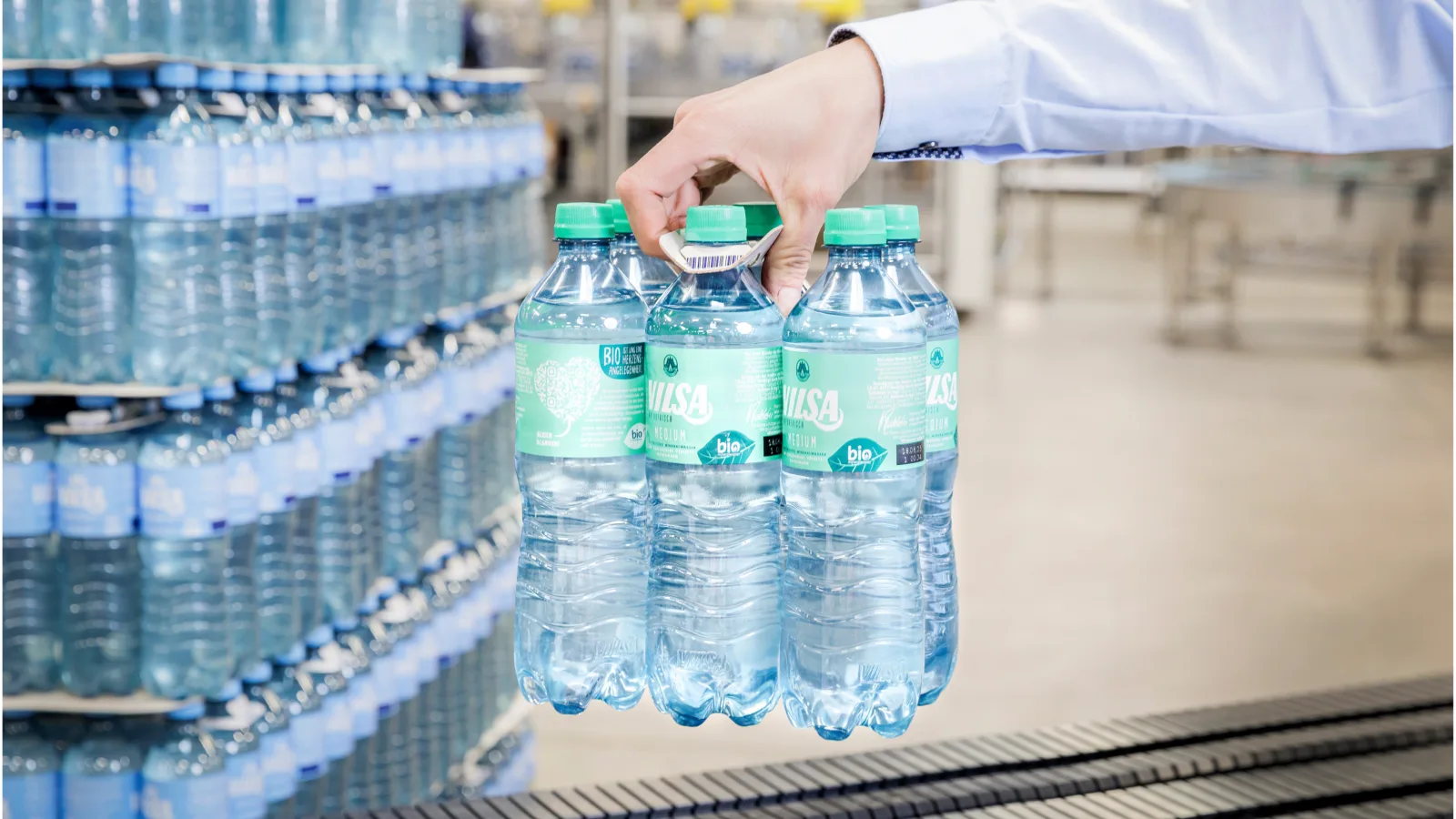
First Mover
Nature, responsibility and quality form the basis of VILSA-BRUNNEN’s company philosophy. In its effort to become ever better, the mineral water bottling plant makes consistent use of new technologies – with KHS as a partner it can depend on.
While still in kindergarten, Henning Rodekohr and his sister used to plant trees with their parents in their local surroundings. When the children then later sold their toys at yard sales, the proceeds were donated to various nature conservation projects. “We grew up with the deep conviction that here we live in, with and of course off the gifts of nature,” says Rodekohr, managing partner of VILSA-BRUNNEN. He runs the family business in Bruchhausen-Vilsen in Lower Saxony, Germany, now in its fourth generation. “For us, this means we hold great responsibility which we’ve expressed in our motto of ‘protecting tomorrow today’. In other words, we do our bit wherever we can to ensure that our future world remains as intact, natural and habitable as possible.”
