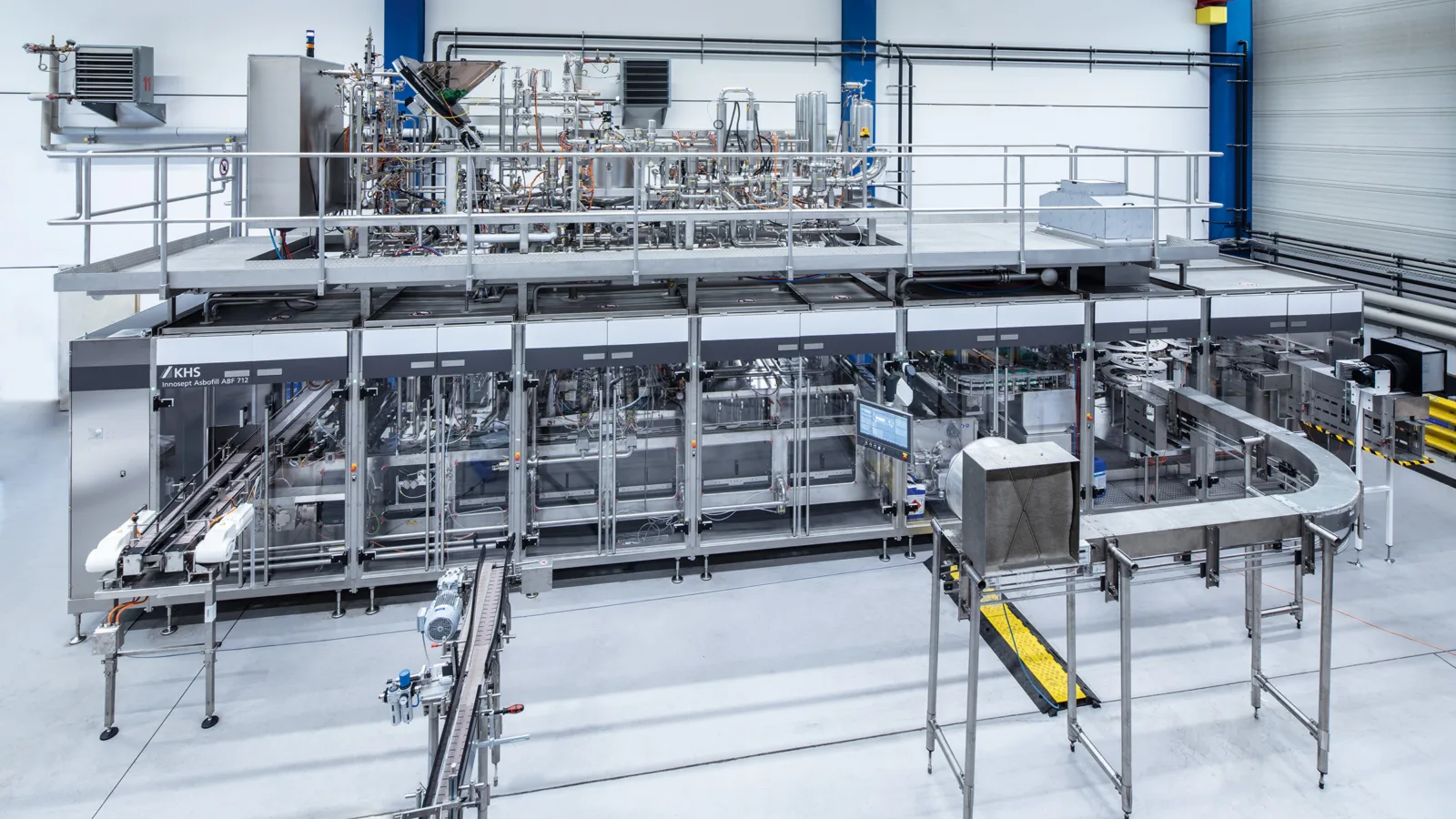
Incluso más
A menudo es la suma de cosas aparentemente pequeñas lo que tiene un gran impacto: Esto también se aplica al llenado de bebidas sensibles en botellas PET y HDPE. Con toda una gama de innovaciones, KHS garantiza una mayor eficiencia, más flexibilidad, una mayor facilidad de uso e incluso una mayor seguridad del producto.
