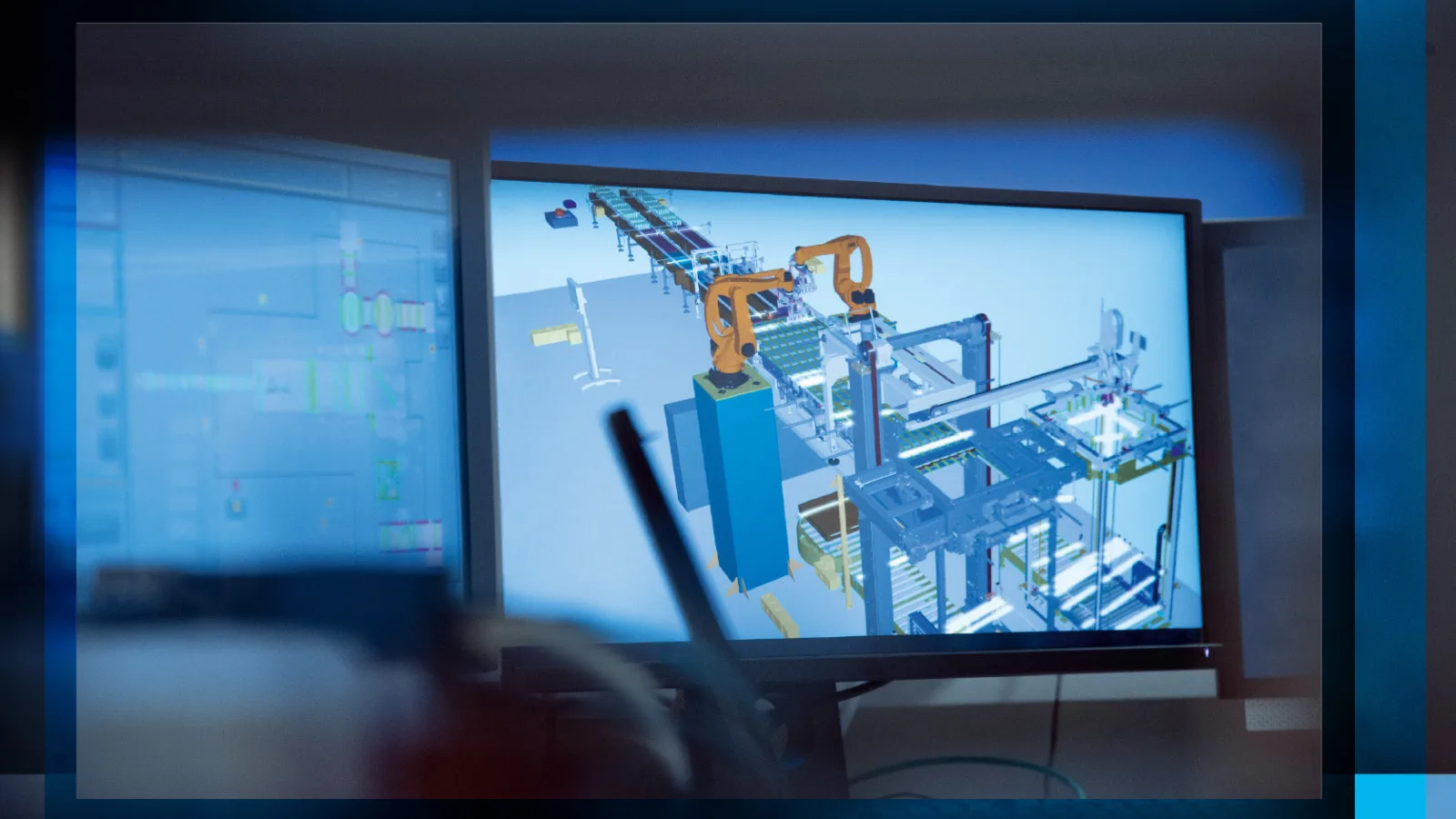
Like two peas in a pod
Everyone’s talking about Industry 4.0. The KHS experts in Worms practice what they preach: for years they’ve been commissioning machines virtually – but this isn’t all digitalization is capable of by a long shot ...
Digitalization is nothing less than an industrial revolution which is presenting companies with vast challenges. Unlike the last three waves of industrialization – mechanization, mass production and automation – Industry 4.0, as the process of digital transformation is also known, no longer takes place in the real world but increasingly in a virtual sphere comprised of enormous amounts of data. Whereas in the past the first steam engine, then the assembly line and finally the use of electronics heralded periods of radical change, today not one but several megatrends such as automation, connectivity, mobility, globalization and security have to be combined with one another. With the help of smart, digital technology production processes are gradually being networked and automated so that machines, products, entire systems and – last but not least – people can communicate and work with one another efficiently.
In particular what’s known as the digital twin enables procedures to be transferred to a virtual environment by tracking and imaging all phases in a product’s life cycle. All production processes and products can then be simulated virtually. Alternative, optimized production sequences appear on screen, boosting the efficiency of production lines.
