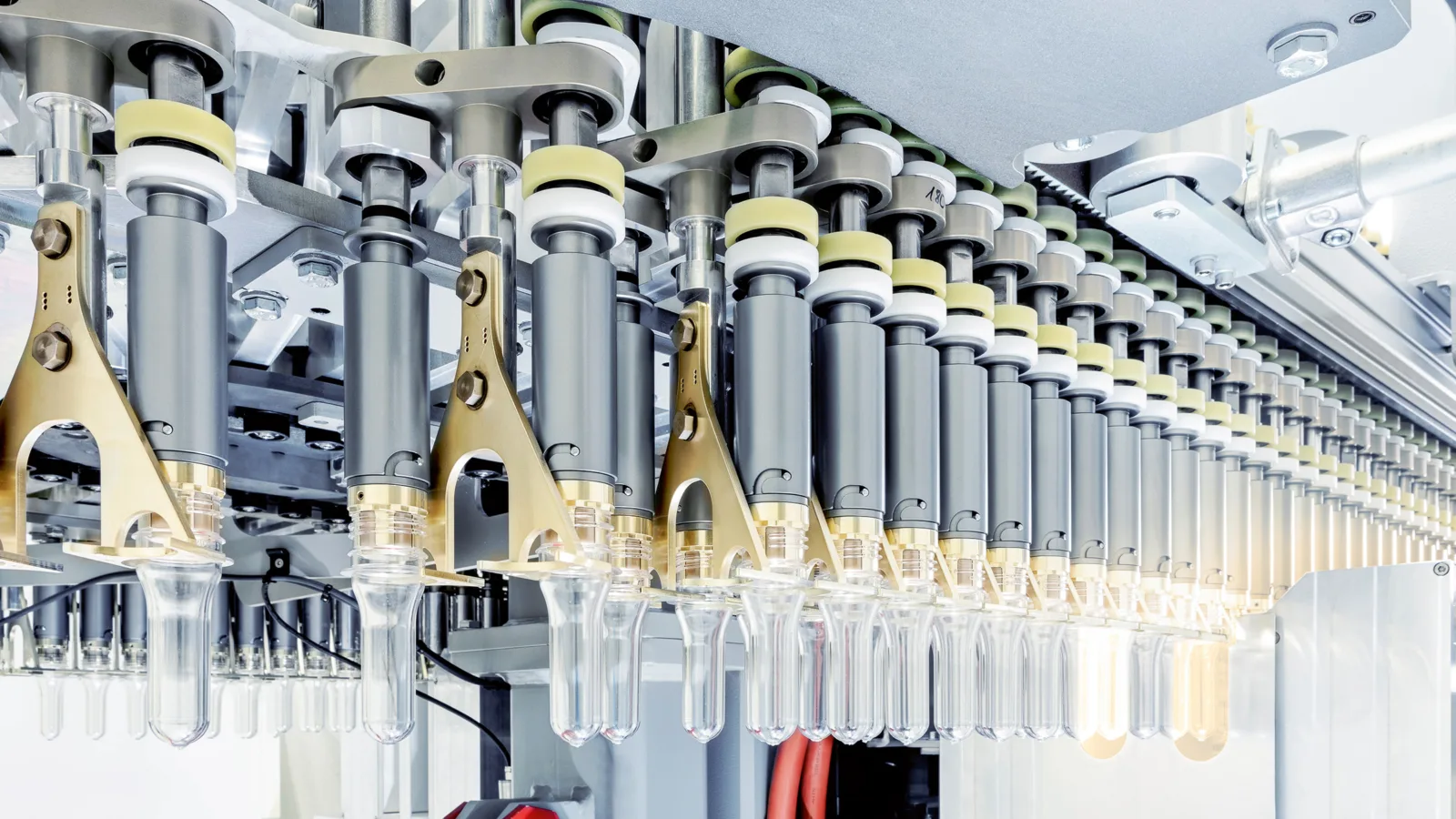
Even better in every respect
With its new generation of Blomaxes KHS Corpoplast shows how it has helped its successful formula to even greater triumph. Packed with a multitude of innovations, the latest generation isn’t just more powerful than its predecessor but above all also more sustainable and more economical.
