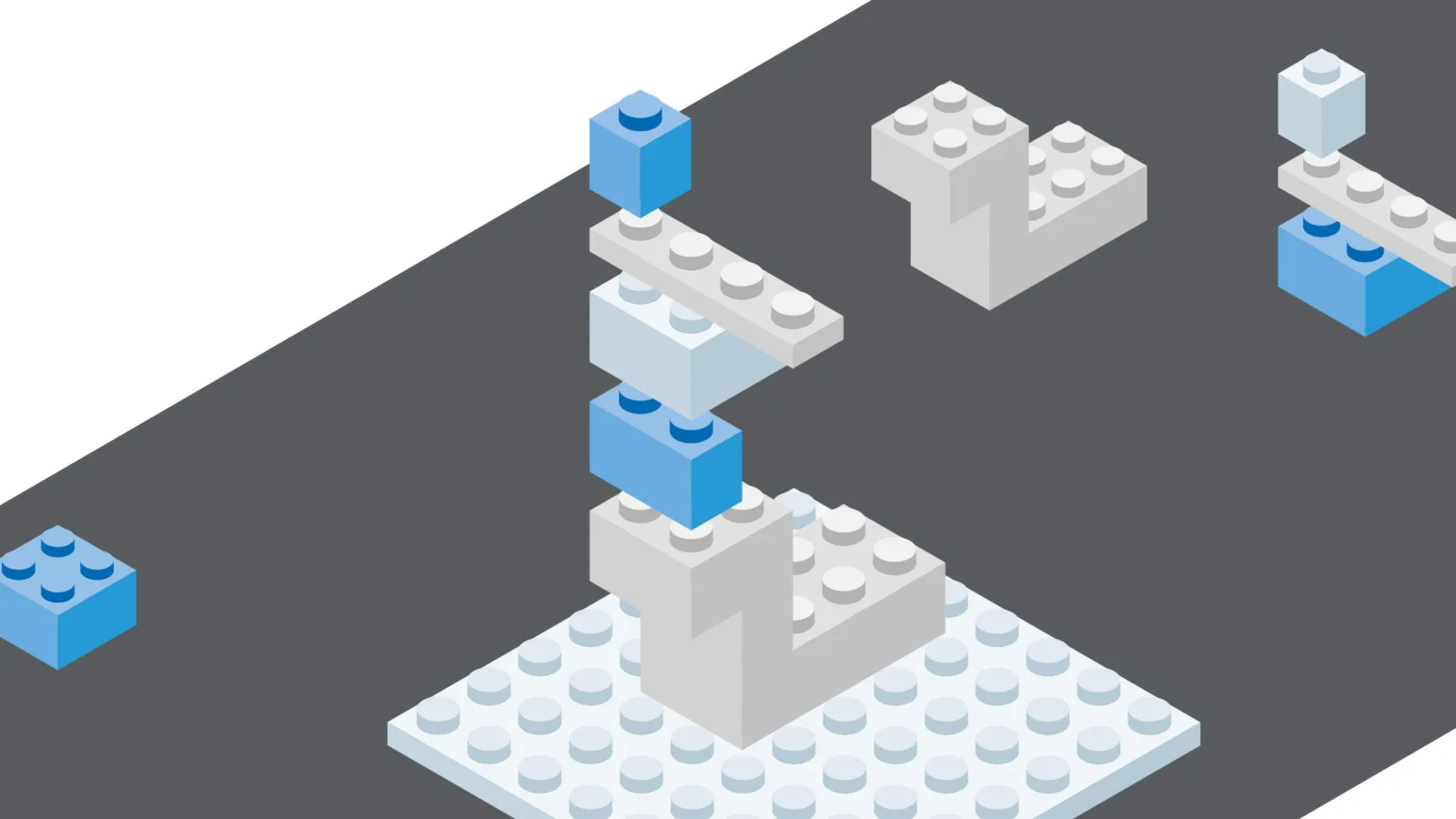
… more than just the sum of their parts
With its portfolio of blocked systems, KHS ensures investment security for its customers. / The wide range of solutions for both wet and dry parts keeps a close eye on the total cost of ownership - and therefore the sustainable business success of the user.
