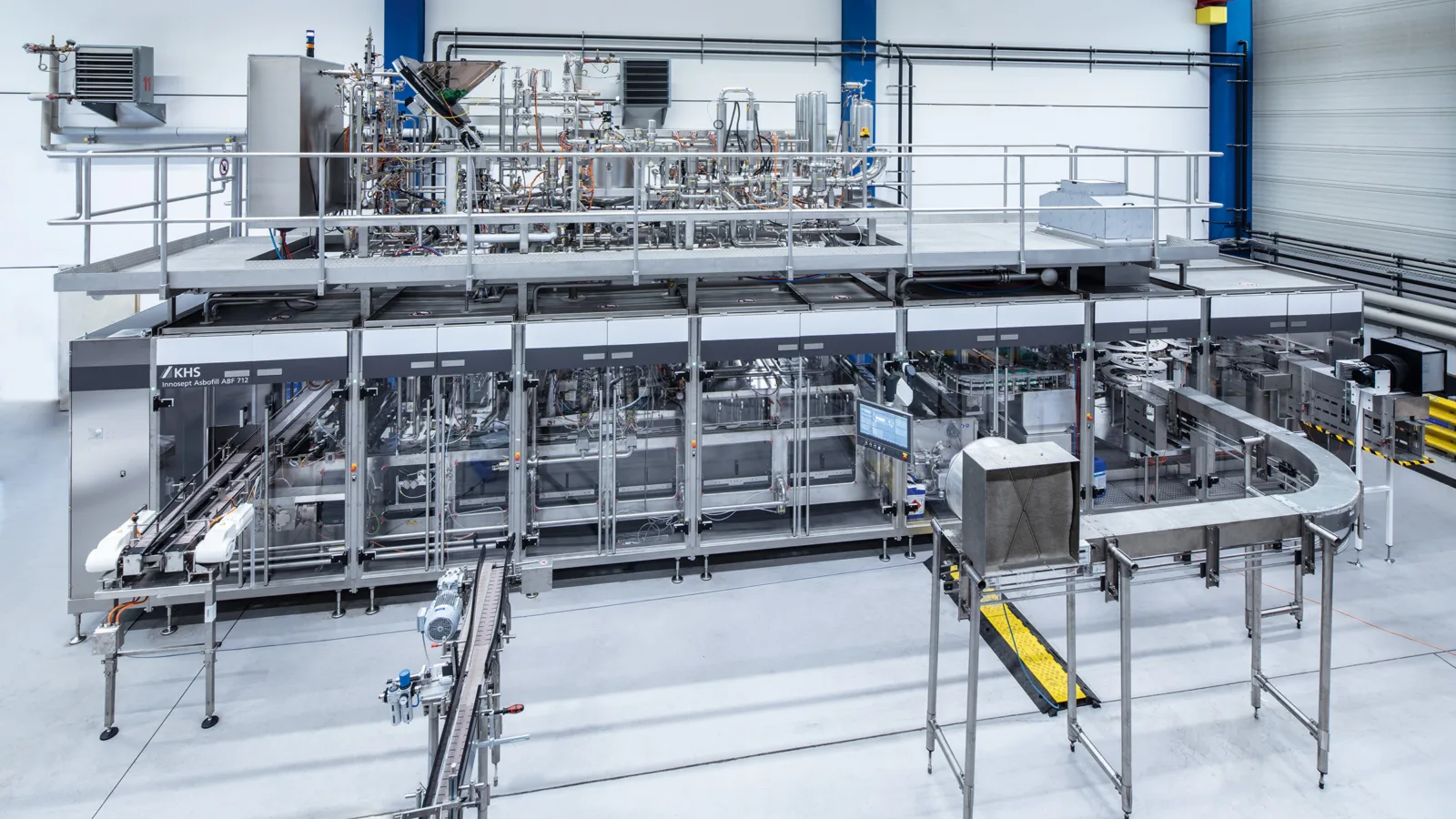
Mehr drin
Oft ist es die Summe vermeintlich kleiner Dinge, die große Wirkung entfaltet: So auch bei der Abfüllung sensitiver Getränke in PET- sowie HDPE-Flaschen. Hier sorgt KHS mit einer ganzen Reihe von Innovationen für höhere Effizienz, mehr Flexibilität, größeren Bedienkomfort und noch höhere Produktsicherheit.