Las bebidas mezcladas con leche, jugos, batidos, tés helados y productos saborizados están de moda, y la lista de bebidas sensibles es cada vez más larga. Demandan altos requerimientos de envasado higiénico para que el consumidor pueda disfrutarlos frescos. “Para el llenado y taponado de bebidas sin recontaminaciones, el envasado en condiciones asépticas es un proceso particularmente cuidadoso”, explica Manfred Härtel, Gerente de Producto de Envasado de KHS en Bad Kreuznach. “Para esta tecnología apenas hay alternativas. KHS es uno de los pioneros en este campo. Con más de 25 años de experiencia, somos un auténtico especialista en higiene y frescura. Esto también se expresa en el hecho de que ofrecemos a nuestros clientes todo un abanico de soluciones adaptadas a las más variadas necesidades”.
En términos de su tarea real, el envasado estéril de productos sensibles, la tecnología de KHS siempre es de vanguardia y siempre garantiza las mejores condiciones higiénicas posibles. No obstante, KHS trabaja continuamente para seguir mejorando las máquinas y los equipos. En la actualidad, un total de siete optimizaciones para las llenadoras asépticas modulares lineales KHS (para las variantes, consulte el recuadro “Eficientes y flexibles”) están ayudando a aumentar aún más especialmente su eficiencia y flexibilidad.
Nuevo - Bloque aséptico variable
Las llenadoras lineales asépticas KHS se pueden unir en bloque de forma especialmente compacta con una máquina de moldeo por estirado-soplado rotativa, en este caso con la InnoPET Blomax V. Para ello se desarrolló un módulo de transferencia que armoniza el flujo continuo de botellas PET con el proceso de llenado. Esto se hace con la ayuda de un carrusel de transferencia que divide los envases en unidades de 10 cada una. En una breve fase de parada, estas se retiran mediante pinzas y se insertan en las placas de soporte de la llenadora. El módulo existe en tres variantes: Para la unión en bloque con la máquina de estirado-soplado, con una salida adicional a la máquina de recubrimiento Plasmax, o una entrada adicional de botellas que permite que la llenadora procese botellas PET y HDPE.
Nuevo - Entrada optimizada de botellas
Con el rápido crecimiento de la variedad de formatos y diseños de botellas, también aumentan las demandas de flexibilidad del sistema. A diferencia de antes, la entrada de la botella ya no se ajusta en un proceso iterativo después de un cambio de formato mediante aflojar y apretar tornillos, probar y reajustar. Las ruedas de mano provistas con escalas permiten ajustar la altura y el diámetro del envase de forma fácil y precisa y, al mismo tiempo, garantizan que este ajuste se pueda reproducir en cualquier momento. Al cambiar el formato de la máquina, esto permite un ahorro de tiempo de hasta un 40%.