High demand for quality
At product level, what VILSA calls its ‘pledge to nature’ perfectly expresses this philosophy. “Our mineral water has been a carefully guarded, unspoiled treasure for thousands of years. This is why we protect our natural spring so that it can also reliably supply generations to come,” explains Rodekohr. “And we impose heavy restrictions on ourselves: the VILSA brand doesn’t use any colorings, artificial flavorings, preservatives or sweeteners.”
VILSA-BRUNNEN
Fact check
1908
Brothers Georg and Jonny Dörgeloh discover a bubbling spring in Vilsen that in 1912 is officially entered in the commercial register.
531
million liters of product were bottled in 626 filling processes in 2024 – a respective increase of 9% over the previous year.
No. 3
among Germany’s returnable brands, leading brand in Northern Germany.
100%
recycled PET is used to make all non-returnable VILSA bottles.
> 500
employees work at the Bruchhausen-Vilsen plant in Lower Saxony, Germany.
www.vilsa.de
Unique product protection
The company makes similarly high demands of the quality of its packaging as it does of product quality. “When we use organic raw materials in our soft drinks Plus Bio or Bio Limo, for instance, we naturally want our products to reach our consumers in perfect condition,” Rodekohr emphasizes. He’s found the best means of doing so in the FreshSafe PET system from KHS. Here, with the help of Plasmax technology developed by the Dortmund systems supplier, the insides of non-returnable bottles made of recycled PET are coated with a wafer-thin layer of silicon oxide. This unique form of product protection guards sensitive beverages against oxygen pickup and carbonated products from loss of CO2.
Longer shelf life, unadulterated quality
VILSA-BRUNNEN had the very first latest-generation Plasmax machine installed in 2023. On this InnoPET Plasmax 80ER, non-returnable PET bottles can be coated at a speed of up to 24,000 an hour. The machine