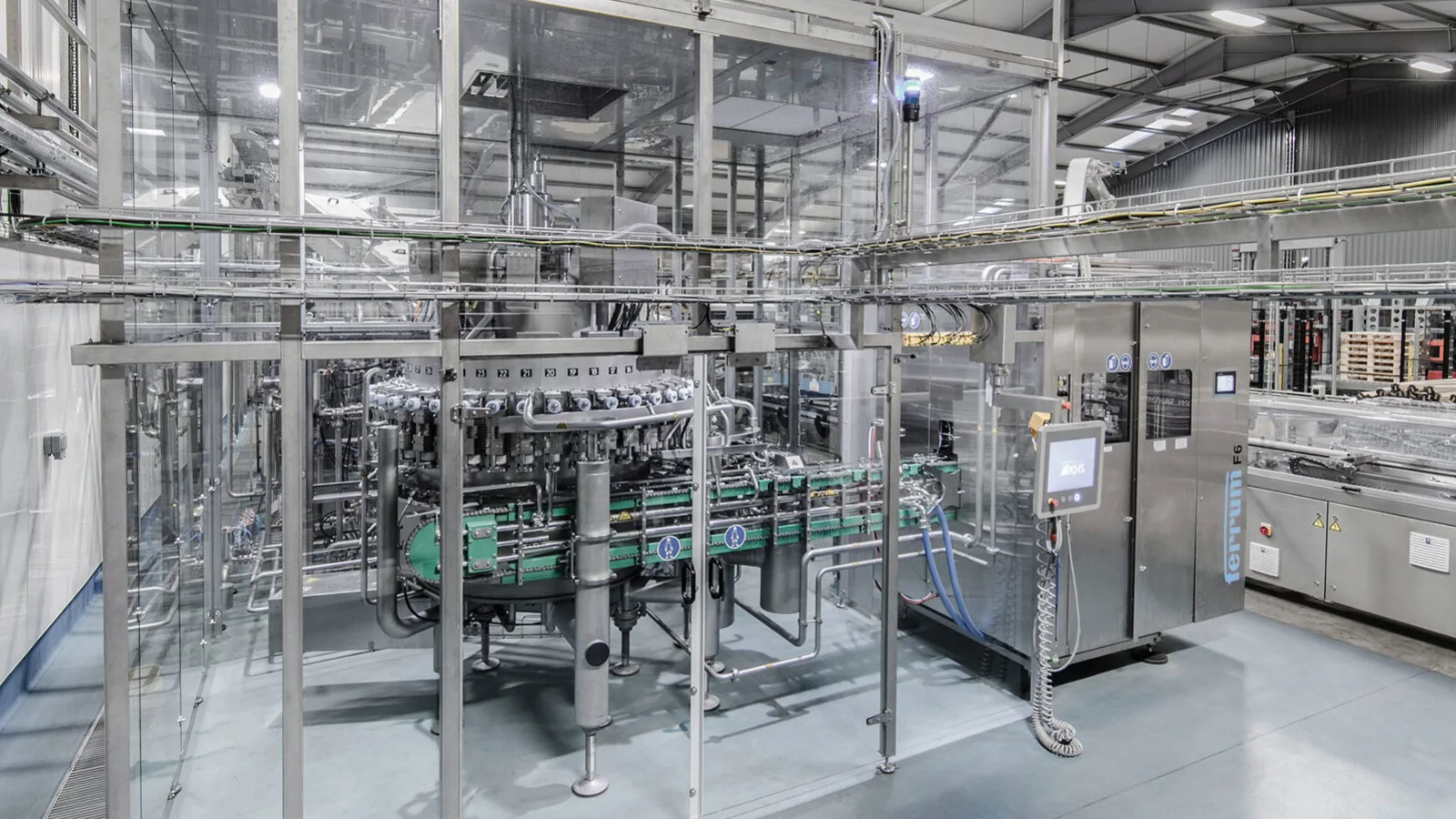
Alles dicht
Beim Dosenverschließen setzt der Schweizer Maschinenbauer und Marktführer Ferrum Maßstäbe in Bezug auf Qualität, Flexibilität und Effizienz. Da ist eine enge Partnerschaft mit KHS als Experte für die Dosenabfüllung fast selbstverständlich.
