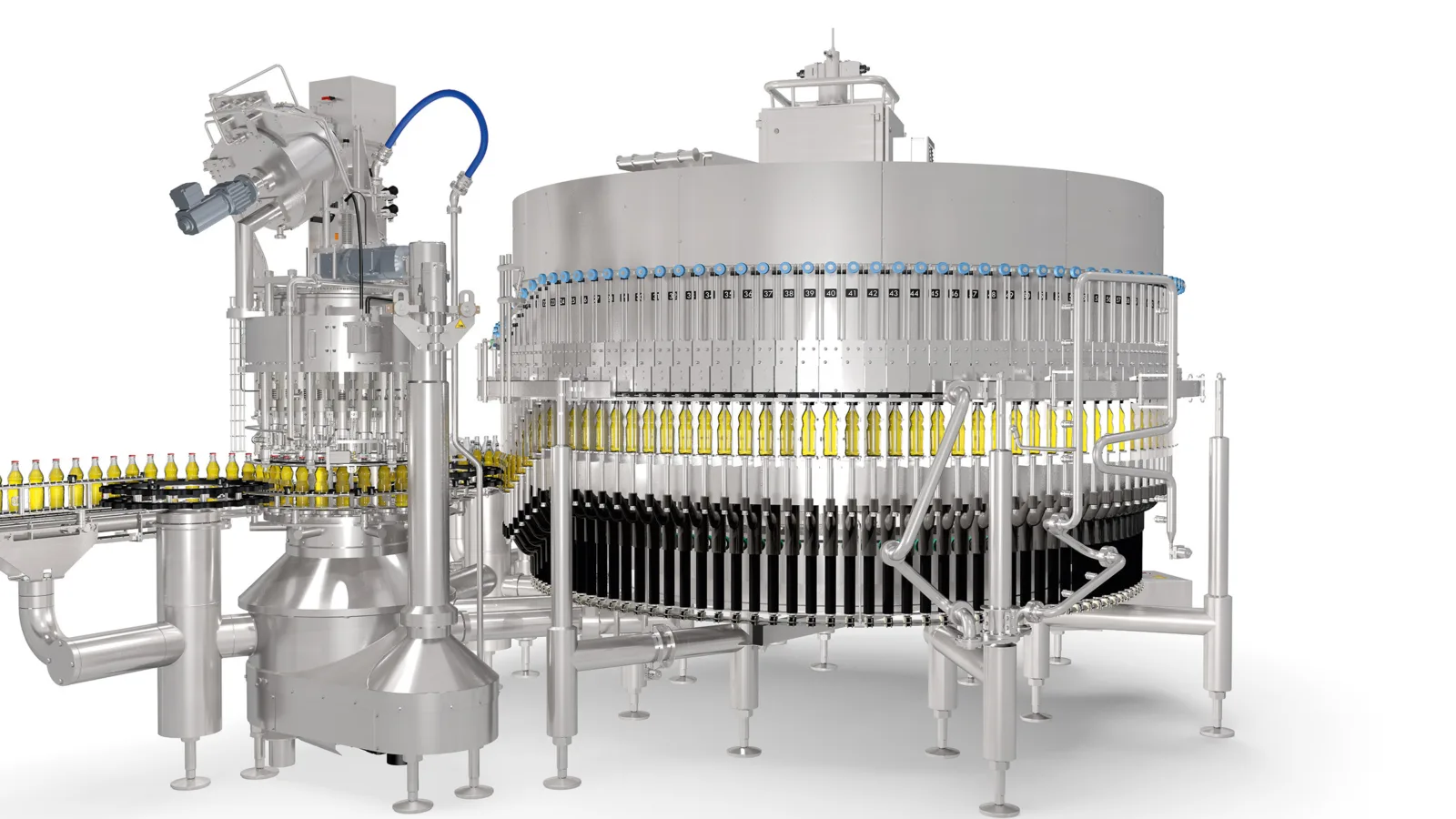
Grows with the job
More speed and greater scope are what beverage producers with a large product portfolio and frequent product and container changeovers in particular wish for. All this is provided by the new long-tube filler from KHS – complete with the added perspective of future growth.
Long-tube fillers are frequently operated in the sensitive beverage segment, for example to bottle beer or hot fill sensitive products such as juice. They’re most commonly used to process glass or PET bottles and contour containers holding up to three liters of product. The long-tube principle permits fast flow rates and short filling times as the bottom-up filling method causes very little turbulence in the container. This makes for low oxygen pickup, important when bottling orange juice, for instance. This would otherwise lose its appetizing yellow color and turn brown unless additives such as vitamin C are used. Unlike the normal filling of juice, where the fruit fibers collect at the top of the container and form clots, during long-tube filling less air attaches itself to the fibers and no clots are formed.