For over 20 years the name Blomax has been synonymous with pioneering PET stretch blow molding technology the world over. With the recently launched fifth generation in its new InnoPET Blomax Series V KHS Corpoplast is setting standards with abundance – especially when it comes to sustainability and performance.
“Thanks to the close dialog we have with our customers we’re continuously improving our stretch blow molder,” emphasizes Marco Böhnke, product manager for Block and Stretch Blow Molding Technology at KHS. The new series, however, is distinguished by a whole host of innovations, some of them real trailblazers. “With the successful development of a completely new heating concept, the Double Gate or DoGa, we’ve now made a real advance in the technology,” explains Böhnke proudly. In the enclosed heating module the preforms pass through a double gate to the left and right of the near infrared (NIR) heaters, now arranged centrally for the first time. This procedure has enabled the preform pitch to be more or less halved to 18.5 millimeters and the number of heater boxes to be reduced by close to 50%.
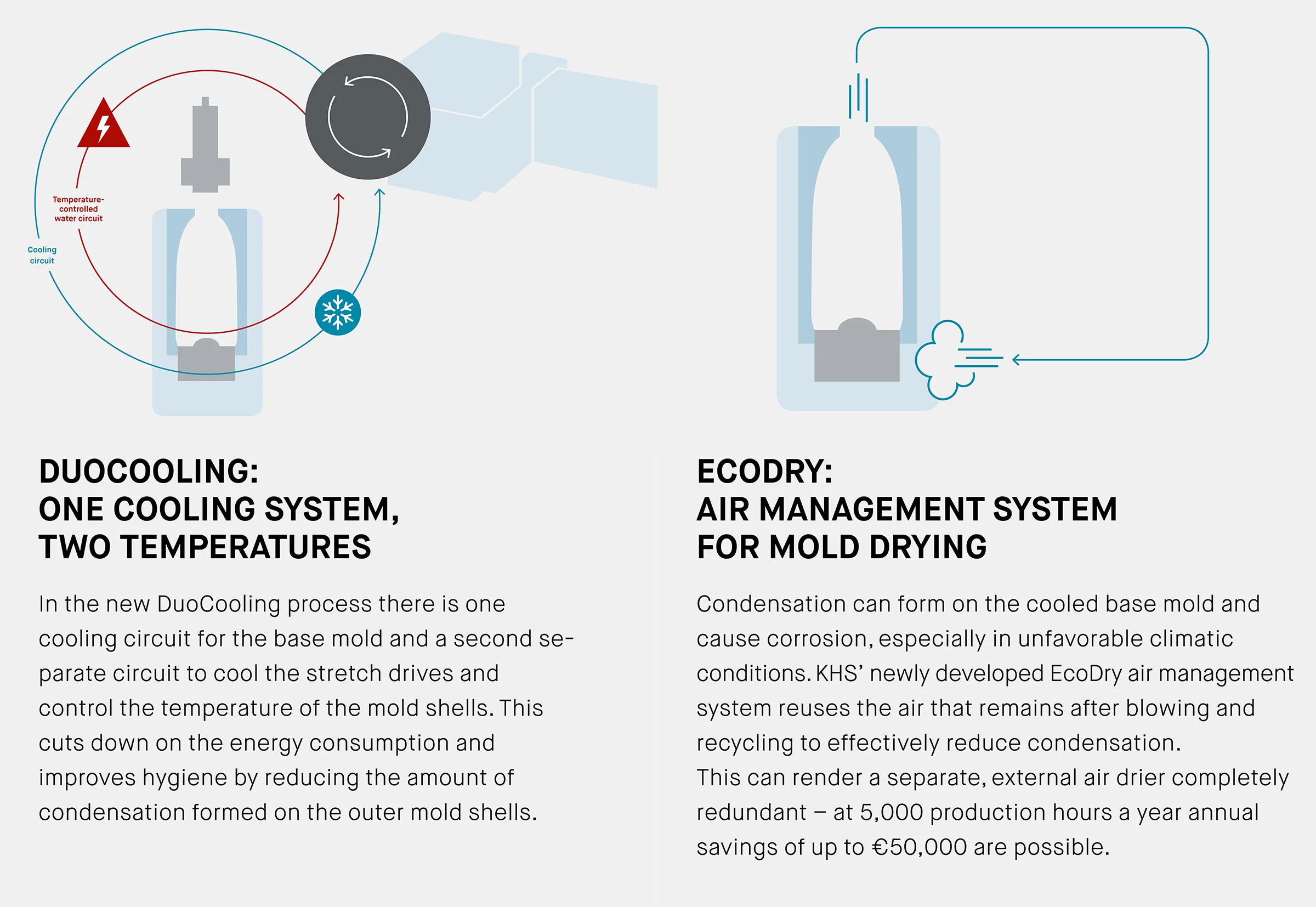
Lower energy consumption
Together with a further optimized reflector and newly developed air management system energy savings of up to 40% are made compared to the previous Blomax IV series. Efficiency is very important here: an improved valve block, which considerably reduces the volume of dead space, aims to provide customers with a machine which is as energy efficient as possible. With reference to their degree of sustainability KHS’ further developed stretch blow molders not only prove convincing with their lower energy consumption but also regarding their savings in material. For instance, an optional focus lamp specifically heats the area below the neck ring. This permits a better distribution of materials during the stretch blow molding process, allowing previously unstretched PET beneath the neck ring to now be used. This means that lighter preforms can be utilized. Reducing the amount of material used by one gram per bottle results in a saving of up to €300,000 at a production of 200 million bottles a year, for example.
Innovative cooling
The cooling concept is also new on the InnoPET Blomax Series V. The revolutionary process is known as DuoCooling which makes use of an external cooler with two cooling circuits with different temperatures. There is one cooling circuit for the base mold and a second circuit to cool the stretch drives and also control the temperature of the mold shells. Besides saving on cooling energy the system also reduces the amount of condensation formed on the outer mold shells. This helps to improve hygiene – an important aspect, especially when bottling sensitive beverages.