Angesichts der Diskussion über die Reduzierung von Plastikmüll sind Getränkedosen weltweit auf dem Vormarsch. Um den wachsenden Anforderungen an Wirtschaftlichkeit sowie Umwelt- und Verbraucherfreundlichkeit bestmöglich zu entsprechen, wird auch dieser Behälter gleich auf mehreren Ebenen laufend optimiert. So ist beim Material längst Aluminium an die Stelle von Stahl getreten, die Wanddicke wird immer geringer, um Ressourcen einzusparen, und eine Vielfalt an Dosengrößen und Formaten erfordert hohe Präzision und Flexibilität der verarbeitenden Maschinen. Das betrifft die Stabilität der immer fragileren Trinkgefäße ebenso wie die Umstellung von Produkten und Formaten während der Produktion, die möglichst effizient und ohne Zeitverlust erfolgen soll.
Bewährter Partner
Diese Entwicklung gilt nicht nur für die beiden KHS-Füllerbaureihen Innofill Can DVD und Innofill Can C, die heute als technologische Benchmarks in der Branche gelten. Den dynamischen Marktanforderungen müssen sich selbst die Verschließer anpassen, mit denen die Deckel auf die Behälter aufgebracht und damit fest verbunden werden. Als kompetenter Partner für diese Maschinen, ohne die keine Dosenlinie komplett ist, hat sich Ferrum im Markt bewährt – und das bereits seit vielen Jahren. Schließlich blickt das Schweizer Unternehmen wie KHS auf eine lange Tradition zurück: Schon vor über 100 Jahren stellte man den ersten mechanischen Verschließer vor. Zwischenzeitlich beläuft sich die installierte Basis weltweit auf insgesamt 2.700 Stück. Bei allen großen und namhaften Getränkeherstellern stehen die Anlagen des eidgenössischen Maschinenbauers.
Welche Auswirkungen aber haben die aktuellen Veränderungen für Verschließer? „Die Lightweight-Dosen stellen wirklich große Herausforderungen an die Technik“, sagt Marc Zubler, Leiter Verkauf und Produktmanagement bei Ferrum Packaging. „Je dünner und damit labiler sie werden, desto wahrscheinlicher ist es, dass die Behälter bei der Verarbeitung Schaden nehmen. Da reicht schon die kleinste Störkante an einer Dosenführung, die ein Bediener vielleicht übersieht. Stellen Sie sich die Dynamik unserer im Vergleich zum Füller selbst eher kompakten Anlagen vor: Mit ihrem kleinen Teilkreis entwickeln sie angesichts der hohen Geschwindigkeit enorme Fliehkräfte, da muss die Einstellung der Maschine auf den Zehntelmillimeter genau erfolgen.“ Obwohl sich das Gewicht einer Aluminiumdose in den letzten 35 Jahren von 23 Gramm um über 60 Prozent auf heute 9 Gramm reduziert habe, sei damit das Ende der Fahnenstange noch nicht erreicht, meint Zubler. Er ist davon überzeugt, dass die Industrie weiterhin versuchen werde Material einzusparen, bis die Zahl der Störungen im Fertigungsprozess zu hoch werde.