One of the major prerequisites for this is that the engineering is consistent throughout the entire value chain in order to prevent what’s known as data discontinuity at the interfaces between the various engineering disciplines, namely mechanical components, electrical equipment and software. Unlike the way much work is done today, projects are not processed sequentially, i.e. separately and consecutively. Instead, in an ideal scenario all departments work in parallel across their respective disciplines on the implementation of a project and share a common data model – the basis for the digital twin which depicts every last detail of a system virtually and permits precise simulation.
»In increasing virtual commissioning we want to continue to shorten lead times and lower fault-related costs.«
![]()
Head of the Palletizing Product Center, KHS
The shared data challenge
For an engineering company like KHS, which not only manufactures a huge number of different machines but whose research and development departments also have a colossal geographical spread, this is a major challenge.
The KHS engineers at the Palletizing Product Center in Worms have been working on the virtual depiction and simulation of machines and system parts for 13 years now. Simulation and virtual commissioning especially lend themselves to use with logistics systems such as palletizers or conveyors. It all began with the evaluation of various tools, followed by the first projects centering on pallet conveying systems and the loading and unloading of kegs. In 2015 more than 70 different hardware-in-the-loop projects were realized, with which system behavior and material flows could be simulated and the control program tested. KHS Brazil has been involved in the project since 2016 and is responsible for generating 3D machine models.
“Our aim is to continue to shorten lead times and lower fault-related costs by expanding our virtual commissioning setup,” explains Stefan Diesner, head of the Palletizing Product Center. In order to estimate just how high these savings can be, it helps to take a look at the rule of ten. This states that the cost of fault correction increases by a factor of ten the later in the process an error is discovered. If a fault is only found and eliminated during factory commissioning, for example, the financial burden is ten times higher than if the correction had already been made to the software engineering during virtual commissioning.
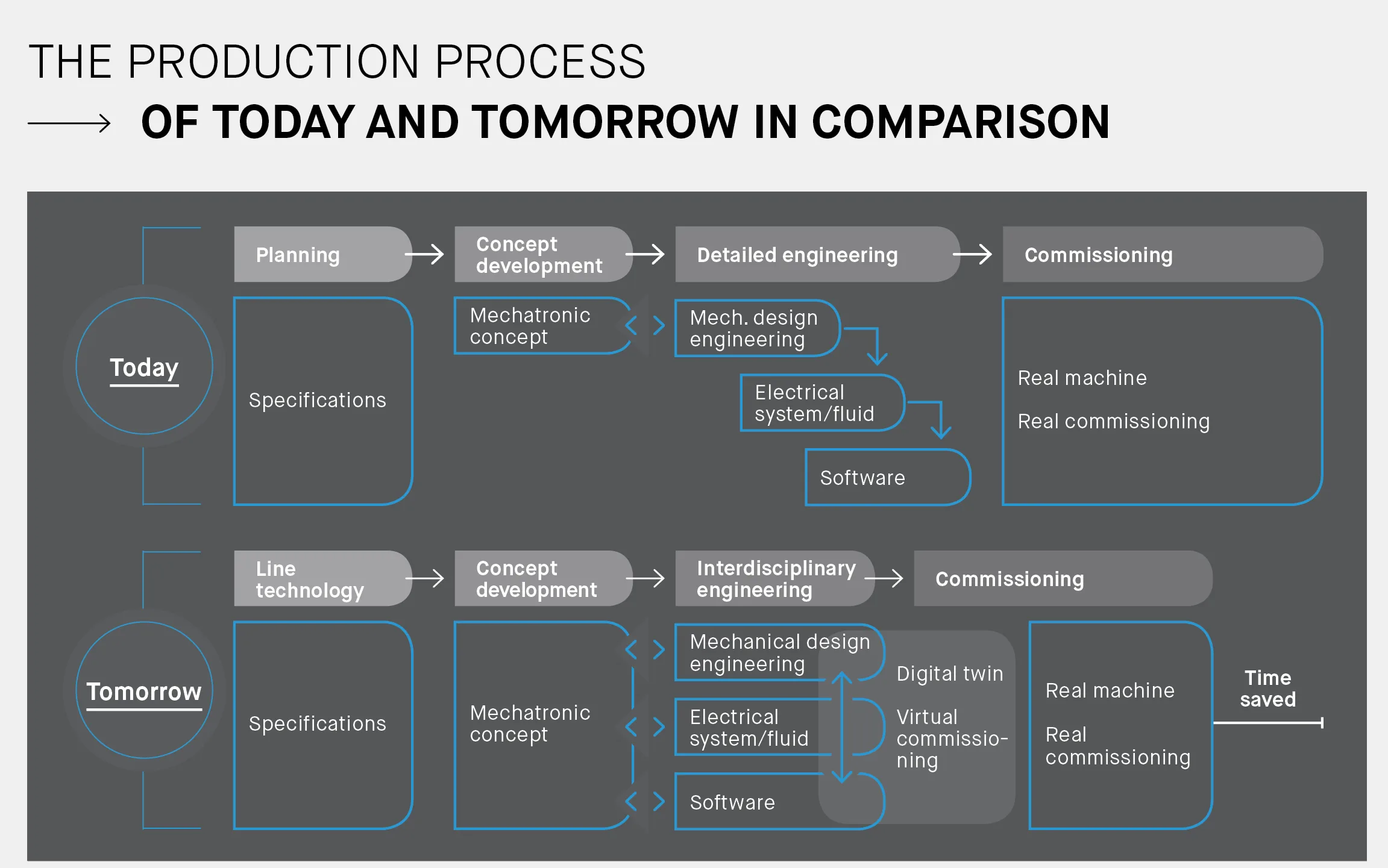
Reduced time and effort
A further objective of the current project is to reduce the amount of time and effort required for virtual commissioning. One basic condition here is that the data is consistent. "With virtual commissioning we have control over the data consistency," Diesner explains. "All data is generated and stored at our production site, albeit still in a number of different systems. Further steps must be taken here before efficient and bidirectional access to this data is provided by a virtual engineering tool that includes simulation. Once this has been done, we can configure the system according to customer specifications or quickly and efficiently commission adapted machine designs on screen."