Milchmixgetränke, Säfte, Smoothies, Eistees oder Near-Water-Produkte sind im Trend – und die Liste der sensitiven Getränke wird stetig länger. Sie stellen hohe Anforderungen an eine hygienische Abfüllung, damit der Konsument sie frisch genießen kann. „Für das rekontaminationsfreie Abfüllen und Verschließen von Getränken ist insbesondere die Abfüllung unter aseptischen Bedingungen ein schonendes Verfahren“, erklärt Manfred Härtel, Product Manager Filling bei KHS in Bad Kreuznach. „Zu dieser Technologie gibt es kaum Alternativen. KHS ist einer der Pioniere auf diesem Feld. Mit über 25 Jahren Erfahrung sind wir ein echter Spezialist in Sachen Hygiene und Frische. Das drückt sich auch darin aus, dass wir unseren Kunden eine ganze Palette an Lösungen bieten, die den unterschiedlichsten Bedürfnissen angepasst wurden.“
Zwar ist die KHS-Technologie hinsichtlich ihrer eigentlichen Aufgabe, dem getränkesterilen Abfüllen sensitiver Produkte, stets auf dem neuesten Stand der Technik und sorgt stets für möglichst optimale hygienische Rahmenbedingungen. Dennoch arbeitet KHS kontinuierlich daran, die Maschinen und Anlagen weiter zu verbessern. Aktuell tragen insgesamt sieben Optimierungen für die modular aufgebauten linearen KHS-Aseptikfüller (Varianten siehe Kasten „Effizient und flexibel“) dazu bei, insbesondere deren Effizienz und Flexibilität weiter zu steigern.
Neu - Variabler Aseptikblock
Die linearen aseptischen KHS-Füller lassen sich besonders platzsparend mit einer rotativen Streckblasmaschine verblocken – in diesem Fall mit der InnoPET Blomax V. Dafür wurde ein Transfermodul entwickelt, das den kontinuierlichen PET-Flaschenstrom mit dem schrittweisen Füllprozess harmonisiert. Das geschieht mithilfe eines Übergabekarussels, das die Behälter in Einheiten zu je 10 Stück aufteilt. In einer kurzen Stoppphase werden diese durch Greifer entnommen und in die Trägerbleche des Füllers eingesetzt. Das Modul gibt es in drei Varianten: Für die Verblockung mit der Streckblasmaschine, mit einem zusätzlichen Auslauf zur Plasmax-Beschichtungsmaschine oder einem zusätzlichen Flascheneinlauf, der es dem Abfüller erlaubt, sowohl PET- als auch HDPE-Flaschen zu verarbeiten.
Neu - Optimierter Flascheneinlauf
Mit der rasant wachsenden Vielzahl von Flaschenformaten und -Designs steigen auch die Anforderungen an die Flexibilität des Systems. Anders als bisher wird der Flascheneinlauf nach einem Formatwechsel nicht mehr in einem iterativen Prozess mit Lösen und Festziehen von Schrauben, Probieren und Nachjustieren eingestellt. Mit Skalen versehene Handräder erlauben die einfache und exakte Einstellung von Behälterhöhe und -durchmesser und stellen gleichzeitig sicher, dass diese Einstellung jederzeit reproduzierbar ist. Bei der Formatumstellung der Maschine ermöglicht das eine Zeitersparnis von bis zu 40 Prozent.