is blocked with an InnoPET Blomax stretch blow molder in an InnoPET FreshSafe block – the former also a model of the newest generation. Outputs of up to 48,000 containers per hour are possible. “Thanks to this fantastic system, we can lengthen the shelf lives of our products and ensure their unspoiled enjoyment,” the businessman smiles. “The coating is completely invisible and the plastic bottles can be excellently recycled without any great effort being involved.” The bottlers in Vilsen are so pleased with this concept that all of their beverages filled into non-returnable PET bottles now have product protection, even their pure mineral water – which is a total novelty on the German market.
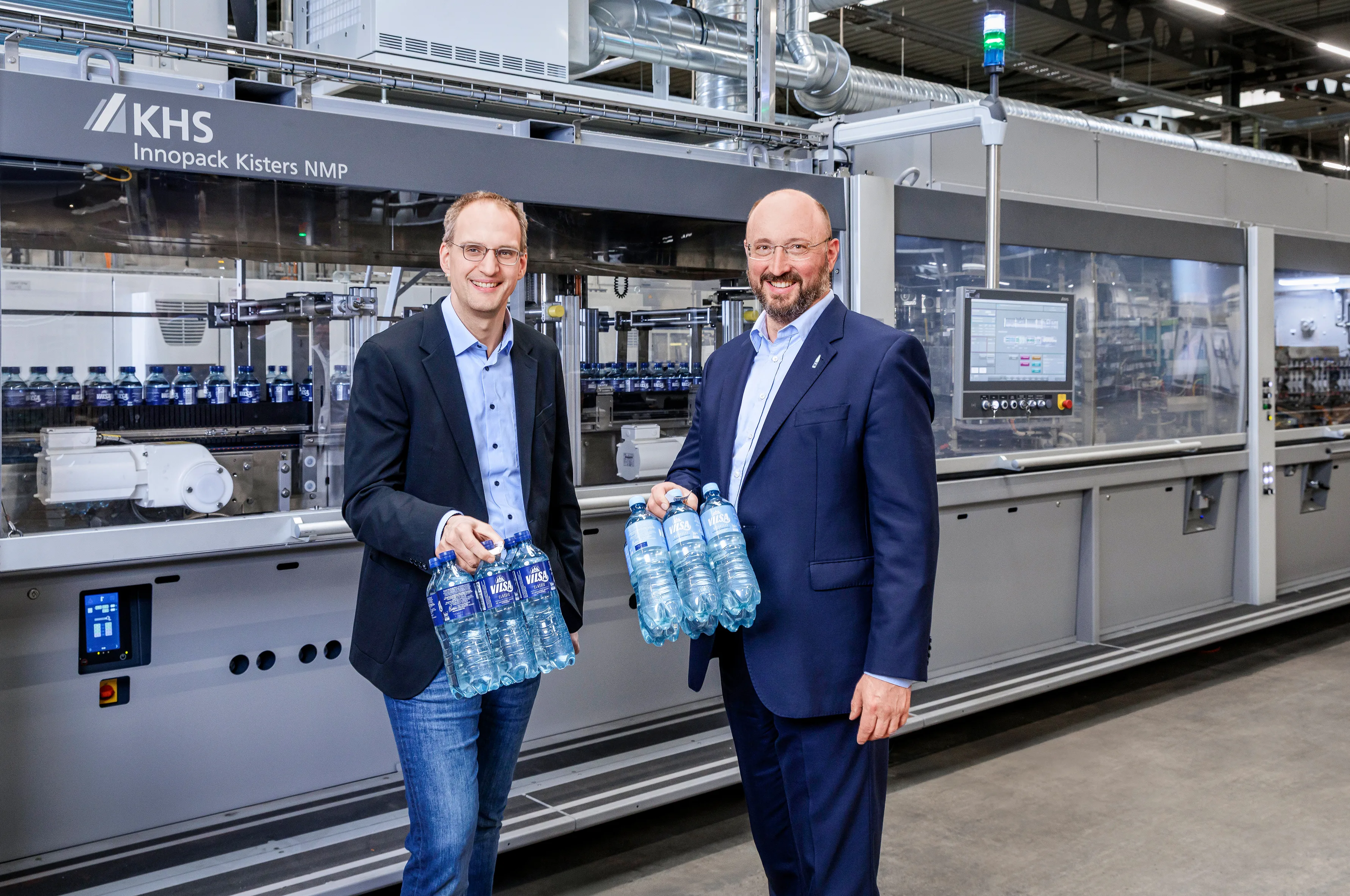
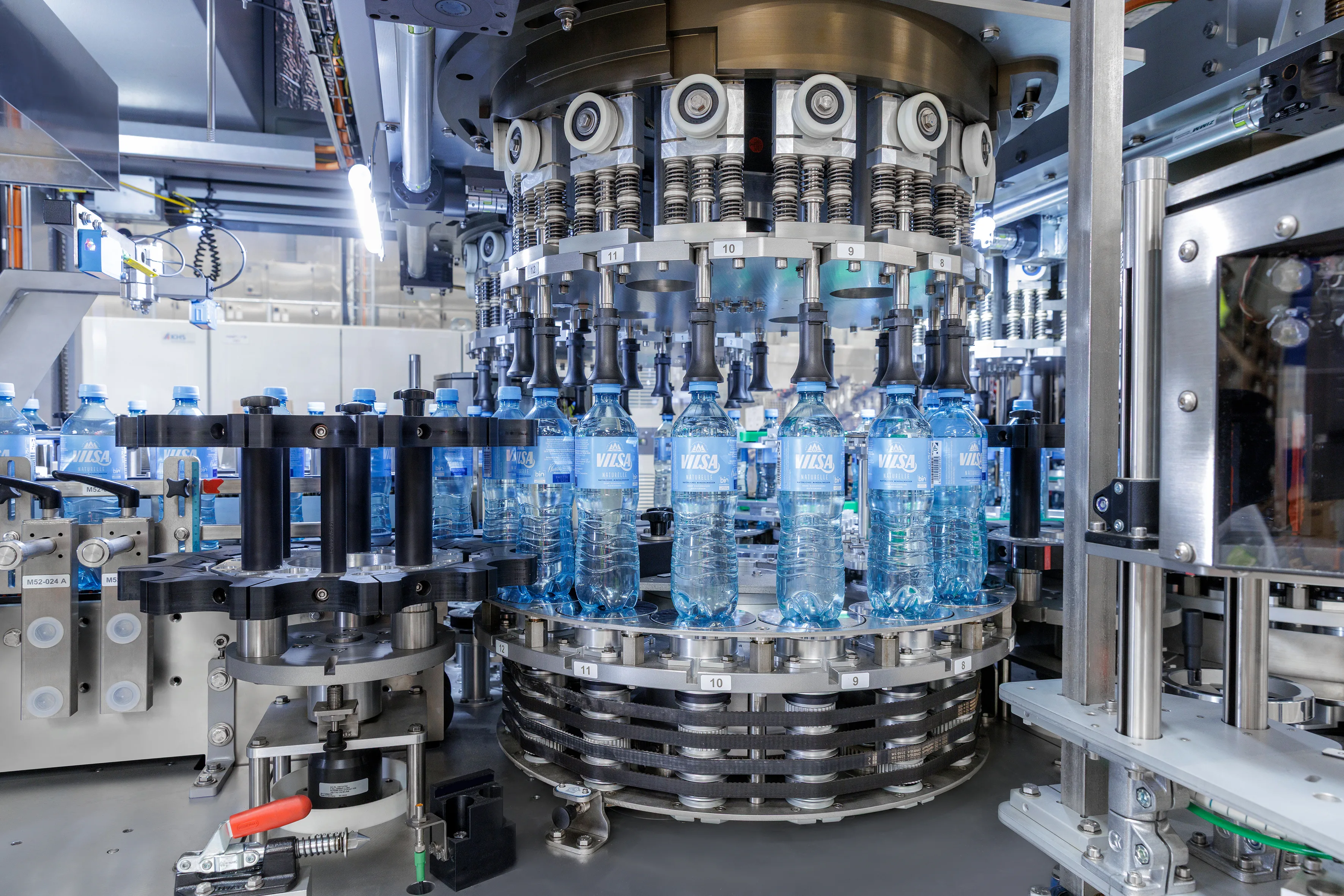
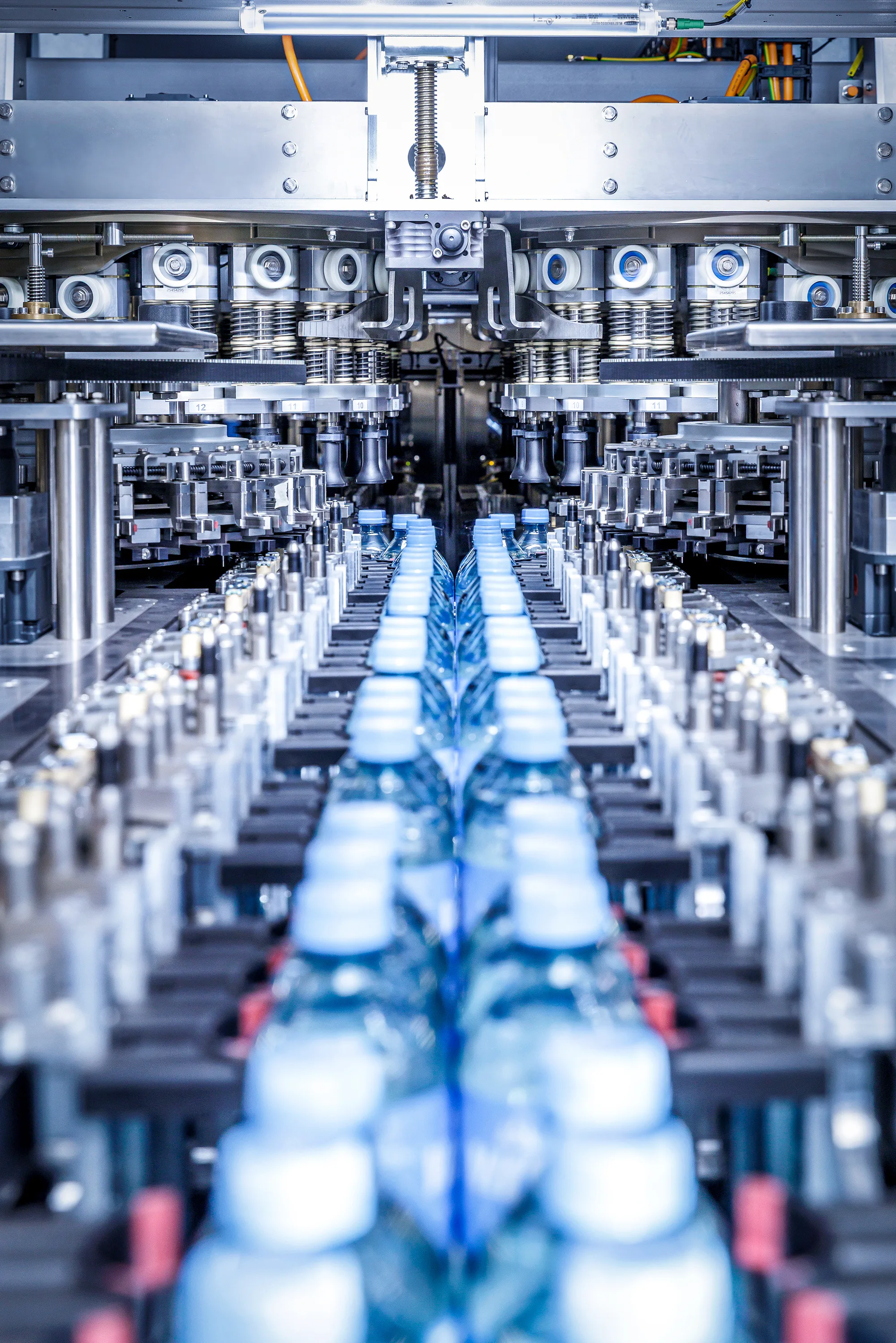
Reliable partners embracing new avenues: Henning Rodekohr, VILSA-BRUNNEN, and Dr. Matthias Caninenberg, KHS, are delighted with the NIX-PACK without any film.
