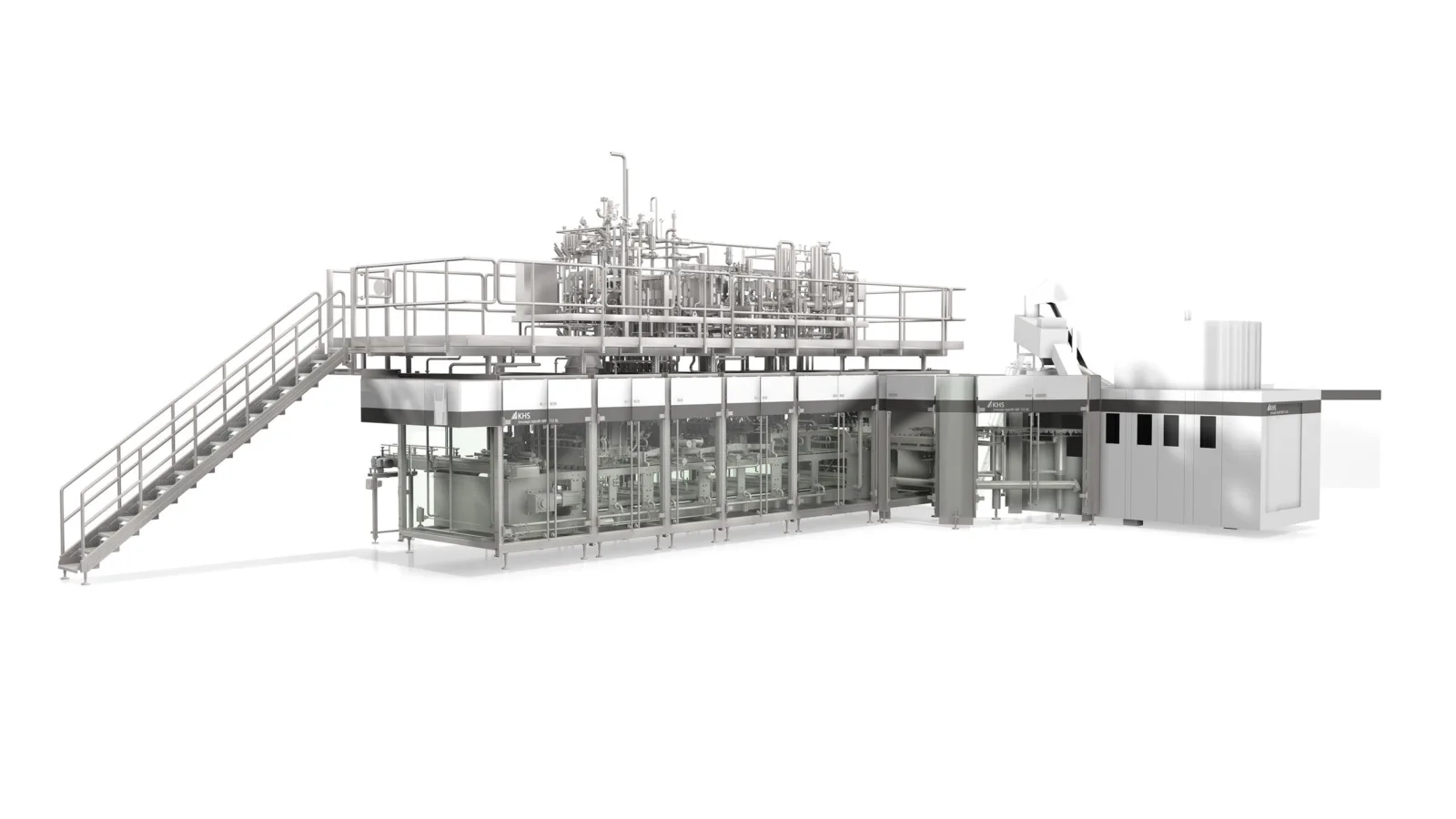
Triple bonus
Expert for the hygienic filling of sensitive beverages KHS now presents its aseptic linear machine as a block concept. / The new development provides a triple bonus, with each of the three technical highlights giving operators greater microbiological safety and more flexibility.