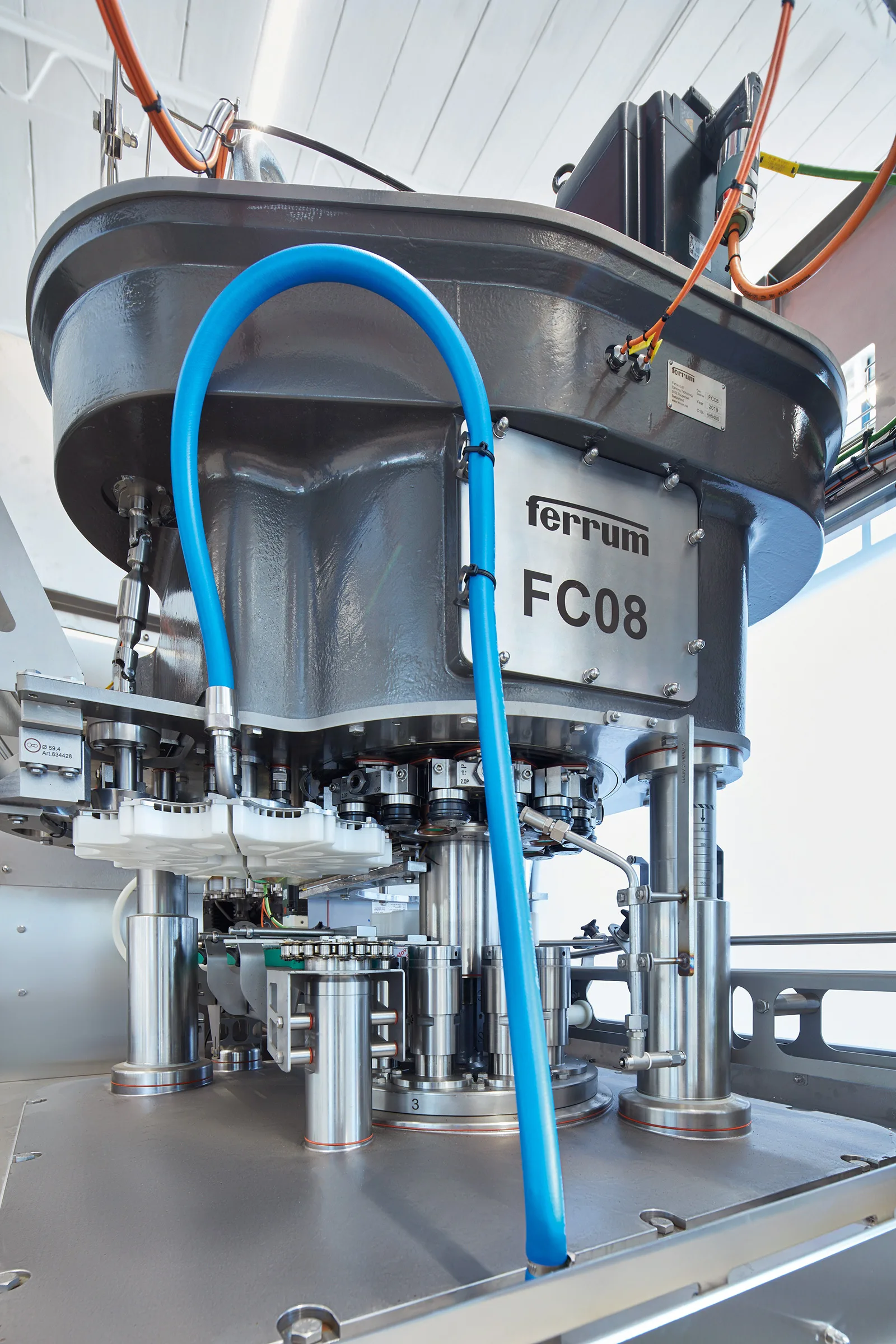
Der Ferrum-Verschließer FC08 verfügt über 8 Falzstationen – mit 19.800 bis 60.000 Dosen pro Stunde rangiert er im mittleren Leistungsbereich.
