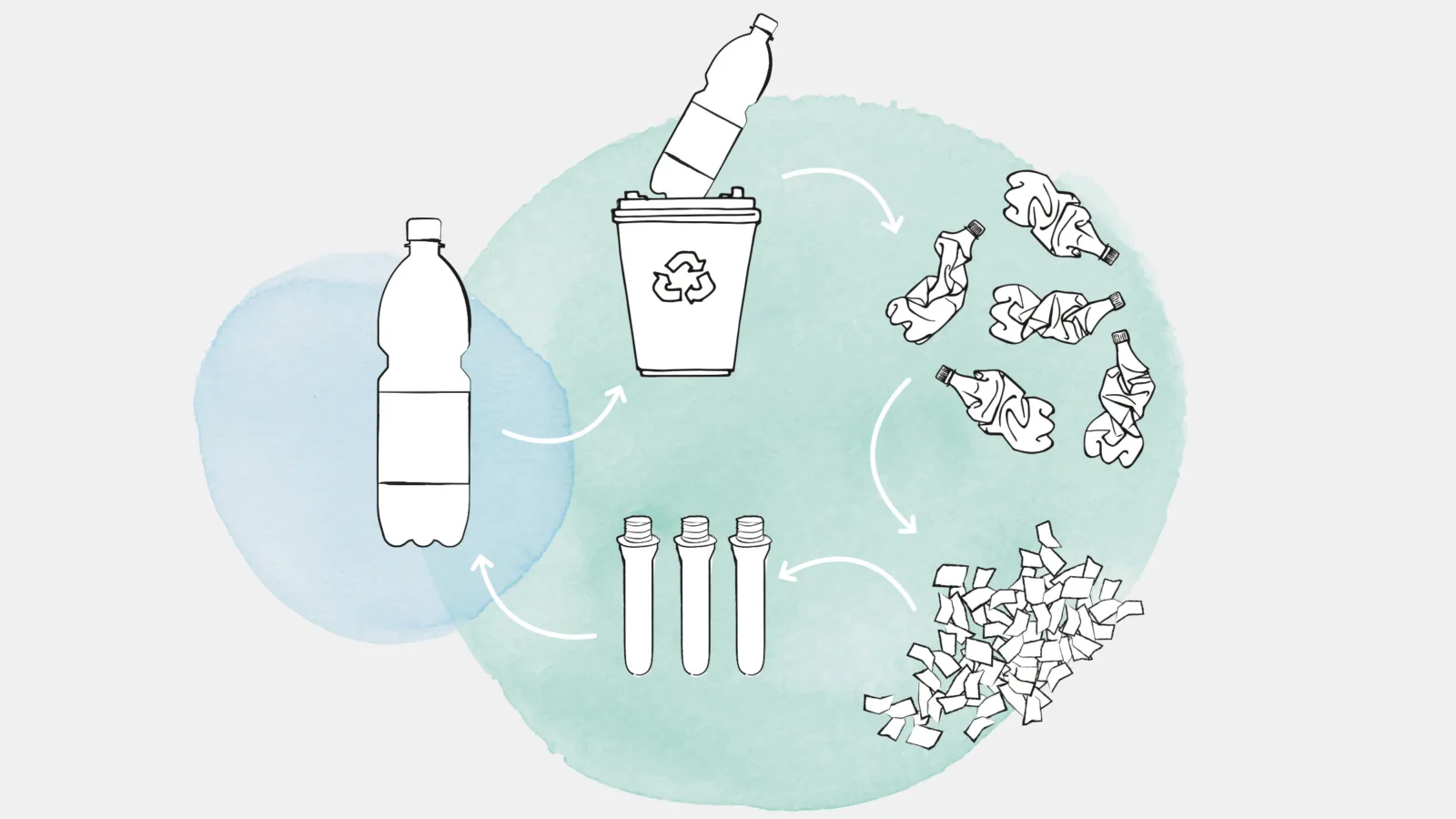
A constant cycle
Increasingly environmentally-friendly legislation is presenting juice and nectar producers with major recycling challenges. In this context KHS provides the only barrier system which allows materials to be fully segregated and completely recycled: FreshSafe PET®.
