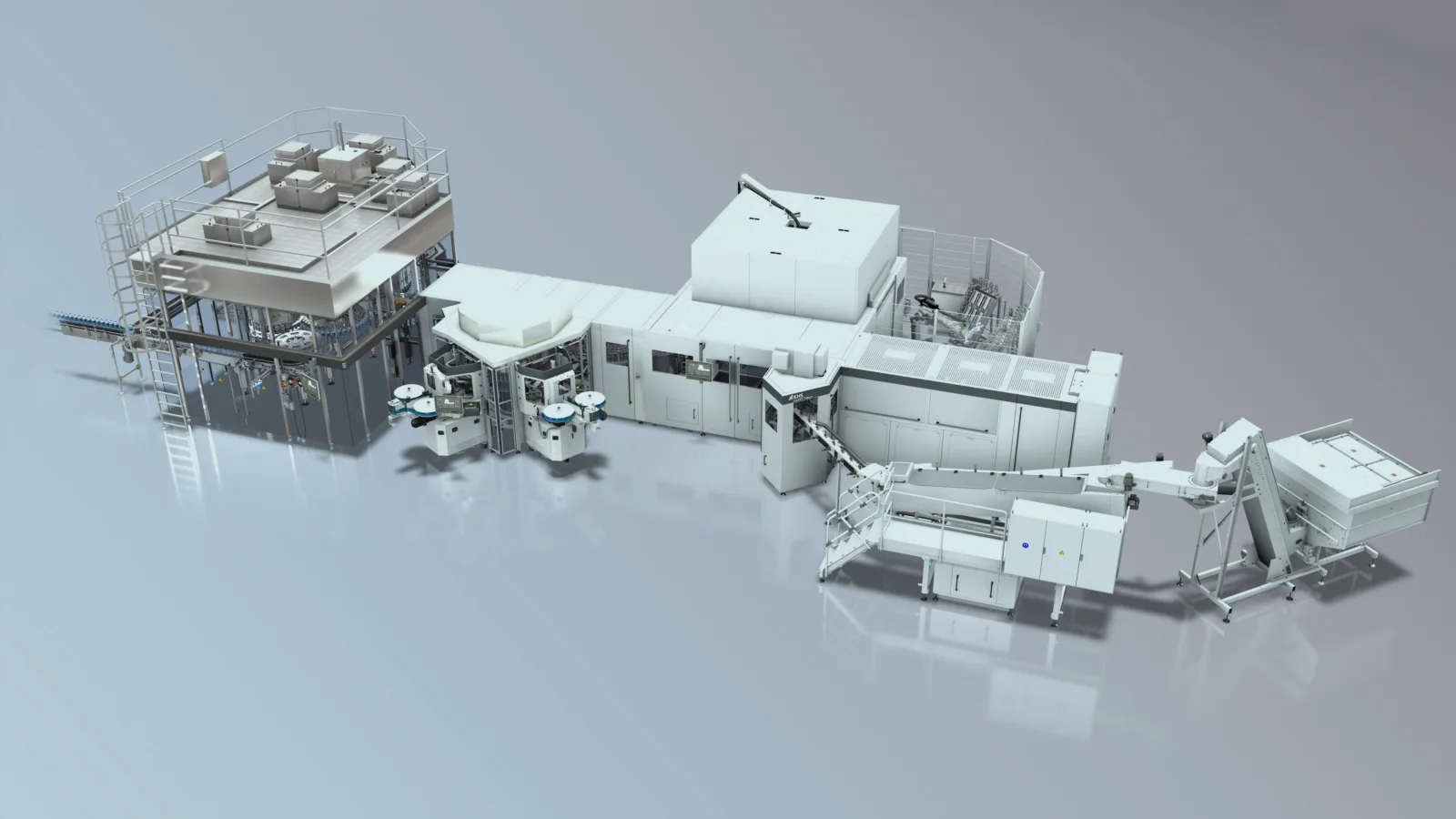
Flexible and efficient
The example of KHS’ stretch blow molder/labeler/filler block illustrates how automated format changeovers function in detail. And it shows that beverage producers can combine maximum flexibility with a high level of efficiency.
PET lines today are very rarely configured exclusively from individual machines. One of KHS’ system solutions in this field, for instance, is its InnoPET TriBlock comprising a stretch blow molder, labeler and filler – as on the line equipped with the KHS InnoPET iflex automatic changeover option (see the article No time to lose). The filling section is thus a self-contained, compact machine concept that exactly meets the demands beverage producers have of modern production technology. Besides taking up little space with its shorter conveying segments plus its reduced maintenance effort, this block system scores with its short changeover times. The last aspect is where the KHS InnoPET iflex comes into play on the InnoPET TriBlock line; this example shows how automation can help operators to save a considerable amount of time during production. To this end, various functions were developed for the different segments that considerably increase the level of automation and make manual intervention largely superfluous with a few clicks on the HMI.
Format changeovers by robot
PET bottles are produced in the stretch blow molding module. When formats are scheduled for a changeover, the iflex first triggers the automatic loading of recipes for the heating profile, blow pressure, preform conveying and inspection technology.
