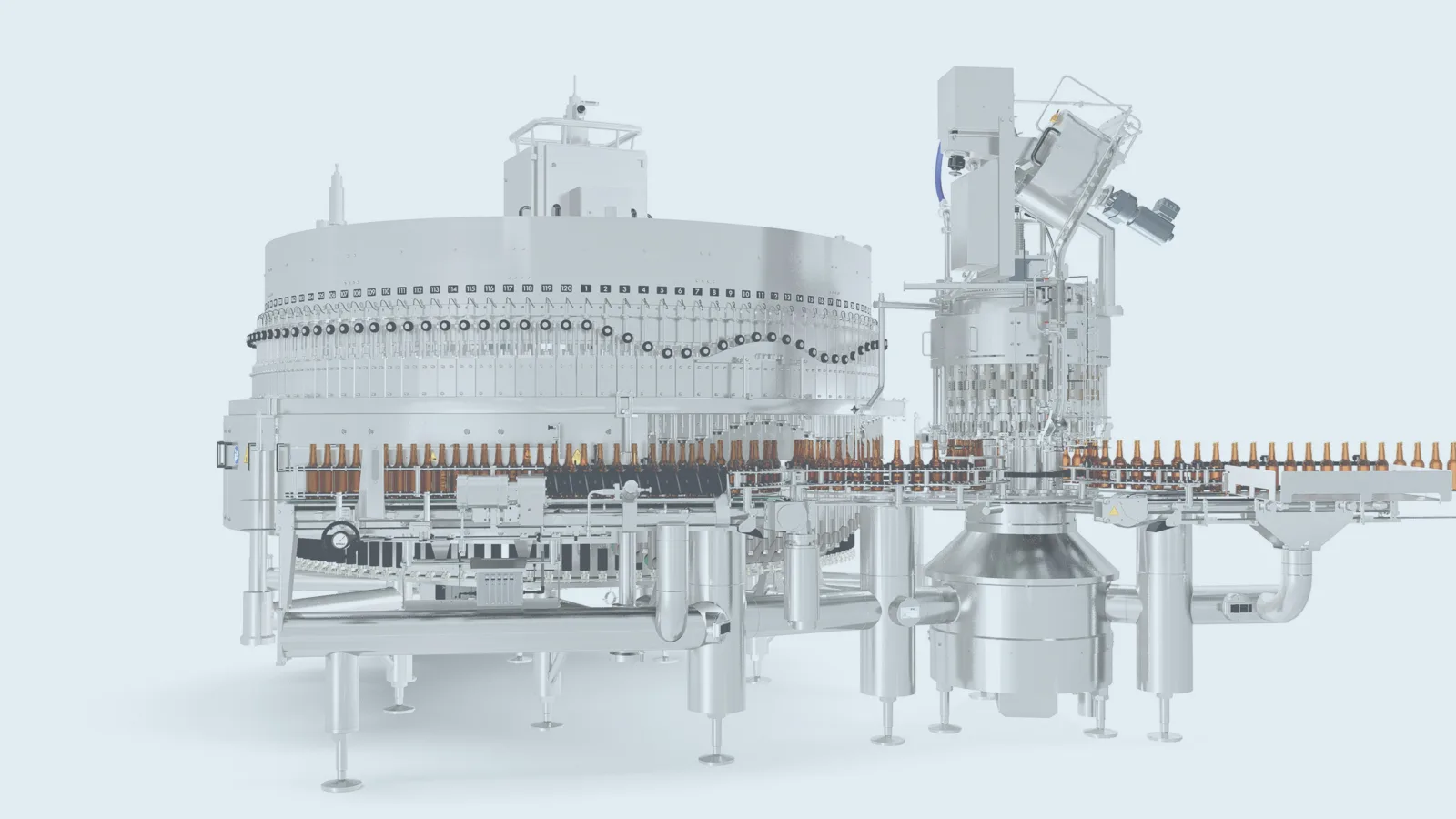
clever and smart
A perfect mix: the Innofill Glass DRS ECO combines a tried-and-tested filling system with new, digital technologies. The glass filler thus scores on both efficiency and sustainability.
The world of brewing is in constant flux: time and again traditional companies find themselves addressing new niches on the market in order to combat stagnating or declining sales figures. Although adding mixed beer beverages or soda pop to the range of products diversifies the portfolio and lowers the risk to sales it also makes production all the more complex.
Accordingly, high demands are made of the flexibility and efficiency of the brewery’s plant technology – and especially its filling and packaging equipment. As a reliable partner to the beverage industry, Dortmund systems supplier KHS has been meeting such demands for years.
