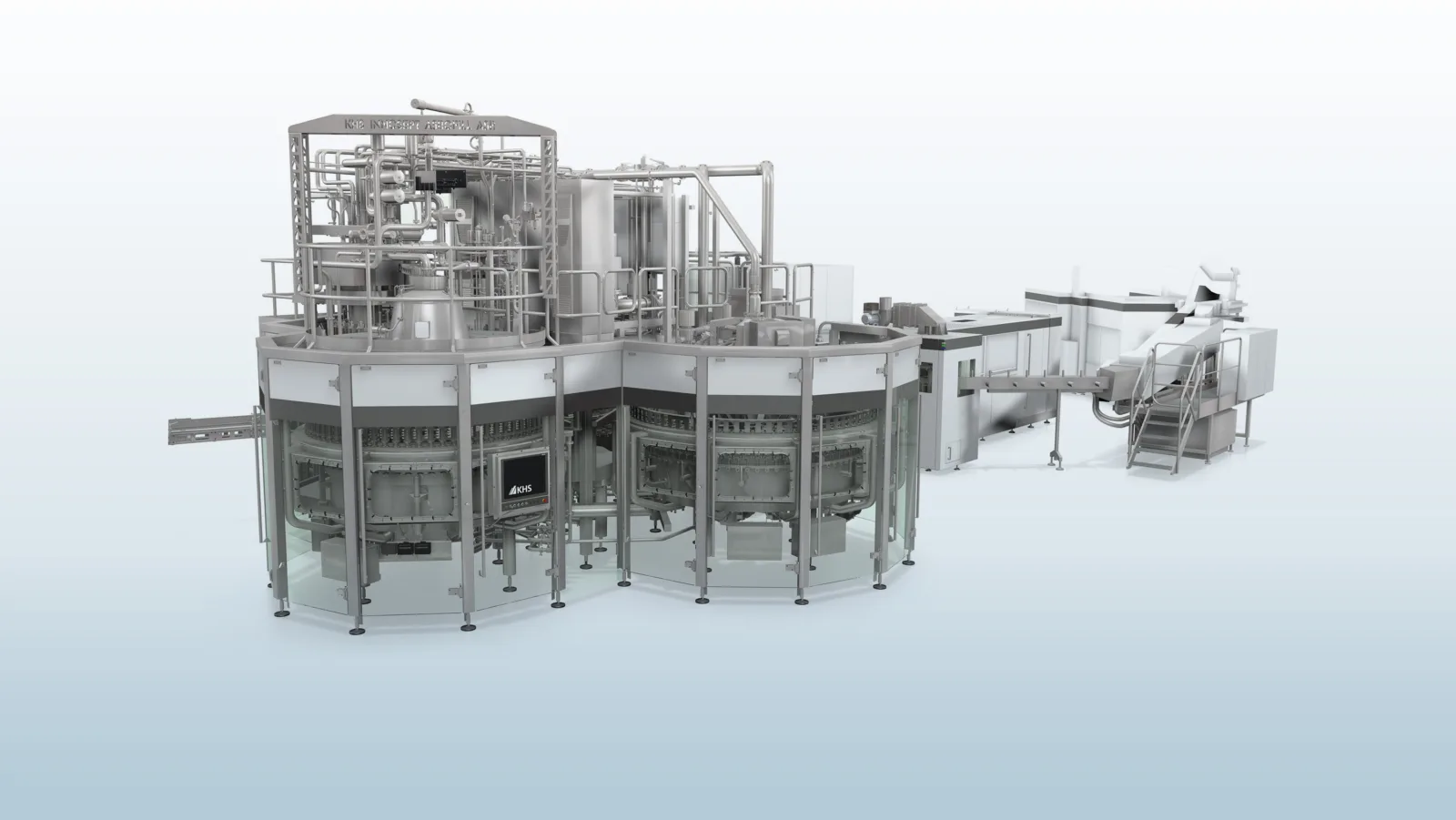
Hygiene customized
A new modular system with rotary machines for hygienic filling gives producers of sensitive beverages the exact degree of safety they need. / Customized to suit their respective hygiene requirements, reliable and economical systems can be configured which prove convincing in practice.
Compared to the classic means of preserving food and beverages aseptic filling is a gentle alternative which does not have a detrimental effect on either the product taste or vitamin content. It is thus with good reason that this method has vastly increased in importance over the last ten years.
As one of the founders of this technology and with over 25 years of experience to its name KHS is therefore a true specialist in the filling of sensitive beverages such as milk, mixed milk drinks and juice. The expertise of the Dortmund systems supplier goes far beyond the mere development and manufacture of filling systems, however; with its specifically adapted plant engineering it centers on the diverse requirements of its customers.
Modular and tailored to requirements
The company has now presented a pioneering innovation which has a positive impact on the company’s entire portfolio: a concept which satisfies all hygiene specifications and required production capacities. The system’s most important classification criterion are the hygiene categorization classes specified by the VDMA, the German Engineering Association. A distinction is made between the following three categories for the filling of sensitive products:
Class III (ultraclean filling):
includes low-germ filling products such as fresh juice and slightly carbonated spritzers; depending on the product specifications also natural and drinkable yogurt with a shelf life of less than 14 days.
