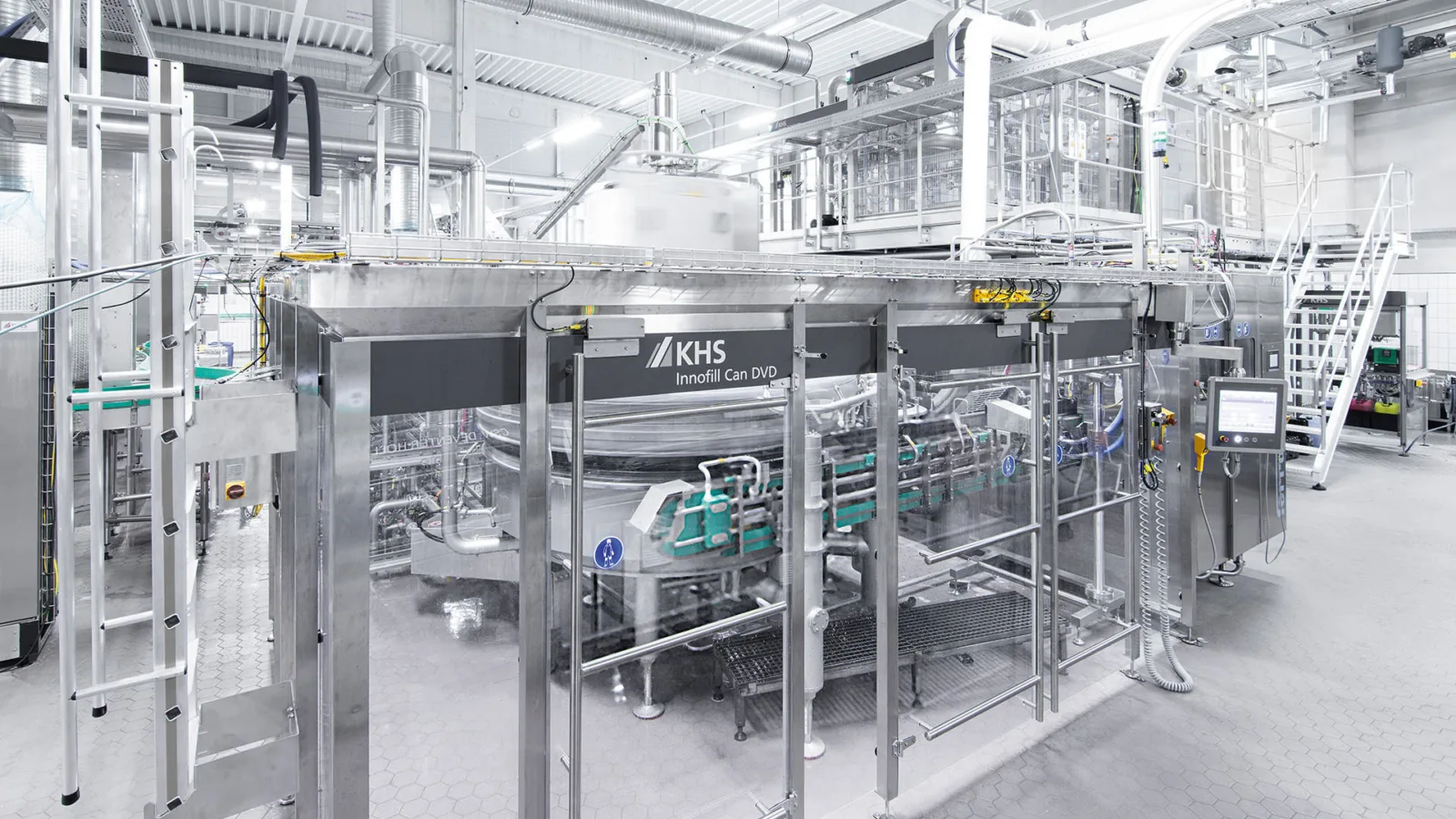
Freedom in filling
KHS’ reliable and highly efficient can fillers for the high capacity range have proved themselves many times over in practice and are extremely popular with customers. A number of technological upgrades now make these machines even more flexible and hygienic.
