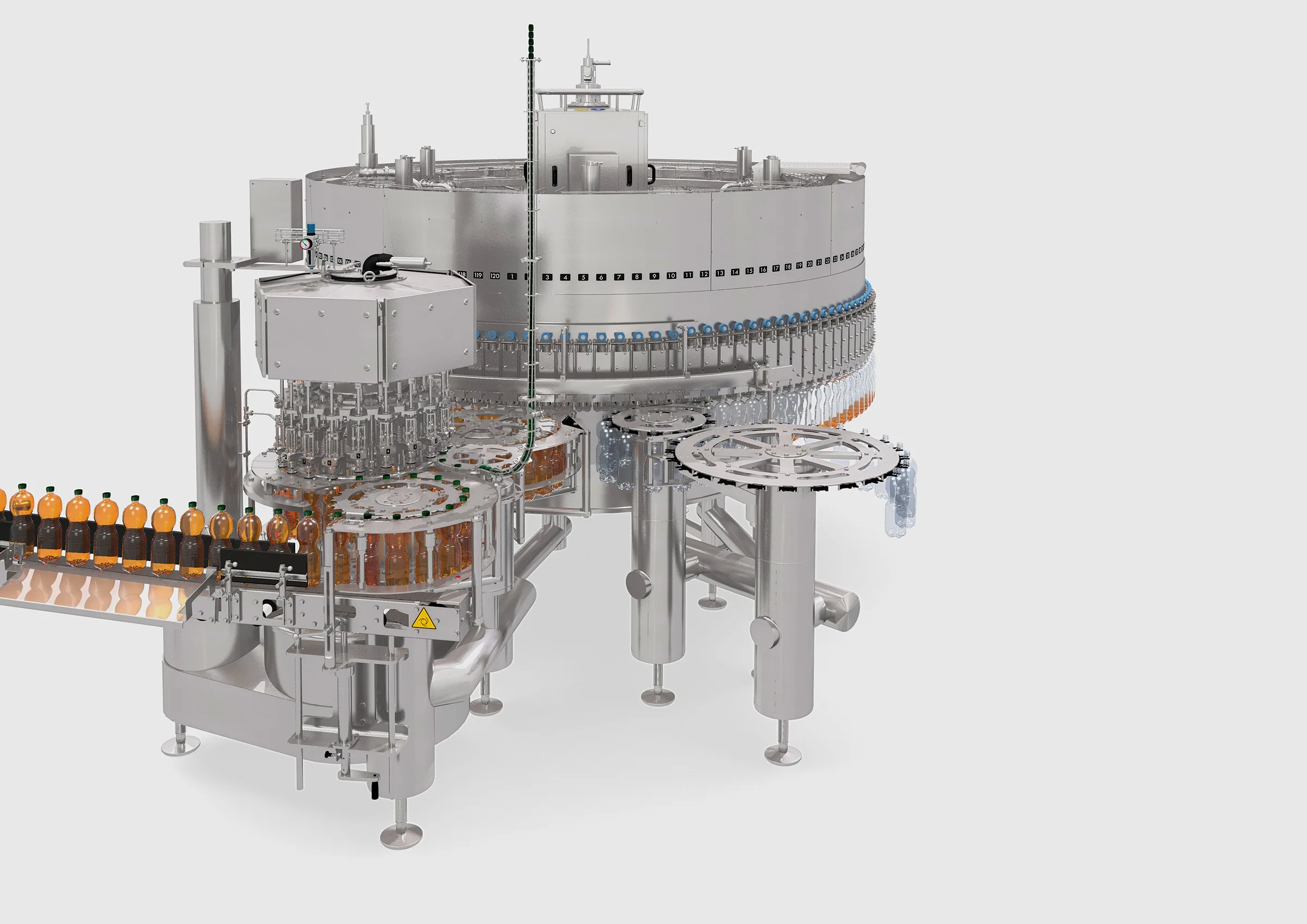
Beverage producers are perfectly equipped to meet future market demands with the new KHS filler featuring a servo screw capper.
Greater flexibility
“No one can predict which trends will still prevail in the industry in five years’ time,” Härtel ascertains. “This is why we’ve made our platform so modular that it can be converted to other beverages or PET containers at any time according to market requirements.” Individual components can thus be bought in at a later stage and integrated into the existing machinery with relatively little effort. “Depending on which filling system a customer goes for, they can react to changing market requirements. Thanks to the modularity of the filling systems, functions and features can be easily added. Our DRV system, for instance, processes carbonated and still beverages. For the non-contact filling of water and hot filling of juice at temperatures of up to 95°C, we then have our NV filling system. And for beer and mixed beer beverages there are our DVF and DRF long-tube filling systems,” smiles Härtel.