Resource-conserving secondary packaging
Rodekohr is positively electrified by a further KHS packaging system he has invested in: Nature MultiPack or NMP turns PET bottles into packs using not shrink film but just a few dots of adhesive. “With Nature MultiPack, we save 2,000 kilometers of film a year, which amounts to 50 metric tons of plastic. Depending on the container size, we thus cut our CO2 emissions by around 40 to 70%.” Once again, VILSA is a first mover by introducing this resource-conserving style of secondary packaging to the German beverage and food retail trade on a broad scale for the first time.
Positive response from retailers
The latter – otherwise usually less welcome to change – has shown itself to be just as enthused as the beverage producer. “Getting rid of shrink film is an important, eye-catching new direction for retailers,” Rodekohr claims. “Who hasn’t ever been annoyed by untidy-looking shelves of non-returnable packs with the packaging torn open?” VILSA has been familiarizing its customers with the new format since May 2025 through a creative, cross-media campaign – marketing its NMP under the name of NIX-PACK, a word play on “six pack” and the German word “nichts” or nothing. Beforehand, its conventional shrink packs had advertised the impending switch with “This film will soon disappear as if by magic” printed on them.
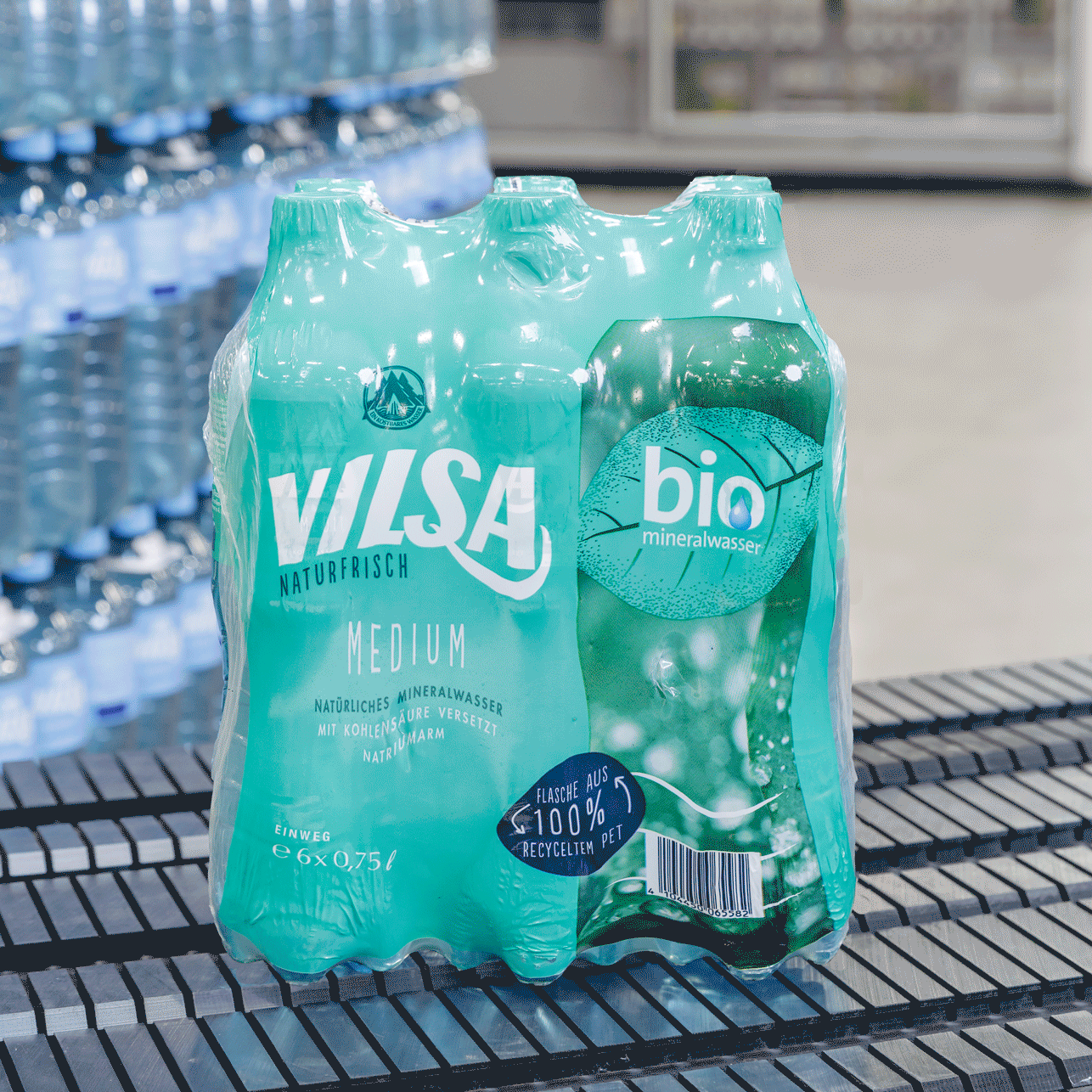
Since May 2025, VILSA has been introducing its customers to its new, climate-friendly secondary packaging and the disappearance of the shrink film it used to use in a marvelously magical manner!