With its most recent additions for the hygienic filling of sensitive beverages KHS is continuing to build up its comprehensive program of blocked machine systems. The portfolio now caters for a multitude of different customer requirements in both the filling and packaging and palletizing sections. Frank Haesendonckx, head of Sales and Technology at KHS Corpoplast in Hamburg, is keen to emphasize that the plant technology currently available in this field by no means signals the end of the line. On the contrary: “At KHS the entire blocking concept is so modular that we can offer a whole variety of systems,” he explains. “Our open architecture and intelligent block interfaces also enable totally different systems which transcend the usual boundaries to be created quickly and easily.” Unlike the standard systems frequently applied KHS supplies flexible systems which can be modularly adapted to satisfy the demands of the market, also in the medium capacity range.
Without question KHS has extensive experience in machine blocking as the company is one of the pioneers in this sector; as early as in 2002 and 2004 initial plans were presented at international trade shows, with the first concrete steps in this direction undertaken in practice in 2005. In 2008 the KHS InnoPET BloFill stretch blow molder/filler block then went into operation – at the time one of the first on the market and still the most successful model to date.
KHS not only has a wealth of experience with blocked machinery, which centers on the stretch blow molder, but also with fillers – not to mention in packaging and palletizing. Karl-Heinz Klumpe, packaging product manager for KHS in Kleve, refers to the company’s long tradition in modular systems for the packaging segment. “We’ve been pursuing this idea for over 20 years,” he states. “In principle all packaging machines from KHS Kisters have a modular design. If you will, a tray shrink packer is also a block system in a broader sense of the word. As opposed to in the USA, where we still have a tray packer and straight film packer in our portfolio which are joined by a turner or stacker, in Europe all of the components have long been merged to create a single machine.” Klumpe confirms that specific customer requests and requirements carry great weight at KHS. “The magic word at KHS is ‘customizable’. With blocked systems there really are countless feasible options for modularization, meaning that as a result we can configure our systems with the corresponding degree of flexibility,” he stresses.
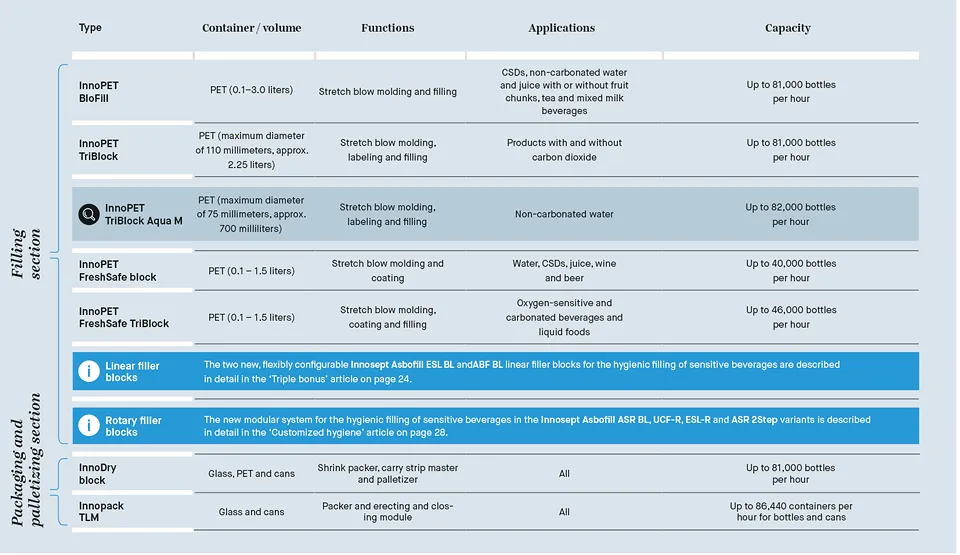
Example KHS blocks
The big exception: Aseptic blocks and sensitive beverages
For the no less than six hygienic fillers blocked with standard stretch blow molders, in some respects other rules apply than for classic filler blocks, underlines Thomas Niehr, the man responsible for aseptics and sensitive beverages at KHS in Bad Kreuznach. “When special hygiene requirements apply, savings in materials and personnel are less of an issue. Rather, the focus is on keeping the aseptic zone as small as possible in order to minimize the risk of microbiological contamination.” His colleagues’ customers also profit first and foremost from the reduced maintenance effort as a result of blocking. “Our transfer module – in other words, the link between the stretch blow molder and the aseptic, ESL or UCF filler – is a complex machine which has to be regularly serviced so that it can provide the required level of hygienic safety.” The two following articles ('Triple bonus’ on page 24 and ‘Customized hygiene’ on page 28) illustrate how much care and attention has to be paid to aseptics and sensitive beverages and outline which totally new, modular block concepts Thomas Niehr and his colleagues at KHS have developed to this end.