With its Innosept Asbofill ABF machine KHS supplies a tried-and-tested linear filling system for hygienic filling in the medium capacity range. Three new developments have now made this proven plant engineering more powerful than ever before:
- A new transfer module enables it to be blocked with a standard KHS stretch blow molder.
- A modular system permits various modules to be retrofitted or replaced at a later date.
- The first chunk filler for the aseptic area from KHS can fill bigger particles than was the case to date, thus giving users maximum flexibility when designing their products.
With its enormous flexibility the Innosept Asbofill ABF is up to the minute: with ever larger product varieties and increasingly smaller batch sizes the number of product changeovers is on the rise. The great diversity of products, such as juice, iced tea, near-water beverages, milk and mixed milk beverages, and huge range of containers in use call for systems which can quickly and easily adapt to the manifold demands of beverage producers.
A new transfer module forges a basic link between the rotary stretch blow molder and the linear filler. In this development the continuous rotational motion of the stretch blow molder had to be converted into the linear, step-by-step cyclic movement of the filler. With this specific challenge mastered, the innovative block system now rounds off the KHS portfolio for sensitive products.
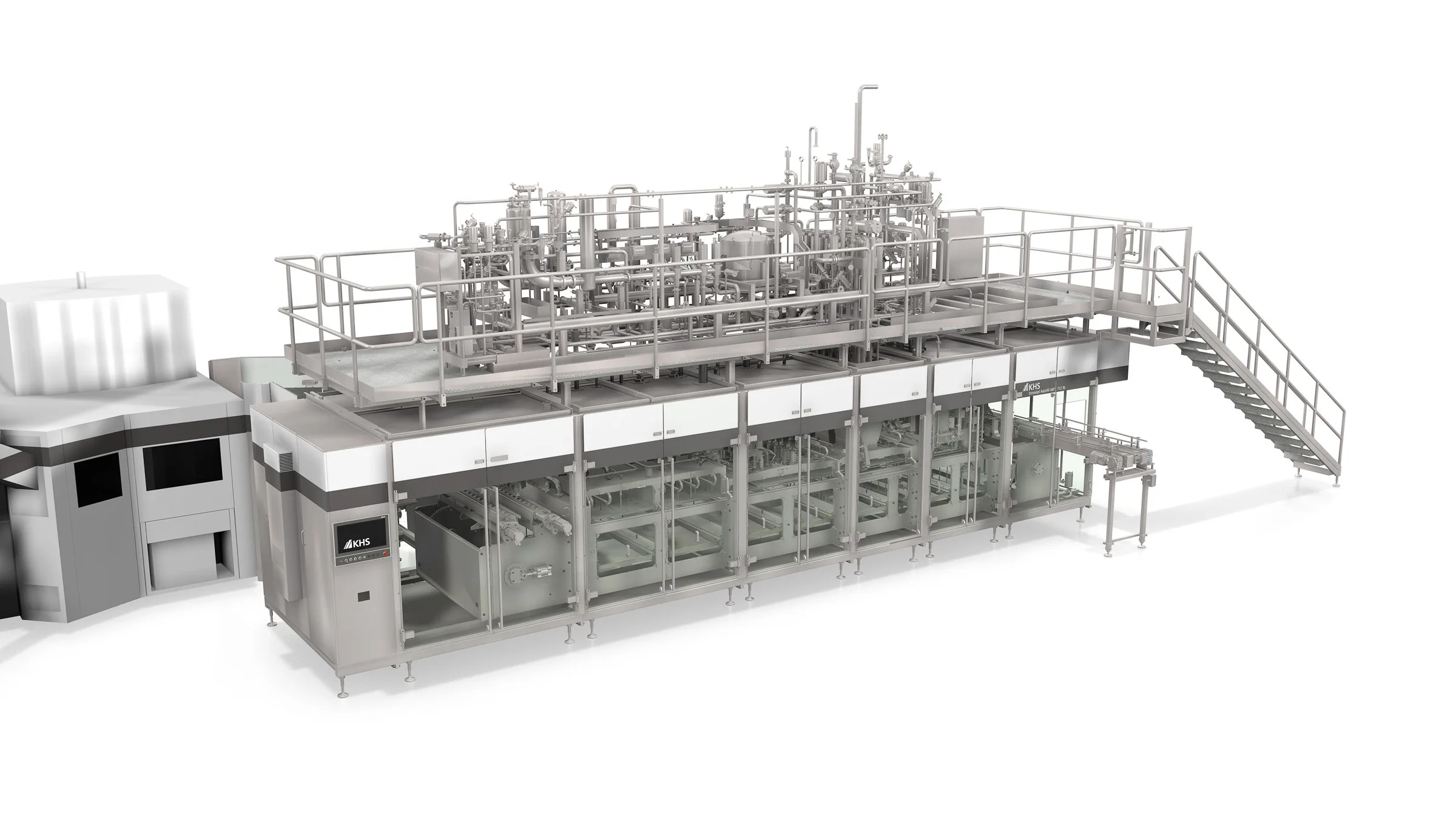
The valve manifold and sterile air filter have been placed at the top of the system to keep the space required for the sterilization unit, filler and capper as small as possible.