In the meantime Worms is looking ahead: virtual commissioning is the first step towards digitalized systems for the beverage industry and the real digital twin. In the future this will be able to do much more than simply facilitate virtual commissioning. To this end, the digital twin has to be plied with more information, however, such as data on conversions for KHS customers or operational data from production - an undertaking which will also pose a number of exciting challenges in the years to come.
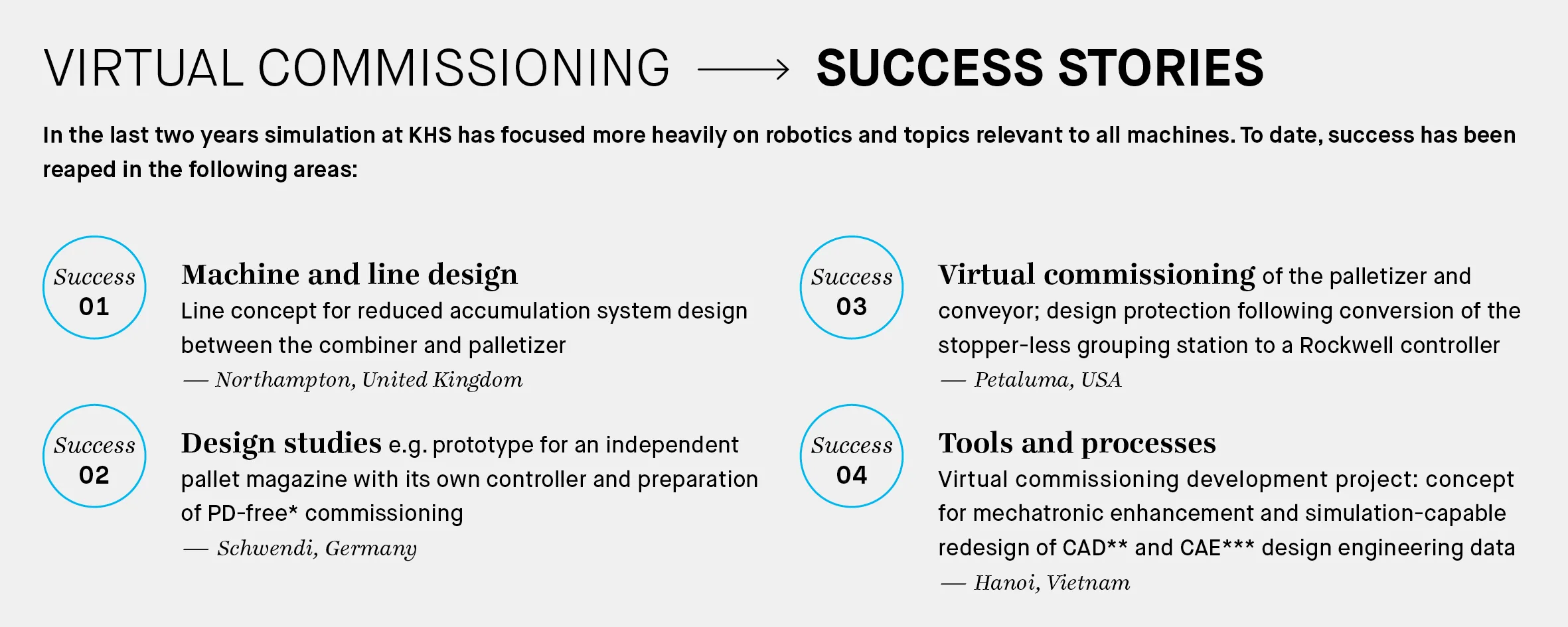
* PD-free = without a programming device (laptop) as no program corrections are needed on site.
** CAD = computer-aided design or the support of design engineering tasks by a computer.
*** CAE = computer-aided engineering; covers all kinds of computer sup- port for work processes in technology.