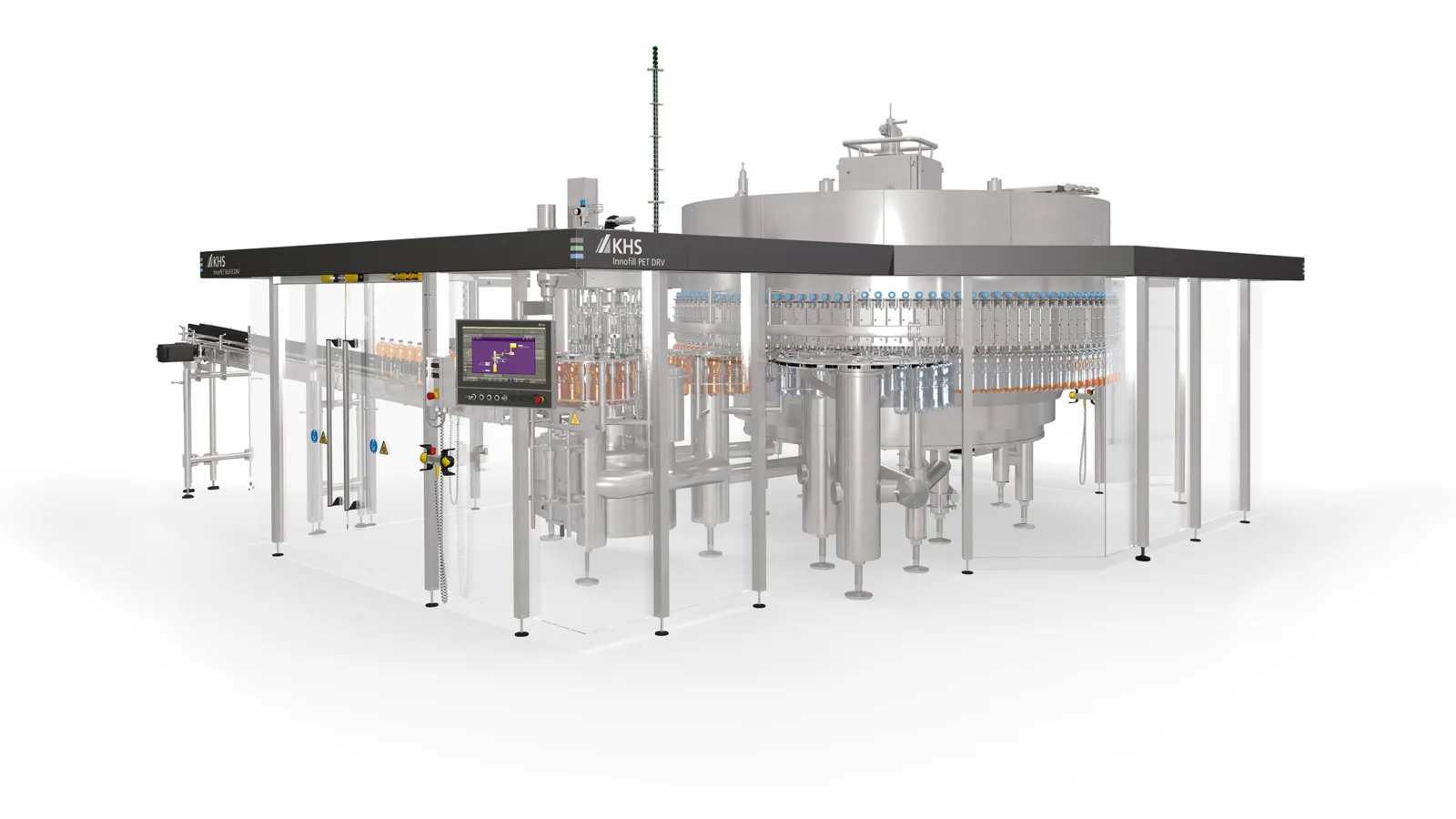
Abierta para todo
La nueva plataforma de llenado PET de KHS se caracteriza por la estandarización y un gran número de mejoras tecnológicas. Los fabricantes de bebidas difícilmente puedan lograr más flexibilidad y seguridad futura para el envasado de su creciente variedad de productos.