Enormously flexible
The Innosept Asbofill module can be varied according to the bottler’s requirements and product range. The base machine with its respective sterilization, drying, filling and capping modules can be easily and cost-effectively retrofitted with further units at a future point in time. Feasible options include a second filling module to boost capacity when running larger container volumes or an extra capping module for foil seals. A dosing module can also be installed as an addition or alternative to the classic filling system. The system’s great flexibility permits fast format changeovers within the space of just five to ten minutes or product changeovers in only thirty minutes. This system is therefore qualified to process a multitude of different products – regardless of their consistency, the bottle geometry, container volume and type of cap.eren Konsistenz, der Flaschengeometrie, dem Behältervolumen oder der Art des Verschlusses.
Flexible and low on space
- For VDMA hygiene classes V (aseptic filling) and IV (extended shelf life): 12,000 bottles per hour (Twin version: 24,000 bottles per hour)
- Container volumes from 100 milliliters to 3 liters, made of either PET or HDPE
- With flat caps, sports caps or foil seals – can also be combined within one machine
- Aseptic zone measures just 1.5 cubic meters
Trend for chunks
In many bottlers’ steadily augmenting product ranges there is a discernible trend towards ever larger chunks – not just in food such as soups, sauces and preserves but also in beverages and milk products. Depending on the size of the fibers or chunks various filling systems are needed to add these products. Juice producers, for example, usually fill their entire portfolio using what’s known as a pulp nozzle which can process a fiber and particle content of about 10%, fiber lengths of 15 millimeters and chunks with crushable particles measuring 2 x 2 x 2 millimeters. Dairies, on the other hand, mostly use a standard nozzle which permits a product viscosity of up to 1,000 millipascal seconds. This is more or less equivalent to the consistency of a drinkable yogurt.
The new chunk filler is the right option for all thicker products with a viscosity of up to 3,000 millipascal seconds – such as set yogurt, quark, syrup and honey – and for chunky products. The dosing unit, based on tried-and-tested design engineering, can manage particles with a length of up to ten millimeters; this includes chunks of peach, whole cherries and strawberries. Ultimately, all that limits the size of the chunks to be processed on the new chunk filler is the diameter of the bottle neck.#
The Innosept Asbofill ABF now provides two basic means of adding solid particles to a liquid: either a fully mixed product is filled – in which case the chunk filler is used in place of the normal IFM*-based filling system – or chunks are added upstream, as is the case with milk products, for instance, where the fruit mix first has to be shaken up from the base of the bottle by the consumer just before drinking and is then mixed with the yogurt, for example. With the latter method the chunk filler has to be integrated before the standard filling system.