In combination with the EcoDry air management system, another new feature, the condensation which can form on the cooled base mold and occur in unfavorable climatic conditions in particular is also effectively reduced. EcoDry reuses the air that remains after blowing and recycling and can render a separate, external air drier completely redundant. The permits a further €50,000 maximum to be saved per annum at 5,000 production hours a year.
The InnoPET Blomax Series V also earns top marks for its performance and flexibility. The modular platform concept has six to 36 blow stations with a specific capacity of up to 2,500 containers per hour and station. Depending on the required application KHS offers two variants: the standard blow station for container volumes of 0.1 to 3.0 liters or a microstation for bottles holding between 0.1 to 0.75 liters, depending on the bottle design. In the midst of all this technological complexity KHS has of course not forgotten the operator: the optimized Human Machine Interface (HMI) with self-explanatory operator prompting on a 21-inch multitouch display permits intuitive and simple operation. The new key-in-pocket door safety system, available as a basic component, is also creating milestones in this new generation of machines.
Milestones in KHS stretch blow molding technology
1975 The beginning
Following successful experiments to blow mold bottles in 1968, the stretch blow molders built by the newly founded Corpoplast company are now ready for market. Their output starts at about 200 bottles per hour and cavity. This gradually rises to 850 bottles per hour until the launch of the next generation.
1994 The second generation
Corpoplast presents the next generation with its B 177 machine which can produce around 1,100 bottles per hour and cavity. The preferential heating method is one of its notable new features where an adapted preform heating profile facilitates improved material distribution.
2000 Blomax Series III
To mark improvements in design engineering and increases in capacity, in 1998 the machine program is given the new name of Blomax. In 2000 the Blomax Series III is launched to market. It comes with six to 20 cavities, each of which can blow mold up to 1,500 bottles an hour.
2009 Blomax Series IV
At a rate of up to 72,000 bottles an hour Corpoplast again sets a new world record. This includes, for instance, its near infrared (NIR) heater, which cuts the amount of energy used by approximately 30%, or its CLeverLoc blow stations, where the mold is closed by toggle levers without the need for additional locks.
2018 Blomax Series V
Above and beyond its constantly optimized, tried-and-tested technology the fifth generation scores over its predecessor with a number of new and further developments. It not only ensures greater sustainability but also provides an even higher throughput of 2,500 containers maximum per hour and cavity.