Con respecto al envasado de sus productos, los embotelladores se enfrentan a multitud de retos económicos y ecológicos. Por un lado, están bajo una enorme presión de tiempo y costes: Se deben desarrollar y poner en funcionamiento soluciones y tecnologías de envasado nuevas y cada vez más eficientes lo antes posible. Al mismo tiempo, el consumo de materiales, medios y energía debe reducirse aún más, y aumentar la eficiencia y la productividad. Por otro lado, la industria de bebidas, como muchos otros sectores, están en el foco de la legislación: La mayor regulación de las cuotas de reciclaje y las emisiones de CO2, o la introducción de tapones atados prescritos por la UE como parte de su directiva de plásticos de un solo uso, son solo algunas de las medidas con las que los fabricantes deben contribuir a la protección climática. Los consumidores, cada vez más conscientes del medio ambiente, también esperan esto y, al mismo tiempo, no quieren prescindir de una amplia variedad de productos o embalajes que sean prácticos y asequibles al mismo tiempo.
Soluciones en bloque para PET, con proyección de futuro
En el contexto de estos desarrollos, KHS ofrece a sus clientes una amplia gama de soluciones unidas en bloque con visión de futuro, especialmente para el envasado de botellas PET. Incluyen la última tecnología de moldeo por estirado-soplado (ver cuadro KHS InnoPET Blomax Serie V), con o sin protección de barrera totalmente reciclable, así como etiquetadoras de alto rendimiento. Un componente central de estos equipos son naturalmente las llenadoras. Aquí, KHS ofrece soluciones innovadoras para bebidas carbonatadas y sin gas, así como para el envasado de todo tipo de productos sensibles, con una capacidad de hasta 90.000 botellas por hora.
La nueva plataforma modular, configurable y ampliable, es francamente revolucionaria en la tecnología de llenado de PET del proveedor de sistemas de Dortmund. Implementadas consistentemente para llenadoras de botellas de vidrio en 2020, las máquinas para botellas de plástico ahora también cumplen con los requisitos más exigentes de los clientes para una máxima adaptabilidad y seguridad futura. “En cuanto a sus productos, el mercado de bebidas está sujeto a un proceso de cambio muy dinámico”, dice Manfred Härtel, Gerente de Producto de Envasado de KHS en Bad Kreuznach. “Los embotelladores quieren y deben, por lo tanto, mantener todas las puertas abiertas cuando invierten hoy en su tecnología de producción para poder adaptar su gama a las necesidades del consumidor en cualquier momento”. En consecuencia, los aspectos de flexibilidad, sostenibilidad, calidad del producto y eficiencia requieren la mayor atención, en combinación con tecnología inteligente que garantice un control y un seguimiento fluidos de la producción. Para cada uno de estos aspectos, la nueva plataforma de llenado PET de KHS ofrece no solo una, sino varias soluciones.