Maximum flexibility is also enhanced by the high degree of automation for format and product changeovers. “Even now, for example, operators don’t need more than a quarter of an hour to change a 0.5-liter bottle over to a 1.0-liter PET bottle,” the product manager says.
KHS InnoPET Blomax Serie V.
PET fillers are seldom a solitary phenomenon but instead a fixed feature of the KHS portfolio of block systems. The same applies to KHS’ latest-generation of stretch blow molders, the InnoPET Blomax Series V, that’s distinguished by its outstanding productivity. Its output, for instance, has now been increased to up to 2,800 bottles per blow station and thanks to intelligent process control, NIR heating and a simple modular design it also boasts an efficiency of over 98%. The InnoPET Blomax Series V is convincing when it comes to sustainability, not only with its ability to save on bottle weight but also regarding its flexibility in the processing of recycled or virgin PET. Moreover, numerous technical optimizations considerably reduce the amount of energy and blow air used by up to 40% compared with the previous series.
More climate protection
When customers demand sustainable beverage filling with maximum energy savings and minimum CO2 emissions, beverage fillers are perfectly equipped to supply this with the new PET filler platform. “On the DRV filling system, for instance, CO2 consumption has been cut from 150 grams per hectoliter to practically zero,” explains Härtel. “We also no longer use CO2 as a pressurization gas, instead favoring sterile air.” Countless design improvements also help to save energy – from the compact tubular ring bowl to the highly effective servodrives. Moreover, as the new filler permits filling temperatures of up to 24°C, no more investment and operating costs are incurred for energy-intensive cooling devices. A further plus is that at these temperatures no condensation is formed that needs to be dried using a high amount of energy before the bottles are packaged in film or cardboard. The hygienic design also contributes to the overall sustainability of the new technology: as the clear, straightforward design of the machine surfaces enables a free runoff of liquids, cleaning and disinfection procedures are easier and shorter. Finally, as bottles are conveyed through the machine by their neck rings, the handling of lightweight containers is supported, thus helping to ensure that products are packaged safely and reliably while saving on resources.
Best possible quality
In view of the increasing variety of products and ever more frequent type changeovers, avoiding flavor carryover is of central importance. One key prerequisite needed to achieve the level of flexibility beverage fillers require is thus to choose the right sealing material for the expansion joint seals on valve pistons and switching cylinders. “KHS uses PTFE* here,” emphasizes Härtel. “This material can be excellently cleaned and absorbs practically no flavoring substances – unlike standard seals made of elastomers such as EPDM** that soak up liquid like a sponge during production. When there’s a drop in concentration with the next product in the filling sequence, the EPDM again releases these flavorings – water, for example, then tastes of the beverage previously filled. In order to prevent this unwanted effect, the production plan has to be scheduled by flavor: the week thus starts off with a mineral water, for instance, and continues with the filling of products with an increasingly intensive taste, such as energy drinks. After these have been processed, the filler then has to be thoroughly cleaned before water can be bottled. By considerably reducing the flavor transfer, our filling valves give our customers more freedom in their production planning.”
* PTFE = polytetrafluorethylene (Teflon).
** EPDM = ethylene-propylene-diene rubber.
»We’ve made the new filler platform so modular that it can be converted to other beverages or PET containers at any time according to market requirements.«
![]()
Filling product manager for KHS
The solid jet principle of the NV filling system with its practically drip-free gas lock also helps to ensure a high product quality. “From a microbiological standpoint, it’s beneficial if the beverage doesn’t come into contact with the bottle neck,” Härtel continues. The product manager also always keeps an eye on the amount of oxygen pickup. It’s important to avoid this wherever possible, for instance when hot filling juice. “Too much oxygen pickup could cause pulp to float to the surface and thus form clumps; it would also lower the vitamin C content in the products.” Oxygen pickup is an extremely relevant topic for breweries in particular. “Bottom-up filling on our DVF and DRF long-tube valves significantly reduces oxygen pickup and allows beer and mixed beer beverages of excellent quality to be filled into PET bottles.”
The exact filling volume is determined with the help of an inductive flow meter or – optionally – a mass flow meter. Two different filling speeds are configured as standard that ensure optimum flow behavior and low-foam filling. A number of optional additional components are available for the best possible processing of different volumes and viscosities, such as a large spectrum of bottle sizes or juices with a low or high viscosity. A control valve upstream of the filling valve can freely regulate the filling speed to enable production within a capacity range ideally suited to the type of beverage, amount of foaming, bottle volume and viscosity. Together with extremely gentle container control, this results in less product loss.