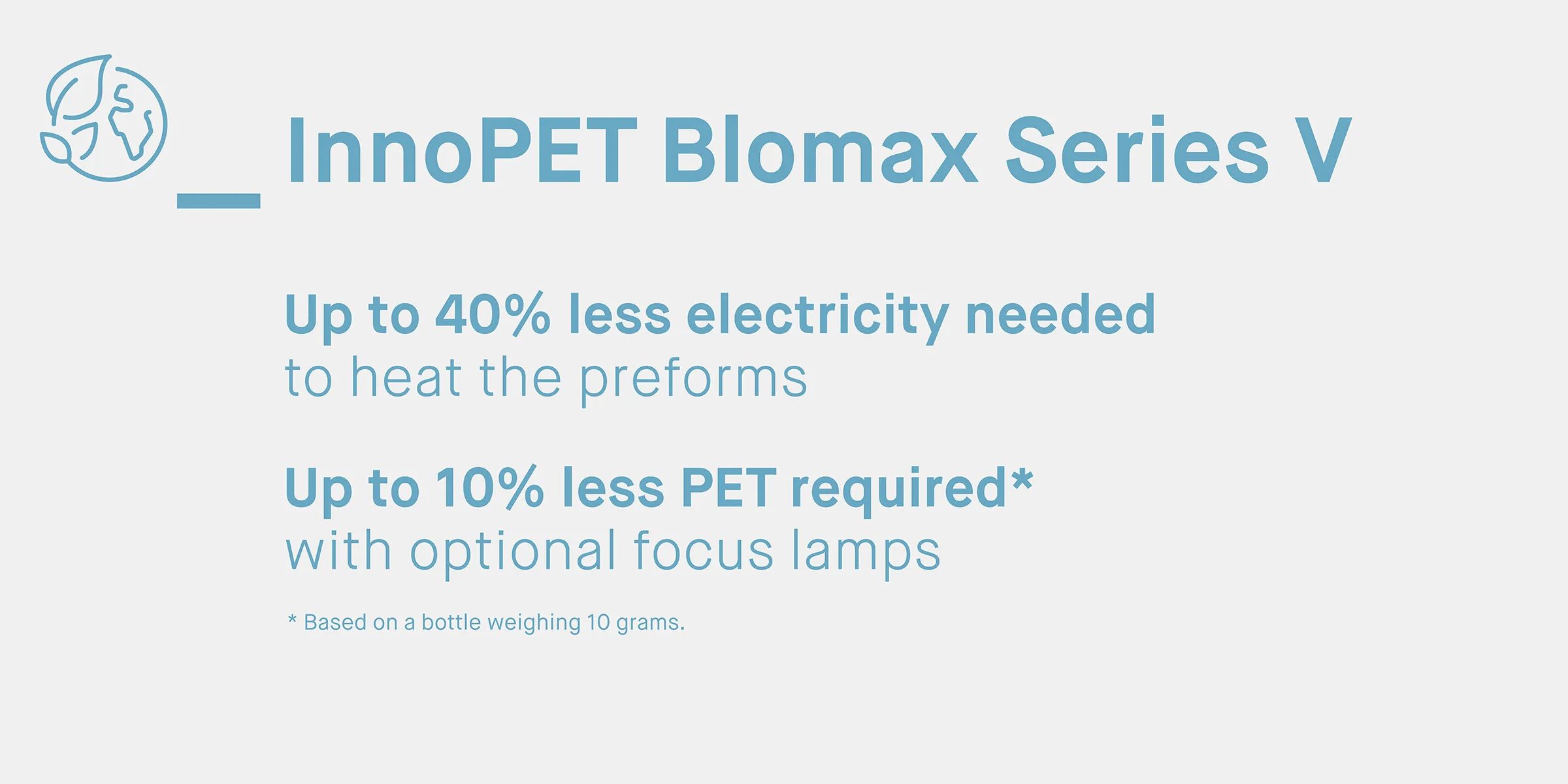
Technological quantum leap
It’s thus no surprise that Marco Böhnke is pleased with the technological quantum leap made by the latest machine generation. “We’re very proud that once again we’re setting a number of new benchmarks with the InnoPET Blomax Series V.” It goes without saying that this progress is not merely an end in itself. “We want to pass on the knowledge gleaned and benefits reaped from our new Series V to our customers so that they can produce even more efficiently and sustainably.”