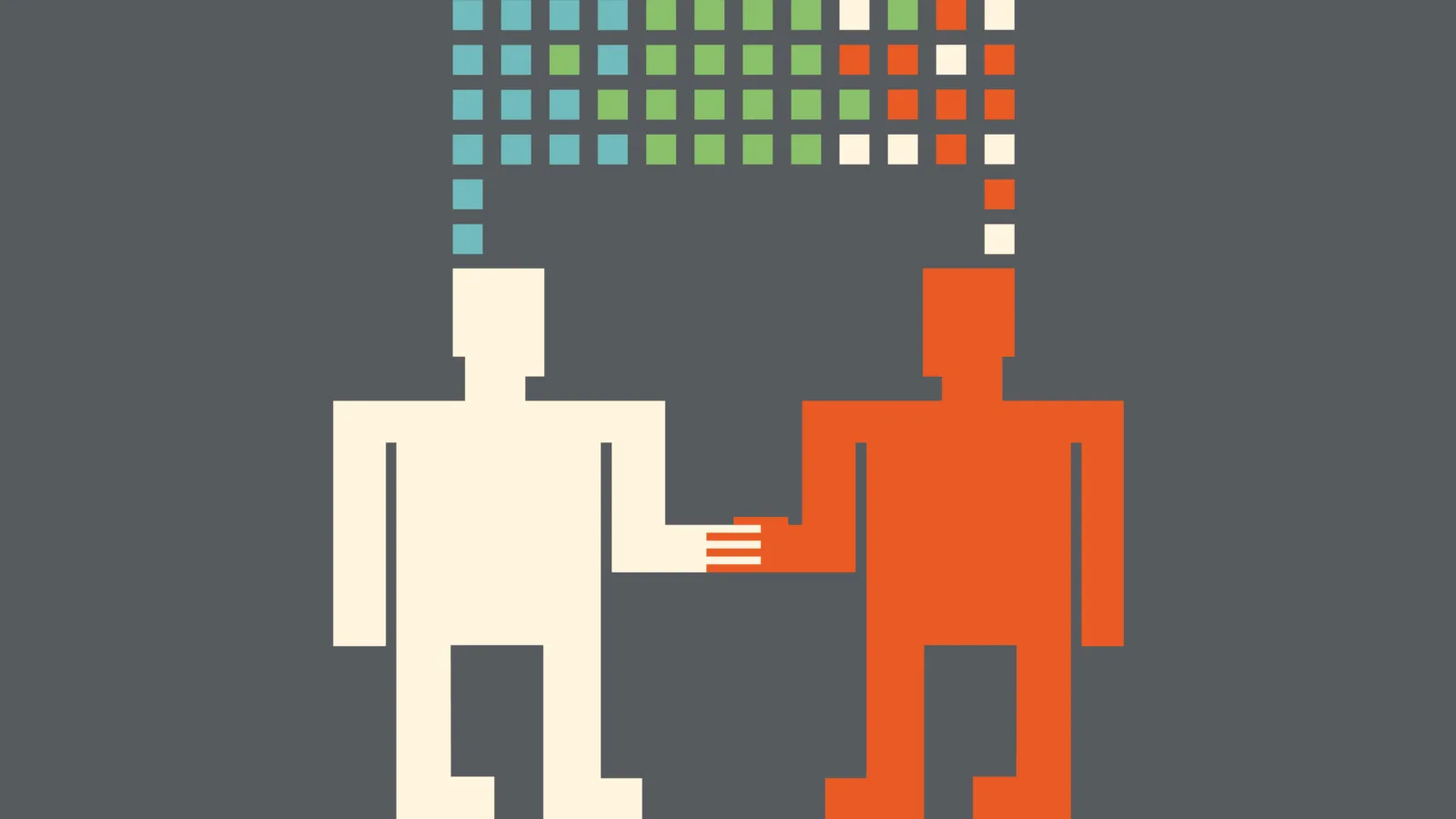
Mutual understanding
With its new standard interfaces KHS facilitates and optimizes communication between its machines and beverage producers’ MES systems – regardless of the supplier of the latter. This saves time and money during commissioning and also improves the quality of data.