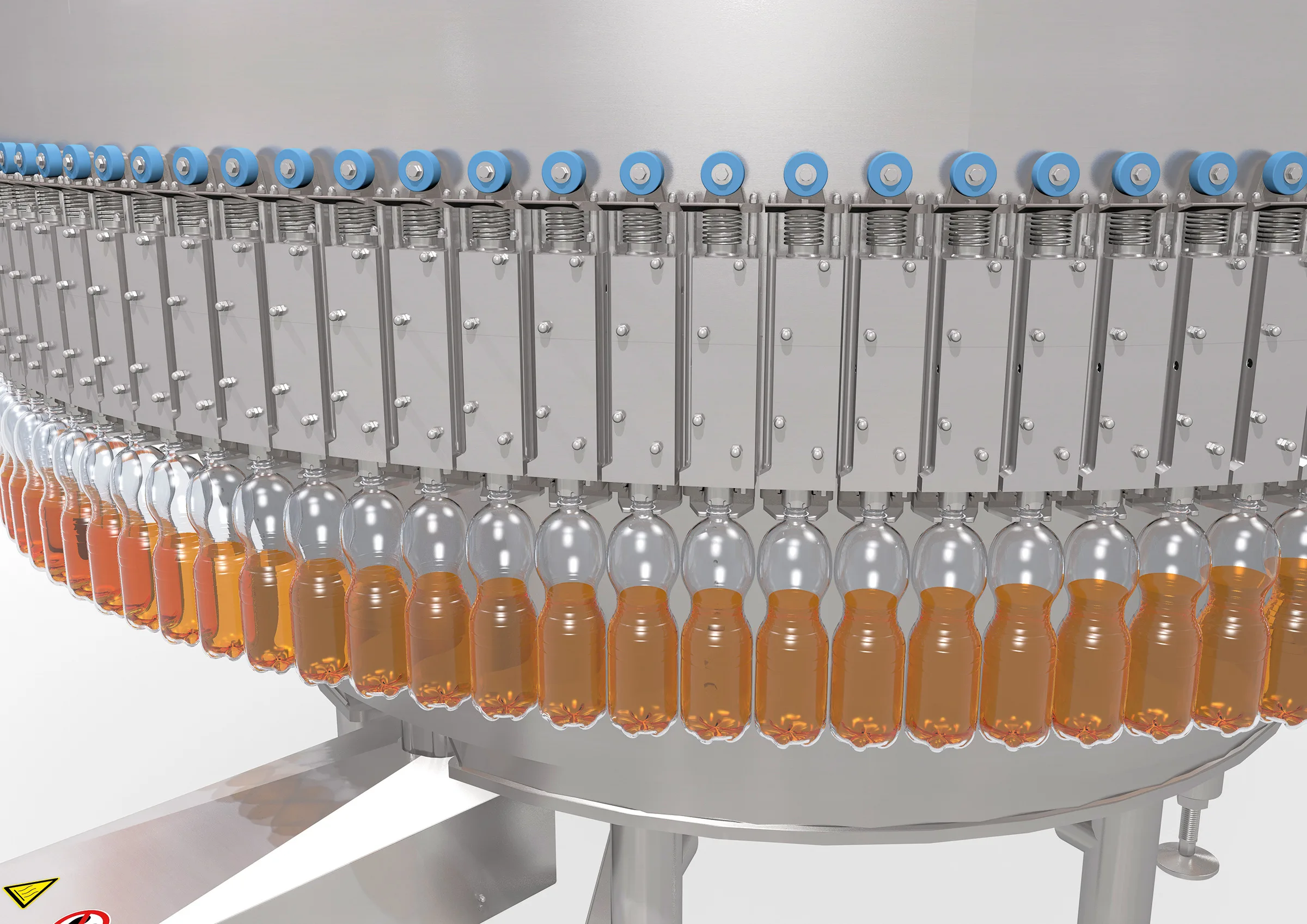
El diseño claro y lineal con superficies lisas y en gran parte cerradas aumenta la higiene y facilita la limpieza y la desinfección.