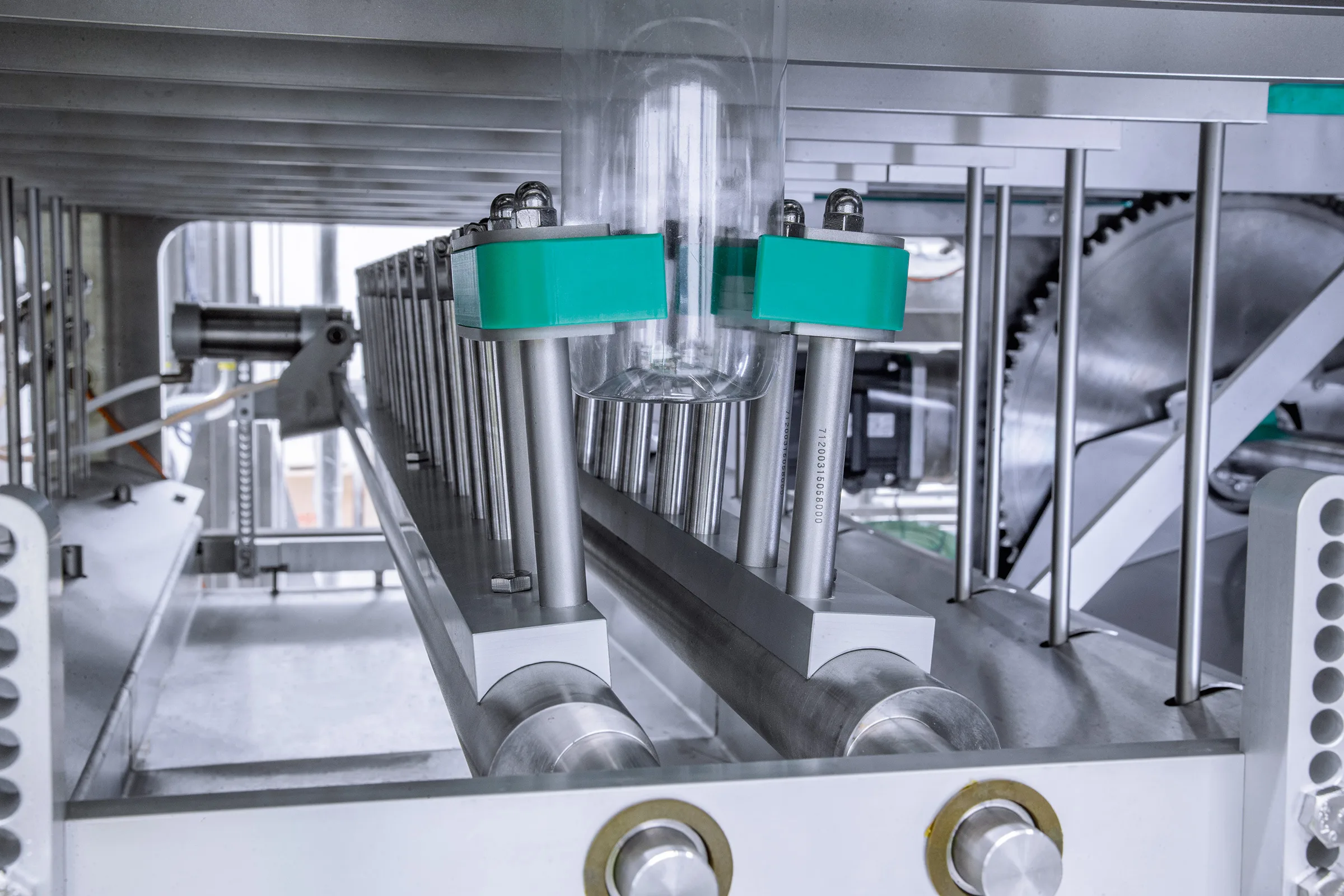
Verbesserte Flaschengreifer verhindern dank ihrer größeren Kontaktfläche eine unerwünschte Rotation des Behälters beim Verschließen.
Neu - Flexible Servoverschließer
Anstelle von einem Antrieb für alle zehn Verschließerköpfe ist ab sofort jeder Verschließerkopf mit je zwei Servoantrieben versehen: Während der erste Antrieb den Verschließerkonus hebt und senkt, sorgt der zweite Antrieb für die Verschließdrehung. Die Programmierung der Servoantriebe erfolgt über das HMI. Die Automatisierung der Umstellung und die damit verbundene Reproduzierbarkeit ermöglichen die Verarbeitung unterschiedlicher Verschlüsse und erhöhen so die Flexibilität, ohne dass ein manuelles Justieren durch den Bediener erfolgen muss. Die für das korrekte Verschließen der PET-Flaschen notwendigen Parameter werden in sogenannten Verschlussrezepten gespeichert; jeder eingesetzte Verschluss kann individuell eingestellt werden.