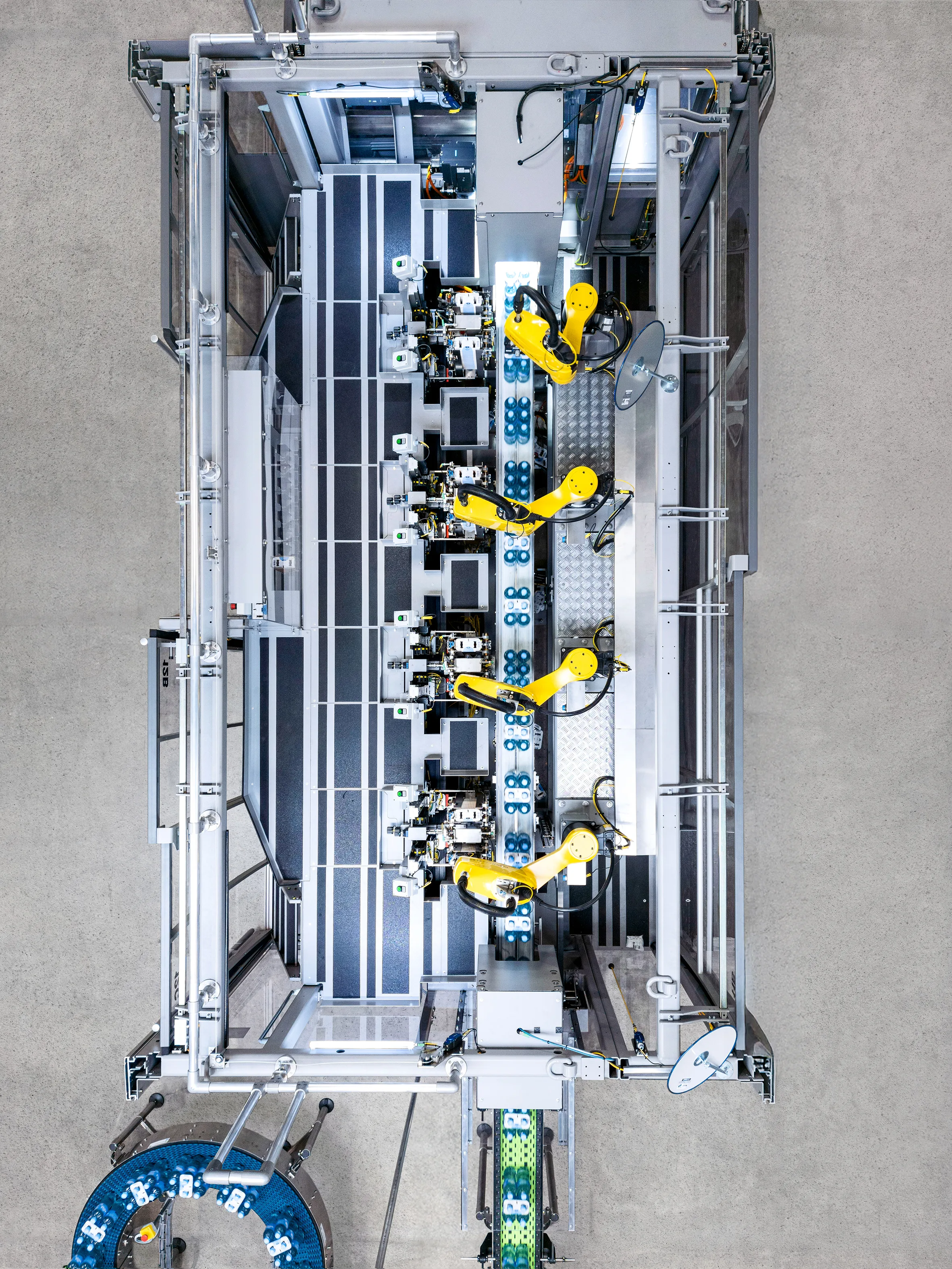
The BottleClip Carrier, a minimalist carrying handle made of kraft paper, is attached by the new robot clip applicator – that needs much less space to do so than the previous module for carrying strips consisting of plastic film.