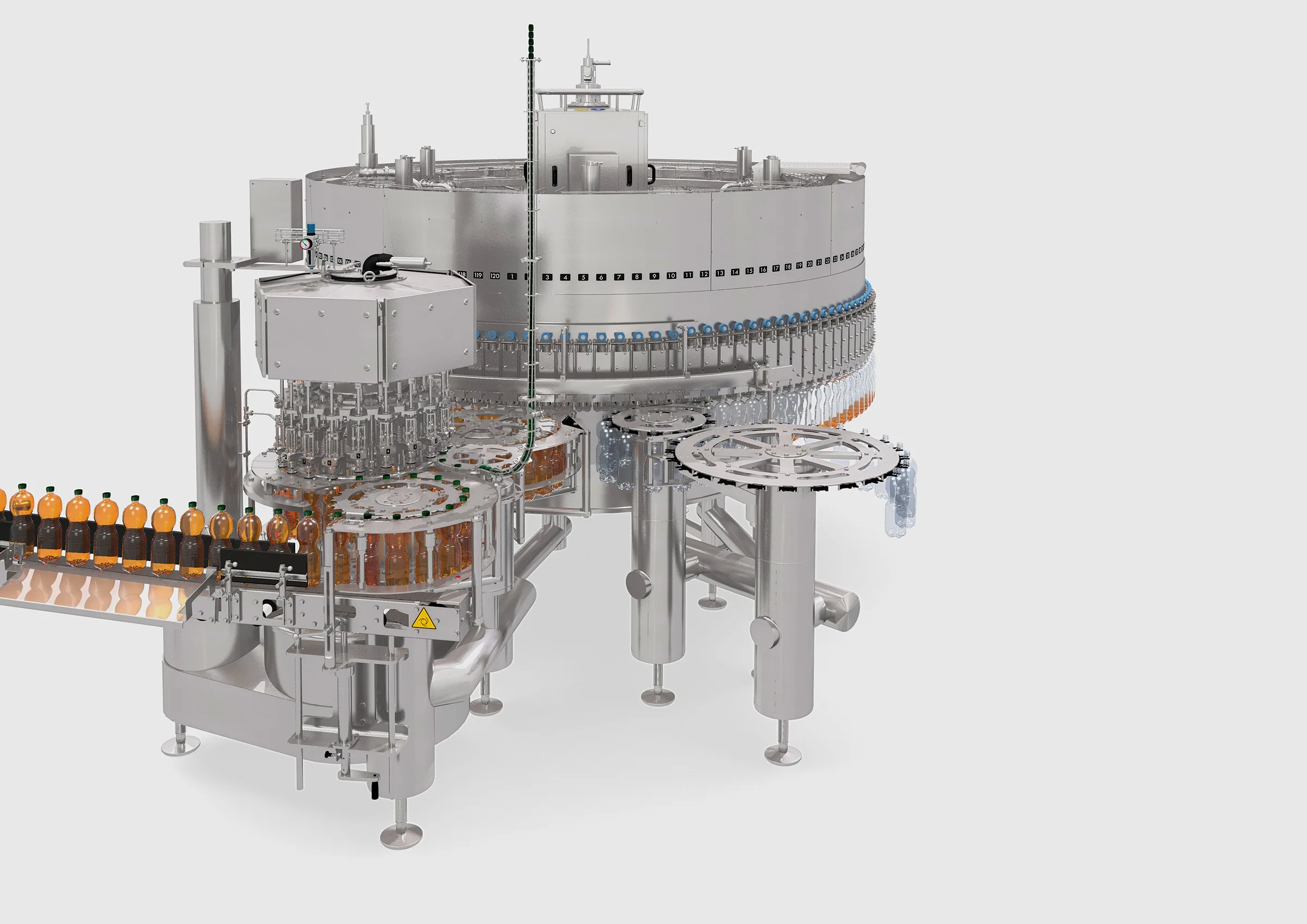
Con la nueva llenadora de KHS con taponador de tapas roscadas con servomando, los fabricantes de bebidas están bien preparados para los futuros requerimientos del mercado.
Mayor flexibilidad
“Nadie puede predecir qué tendencias de la industria prevalecerán dentro de cinco años”, afirma Härtel. “Por esta razón, hemos diseñado nuestra nueva plataforma de forma tan modular que se puede convertir a otras bebidas o envases PET en cualquier momento, según los requisitos del mercado”. De esta manera, los componentes individuales se pueden comprar en un momento posterior e integrarse en las soluciones existentes con un esfuerzo manejable: “Dependiendo del sistema de llenado que elija un cliente, puede reaccionar a los requisitos cambiantes del mercado. Gracias a la modularidad de los sistemas de llenado, se pueden añadir fácilmente funciones y propiedades. Con nuestro sistema DRV, por ejemplo, se pueden procesar bebidas carbonatadas y no carbonatadas. El sistema de envasado NV está disponible para el llenado de agua sin contacto y el envasado de jugos en caliente a temperaturas de hasta 95 grados centígrados. Y para la cerveza y las bebidas mezcladas con cerveza, están nuestros sistemas de llenado de tubo largo DVF y DRF”, dice Härtel.