Class IV (extended shelf life):
pertains to dairy products in the cold chain, such as ESL milk with a shelf life of under 28 days, natural and drinkable yogurt, cold-filled smoothies and iced tea and fruit juices which have to be filled without the risk of recontamination.
Class V (aseptic filling):
includes germ-free products to be filled, such as UHT milk and cream which uncooled have a shelf life of several months, and non-carbonated water, juice beverages and near-water beverages.
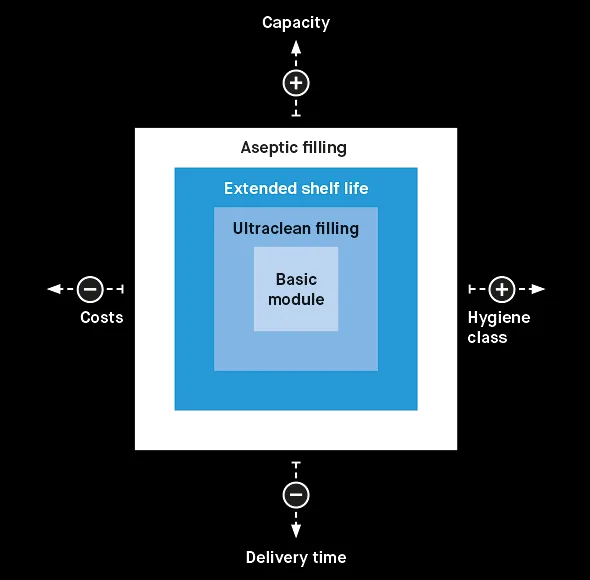
The modular design of the rotary filler block ... is flexible with regard to its hygiene class and capacity. It cuts costs and reduces delivery times.
For each of these hygiene classes the new KHS concept has its own machine engineering adaptations in the form of standardized modules. In the future the filler can be configured depending on which hygiene class a bottler’s products fall under and precisely tailored to suit the exact specifications of each and every customer.
Adjusted to the producer’s capacity requirements, the new KHS concept can cater for outputs ranging from 24,000 to 54,000 bottles per hour. The system offers plenty of scope as regards the bottle size, too; the combination of container volume and output capacity can be configured for 500 milliliters, 1.0 liter and 1.5 liters.
Based on its many years of experience KHS has opted for a method of preform, bottle and cap sterilization which is considerably easier to operate than the aseptic blow molder setup. “Keeping a rapidly rotating blow molder permanently sterile is a very complex challenge – one without any notable benefit,” states Thomas Niehr, head of Aseptic Filling Technology at KHS. “A lot of time and effort is involved in format changeovers to prevent the sterile blow molder from being recontaminated. This makes great demands of the operator and the machine environment and poses a high risk of serious errors.”
In the rotary machine range a future alternative to the proven bottle sterilization system on the Innosept Asbofill ASR is proffered by the new Innosept Asbofill ASR 2Step. This differs from the classic version in that it integrates new, space-saving H₂O₂ systems on the transfer stars between the stretch blow molder and filler. This reduced form of bottle sterilization is made possible by the preforms being sterilized at the infeed to the stretch blow molder. On the Innosept Asbofill ASR 2Step there is thus no need for a sterilization carousel and the drying module can be made much smaller. Both features result in a system which is much neater and more compact.
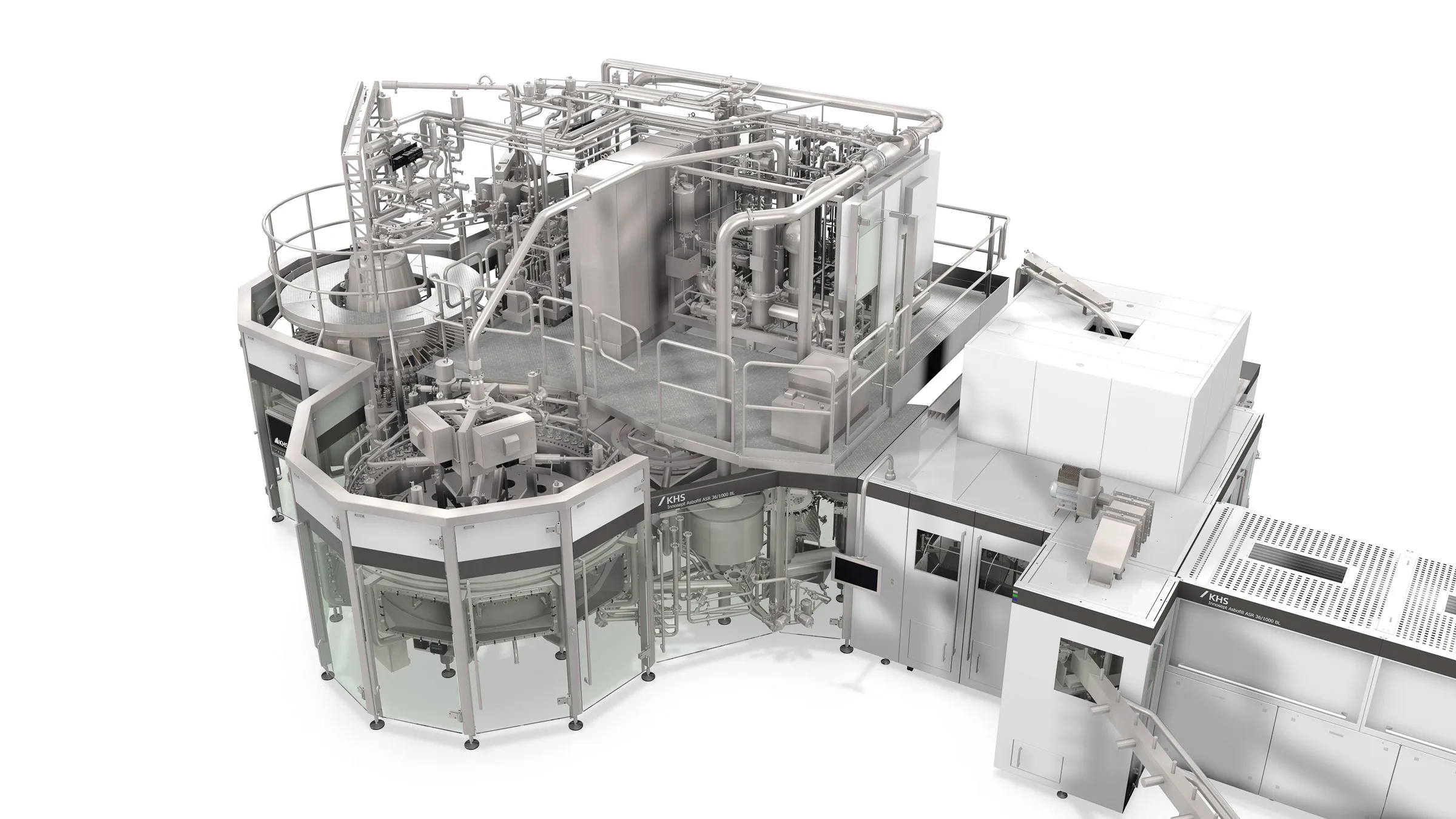
Physically separating the process technology (above) from the filling system (below) results in a smaller aseptic zone and improved hygiene.
Preform sterilization