Much smaller carbon footprint
The packs are produced on the most up-to-the-minute KHS machine currently in operation, an Innopack Kisters NMP-M that at VILSA turns up to 24,000 bottles holding between 750 milliliters and 1.5 liters into packs of six every sixty minutes. Up to 108,000 containers can be processed per hour. One notable feature of this machine over its predecessor is its much smaller carbon footprint. “To this end, we first reduced the setting station to half of its former length,” explains Dr. Matthias Caninenberg, head of Nature MultiPack Technology at KHS in Kleve. “And we’ve developed new, very small, user-friendly carrying handles made of recycled kraft paper. Four robots flexibly clip these onto two bottles in each pack that can consist of two to ten containers. Unlike the handle applicator module that applied the previous carrying strip made of plastic film to the pack in 17 different individual functions, the new robot clip applicator takes up much less space. This has shortened the entire machine by about seven meters and made it shippable in a single container.”
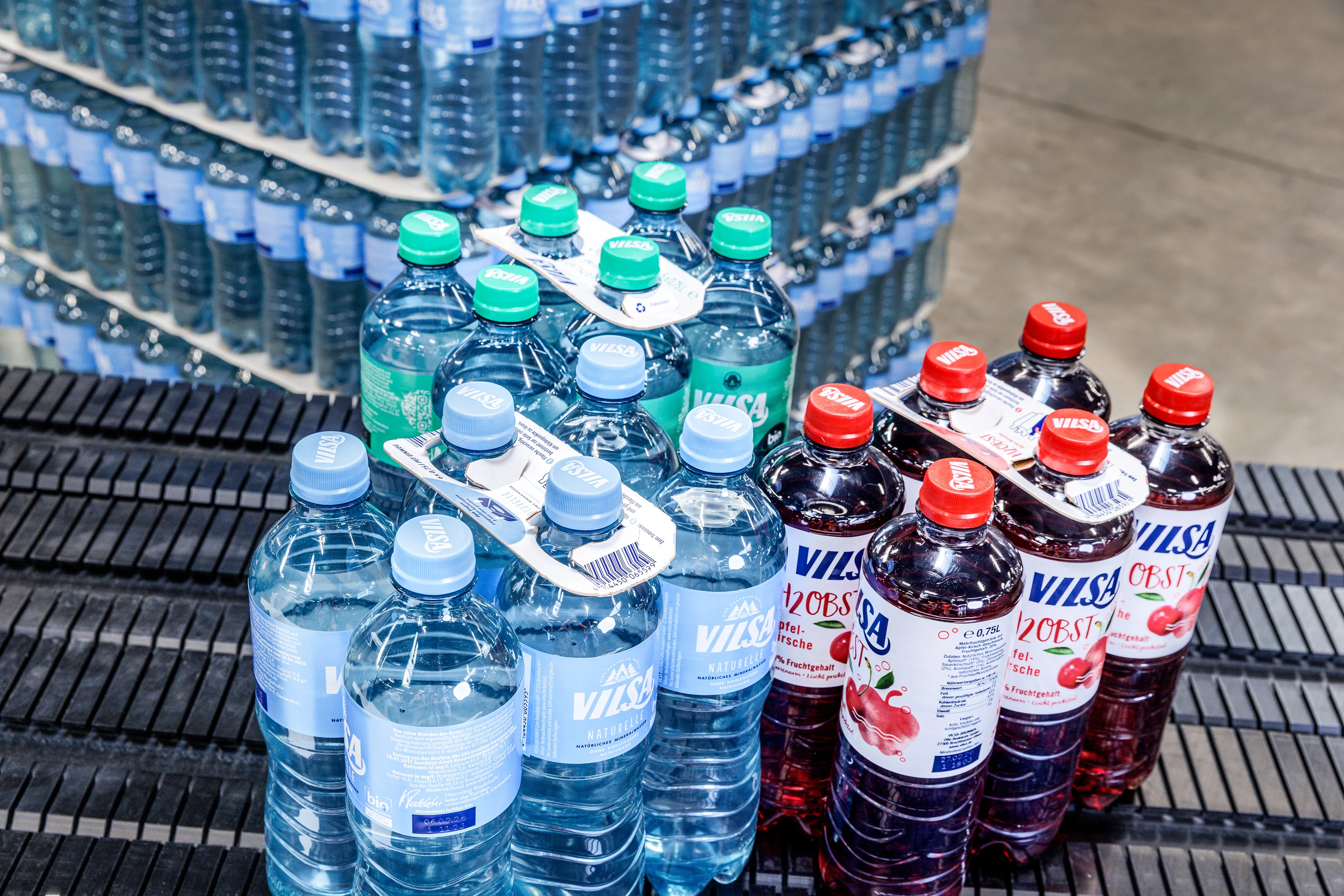
The entire VILSA product portfolio in non-returnable PET bottles – here, just a small selection – benefits from invisible Plasmax product protection, climate-friendly Nature MultiPack and the minimalist BottleClip Carrier.