The KHS block program is not only flexible with regard to the technical components but also the site of production. “For a customer project in India we’re currently blocking a stretch blow molder made in Hamburg with a standard filler manufactured in India, for instance – a clear example of the flexible structure of our block systems”, says Haesendonckx. This is also proof that the worldwide trend towards blocked machinery is unstoppable.
When KHS combines several machines, each with their own innovative technology, to form a block, the result is more than just the sum of its parts. Thanks to the compact design and direct connection of two or three machines, among the most obvious advantages and synergies of such systems are the lower space requirement and omission of air conveyors – with all of the positive cumulative effects these entail. These primarily include a lower cost of investment, simple and efficient operation and less maintenance effort.
As the compact machine has a smaller footprint, fewer materials are needed. This not only gives users a number of cost benefits but also cuts down on the effort required for maintenance. Depending on the application, directly linking the individual components, an intelligent drive concept and safe bottle handling make for a very efficient line performance.
Frank Haesendonckx comes back to one particular aspect briefly mentioned in the above: operation. “Where several machine operators are usually required to overcome the buffer segments when moving from one machine to another, the components on a block are rarely more than one or two steps apart,” he elucidates. “This makes work very much easier for the operator and helps to prevent blind spots in line operation. These could cause the stretch blow molder to stop if there’s a backup, for example, or, vice versa, that the filler halts production if no more bottles are fed onto the line.” Larger screens which are networked with one another simplify control and the increasing standardization of components and processes reduces both the time and effort need for training and the manpower required.
In order that things remain simple and convenient for users during servicing, each block is treated as one machine. This ensures that all technical support, whether this be provided in the form of conversions, servicing or spare parts, comes from a single source.
To conclude, Frank Haesendonckx sums up the benefits of the KHS block system for users. “On the one hand, everything we develop regarding blocked systems aims to lower the total cost of ownership or TCO. After all, the intention is to support the economic success of our customers. On the other, we also help our clients to adapt their production process to current market and consumer requirements which in particular are increasingly affecting the packaging itself.”