2Step sterilization has the advantage that it is much simpler to perform and that product-dependent parts and molds can be replaced much faster than on a sterile blow molder. On the stretch blow molder changeovers are made under normal environmental conditions; this does not affect the degree of microbiological risk. In this context Niehr refers to another important benefit of 2Step sterilization. “Preform sterilization enables the bottle material to be disinfected upstream of the stretch blow molder. Experience has shown that only few very microorganisms again come into contact with the bottle in the stretch blow molder. Bearing this in mind we can considerably streamline the disinfection of the ‘finished’ bottles, which in turn greatly reduces the footprint of our machine.” Another advantage of this process is that in aseptic filling according to hygiene class V the amount of hydrogen peroxide required for sterilization can be decreased and the bottle drying temperature lowered.
For reliable, recontamination-free filling it’s of central importance that the aseptic or hygienic zone and the external influences on this zone are kept down to a minimum. This means that all modular fillers can be blocked with standard stretch blow molders from KHS. A specially developed block module for the hygienic transfer of the fully blown bottles to the filler reduces the space requirement, lowers the amount of investment, cuts down on the installation effort and calls for much less intervention in the customer’s infrastructure. “Safety always comes first,” explains Niehr. “The simpler the cleaning and monitoring of the system, the lower the risk of recontamination. This is why all electronic components, drives, wires and piping are positioned outside the aseptic zone; even with the capper only the cone is in the area to be sterilized. The fewer parts there are in this section, the less I have to keep clean as a bottler.” A sophisticated room-within-a-room concept with cladding doors mechanically protects the seals in the aseptic section, providing not only maximum hygienic safety but also ease of operation. The principle of clearly separating the process and filler areas is another plus where hygiene is concerned. The valve manifold and sterile air filter are placed at the top of the systems to keep the space required for the sterilization unit, filler and capper as small as possible. The aseptic zone on KHS’ rotary machines takes up just 12 to 14 cubic meters of space, depending on the container size.
Economical system
Alongside all of the hygienic safety features, for which KHS’ entire sensitive product portfolio has stood for many a year, first and foremost the innovation of the modular system gives sensitive beverage bottlers three main advantages, emphasizes Niehr. “Firstly, thanks to the concept of modularization our customers can configure their machines exactly according to their requirements. Oversized systems not running at full capacity often lead to longer downtimes which always increase the risk of contamination. Secondly, modularization leads to standardization, which in turn means that in principle all basic and module parts can be pre-produced and stocked by KHS. The customer thus benefits from shorter delivery times. And thirdly, the modular system also generates certain cost benefits,” concludes Niehr. “These savings give us additional scope for integrating further safety systems, with which we consistently endeavor to permanently increase the standard of safety on our aseptic filling machines.”