Throughout Europe manufacturers are not only responsible for the quality of their products but also for the avoidance, reuse and recycling of their packaging. This is regulated in Germany by the new German Packaging Law. In effect since the beginning of this year, it aims to reduce the impact on the environment with various measures designed to prevent waste. With returnable systems the mandatory quota has risen to 70% from the 42% previously obtained. Recycling quotas have also been significantly raised. This applies to plastic packaging in particular: where in Germany only about 36% of this was recycled to date, the new legal recycling quota is now 58.5%. This will rise to 63% in 2022.
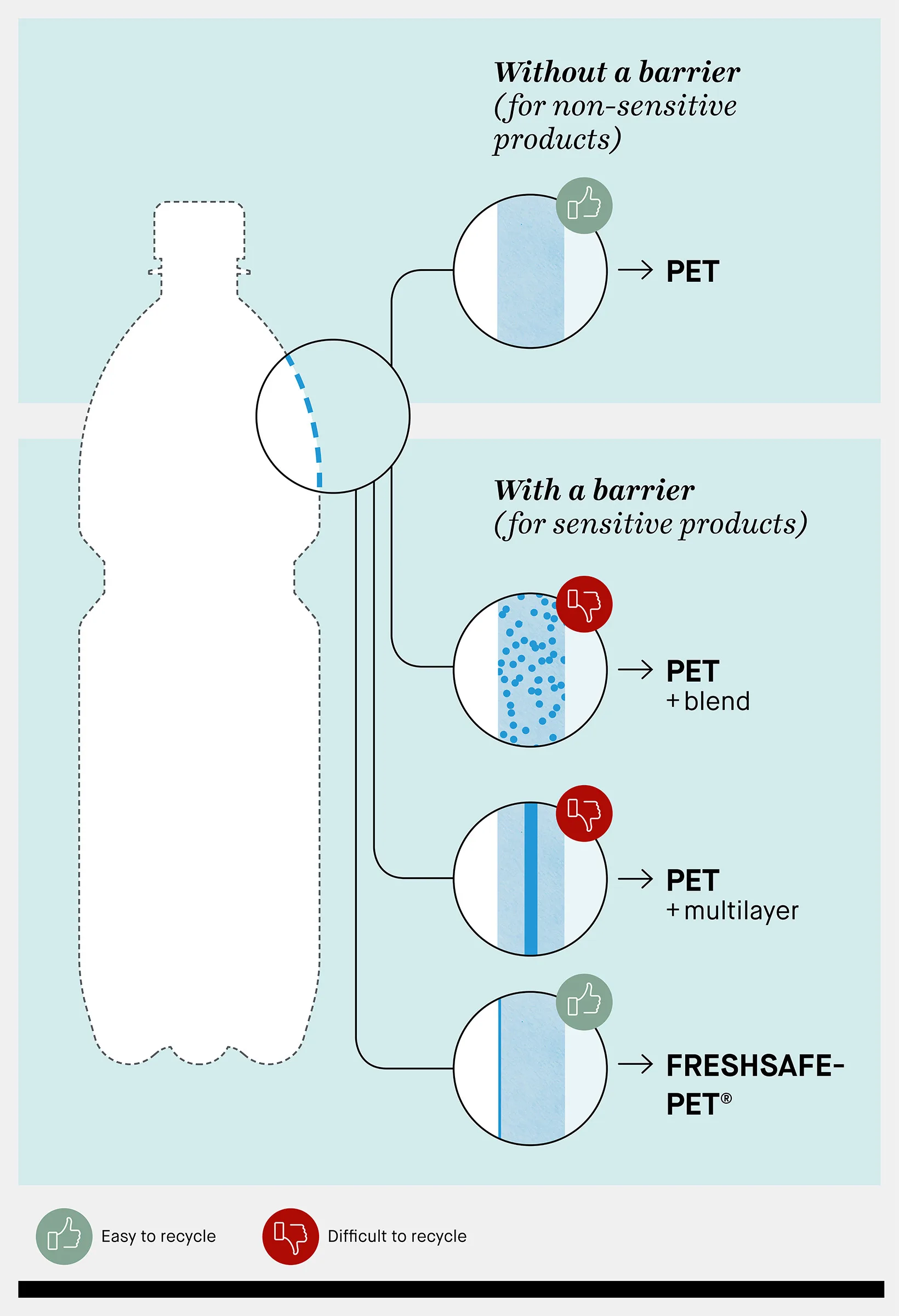
Recyclability – One-way PET bottles PET bottles without a barrier coating (for non-sensitive products) produce 100% pure PET in the recycling process. In plastic bottles with barrier protection (for sensitive products) the additives are practically inseparable from the PET – except with FreshSafe PET®. Here, the protective layer is simply washed off during the recycling process.