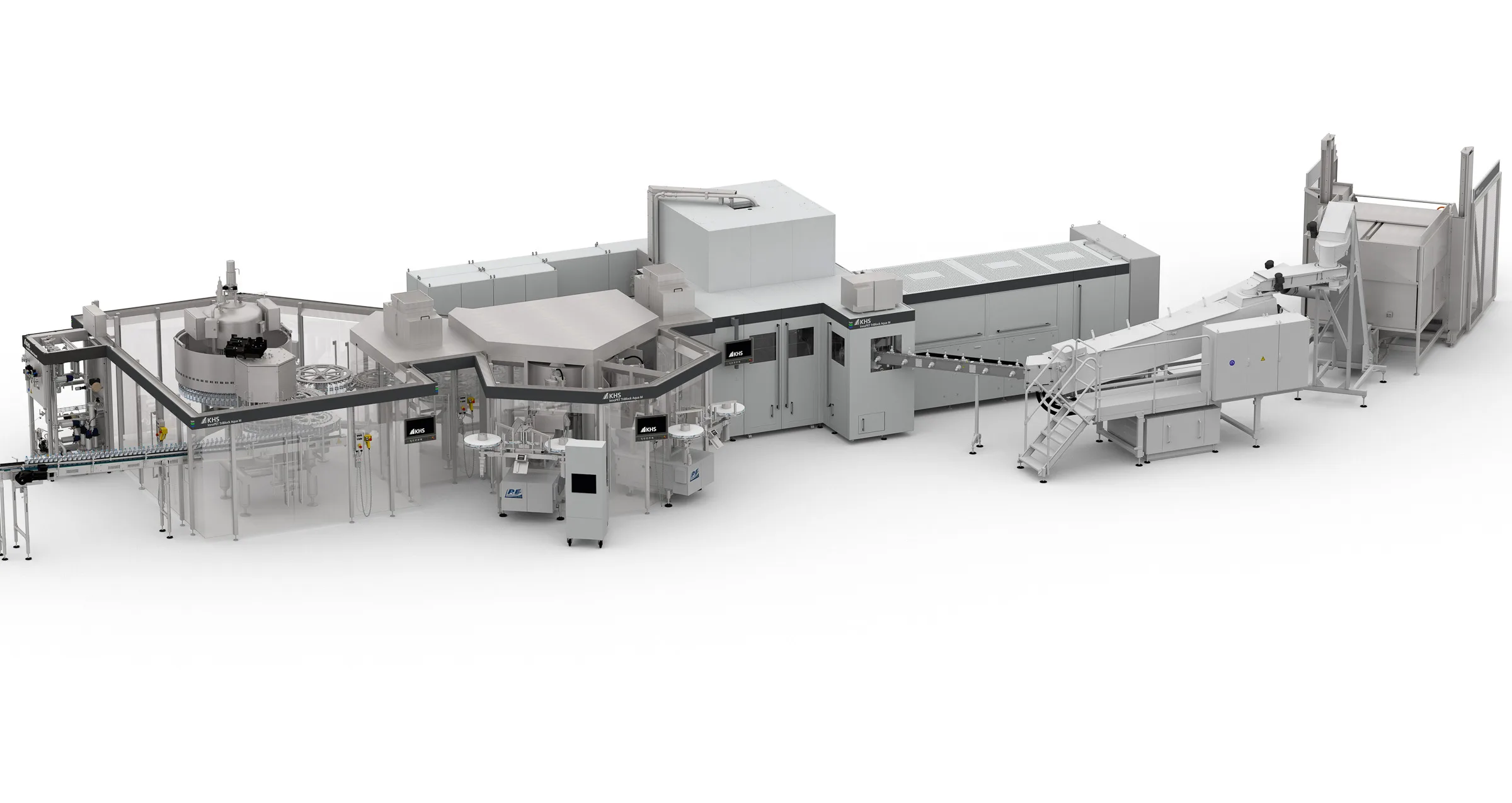
InnoPET TriBlock Aqua M
Benefits on bloc
Conveying and buffer segments no longer required
Compact layout and machine block
Fewer interfaces
Synergies created by shared controllers, safety equipment and cladding
Gentle bottle handling
Shorter segments for improved hygiene
Simple operation and short distances
To conclude, Frank Haesendonckx sums up the benefits of the KHS block system for users. “On the one hand, everything we develop regarding blocked systems aims to lower the total cost of ownership or TCO. After all, the intention is to support the economic success of our customers. On the other, we also help our clients to adapt their production process to current market and consumer requirements which in particular are increasingly affecting the packaging itself.”