Geschmacksneutrale Verarbeitung
Mit wachsenden Anforderungen ist der Füller-Verschließer-Block auch in puncto Hygiene konfrontiert. In Anbetracht der zunehmenden Variantenvielfalt bei Getränken wird zum Beispiel der Schutz vor Geschmacksübertragung immer wichtiger. Neben der genauen Abstimmung der Produktfolge im Produktionsplan, der viel Know-how erfordert, gibt es technische Maßnahmen, die das Risiko einer Vermischung unterschiedlicher Geschmacksrichtungen – beispielsweise beim Wechsel von Energydrinks auf Near-Water-Getränke – minimieren. Dichtungen sind deshalb aus FKM beziehungsweise FFKM, sogenannte Elastomere, die beständig gegen Inhaltsstoffe der abgefüllten Produkte sind sowie nahezu keine Aromen aufnehmen und abgeben. „Bei unseren Dosenfüllern stehen die geschmacksneutrale Abfüllung und Verarbeitung an erster Stelle. Dafür weisen unsere Füllventile anstelle konventioneller Schiebedichtungen eine Tulpenführung mit Faltenbälgen aus PTFE (Teflon) auf – mit demselben Effekt“, erklärt Timo Jakob, Konstruktionsleiter Fülltechnik bei KHS. Doch nicht nur der Geschmacksübertragung haben die Dichtungen etwas entgegenzusetzen: „Außerdem verdoppeln sie die Lebensdauer der Füllventile und sind leichter zu reinigen“, betont Jakob. „Dasselbe gilt für die gesamte Maschine, deren Reinigungsintervalle sich um 20 Prozent verkürzen und deren Wartungszyklen erheblich verlängert werden. Dazu tragen vor allem der besonders hygienische Aufbau des Füllers sowie der Verzicht auf eine Wasserschmierung im Bereich des Füllerkarussells bei, der zugleich eine Verunreinigung der offenen Dosen wirkungsvoll verhindert.“
Tempo und einfache Handhabung von Formatwechseln sind essenzielle Bestandteile der Flexibilität – nicht nur beim Füller, sondern auch beim Verschließer: „Unsere Maschinen lassen sich dank integriertem Werkzeug-Schnellwechselsystem mit wenigen Handgriffen einfach verstellen“, betont Zubler. „Optional kann die Falzkurve als manuelle ausrück- und schnellverstellbare Variante bis hin zur vollautomischen Falzkurve mit einfacher Bedienung über das HMI ausgeführt werden. Das bietet wiederum höchste Flexibilität und Effizienz, sofern unterschiedliche Materialen wie Aluminium oder Stahl verwendet werden. Dank einer zusätzlichen farblichen Markierung je Format wird der Wechsel für den Bediener noch einfacher und sicherer.“ Während eine Anpassung der Dosenhöhe ganz einfach sei und eine Umstellung des Durchmessers weder Maschine noch Bediener vor besondere Herausforderungen stelle, wäre ein Wechsel der Deckelgröße aufwendiger, sagt Zubler. Aus diesem Grund gehe man zunehmend dazu über, die Sleek-Cans – trotz ihres um 5 Millimeter größeren Durchmessers – anstelle des bisher üblichen 202-Deckels mit dem etwas kleineren 200-Deckel der Slim-Dose zu verschließen.
»Gemeinsam mit Ferrum genießen wir großes Vertrauen bei unseren Kunden in der Getränkeindustrie.«
![]()
Konstruktionsleiter Fülltechnik, KHS
Nur vermeintlich einfach
Das grundsätzliche Prinzip des Verschließens besteht darin, dass der Aluminiumdeckel aufgelegt und dessen Rand zusammen mit dem gebördelten Dosenrand durch Falzkopf und Falzrolle des Verschließers umgelegt und zusammengepresst wird. Dabei entsteht eine Verbindung aus fünf sich formschlüssig umfassenden Metallschichten. Weil dieser einfach wirkende Prozess komplexes Know-how erfordert, unterhält Ferrum ein eigenes Falzlabor, das den Anforderungen des Marktes entsprechend optimale Lösungen entwickelt.