* IFM = inductive flow metering
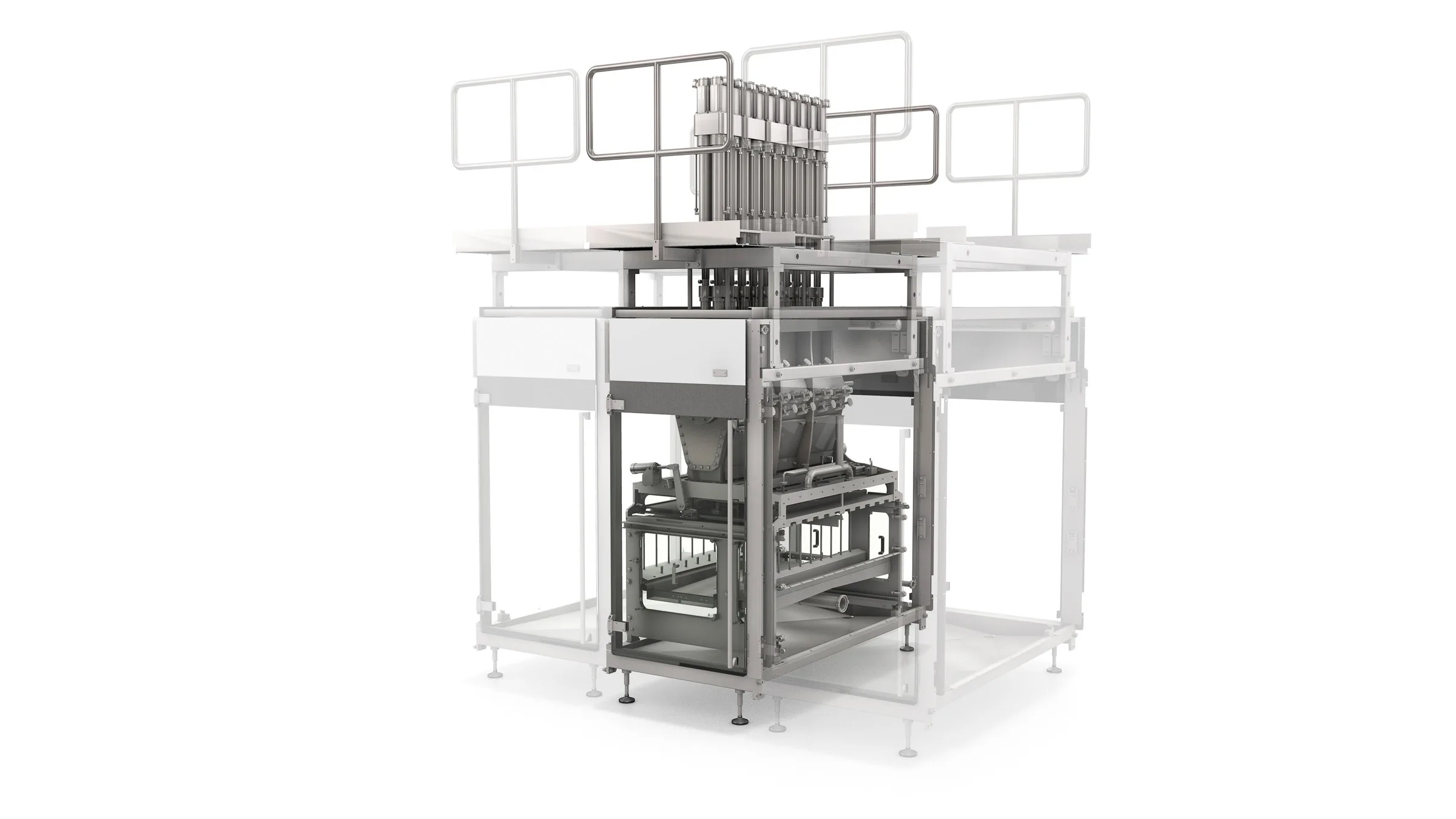
The chunk filler can process peach chunks, whole cherries and strawberries. The chunk size is limited by the diameter of the bottle neck alone.
Minimum aseptic zone
All told, the new Innosept Asbofill ABF scores with the same hygienic safety naturally found throughout the entire KHS aseptic portfolio. Thanks to neck handling, which at the same time gives users maximum freedom of design regarding the bottle shape, the dimensions of the aseptic zone can be kept down to an absolute minimum. Even in the variant with the highest capacity this only takes up 1.5 cubic meters of space. This makes the linear platform clearly superior to larger rotary systems, especially for smaller batches and in a capacity range of up to 12,000 bottles per hour. This superiority is further underlined if we look at the system’s flexibility: format changeovers on the Innosept Asbofill ABF are quick and simple as only a single drawer has to be replaced, leaving the aseptic zone untouched.