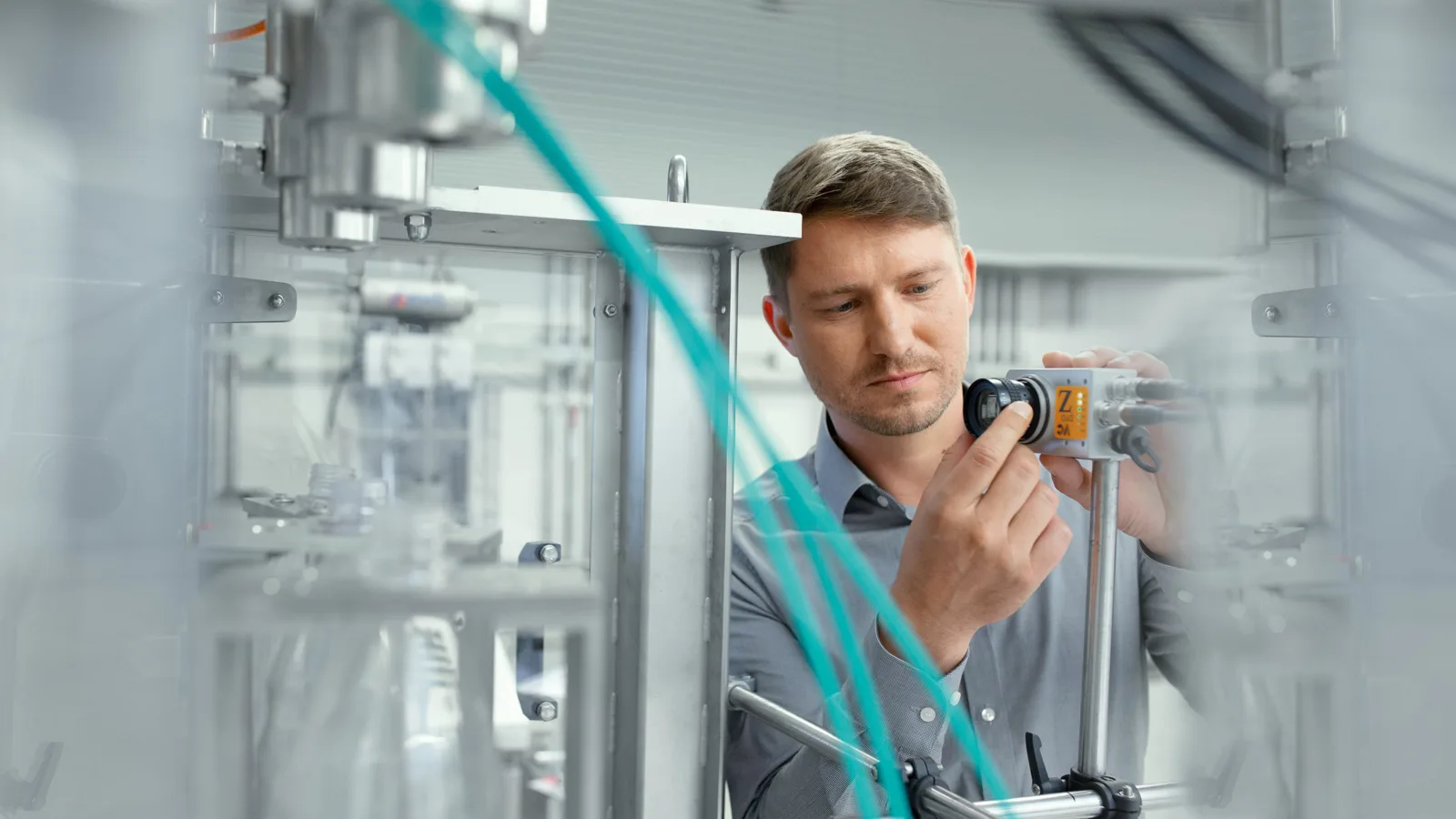
The future of filling
When Jochen Ohrem in Bad Kreuznach initiates a new research project, things promise to be exciting. What’s then produced in cooperation with various powerful partners is often an innovative and pioneering achievement – as is the case with the intelligent filling valve.
In the rapid advance of digital technology the term “Industry 4.0” has become something of a buzzword over the past few years. While initially the aim of establishing Germany as a center of technology and making it fit for the future was more of a political endeavor, industry itself is now increasingly addressing this concept. Universities and universities of applied sciences have since also joined the throng in order to turn their innovative technological ideas into practical applications shoulder to shoulder with business, trade and industry. This is often realized in the form of funded projects tendered by the German Federal Ministry of Education and Research (BMBF), for example, with subsidies of up to 50%.