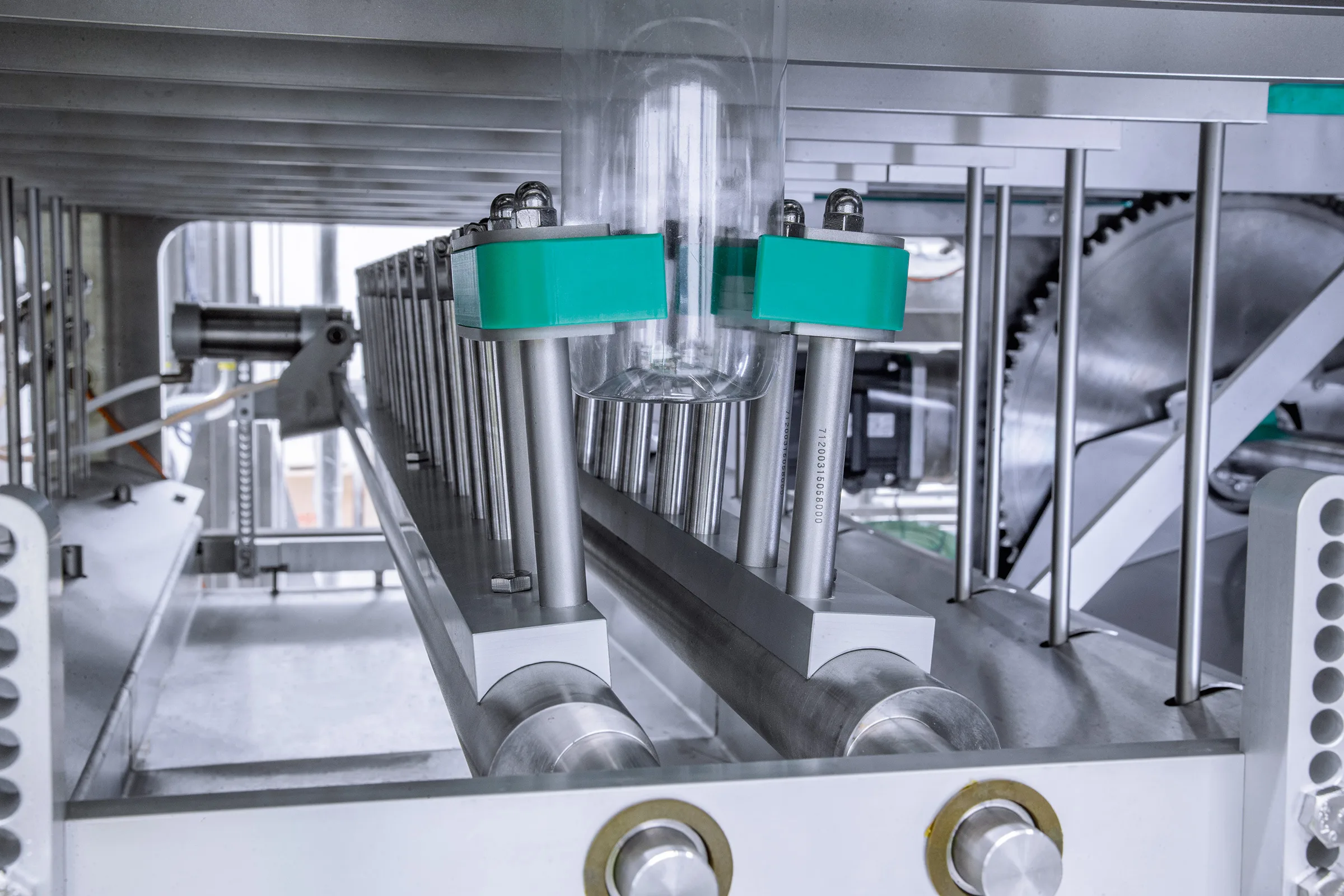
Gracias a su mayor área de contacto, las pinzas mejoradas de agarre de botellas evitan la rotación no deseada del recipiente durante el taponado.
Nuevo - Servocerrador flexible
En lugar de un accionamiento por cada diez cabezales de cerrado, ahora cada cabezal está equipado, cada uno, con dos servoaccionamientos: Mientras que el primer accionamiento sube y baja el cono taponador, el segundo accionamiento realiza la rotación para el taponado. La programación de los servoaccionamientos se realiza mediante el HMI. La automatización del cambio de formato y la reproducibilidad asociada permiten procesar diferentes cierres, y así aumentar la flexibilidad sin que el operador tenga que realizar ajustes manuales. Los parámetros necesarios para el correcto cierre de las botellas PET se almacenan en las denominadas recetas de cierre; cada cierre utilizado se puede ajustar individualmente.