The most recent example of this is the new, sustainable generation of glass fillers. “Our new filler is based on our fully automatic, computer-controlled filling system which has proved itself in practical operation,” explains Manfred Härtel, filling product manager for KHS in Bad Kreuznach, Germany. “What’s new is the modular machine design with countless optimized features. These include a standardized basic structure and standardized components in order to make installation and commissioning as efficient as possible. And thanks to improved availability we can also deliver faster.” The machine’s modular design also gives customers greater security for the future, emphasizes Härtel. “Customers who invest in a base machine now can retrofit it with additional components in the future – according to the changes in the beverage market and their own production policies.” The system couldn’t be more flexible.
»Customers who invest in a base machine now can retrofit it with additional components in the future.«
![]()
Filling product manager for KHS
More efficient, sustainable and intelligent
The Innofill Glass DRS ECO also includes a whole host of new future-proof technologies which make the filler more efficient, more sustainable and more intelligent. These include, for example, continuous, infinitely variable regulation of each individual filling valve and digital camera-based systems which monitor and control the filling process. All told, compared to the previous model these help to boost the machine’s performance and bring about considerably lower energy and media consumption. They also allow precise reproduction of top product quality and ensure maximum product safety.
Another plus is the machine’s hygienic design. This enables a free runoff of liquids and simplifies cleaning. It also means that cables and lines are installed in the frame tubes, individual star modules are ‘invisibly’ interconnected, there are no screw fittings in the hygiene area and joints are sealed without gaps.
The new filler features the word “ECO” in its title because it uses KHS’ unique ECO system, a special evacuation and CO2 purging process for glass bottles. In it the bottles are purged with a much reduced quantity of inert gas coupled with simultaneous vacuum support. Compared to conventional methods this uses up to 50% less CO2. By optimizing the vacuum pump KHS has also cut energy consumption by 20% over the previous machine variant.
Fast format changeovers
With the help of the serial QUICKLOCK quick-action locking system from KHS bottle guide parts on the Innofill Glass DRS ECO can be exchanged with just a few manual adjustments performed without tools. This reduces changeover times on fillers and rinsers by about 30%. The lightweight hygienic design of the technology gives the format parts a secure hold and is easily accessible for cleaning and disinfection. The stability of the technology also means that it’s resistant to broken glass and chemicals.
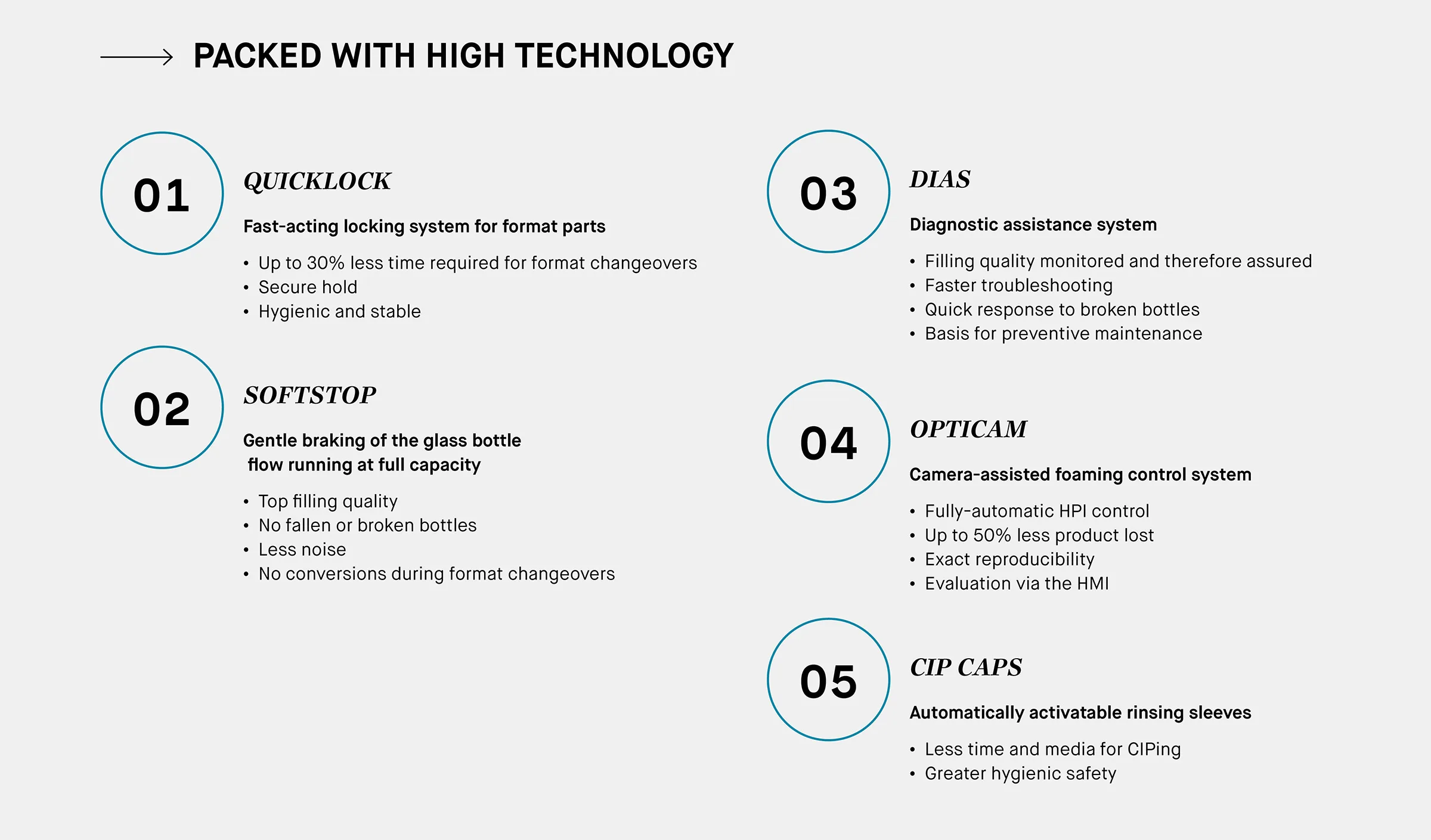
Gentle braking
Before conventional bottle flowgates are activated, the filling speed has to be throttled to prevent glass breakage. This procedure, essential on older machines, yields inconsistent filling and foaming results, thus affecting the quality of the product. On a format changeover the bottle flowgate also has to be converted. The new optional KHS SOFTSTOP product is a compact, hygienically designed bottle flowgate which can be activated running at full capacity. A light barrier measures the distances of the containers before they are fed into the filler. A brake wedge is exactly positioned between two bottles so that the filler capacity remains the same regardless of its speed. This is gentle on both containers and machine parts, reduces noise levels and gently decelerates the bottle flow without causing the bottles to fall over or break. Foaming is more constant and – depending on quality requirements – can be cut down to a minimum. This helps to avoid excessive foaming and reduces product loss. During a format changeover the operator simply sets the bottle flowgate automatically to the diameter of the new container. Conversion is not required.