In 2014 KHS presented the first can filler in a totally new generation: the Innofill Can DVD. With this the Dortmund systems supplier thus not only followed the growth trend for cans but also brought its filling equipment into line with the technological state of the art in a number of ways. The Innofill Can DVD scores on three major points:
- Low oxygen pickup, low CO₂ consumption
Oxygen pickup is reduced by up to 40% by the extremely effective low-pressure CAN+ purging process at low levels of CO₂. - Long service life, more flexibility
The gapless bell guide with PTFE (Teflon) expansion joints doubles the service life of the filling valves. They are easier to clean and absorb far fewer flavoring substances. - Superior hygiene levels, less cleaning effort
The extremely hygienic design of the machine and elimination of water lubrication in the filler carousel area prevent the open cans from being soiled. Cleaning intervals are shortened by 20% and maintenance cycles are considerably lengthened.
“With our new can filler we really set standards in 2014,” says Manfred Härtel happily, filling product manager for KHS in Bad Kreuznach. “Even today this technology is still the best on the market."
»We’re extremely good at high tech and high speed at KHS.«
![]()
Filling product manager for KHS
“We satisfy high hygiene requirements without compromise, especially those made by sensitive beverages such as non-alcoholic beer, mixed beer beverages and flavored ciders,” he continues. KHS can fillers not only display a high standard of hygiene inside the machine but also outside it – an aspect that’s becoming increasingly important in view of the trend towards beers and mixed beverages with less or no alcohol.
Härtel knows why ‘his’ machine is so popular with customers. “Our filling valves are famous for their hygienic properties, compact design and simple handling and maintenance.” The over 40 years of experience KHS has in can filling are also convincing. “We’re extremely good at high tech and high speed,” he smiles proudly. “This segment is undergoing a disproportionate growth worldwide. This is also expressed in the high demand for our fillers – from the low capacity range to an output of 135,000 cans an hour. Thanks to their stable performance these systems score on their high availability and optimum efficiency. This naturally creates great trust among our partners in the beverage industry.” This applies especially to bottlers with a wide assortment of products, this requiring maximum flexibility of the technical equipment on the production line.
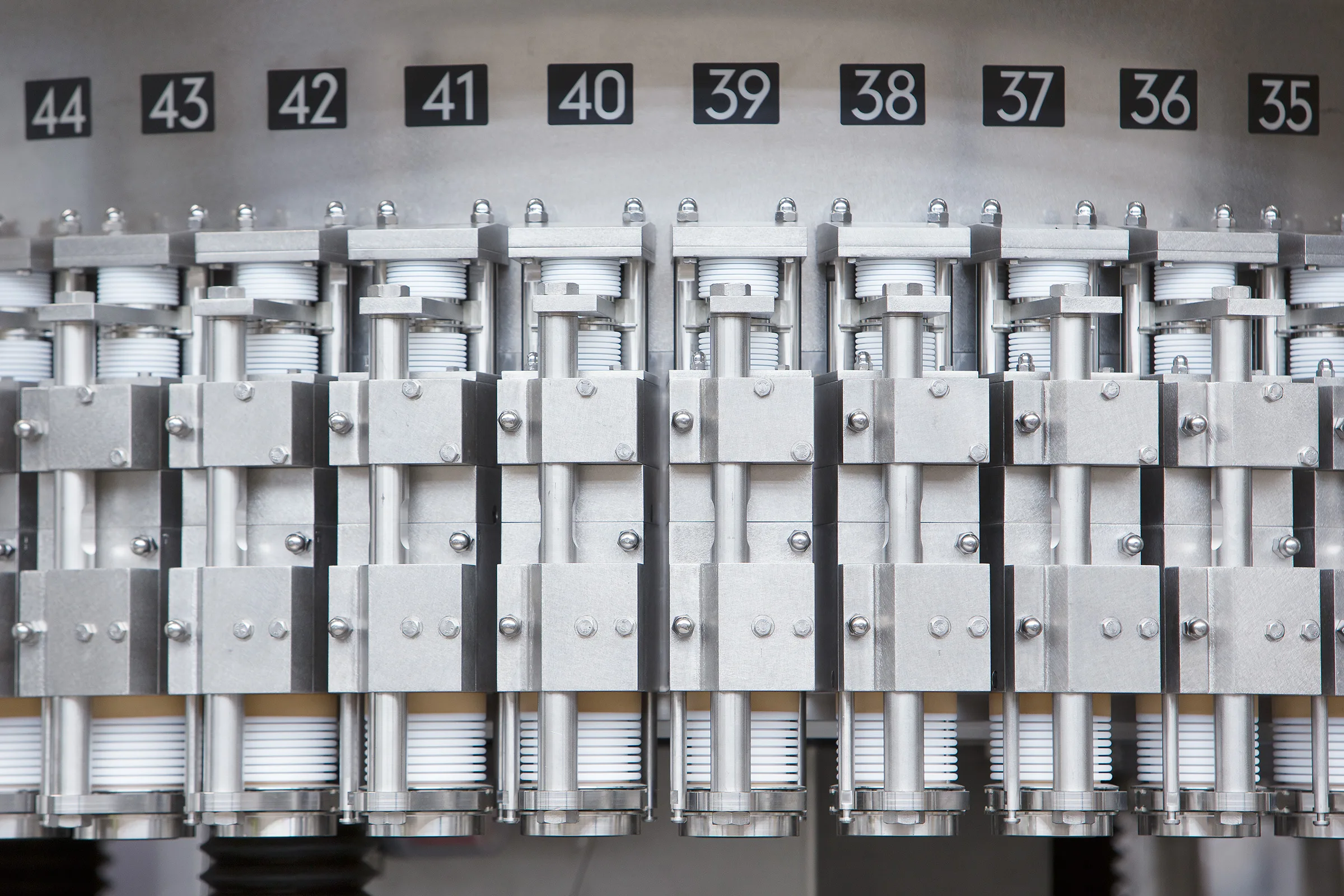
The most important upgrade and a big plus when it comes to hygiene is the pneumatic lowering device for the centering bells.