Nuevo - Fijación mejorada de la botella
Para el proceso de taponado, las pinzas de agarre de las botellas fijan los envases justo por encima del piso para evitar la rotación, mientras que el cabezal taponador cierra la tapa de la botella. Los amortiguadores de goma redondos anteriores, cada uno sostenido por un brazo, ahora están siendo reemplazados por mitades de casquillos significativamente más grandes, que están unidos a dos brazos cada uno. El efecto es similar a sostener una botella con dos manos en lugar de con cuatro dedos: La superficie de contacto más grande evita de manera confiable la rotación no deseada del envase. Las botellas se cierran correctamente, el número de envases rechazados por fugas y, por lo tanto la tasa de rechazo, se reduce significativamente.
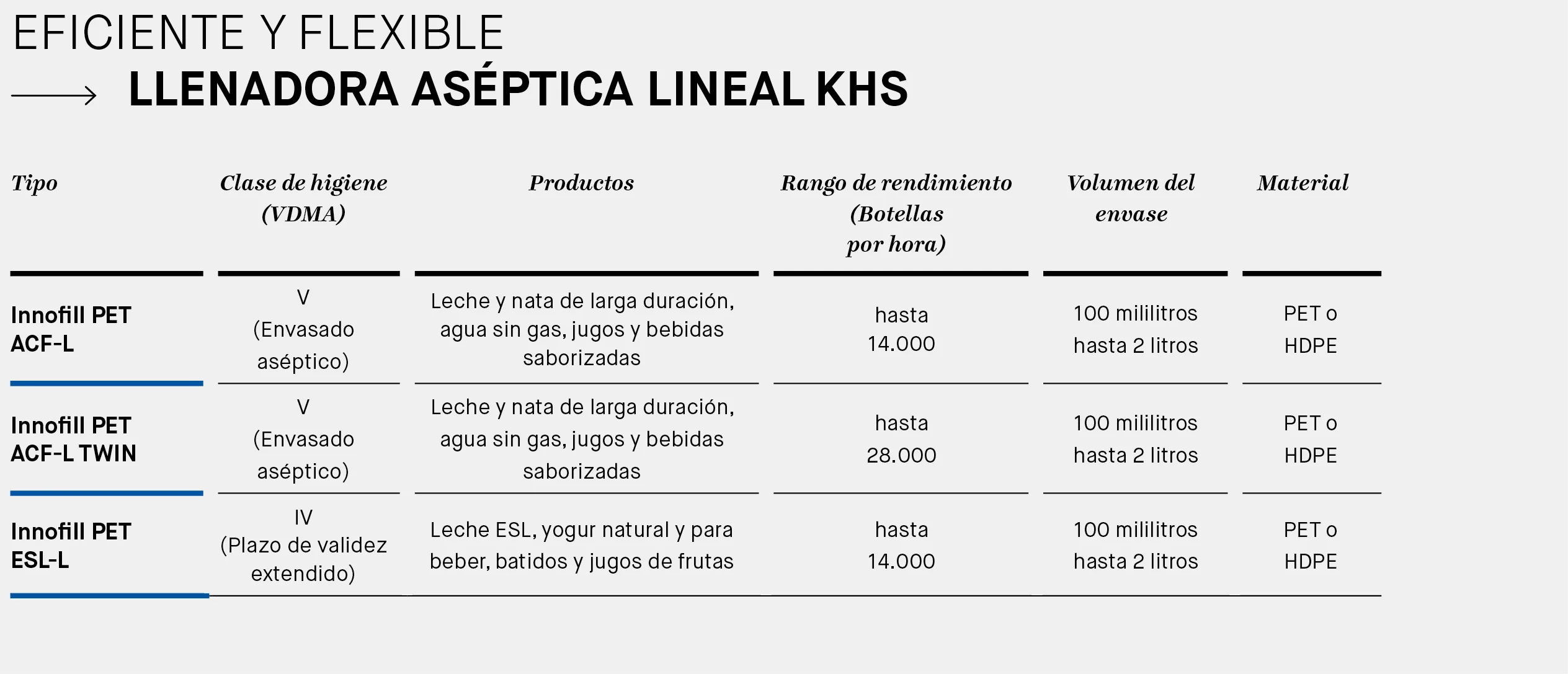
Nuevo - Comportamiento de llenado mejorado a través de válvula de conmutación
La creciente variedad de productos en la industria de bebidas significa que algunos productos son más difíciles de llenar que otros debido a su comportamiento de formación de espuma; aquí se requiere flexibilidad. Una nueva válvula de conmutación controla el volumen de entrada a la válvula de llenado propiamente dicha y, de esta manera, permite un total de cuatro velocidades de entrada diferentes. Si la entrada es más lenta o de menor volumen, la formación de espuma se reduce. La velocidad de entrada se almacena en las recetas del producto, no es necesario cambiarla manualmente. Se mejora la exactitud del llenado. Esto facilita la reproducción del volumen de llenado. La formación de espuma en la botella durante el proceso de llenado se minimiza. Esto asegura un rendimiento estable con propiedades muy diferentes de las bebidas. Como resultado, aumenta la eficiencia y la flexibilidad requerida para llenar una amplia gama de productos.
Nuevo - Nueva válvula de llenado con ranura anular para pulpa y fibras