The most important new feature on this machine is the mold changeover when the new batch requires a different bottle size or shape. Here, the switch is made with the help of a robot that changes the two side mold shells and base mold fully automatically and very quickly during ongoing production. It removes the previous molds from the stations, places them in the mold set magazine, takes out the new molds and slots them back into the stations without any need for action from the operator. The robot needs just 41 seconds per station for this short, fully reproducible procedure. The time for manual intervention is thus reduced from a previous 95 to just eight minutes. This is further facilitated by automatic bottle base detection adjustment at the blow wheel transfer star with the help of several sensors. All the operator has to do by hand is to start the format changeover and later start the new production run.
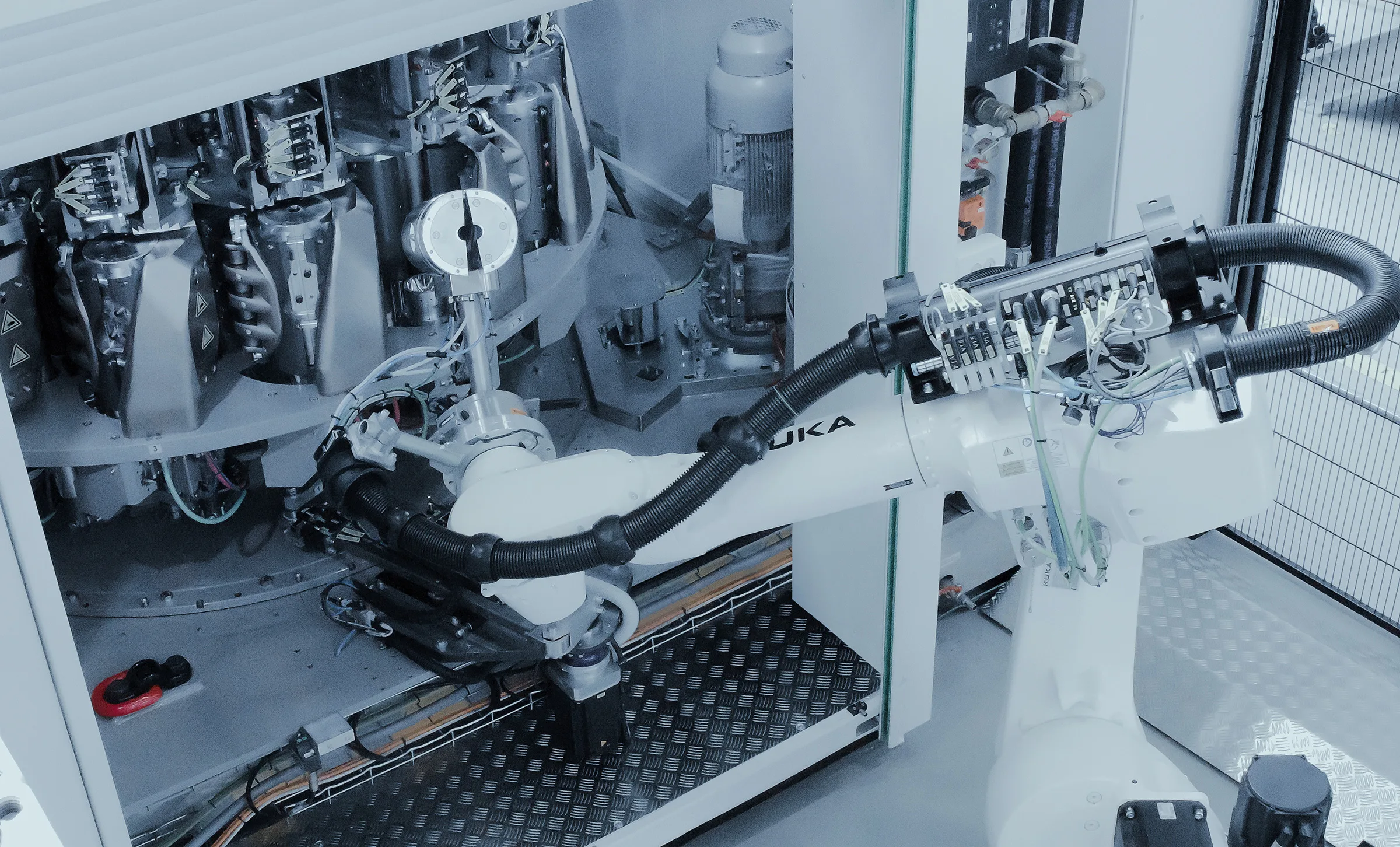
The robot needs just 41 seconds per stretch blow molding station for automatic conversion of the side mold shells and base mold during ongoing production.

You can find more information about our InnoPET TriBlock stretch blow molder/labeler/filler block on khs.com
Less manual intervention
The time and effort needed for manual work by the operator is also reduced in the labeling module. This is chiefly thanks to automatic adaptation of the label gluing height and bottle diameter. The operator still carries out the toolless changeover of the vacuum drum, brushes and bottle guide parts, however. Nevertheless, two labeling stations can now be converted within 20 minutes.