Unmittelbar vor dem Verschließen erfolgt die Unterdeckelbegasung, die den Sauerstoffgehalt im Kopfraum auf ein Minimum reduziert, um eine möglichst lange Haltbarkeit des Produkts zu erzielen. Bei stillen Getränken nutzt man wenige Milliliter flüssigen Stickstoffs, der mit seiner Temperatur von -178 Grad Celsius zunächst eine kleine Eislinse auf der Oberfläche der Flüssigkeit bildet. Innerhalb weniger Sekunden schmilzt diese und wird zu Gas, das den nun dichten Behälter so stabilisiert, dass er sich nicht mehr zusammendrücken lässt. Bei karbonisierten Getränken hingegen wird dafür CO2 eingesetzt. „Die von vielen großen Getränkeherstellern geforderte Reduzierung des CO2-Verbrauchs ist bei uns ein großes Thema“, betont Zubler. Deshalb biete Ferrum als bisher einziger Anbieter im Markt bei seinen Verschließern der jüngeren Generation die Möglichkeit, den Gasverbrauch bei verschiedenen Leistungen je Dosenformat einzustellen und damit entsprechend zu senken.
„Optional kann unsere Maschine mit einer CO2-Absaugung ausgestattet werden, die das CO2-Luftgemisch aus dem Verschließer und dem Arbeitsbereich des Bedieners abführt“, sagt Zubler. In der neuesten Verschließergeneration erfolge dieser Schritt statt wie bisher von oben nun von unten. Dabei handele es sich insofern um eine Optimierung, da CO2 schwerer als Luft sei. „Mit Hilfe der Absaugung wird die CO2-Konzentration im Produktraum des Verschließers deutlich gesenkt“, erklärt Zubler. „Indem sich die Luftqualität in der Umgebung nachweislich verbessert, sorgt diese Maßnahme für mehr Arbeitssicherheit.“ Das abgesaugte CO2 wird über ein Rohrleitungssystem sicher nach außen geführt.
»Die Unterstützung durch das globale Servicenetz von KHS macht unsere Partnerschaft rundum zu einer Win-win-Geschichte.«
![]()
Leiter Verkauf und Produktmanagement, Ferrum Packaging
Hohe Leistung
Während bei einem Großteil des Wettbewerbs maximal 100.000 Dosen pro Stunde möglich sind, bietet Ferrum Maschinen an, die bis zu 2.500 Dosen pro Minute – beziehungsweise bis zu 150.000 pro Stunde – verarbeiten können. Dank ihrer stabilen Leistung punkten die Verschließer mit hoher Verfügbarkeit sowie optimalem Wirkungsgrad und schaffen dadurch großes Vertrauen bei den Partnern in der Getränkeindustrie. „Das ist einer der Gründe, warum die langjährige erfolgreiche Zusammenarbeit für uns beide einen so hohen Stellenwert ausmacht“, unterstreicht Jakob. „Schließlich genießt KHS den Ruf als Experte für Dosenfüller in allen Leistungsbereichen.“ Die enge Kooperation soll auch in Zukunft fortgesetzt und intensiviert werden. Ziel ist die Entwicklung noch effizienterer Anlagensysteme, darunter ein Füller-Verschließer-Block aus einer Hand.
Schon heute bieten KHS und Ferrum ihren Kunden integrierte Lösungen, die den steigenden Ansprüchen an Effizienz, Nachhaltigkeit und Automation gerecht werden. Zum vereinten Erfolg trägt außerdem die Zusammenarbeit im Bereich Service und After Sales bei. Ferrum Packaging selbst unterhält mit fünf Standorten und 48 Vertretungen weltweit ein eigenes Vertriebs- und Servicenetz und ist stolz auf seine „unschlagbare Reaktionszeit“, wie Marc Zubler es ausdrückt. Unterstützung erhalten die Schweizer durch das globale Servicenetz von KHS – das macht die Partnerschaft rundum zu einer klassischen Win-win-Geschichte. Von dieser profitieren nicht nur die unmittelbar Beteiligten, sondern letztendlich vor allem die Kunden.