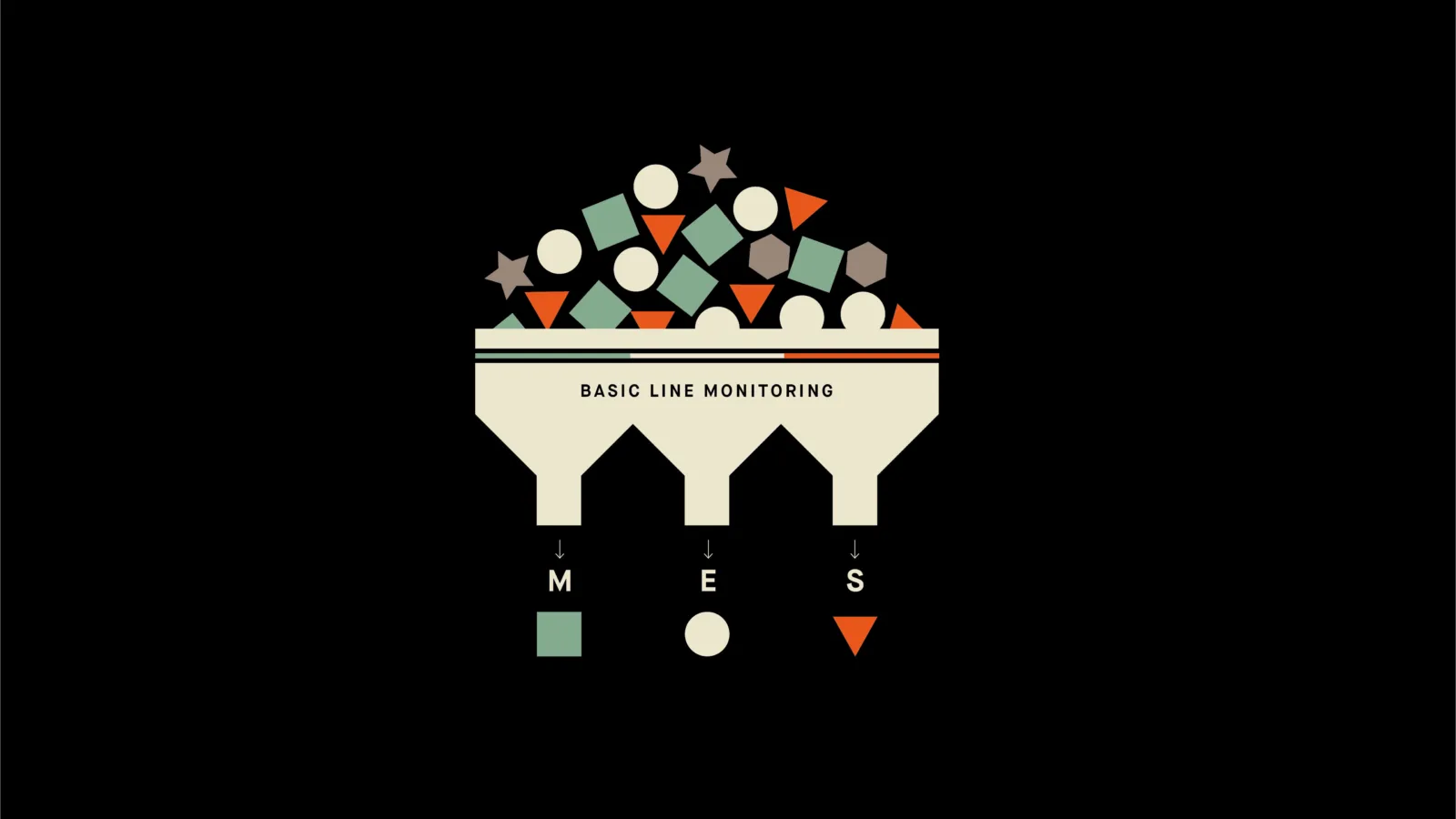
Purely and simply good
Basic Line Monitoring from KHS, a new web app based on Innoline MES, is intuitive and easy to use. It allows operators and shift supervisors to concentrate solely on the data needed to assess the efficiency of their lines.
The modular Innoline MES* production management system from KHS is software which has been specifically tailored to the requirements of the beverage industry. It provides greater transparency in line monitoring and order management and performs control functions on the line. The IT system includes a total of six modules with various functions which can either operate as stand-alone units or be used in combination.
*MES = Manufacturing Execution System, the process-related execution level of a multilevel production management system.