Simple operation
What’s more, an innovative loading concept has also lessened the amount of operator involvement. The new carry clips are supplied in boxes of 215 by the blanks magazine and removal chutes. They are inserted according to the Poka-Yoke principle that makes operating errors practically impossible. They are then automatically conveyed to the robots and fed into one of two robot magazines.
“We can only successfully embrace new avenues such as these with a strong and reliable partner like KHS.”
![]()
Managing partner of VILSA-BRUNNEN
Reliable technology partner
Henning Rodekohr explains why it’s important for his company to be a technological first mover. “Of course there’s always a certain development risk involved when investing in a system that’s not yet established itself on the market,” he states. As an entrepreneur, he believes it’s more important to adopt a long-term perspective that’s more likely to pay off rather than trying to make a quick buck. “We do this to help technologies we think are good, right and promising to achieve a breakthrough – both in the interests of our company and of our entire industry. This only works with a strong partner, however, whom you can rely on 100%. It’s therefore good to know that with KHS, we can successfully embrace new avenues like these.”
Looking to the future, Rodekohr wants to remain open to inspiration and curious about innovation in order to become a little better each and every day – also in constant dialog with his systems provider.
Facilitator: three KHS technologies for VILSA
With three pioneering systems, Dortmund engineering company KHS is helping the VILSA beverage brand to meet its ambitious sustainability targets and at the same time give consumers the best possible packaging.
Plasmax: long shelf lives for sensitive products
Thanks to revolutionary Plasmax barrier technology from KHS, up to 60,000 PET bottles an hour can be covered with a wafer-thin interior coating very similar to glass. This system combines highly effective product protection with 100% recyclability by material type and unrestricted use of recyclate.
On the one hand, the barrier protects carbonated soft drinks and water from loss of CO2. On the other, it prevents oxygen pickup in bottles of sensitive beverages which would cause the product to suffer. Beverages filled into Plasmax-coated containers keep for six months and longer.
In order to recover pure PET which can be fully reused from empty bottles, the layer of silicon oxide is simply washed off during the recycling process.
Nature MultiPack: waste prevention and climate protection
Already PPWR-compliant and perfectly set up for the future: the unique Nature MultiPack (NMP) from KHS is an outstanding example of climate-friendly packaging in the beverage industry. In place of shrink film, paper or cartons, here just a few dots of adhesive are needed to turn PET bottles or aluminum cans into packs. Compared to conventional systems that use shrink film as secondary packaging, NMP requires up to 85% less material and in the best case reduces energy consumption during production by two thirds.
Foaming the adhesive during application gives the dots greater elasticity with a triple benefit:
- Firstly, the consumer can separate the bottles from one another more easily.
- Secondly, damage to the PET bottle is prevented as it is separated from the pack.
- Thirdly, the flexibility of adhesive and pack ensures safe transportation.
BottleClip Carrier: minimalist carrying convenience
So that Nature MultiPack can do without any plastic having to be used for shipping, together with the Hinojosa Packaging Group KHS has developed a carrying handle made of cardboard. This is slotted by a robot onto two bottles in the pack, regardless of how many this actually contains. The carrier is large enough to include product information and the multipack barcode – but at the same time is as small and as stable as possible. This not only makes for a minimized carbon footprint; as opposed to standard handles made of plastic film that often cut into the shopper’s hands, the cardboard carrier is far more pleasant to grip and transport.
Any further questions?
1. PPWR = Packaging and Packaging Waste Regulation, the packaging directive passed by the European Union at the end of 2024 that provides the updated legal framework for packaging and packaging waste in the EU.