Neu - Verbesserte Flaschenfixierung
Die Flaschengreifer fixieren als Verdrehsicherung die Behälter für den Verschließvorgang kurz über dem Boden, während der Verschließerkopf den Flaschenverschluss zuschraubt. Die bisherigen von je einem Arm gehaltenen kreisrunden Gummipuffer werden jetzt durch deutlich größere Halbschalen ersetzt, die auf jeweils zwei Armen angebracht sind. Der Effekt ist ähnlich, als würde man eine Flasche statt mit vier Fingern mit zwei Händen festhalten: Die größere Kontaktfläche verhindert zuverlässig eine unerwünschte Rotation des Behälters. Die Flaschen werden korrekt verschlossen, die Zahl der als undicht ausgeschleusten Behälter und damit die Ausschussrate reduzieren sich deutlich.
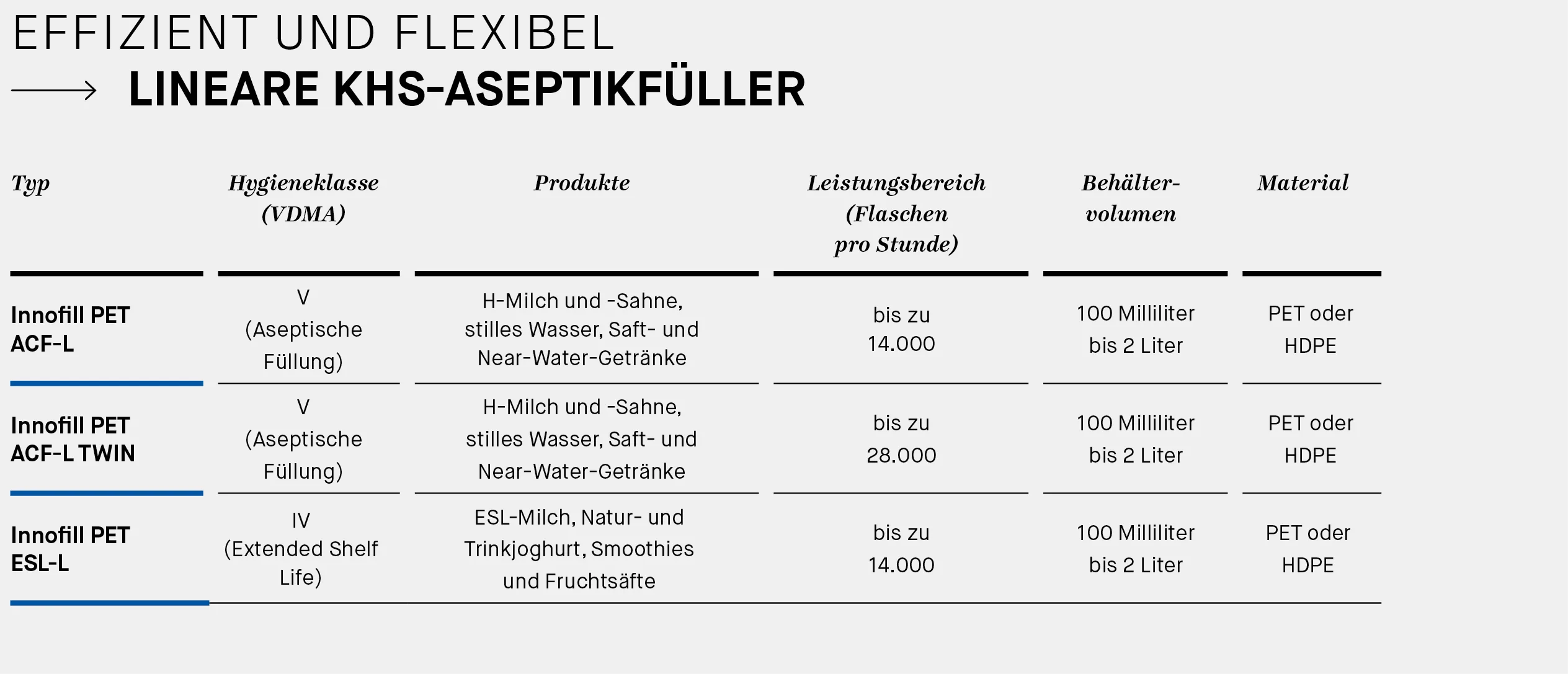
Neu - Verbessertes Füllverhalten durch Umschaltventil
Die zunehmende Produktvielfalt in der Getränkeindustrie führt dazu, dass manche Produkte aufgrund ihres Schaumverhaltens bei der Abfüllung aufwändiger sind als andere – hier ist Flexibilität gefragt. Ein neues Umschaltventil steuert das Volumen des Zustroms zum eigentlichen Füllventil und ermöglicht damit insgesamt vier verschiedene Zulaufgeschwindigkeiten. Erfolgt der Zulauf langsamer beziehungsweise mit geringerem Volumen, verringert sich das Aufschäumen. Die Zulaufgeschwindigkeit wird in den Produktrezepten hinterlegt, ein manuelles Umstellen entfällt. Die Füllgenauigkeit wird verbessert. Dadurch lässt sich das Füllvolumen einfacher reproduzieren. Die Schaumbildung in der Flasche beim Füllvorgang wird minimiert. Das sorgt bei stark unterschiedlichen Getränkeeigenschaften für eine stabile Leistung. In der Folge erhöht sich die Effizienz, und die für die Abfüllung eines breiten Sortiments erforderliche Flexibilität steigt.
Neu - Neues Ringspalt-Füllventil für Pulpe und Fasern