Based on Innoline MES KHS has now developed a Basic Line Monitoring (BLM) app. It’s convincing on two counts: firstly, it’s the first product to be placed on a new, web-based Innoline MES 2.0 platform – a further development which requires less configuration effort and to which the other modules can also be successively adapted. Secondly, BLM only focuses on the data points which are needed to assess line efficiency and detect any sources of loss. The system therefore helps KHS commissioning engineers and site managers to make ramp-ups more efficient and makes it easier for customer operators and shift supervisors to quickly identify weak points or causes of any loss in performance. Users at operator level are only given the information they need to perform their tasks.
»Our BLM app allows you to take in the really important values at a glance without having to laboriously search for them.«
![]()
Innoline MES product expert at KHS
Intuitive and easy to use
The web-based, responsive user interface provides great ease of operation. Data can also be viewed on mobile devices; this gives operators greater freedom of movement than on the stationary HMI operator panel (Human Machine Interface) – which nevertheless still has its credentials as here, directly on the machine monitor, BLM screens can also be displayed.
Where the use of Innoline MES modules and access to individual applications and information required operators to navigate their way through relatively complex menus to date, operation of the BLM app is intuitive. Starting with a block diagram of the entire line, the module enables users to explore the various details in greater depth using touch drill downs.
A clearly structured status summary, for example, plainly shows which faults on upstream or downstream machines cause the filler to stop production. This allows operators to concentrate on disruptions which are critical to the line’s performance instead of working their way through a clutter of error messages.
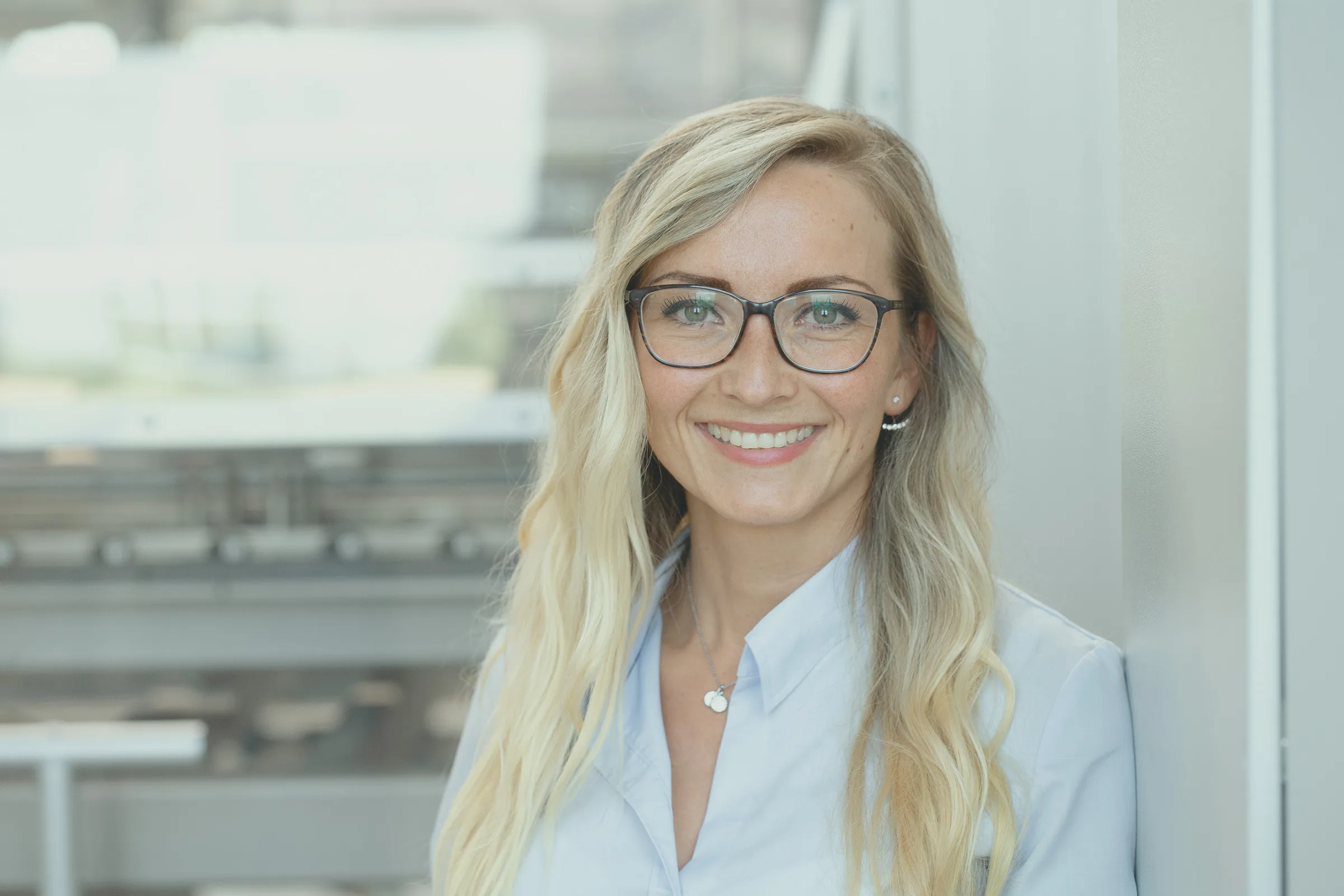
Continuous coordination between OT, IT and Commissioning is important, believes Meike Schulz who is responsible for OT security at KHS.