Made possible by Teflon
It’s worth taking a look at the details. One key prerequisite needed to achieve the required level of flexibility is the choice of the right sealing material for the expansion joint seal.
“We continue to rely on Teflon here,” says Härtel. “This material can be excellently cleaned, gives our valve seals a much longer service life and doubles the change intervals with the added bonus of much shorter changeover times. Looking at the range of materials on offer, however, what’s most important is that PTFE* absorbs practically no flavoring substances – unlike standard seals made of elastomers such as EPDM** that soak up liquid like a sponge during production. When there’s a drop in concentration with the next product in the filling sequence, the EPDM again releases these flavorings. In order to prevent this unwanted effect, production has to be scheduled by flavor: the week thus starts off with a mineral water, for instance, and ends with the filling of a product with an intensive taste, such as an energy drink. With our filling valves the transfer of flavor is cut down to an absolute minimum, giving customers more freedom when planning.”
* PTFE = polytetrafluorethylene (Teflon).
** EPDM = ethylene-propylene-diene rubber.
Freedom in filling is much in demand, also with reference to the temperature of the product to be filled. With the revamped KHS can filler beverages can also be filled when warm. This process becomes more significant particularly regarding the processing stages further down the line as it eliminates the formation of condensation. This more or less rules out the risk of cartons, trays and cans in six packs growing soggy, forming mold or being contaminated by microbes. Beer is filled at a temperature of 20°C and carbonated soft drinks at around 22°C. Juice can also be hot filled on the further developed Innofill Can DVD. This application is in increasing demand especially in the low and medium capacity range. “Our customers want flexible machines they can also realize new products on,” explains Härtel. “Our fillers can process widgets***, for example, that release nitrogen into low carbonation beers when the can is opened. This produces a very creamy and compact head, just like a freshly tapped draft beer.”
*** Widget = a hollow plastic device about 3 cm in size filled with nitrogen during the filling process. When the can is opened, the widget releases the nitrogen into the beer. A compact head of foam is formed. It’s often used in English-style beers.
The can filler can also be combined with the Innoket Neo labeling machine, for instance, that dresses the containers with self-adhesive labels. This can be useful if also small batches of individual cans are to be produced.