Wenn das Portfolio es erfordert, können mit dem neuen Ringspalt-Füllventil Getränke mit Fasern und Pulpen ohne Leistungseinbuße verarbeitet werden. So lassen sich selbst Produkte mit 15 bis 20 Millimeter langen Fasern und hohem Pulpenanteil abfüllen, ohne dass es zu Blockierungen oder Verstopfungen kommt. Anders als bei den bisherigen Füllventilen mit Gassperre sitzt bei den neuen Ventilen der Ventilkonus direkt am Auslauf, sodass nichts spritzt oder tropft. Zusätzlich wird der Füllstrahl so homogen und strömungstechnisch günstig geführt, dass in der Flasche deutlich weniger Schaum entsteht.
Neu - Längere Wartungsintervalle
Waren bisher unter mikrobiologischen Aspekten in relativ kurzen Abständen Wartungen erforderlich, die jeweils fünf bis acht Stunden in Anspruch nahmen, werden die Wartungsintervalle jetzt so verlängert, dass diese nicht häufiger als ein- bis zweimal pro Jahr stattfinden müssen. Dank fortschreitender Hygiene, zunehmender Erfahrung im Betrieb der Maschinen sowie moderner Werkstoffe wie PTFE* hat KHS das Sicherheitspolster auf ein sinnvolles Maß reduzieren können. Die auf das Vierfache verlängerten Intervalle bauen aufeinander auf und schließen alle Überprüfungen der bisherigen Wartungen mit ein. Das bringt den Getränkeherstellern eine deutlich höhere Maschinenverfügbarkeit sowie eine Wartungs- beziehungsweise Überholungskostenersparnis von bis zu 20 Prozent innerhalb von fünf Jahren.
* PTFE = Polytetrafluorethylen (Teflon)
»Als Pionier mit 25 Jahren Erfahrung in der aseptischen Abfüllung sind wir ein echter Spezialist in Sachen Hygiene und Frische.«
![]()
Product Manager Filling, KHS
Komplementiert wird die aseptische Fülltechnik von KHS durch ein umfassendes und in der Praxis zigfach bewährtes Portfolio an prozesstechnischen Maschinen: „Wir bieten Lösungen aus einer Hand“, betont Härtel. „Das reicht zum Beispiel von der Ausmischung von Komponenten im Sirupraum über die Entgasung und die aseptische Kurzzeiterhitzung unmittelbar vor dem Abfüllvorgang bis hin zum Stückchendoseur im Zweistromverfahren.“ Das Dortmunder Unternehmen stellt damit die gesamte Bandbreite an Technologien bereit, die zur Herstellung der zunehmend gefragten Getränkesegmente in diesem lukrativen Markt erforderlich sind – von der Rohstoffannahme des Konzentrats bis in die Flasche.