Less is more
Based on the data recorded the BLM module computes the line performance and distinguishes between internal and external reasons for the originators. This means that both the performance of the line as a whole and of KHS’ scope of delivery can be calculated. The most important
- process data (inferences as to quality)
- product counters (good and bad quantities)
- consumption meters (TCO) and
- external failures (e.g. supply of materials) are logged.
According to Wolfgang Heßelmann, the product expert responsible for Innoline MES at KHS, the charm of Basic Line Monitoring lies in its focus on the essentials and its irresistible simplicity. “Our BLM app allows you to take in the really important values at a glance without having to laboriously search for them. Because the module is web based, you don’t have to install any software on the computer. All the customer needs is a link to a website; he or she can then control who has access to the data and who doesn’t.” With this the system can also be viewed outside the line, the customer’s IT setup permitting. Only information is stored on the website and no functions, however. This means that the risk of cyberattacks in this context is manageable.
*Survey by Germany’s Federal Office for Security in Information Technology (BSI), May 2019.
**OT = operational technology
***IEC 62443 = series of international standards governing industrial communication networks – network and system IT security.
Full security: Protection against cyberattacks
As digitalization advances so, too, does the risk of attacks from the Internet – also on plant engineering networks. What is KHS doing as a manufacturer and integrator to ward off the danger to lines and machines and what responsibility does the customer have as the user?
In 2018 every third company was affected by cybersecurity incidents in Germany alone* – some with drastic consequences. In 87% of the cases operations were disrupted or failed. Despite this only 47% of companies pursue a holistic security concept.
*Survey by Germany’s Federal Office for Security in Information Technology (BSI), May 2019.
These figures are alarming, thinks Meike Schulz, who is responsible for OT** security in KHS’ Line Engineering Product Support Department. As opposed to IT Security, which manages the security of Office applications, her department is concerned with the safety and availability of all network subscribers on a production line. “Data security in production has been an issue for some time now,” explains Schulz. “However, the problem only really flared up in 2017 when Wannacry malware launched a huge cyberattack on over 230,000 computers in 150 different countries. Since then this topic has been a major concern – also for our customers.”
**OT = operational technology.
Schulz and her team constantly analyze and discuss potential weak spots and risks. She and her colleagues derive technical and organizational security measures from Regulation IEC 62443***. These include, for example, reworking contractual regulations, requirements for third-party equipment and guidelines and training courses for service engineers to heighten awareness for security issues.
***IEC 62443 = series of international standards governing industrial communication networks – network and system IT security.
Whitelisting
One measure is whitelisting for Windows-based systems or the restrictive assignment of authorizations for applications. Blocking unauthorized applications hardens the system: malware then can’t install itself on the system. OT is, however, also linked to customer networks – such as for the transfer of information to logistics, ERP and PDA systems – and to external data media and laptops. The more interfaces there are, the greater the risk of attack. Responsibility for OT security falls onto several shoulders: both KHS as a manufacturer and integrator and the customer have obligations. As the user of the machinery the latter holds long-term – and thus the greatest – responsibility. “We have to work closely together to effectively counteract OT security risks,” Schulz sums up. “KHS security measures help to minimize the risk of a cyberattack and provide production systems with suitable protection. They thus contribute to the customer’s overall security concept.”
Fast reaction
Heßelmann considers BLM to be useful on two levels. “On the one hand, the line can be brought up to capacity more quickly if operators can quickly identify where the bottlenecks are and react promptly and accordingly. On the other, an immediate analysis can be made as to the impact a fault has on the performance of all devices that support display of the web client.”
Another advantage of BLM is its report function. Here, too, standardized displays and a focus on the essentials make BLM an easy to use tool. Standard reports are automatically generated as a PDF without the necessity of manual filtering. After each shift a report can be immediately opened in the web browser with a simple click. If a distribution list of responsible project managers for both the customer and KHS is stored in the system, if required the BLM app can automatically send emails containing shift or weekly reports.
“We’ve updated our data interface in order to implement Basic Line Monitoring,” explains Heßelmann and promises that “In the future every KHS machine will have a suitable interface so that it’s compatible with BLM.”
Any further questions?
Wolfgang Heßelmann
Product Expert für das Innoline MES bei KHS
+ 49 231 569 1612 wolfgang.hesselmann@khs.com