Financial incentives
In Germany dual waste disposal systems are responsible for the collection, sorting and reuse of recyclable waste. They are obliged to increase the use of highly recyclable packaging and of recyclate and renewable raw materials in the future by providing financial incentives: those manufacturers who use materials in their packaging which are easy to recycle pay a lower fee for participating in the scheme. Those who use composite or other materials which are more difficult to recirculate pay more.
The new regulation also affects producers of juice and fruit nectars who fill their products into non-returnable PET bottles and don’t take part in the established deposit system. These beverages must be protected from external influences such as oxygen pickup. Many juice and nectar bottles made of PET use inseparable multilayer or blended materials to this end as oxygen absorbers. These additives make them less simple to recycle than the normal PET bottle since despite being subjected to elaborate processes the various materials can’t be separated and cause discoloration of the recyclate, for example. This complicates global recycling with non-returnable PET containers and renders bottle-to-bottle recycling, for which colorless rPET is required, practically impossible.
If juice and nectar bottles were to be integrated into the German deposit system, it would be much more difficult to produce clear, transparent PET bottles made of rPET. Approximately 10% of all non-returnable PET bottles currently do not carry a deposit. This means that up to 38,000 metric tons of used PET bottles bypass the deposit system each and every year.
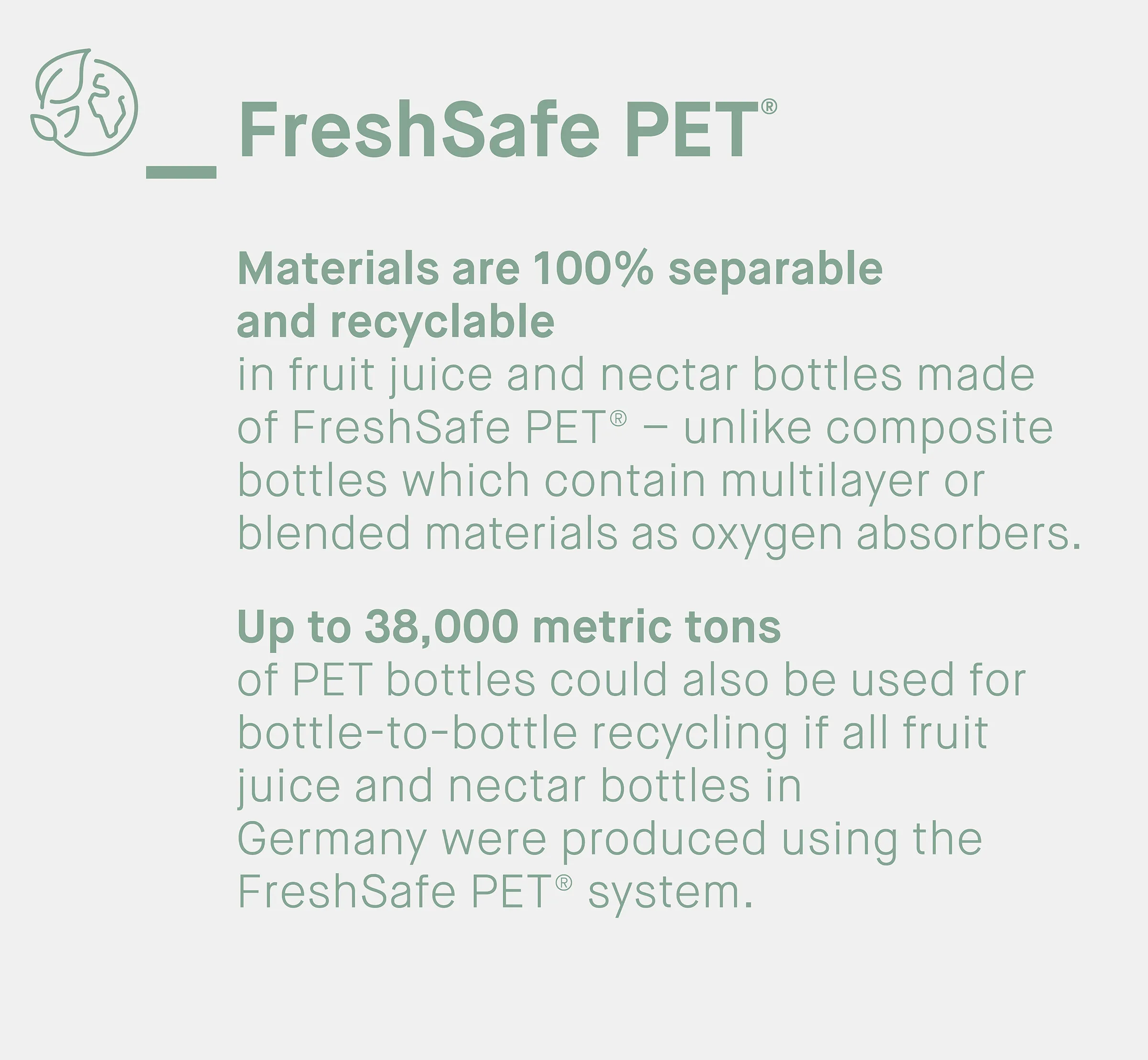
Possible ban
Non-returnable PET bottles which are difficult to recycle could not only be subjected to higher contribution fees in the future but also threatened by a complete ban – and not just in Germany. The European Strategy for Plastics recently presented by the EU requires that all plastic packaging must be reusable or recyclable by 2030. Various national