KHS also takes part in research projects such as the above in an attempt to push the digitalization of the beverage industry. One of these recently concerned filling. Here, the status quo of the filling process was first described and a scenario created as to how this could be usefully further developed in the sense of Industry 4.0. Jochen Ohrem, expert of R&D Management in Bad Kreuznach, Germany, told us what the aim of the project was. “When we started out in 2015, we wanted to raise flexibility and energy and resource efficiency in production processes to new heights with the help of an intelligent control and network system. In doing so, special attention was to be paid to the electronics and sensors.” The title of the project sounded just as sophisticated: “sensor-based subsystems with decentralized cooperation for Industry 4.0 production systems” or DnSPro for short.
»You can chieve more by also thinking outside the box occansionally.«
![]()
Expert of R&D Management at KHS
Profile: Jochen Ohrem
The PhD chemist from Frechen studied bioengineering in Aachen and plant and process engineering in Cologne. His studies centered on process analysis technology, which was also the focus of his thesis. What particularly fascinates him about process engineering is communication between the various disciplines, such as electronics, control engineering, measurement technology, chemistry and mechanical aspects. He has worked for KHS since 2014. One of his first tasks at the company was to identify projects eligible for BMBF funding and put together suitable consortia. Since 2018 the 38-year-old has coordinated the R&D Management Department at KHS, a staff unit which cooperates closely with the company’s research and development departments.
One for all
The underlying task of the project was to engineer a self-learning filling valve. To date, depending on the beverage and container around 20 different types of filling valve with a high variance are used. This had to change, Ohrem emphasizes. “We wanted to develop a single valve which can fill all kinds of product into all kinds of container without the operator having to make any adjustments. We made use of cyber-physical systems (CPS*) for this purpose, with the help of which the valve could determine how to best fill a certain beverage into a certain container as quickly as possible.”
*Cyber-physical systems (CPS) = group of software components with mechanical and electronic parts which communicate via a data infrastructure.
In this context a camera acts as a sensor. During the filling process the inclusion of bubbles and foaming are observed and evaluated to prevent excessive foaming and thus product loss. With the help of microcontrollers and the camera’s evaluation electronics, the filling valve is opened to varying degrees by a stepper motor depending on the fill level, initially at first in ‘training sessions’ with autonomous emptying and filling. The focus was on ‘learning’ a number of skills: self-configuration, analysis and self-diagnosis and, ultimately, self-optimization. To put it more simply, by applying an autodidactic system of artificial intelligence mechanical complexity and manual interventions are supplanted by minimum effort for operation and maintenance.
Interdisciplinary team
Besides KHS a total of six further partners contributed their expertise to the project which was sponsored by the BMBF. Chip manufacturer Infineon from Neubiberg was the specialist for electronic hardware and WIBU Systems from Karlsruhe was responsible for software security – an important aspect when networking digital components (see “Full security” on page 32). Finally, EPOS from Duisburg contributed a number of electronic components and circuits. On the scientific front the project was supported by IT specialists from two universities: the Ruhr University in Bochum and the Ostwestfalen-Lippe University of Applied Sciences in Lemgo. The group was coordinated by KROHNE Innovation from Duisburg, a supplier of sensors and measuring equipment and long-term partner of KHS. “The project team members covered a large number of different disciplines,” Ohrem recalls. “As an engineering company KHS naturally concentrated more on the mechanical than on the electronic aspects. Working together as a team the integration of the electronic components proved extremely successful.”
Networking had top priority in the DnSPro project. First and foremost, this included the many electronic interfaces in the automation pyramid. Links had to be created between the sensors, actuators, microcontrollers and field-programmable gate array (FPGA)**. These had to be networked with the programmable logic controller (PLC) and the higher operator level (HMI) and it had to be possible to access the Internet.
**Field-programmable gate array (FPGA) = an integrated circuit in digital technology into which a logic block can be loaded.