Al mismo tiempo, el alto grado de automatización para el cambio de formato y de producto permite máxima flexibilidad. “Actualmente, el operario no necesita más de un cuarto de hora para cambiar de una botella PET de 0,5 litros a una de 1 litro, por ejemplo”, dice el Gerente de Producto.
KHS InnoPET Blomax Serie V
Una llenadora PET rara vez viene sola, sino que es una parte integral de la cartera de soluciones de máquinas unidas en bloque de KHS. Lo mismo se aplica a la última generación de máquinas de moldeo por estirado-soplado, la InnoPET Blomax Serie V, que se caracteriza por su excepcional productividad. La producción ahora se ha incrementado hasta 2.800 botellas por estación de soplado y, gracias al control de proceso inteligente, al calentamiento NIR y a un diseño modular simple, la máquina de moldeo por estirado-soplado logra una eficiencia de más del 98%. En términos de sostenibilidad, la InnoPET Blomax Serie V impresiona tanto por el posible ahorro en el peso de la botella como por su flexibilidad en términos de procesamiento de PET reciclado o virgen. Además, numerosas optimizaciones técnicas aseguran una reducción significativa del consumo de energía y de aire de soplado de hasta un 40%, en comparación con la serie anterior.
Más protección al medio ambiente
Si los clientes exigen un envasado de bebidas sostenible con grandes ahorros de energía y las menores emisiones posibles de CO2, con la nueva plataforma de llenado de PET están en la mejor posición: “Para el sistema de envasado DRV, por ejemplo, el consumo de CO2 de 150 gramos por hectolitro pudo reducirse a casi cero”, explica Härtel. “Podemos prescindir por completo del CO2 como gas de presurización previa. En su lugar utilizamos aire estéril”. Numerosas mejoras de diseño garantizan al mismo tiempo ahorros de energía, desde carrusel tubular compacto hasta los servoaccionamientos altamente efectivos. Y dado que la nueva llenadora permite temperaturas de envasado de hasta 24 grados centígrados, no hay costes de inversión ni de operación para la tecnología de refrigeración, que consume mucha energía. Además, a estas temperaturas no se forma condensación, que tendría que secarse con un alto consumo de energía antes de efectuar la envoltura en papel de aluminio o cartón. El diseño higiénico también contribuye a la sostenibilidad de la nueva tecnología: El diseño claro y lineal de las superficies de la máquina permite que los líquidos se escurran libremente, lo que hace que la limpieza y la desinfección sean más fáciles y rápidas. Por último, el transporte de botellas a través de la máquina sobre el anillo de apoyo facilita la manipulación de botellas de peso ligero, y contribuye así a un envasado seguro y al mismo tiempo económico de los productos.
La mejor calidad posible
En vista de la creciente variedad de productos y los cambios de bebidas cada vez más frecuentes, evitar la transferencia de aromas es de vital importancia. Por lo tanto, un requisito previo importante para la flexibilidad deseada por el fabricante de bebidas es la decisión a favor del material de sellado adecuado para el sello de fuelle de los émbolos de válvulas y cilindros de conmutación. “Aquí, KHS utiliza PTFE*”, enfatiza Härtel. “Este material es fácil de limpiar y casi no absorbe sustancias aromáticas, a diferencia de los sellos habituales hechos de elastómeros como EPDM**, que literalmente absorben como una esponja durante la producción. Si hay un gradiente de concentración para el siguiente producto en la secuencia de llenado, el EPDM libera los aromas nuevamente; el agua, por ejemplo, sabe como la bebida que se llenó anteriormente. Para impedir este efecto indeseable, el plan de producción debe basarse en el aroma: Para ello, la semana comienza con un agua mineral y continúa con el embotellado de productos cada vez más intensos en sabor, como las bebidas energéticas. Después del procesamiento, la llenadora debe limpiarse a fondo antes de que se pueda envasar agua. Al reducir significativamente la transferencia de aromas, nuestras válvulas de llenado brindan a los clientes más libertad en la planificación de su producción”.
* PTFE = Politetrafluoretileno (teflón)
** EPDM = Caucho de etileno-propileno-dieno
»Diseñamos la nueva plataforma de llenado de una manera tan modular que, según los requisitos del mercado, se puede convertir en cualquier momento a otras bebidas o envases PET«.