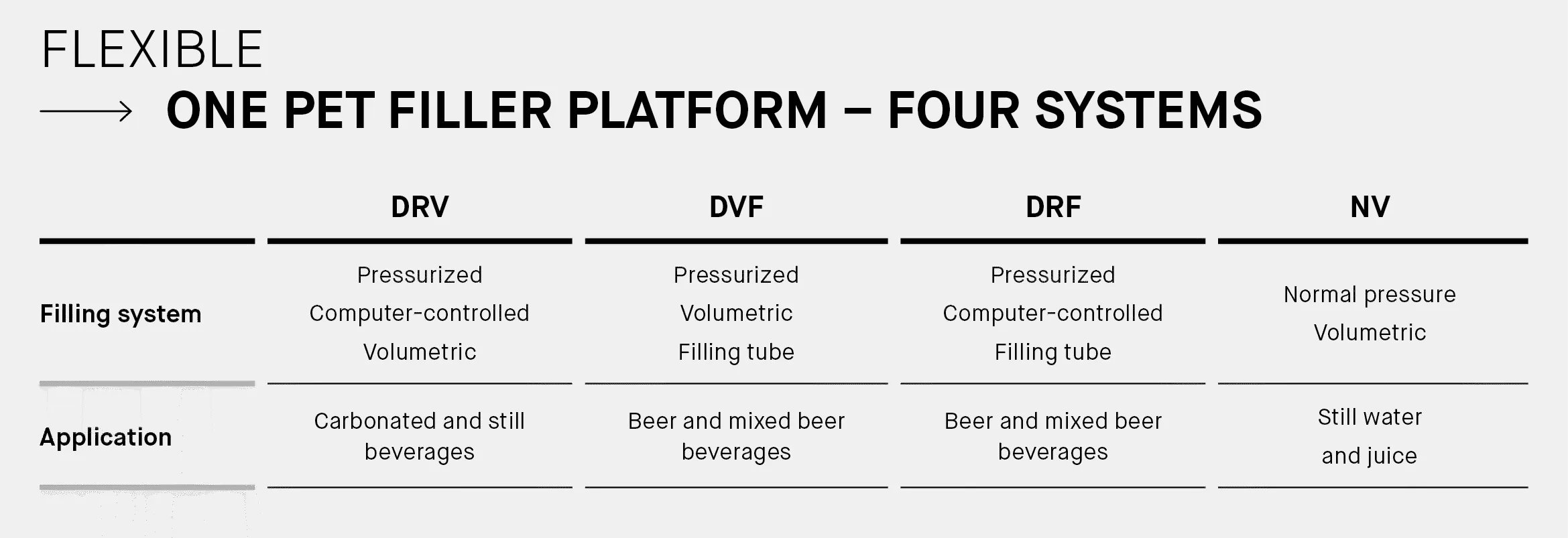
Higher efficiency
“Through the optimum design and deployment of the components on our filling valves, the new filler platform achieves a maximum power density – regardless of the type of beverage,” Härtel states. “We’ve implemented this modularity and standardization in both the machine controller and the mechanical equipment. As our fillers will always have the same construction in the future, installation and commissioning will be much faster. This shortens the time to the start of production and the first commercial product.” Here, semi- and fully automated format changeovers especially ensure a permanently high level of availability during ongoing operation. Some parts of the cleaning system are also already automated, such as the CIP sleeves. In addition to providing hygienic safety, the use of quick functions also means that they save considerably on time. As several operator tasks are now redundant, the number of potential sources of error is also reduced. The durability of all components also makes for greater efficiency as maintenance intervals are now much longer.
Great transparency
The technical highlights of the new filler platform are supplemented by the optional KHS DIAS diagnostic assistance system. This enables all aspects of the entire filling process to be monitored. For this purpose, pressure sensors are installed in every single filling valve that constantly record and document the internal bottle pressure and step sequence. The data gathered is displayed as a pressure graph on the KHS ClearLine HMI (human machine interface) operator panel. Any deviations from target values immediately trigger an alarm, meaning that faults can be quickly detected, localized and independently remedied by the customer. At the same time, the data enables results to be statistically evaluated, on the basis of which future sources of error can be eliminated in advance during preventive maintenance. DIAS therefore ensures consistent product quality and the continuation of ongoing operation.