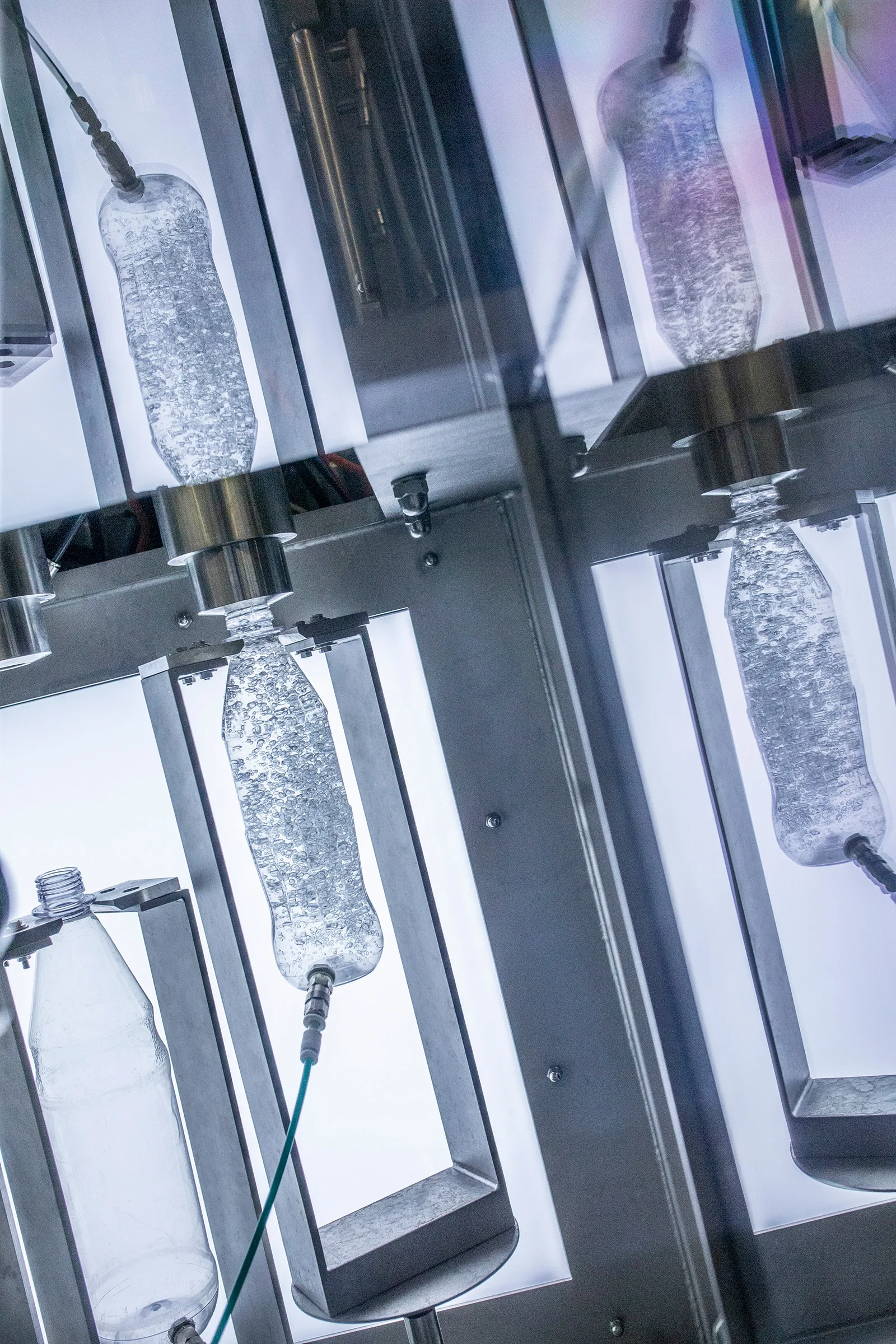
During filling the inclusion of bubbles and foaming are detected and evaluated by a camera.
Feasible and marketable
Asked what the probability is of the research project one day producing a marketable project, Ohrem fires off an immediate answer: “one hundred percent. From a scientific point of view, we could oversize a playground like this and equip it with everything that’s doable – even if later on no customer would ever need such a high level of complexity or want to pay for it. But of course we specifically check what’s actually feasible and marketable. Based on various aspects of our prototype we’ve already launched a number of development projects which focus on implementation in practice.”
One of the topics derived from the project which is currently being studied in greater depth is a decentralized controller for filling machines, for instance. In place of a superordinate filling computer centrally positioned on the machine that regulates the process of all valves, in the future this task can be managed locally by miniaturized computers installed on each valve group or valve. This would allow a pressure sensor to be inserted into each filling valve which would document and analyze the pressure curve. Because this would greatly reduce the amount of wiring involved, this would also result in a number of cost and time benefits, such as during commissioning.
In addition to the specific development projects which have stemmed from the test filler, Ohrem sees a further central use for DnSPro. “For me, DnSPro is a real showcase project when it comes to turning research carried out at universities into an application that is practically viable. This clearly shows that sometimes you can achieve a great deal more by changing your perspective and thinking outside the box instead of religiously pursuing your chosen objectives step by step.”