![]()
Gerente de Producto de Envasado, KHS
El principio de chorro completo del sistema de envasado NV con bloqueo de gas casi sin goteo también contribuye a la alta calidad del producto: “Desde el punto de vista microbiológico, es una ventaja que la bebida no entre en contacto con la boca de la botella”, enfatiza Härtel. El Gerente de Producto siempre vigila la absorción de oxígeno. Es importante evitarla tanto como sea posible, por ejemplo, en el envasado en caliente de jugos: “Por un lado, demasiado oxígeno podría provocar la suspensión de la pulpa y, por lo tanto, la formación de obstrucciones y, por otro lado, reduciría el contenido de vitamina C de los productos”. El contenido de oxígeno es altamente relevante sobre todo para las cervecerías: “El llenado de abajo arriba con nuestras válvulas de tubo largo DVF y DRF reduce significativamente la absorción de oxígeno y permite que la cerveza y las bebidas mezcladas con cerveza se llenen en botellas PET con una calidad excelente”.
El volumen de llenado exacto se determina con la ayuda de un medidor de flujo inductivo u, opcionalmente, un medidor de flujo másico. De forma estándar están configuradas dos velocidades de llenado diferentes, lo que garantiza un comportamiento de flujo óptimo y un llenado con baja formación de espuma. Para el mejor procesamiento posible de diferentes volúmenes y viscosidades, por ejemplo, con un amplio espectro de tamaños de botellas o de jugos diluidos o espesos, hay componentes adicionales disponibles de forma opcional: Con una válvula de control antepuesta a la válvula de llenado, la velocidad de llenado se puede ajustar de forma continua para poder producir en el rango de rendimiento óptimo en términos de tipo de bebida, formación de espuma, volumen de botella y viscosidad. Junto con la conducción extremadamente suave del envase, se logra una menor pérdida de producto.

Mayor eficiencia
“Gracias al diseño y a la disposición óptima de los componentes de nuestras válvulas de llenado, la nueva plataforma de llenado logra la mayor densidad de rendimiento posible, independientemente de la bebida”, enfatiza Härtel. “Hemos implementado esta modularidad y estandarización tanto en el control de la máquina como en la mecánica. Dado que nuestras llenadoras siempre tendrán la misma estructura en el futuro, el montaje y la puesta en marcha se pueden realizar con mayor rapidez. Esto acorta el tiempo hasta el inicio de la producción y el primer producto comercial”. En particular, los cambios de formato parcial o totalmente automatizados aseguran un alto nivel de disponibilidad. Partes del proceso de limpieza ya están automatizadas en la actualidad, como los manguitos CIP. Además de su seguridad higiénica, ofrecen un importante ahorro de tiempo gracias al uso de funciones rápidas. Al eliminar algunas tareas del operador, se reducen las posibles fuentes de error. La durabilidad de todos los componentes también contribuye a una mayor eficiencia, ya que los intervalos de manten
Encontrará más información sobre nuestra llenadora PET para bebidas carbonatadas y sin gas en khs.com.
Alta transparencia
Los aspectos técnicos destacados de la nueva plataforma de llenado se completan, opcionalmente, con el Sistema de Asistencia de Diagnóstico DIAS de KHS. Este permite un control completo de todo el proceso de llenado. Para ello, en cada una de las válvula de llenado se instalan sensores de presión que registran y documentan de forma continua la presión interna en las botellas y la secuencia de pasos. Los datos proporcionados se muestran como una curva de presión en el panel del operador KHS ClearLine HMI (interfaz hombre-máquina). Cualquier desviación de los valores nominales activa inmediatamente un mensaje para que el propio cliente pueda identificar, localizar y corregir rápidamente los fallos. Al mismo tiempo, los datos permiten una evaluación estadística en base a la cual se pueden eliminar de antemano futuras fuentes de fallos como parte del mantenimiento preventivo. Gracias a DIAS se garantiza la calidad constante del producto y el mantenimiento continuo de las operaciones en curso.