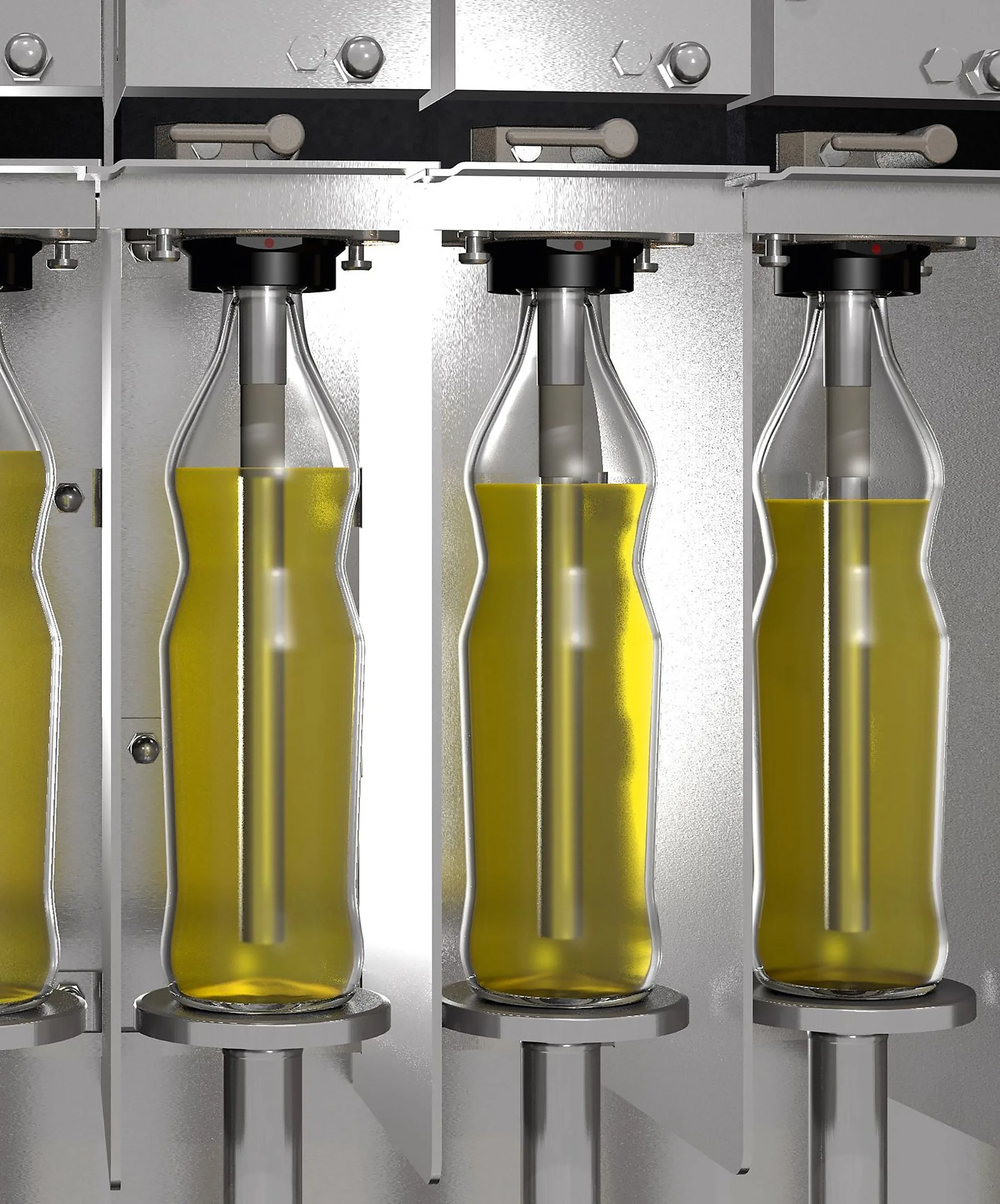
Bottom-up filling ensures low oxygen pickup and makes purging redundant.
A filler with tradition
When filling beer into PET or aluminum bottles without vacuum stability, bottom-up filling also has its advantages: low oxygen pickup makes purging redundant which could otherwise cause the container to contract or buckle.
“Long-tube fillers are a tradition at KHS,” explains Manfred Härtel, filling product manager. “In the 1970s and 80s they were built at our plant in Bad Kreuznach for filling beer. We did actually have a computer-controlled filling system back then but this was still equipped with gears and gear wheels.” These have long been replaced by star drives and servodrives. Nowadays the stars and carousels are blocked digitally and synchronized with servomotors. This eliminates the need for a front table.
Modular design
In its updated form the new long-tube filler is part of the modular Innofill Glass DRS ECO platform concept launched at the end of 2019. Bottlers benefit from numerous optimizations here: on the one hand, the basic machine structure and various components have been standardized for the modular machine version. Thanks to improved availability the fillers can be supplied faster. Installation and commissioning at the customer’s site have also been standardized and accordingly can thus be carried out in less time. On the other hand, the new design greatly improves hygiene: as the front table has been dispensed with, no more puddles are formed. Maintenance- free drive technology also cuts down on the effort required for cleaning.
The serial QUICKLOCK fast-acting locking system from KHS permits bottle guide parts to be exchanged with just a few manual adjustments performed without tools. Changeovers on machines fitted with QUICKLOCK are around 30% faster and generally more hygienic than where standard format parts are used. “This tried-and-tested technology is a particularly useful addition to the long-tube filler with its vast flexibility regarding the range of products and containers,” Härtel states. “As almost any beverage can be filled on this machine, it’s a worthwhile option for contract fillers in particular.” An extremely broad spectrum of modules facilitates individual configuration, thus catering for all of a bottler’s specific capacity requirements with pinpoint accuracy.
»What’s interesting for contract fillers is that almost any beverage can be filled on this machine.«
![]()
Filling product manager for KHS
Flexible growth
The new long-tube filler on the Innofill Glass platform has different filling valves, for instance: a simple variant for the hot filling of juice, a version for filling beer only with closed CO₂ purging or a third all-round module that’s also well equipped for future jobs. This modular filling technology gives beverage producers the flexibility to gradually expand their machine to cater for a growing portfolio. Here, the valves can be equipped with electromagnetic induction flow meters as a volumetric filling system or retrofitted with sensors. The switching cylinder between the tubular ring vessel and valve that allows two or three filling speeds can be replaced by continuous regulation at a later stage of expansion.
“This example shows just how future-proof our machine is with its modular structure,” Härtel smiles. “Additional components can be easily retrofitted at any time, depending on how the beverage market or our customers’ product policies develop.”