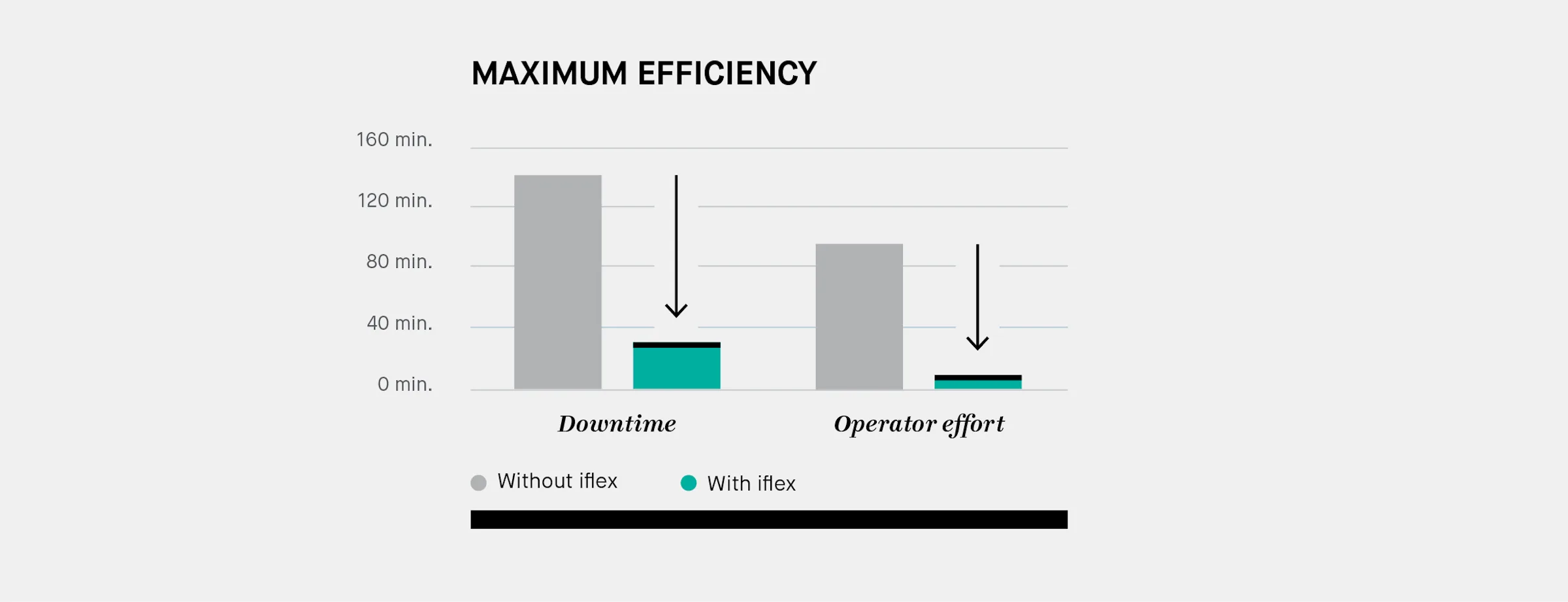
Everything under control: Innoline Flex Control
The Innoline Flex Control line management system is essential if the iflex is to function properly and its potential be fully exploited. It takes over the tasks of line and order management from the beverage producer’s ERP system and orchestrates the automatic changeover of the machines. The basic idea is to help the operator to always do exactly the right thing. By integrating the Innoline Flex Control web GUI into the HMI, data is displayed on the machine operator panel. The operator sees which processing program must be selected when and which materials are needed where to produce the respective current version of the order sequence that has been tactically planned by the system. With the automated iflex variant, this is triggered by the simple press of a button. Alternatively, on the guided iflex version the system clearly prompts the operator through the various steps and provides straightforward instructions for all action that needs to be taken manually.
At the press of a button
In the filler module conversion is fully automatic. Firstly, this avoids handling errors by the operator, and secondly, it prevents the risk of bacterial or microbiological contamination by people entering the hygiene area that would then need foam cleaning. This would delay the changeover by around 30 minutes.
The key components relevant to automatic changeovers are the guides from the filler infeed to the capper discharge that need to be set to the bottle diameter and height. Conical base guides or bottle pockets are used here, for example, where the containers are fixed by simple height adjustment as in a funnel. The discharge conveyor is vertically adjusted by a servomotor instead of being manually cranked; the same goes for the horizontal adjustment of the railings. What’s more, the bottle caps are also changed over automatically, such as when a new beverage features a different cap color from the previous one.
Up to 70% quicker
We can see just how important the new iflex options are on the KHS InnoPET TriBlock in particular when it comes to highly flexible beverage filling if we take a look at the total time saving: depending on the specific changeover routine on site, this amounts to approximately 95 minutes. The remaining manual tasks only take eight minutes on the stretch blow molding module and 20 minutes on the labeling module; on the filling module format changeovers have been fully automated and are completed without intervention in a matter of seconds.
All told, changeovers are now implemented in less than a third of the time previously required, allowing beverage producers to look forward to a high degree of flexibility and efficiency.