In the day and age of the smart factory lines and machines must be able to communicate with the IT systems of their operating company. This also applies to the beverage industry, where reliable data transfer is essential for two main reasons: firstly, this affects line monitoring that creates transparency with regard to line performance. Here, information on the state of each individual machine enables conclusions to be drawn as to how smoothly a line is running, where exactly any possible faults could or do occur and which resources are being and have been used. Secondly, a functioning exchange of data is conditional for an increasing degree of automation in order management. This chiefly refers to the fulfillment of orders defined in the IT system by the machines. Their data-based control unit facilitates material handling, for instance, by helping the operator to ensure, through the provision of bills of materials and material conveying orders, that everything needed for production is in the right place at the right time.
Data transfer between IT system and machine
Interfaces form the basis for vertical integration – that is, communication between the IT system and the machine. To be more precise, interfaces are software modules by means of which data is bidirectionally transferred between the production line and the ERP system. Line monitoring primarily constitutes the scanning of standardized data points by the IT system. Vice versa, the interface supplies the line with select MES data in order that the machines can be properly shut down should any defects in quality be discovered or a target quantity be reached, for instance. The standard interface ensures that this command is executed taking all accompanying factors into account. For order management the IT system – whether from KHS or another manufacturer – can transfer the order data needed for production to be carried out to the machine. Figuratively speaking, the interfaces function similar to a search and translation engine and make sure that the right information is passed on and understood.
Incidentally, interfaces are required regardless of whether the machines and MES systems originate from the same source or whether the operating company uses its own software and not a program provided by the engineering company. In the latter case, to date it was usual for interfaces to be specifically programmed for the customer setup – an undertaking that ties up a considerable amount of resources. “Customization is a cost- and time-intensive exercise,” explains Wolfgang Heßelmann, product manager for Innoline MES at KHS. “Not only does the individual adaptation and implementation of the software take time; in particular, the various test runs required can delay the commissioning of a line.”
Standardized and economical
In this context KHS thus decided to develop suitable standard interfaces that reduce the amount of effort needed and permit a reliable, high quality of data to be generated thanks to the issue of regular updates and new versions.
“By adopting this standardized approach, both our and the customer’s IT systems can be connected up to the machines even better and more cost-effectively,” smiles Heßelmann. “This is made possible by the extra data points we’ve added. We’ve not only improved the quantity but also the quality: as our standard interfaces undergo constant optimization, the data is steadily improving. This has allowed us to considerably reduce the risk of any communication problems occurring in the long term.”
»With our standardized approach, both our and the customer’s IT systems can be connected up to the machines even better and more cost-effectively.«
![]()
Innoline MES product manager, KHS
Are you interested in reliably connecting your machines up to a MES or PDAS? Then visit khs.com for further information!
Line monitoring and order management
Of the two new modules the first one, KHS Innoline MDI LM, manages line monitoring. “Our interface supplies the normed data points on the respective actual state of the machines. Evaluation in the connected IT system gives us an idea of the history,” Heßelmann says. “This permits beverage producers to see which components on the line have an influence on one another, for instance.” Disruptions on the machines and those caused by a lack of materials or media, for example, are observed here. Even if the interface itself is the cause of a problem, it still makes this information available. “This is by no means par for the course for a standard interface. Here, KHS exceeds the requirements of conventional standards such as Weihenstephan or OMAC and has added useful extra data points such as material availability.” The KHS Innoline MDI LM interface also supplies basic data for future IoT applications.
The second module, KHS Innoline MDI OM, supports order management and has been implemented for both KHS and third-party systems. Consistently integrated into the lines, production orders can be transferred from the customer’s ERP system and – with suitable assistance from the operator – fulfilled on the filling systems. Here, the MES system can automatically configure coding and printing systems based on the order data transferred. With reference to the order bill of materials it can also generate transfer orders for driverless LGVs (laser-guided vehicles), for instance, to automate the material supply to the line.
Adaptable system
Flexibility is writ large here. “Our customers can procure the standard interface and connect their plant engineering up to additional functions, such as a line diagnostics or order management system, at a later date,” states Heßelmann. He considers the fact that this is possible not just for KHS’ own MES system but also for that of the customer to be a unique selling point for the Dortmund systems supplier.
In conclusion, the KHS expert mentions one more aspect. “The issue of OT security is becoming more and more important. It thus goes without saying that we’ve safeguarded our interfaces in such a way that they allow content from affiliated third-party systems to be displayed without endangering machine and operational reliability.”
Two communication expertss
KHS Innoline MDI LM (Machine Data Interface Line Monitoring)
- Standard interface for line monitoring
- Now available
KHS Innoline MDI OM (Machine Data Interface Order Management)
- Standard interface for order management
- Now available