Facts and Figures: INNOFILL GLASS DRS ECO
- Capacity range of 15,000 to 80,000 bottles an hour
- Bottle sizes of between 100 milliliters and 1.5 liters
- 48 to 216 filling stations
- Filling temperatures of 4°C to 20°C
- Processes beer, mixed beer beverages and carbonated soft drinks
Individual all-round control
On the filler itself KHS’ optional DIAS diagnostic assistance system monitors all aspects of the entire filling process. Pressure sensors are installed in every single filling valve which constantly record and document the internal bottle pressure, time and step sequence. The evacuation and CO2 purging processes especially are monitored to ensure the lowest possible oxygen pickup. If a broken bottle is detected at any point on the machine, the burst bottle routine is automatically initiated, complete with broken glass removal and reduced or no filling of neighboring bottles to prevent them being contaminated by splinters of glass. The data provided by the sensors can be depicted as a pressure graph on the HMI screen. Any deviations from target values immediately trigger an alarm, meaning that faults can be quickly detected, localized and directly remedied. These data are otherwise a useful general source of information: they enable the results to be statistically evaluated, based on which future sources of error can be eliminated in advance during preventive maintenance. DIAS therefore ensures consistent quality and the continuation of ongoing operation.

New features include the continuous, infinitely variable regulation of each individual filling valve and digital systems which monitor and control the filling process.
Less product loss
One particularly intelligent feature of the new filler is the optional KHS OPTICAM, a camera-assisted high-pressure injection (HPI) control system. “This process step is determinative for the quality of the finished beer as the foam generated during injection displaces the residual oxygen in the bottle,” is how Härtel describes the HPI function. “To date this had to be set by the operator and constantly monitored. Select bottles even had to be sent to the lab to confirm results. With our OPTICAM HPI is automatically regulated with the help of two cameras which observe the amount of foaming.” In the past breweries often created an excessive amount of foam during manual HPI control to make sure that oxygen pickup stayed as low as possible. Accordingly, this resulted in product being lost. “With our automatic control system product loss can be reduced by up to 50%,” smiles Härtel. “Quality settings are thus no longer a matter of how well the operator happens to be concentrating that day but can be exactly reproduced at any time.” It goes without saying that flexible adjustments can be made to the control system on the HMI; the causes of any noticeable deviations can additionally be read out here and settings corrected as required.
Automatically activatable CIP caps
Another option which helps boost efficiency and save resources are the rinsing sleeves which can be swiveled in and out for CIPing at the press of a button. Where manual changeovers of rinsing sleeves used to take up to 20 minutes, this process is now carried out automatically. The fill level probe checks the cleaning status of each individual filling valve by detecting the change in media between caustic, acid, disinfectant or water in the rinsing sleeve or CIP cap based on the conductivity. There’s no longer a risk of operators making a mistake during manual changeovers on sterile or hygienic machines; this procedure is now fully automatic – which also has a positive impact on the hygienic safety.