Si el surtido lo requiere, las bebidas con fibras y pulpas se pueden procesar con la nueva válvula de llenado de ranura anular sin pérdida de rendimiento. Incluso los productos con fibras de 15 a 20 milímetros de largo y un alto contenido de pulpa pueden envasarse sin que se produzcan bloqueos ni atascos. A diferencia de las anteriores válvulas de llenado con bloqueo de gas, el cono de las nuevas válvulas está ubicado directamente en la salida para que nada salpique ni gotee. Además, el flujo de llenado se guía de manera tan homogénea y técnicamente optimizada que la cantidad de espuma generada en la botella es significativamente menor.
Nuevo - Intervalos de mantenimiento más largos
Mientras que anteriormente se requería mantenimiento a intervalos relativamente cortos desde un punto de vista microbiológico, de cinco a ocho horas cada uno, ahora los intervalos de mantenimiento se están extendiendo para que no tengan que realizarse más de una o dos veces al año. Gracias al aumento de la higiene, a la experiencia cada vez mayor en el funcionamiento de las máquinas y a los materiales modernos como el PTFE*, KHS ha podido aumentar el margen de seguridad a un nivel más sensato. Los intervalos cuatro veces más prolongados se complementan entre sí e incluyen todas las comprobaciones del mantenimiento anterior. Esto brinda a los fabricantes de bebidas una disponibilidad de las máquinas significativamente mayor y ahorros en costes de mantenimiento y revisión de hasta un 20% en cinco años.
* PTFE = Politetrafluoretileno (teflón)
»Como pioneros con 25 años de experiencia en envasado aséptico, somos verdaderos especialistas en higiene y frescura«.
![]()
Gerente de Producto de Envasado, KHS
Puede encontrar más informaciones sobre nuestras soluciones completas en el campo de sistemas asépticos en khs.com
La tecnología de llenado aséptico de KHS se complementa con una gama completa de máquinas de tecnología de procesos probadas incontables veces en la práctica: “Ofrecemos soluciones de una sola fuente”, enfatiza Härtel. “Esto abarca, por ejemplo, desde la mezcla de componentes en la sala de jarabe, la desgasificación y la pasteurización flash inmediatamente antes del proceso de llenado, hasta el dosificador de trocitos en el proceso de doble flujo”. La empresa con sede en Dortmund ofrece así toda la gama de tecnologías necesarias para la producción de los distintos segmentos de bebidas en este lucrativo mercado, desde la aceptación de la materia prima del concentrado hasta la botella.