initiatives are following suit. In France, for instance, only recyclable plastic packaging and material combinations will be permitted by 2025. In Great Britain new PET plastic packaging is to consist of an average of 30% recycled PET. More and more multinational beverage producers have also begun to set themselves much higher recycling targets. The Single-Use Plastics Directive stipulates that by 2030 beverage packaging must contain 30% recyclate.
Many fruit juice producers are already optimizing their packaging portfolio so that it can be fully recycled. One unique system in this respect which has proven itself on the market is FreshSafe PET® technology from KHS. In this system the inside of the PET bottle is coated with a wafer-thin layer of glass immediately after the stretch blow molding process. It forms a barrier which stops flavors and carbon dioxide from escaping and oxygen from penetrating the bottle, thus preventing loss of vitamins. Taste and freshness are retained longer in the coated FreshSafe PET® bottle. In the recycling process the layer of glass is simply washed off by the caustic in a standard process. Premium juice producers such as the Eckes-Granini Group are already using this sustainable technology – with much success.
A short video shows how Freshsafe PET® protects high-quality beverages and also helps to reduce waste.
Intelligent on several counts
Investing in this technology not only pays off as it incurs lower fees thanks to 100% bottle recyclability but also yields a number of further economic benefits: bottlers can switch to less expensive standard PET preforms, for example. And they gain from an improved product quality: compared to conventional composite materials the unique KHS system has a much better barrier effect and considerably lengthens shelf lives – with the total costs per bottle lower at the end of the day. FreshSafe PET®, for which demand is increasing the world over, thus helps to substantially increase recycling quotas for PET beverage packaging – also way beyond Germany’s national boundaries.