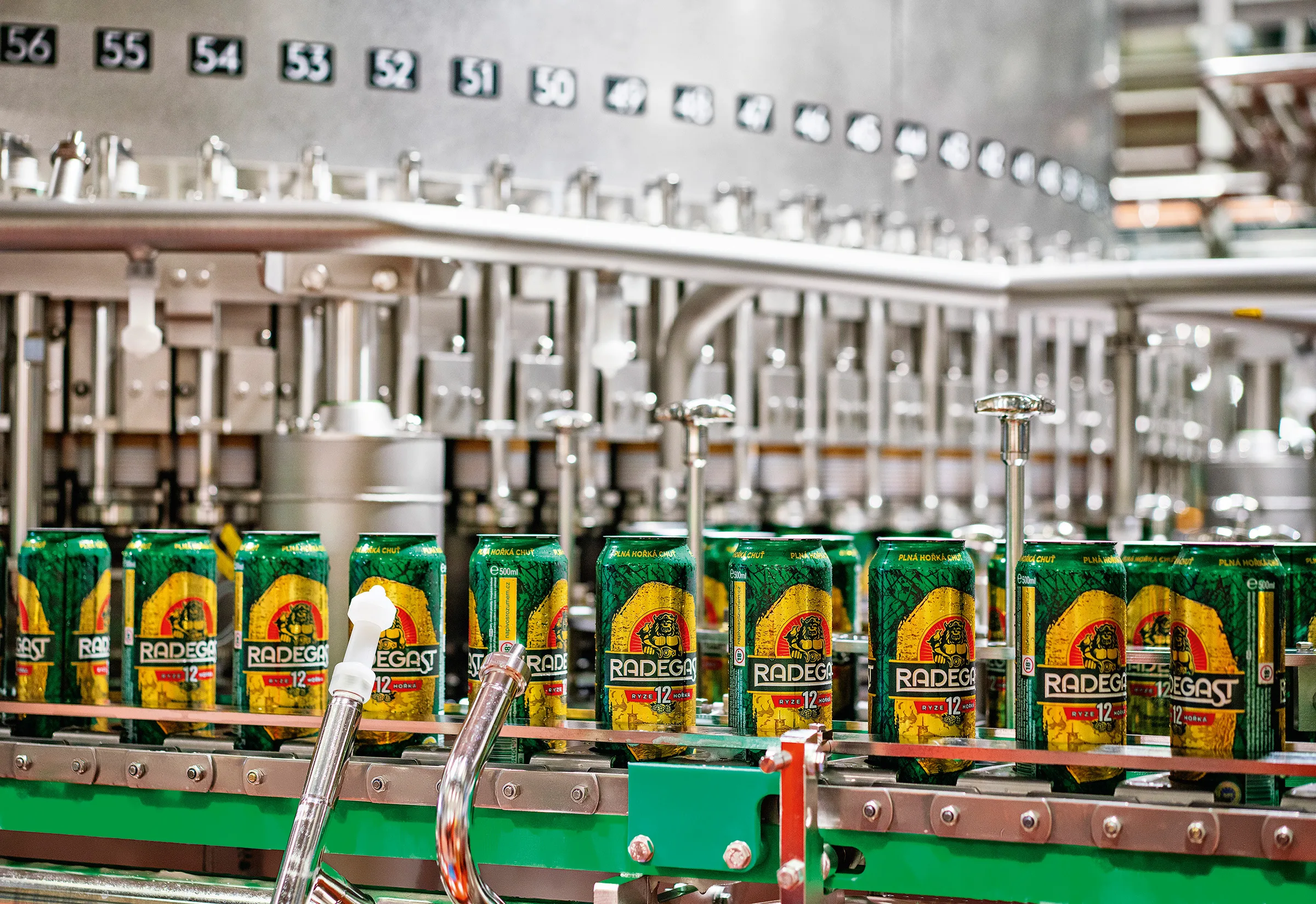
The first can filler to feature the new technological functions went into operation at Radegast Brewery in Nošovice in the Czech Republic in the spring of 2020.
You can find more information on our can filler for the high-capacity range and videos with specific example applications on khs.com.
Pneumatic lowering device
Besides flexibility hygiene is still always a big focus. KHS wouldn’t live up to its reputation as a developer of hightech systems and solutions if it hadn’t become even better in this discipline, too. The most important upgrade on the Innofill Can DVD is thus the pneumatic lowering device for the centering bells. Unlike on previous models these are no longer moved mechanically by rollers and cams. Instead, the proven pneumatic lifting and lowering motion found on the smaller Innofill Can C filler (see the article ‘Compact class’) is now also used on its big brother. “We also want to carry on being pioneers when it comes to compact designs and simple handling,” is how Härtel describes what pushed KHS to explore this further development. “With the pneumatic system we reduce the number of fittings on the valve. You can probably imagine how much strain the rollers in particular are subjected to on a filler where up to 135,000 cans can be processed round the clock seven days a week. Here, a certain amount of abrasion can be caused above the open cans. With this now no longer an issue in the future, we’ve managed to again considerably increase what was already a very high level of hygiene.” The lifting and lowering of the bells is intelligently controlled. As cans are becoming ever thinner as weight and materials are saved, it’s particularly important to guide and fill the containers as gently as possible. Pneumatic actuation allows the contact pressure to be adapted to suit different qualities of material.
The once new technology has long outgrown its pioneer status and since proved itself on the market many times over. With its most recent technological upgrades the KHS Innofill Can DVD can filler is also set to be a real success in the coming years. Of this Manfred Härtel is convinced.