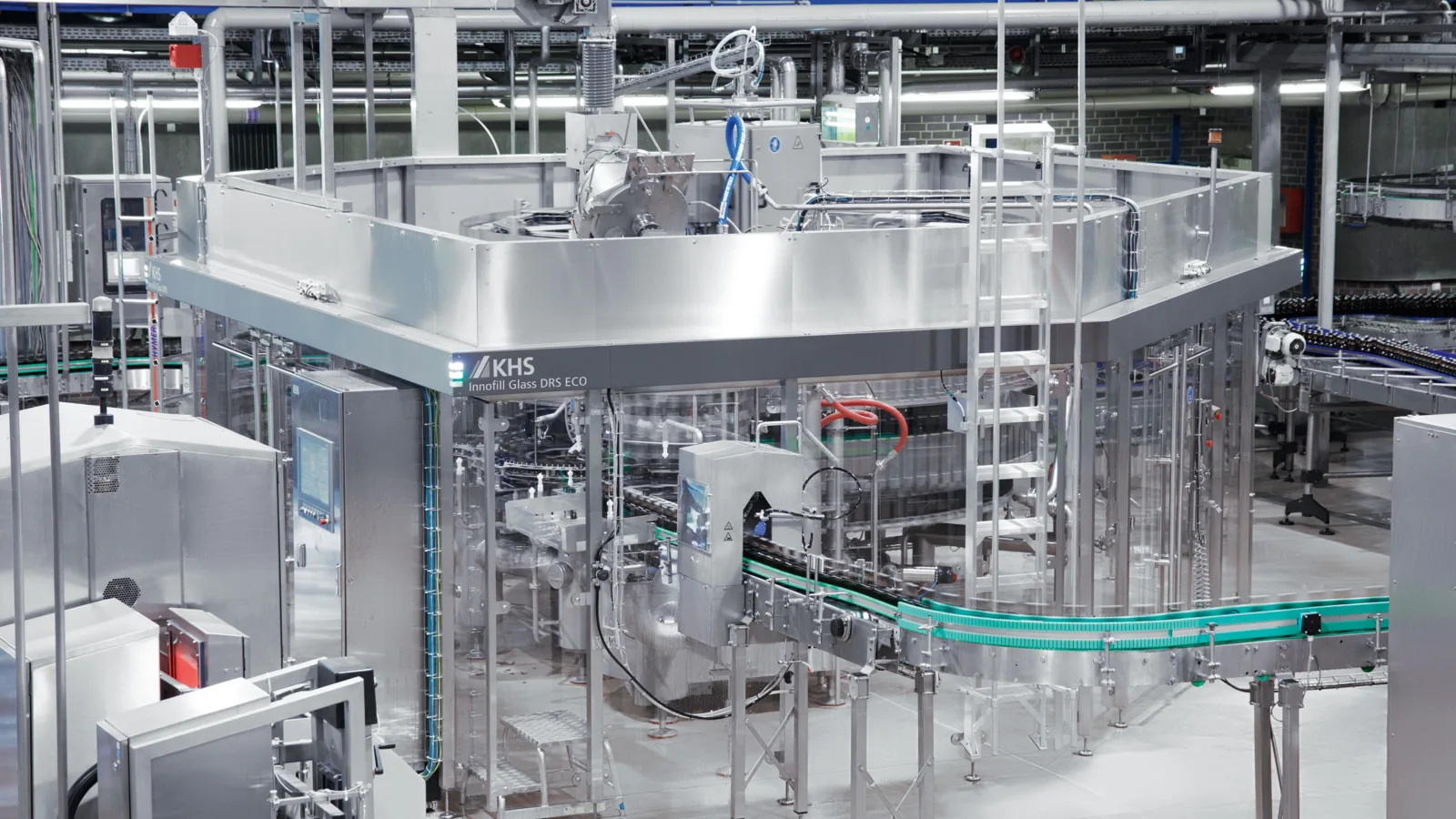
Zona de bajo oxígeno
La nueva Innofill Glass DRS ECO de KHS absorbe menos oxígeno en la cerveza, y para ello no requiere más cantidad, sino menos CO2 que su predecesora. Incluso los cerveceros experimentados están redescubriendo el sabor de sus productos.
Presentada por primera vez como prototipo en la última BrauBeviale en noviembre de 2019, la nueva llenadora modular Innofill Glass DRS ECO de KHS hace tiempo que llegó a la práctica. El primer ejemplar de este tipo se encuentra en la fábrica de cerveza OeTTINGER en Mönchengladbach desde mediados de 2021 y está causando gran entusiasmo en el gerente técnico, Jürgen Brunacker. “La nueva llenadora de KHS nos permite llenar con tan baja absorción de oxígeno que nuestro producto no se ve afectado de ninguna manera. De esta forma no existía anteriormente”.
Una de las razones de su satisfacción es sin duda el exclusivo sistema KHS-ECO, un proceso especial de evacuación y barrido de CO2 para botellas de vidrio. Durante el proceso de evacuación previa, antes de efectuar un barrido con una cantidad exactamente dosificada de CO2, se extrae el aire y, por lo tanto, el oxígeno. El proceso optimizado de KHS es muy eficaz en comparación con los métodos convencionales utilizados hasta ahora que, por ejemplo, prevén dos barridos con el gas: Permite el envasado en una atmósfera casi de un 100% de CO2, por lo que la cerveza casi ya no puede absorber oxígeno. En un segundo paso, la inyección de alta presión inmediatamente antes del taponado de las botellas, mejora aún más la situación. Esto produce una formación de espuma que desplaza la pequeña cantidad de aire del cuello de la botella y debajo de las tapas corona. Para lograr un resultado excelente, es importante que ambos pasos estén bien coordinados, explica Jonathan Lorenz, Jefe de Desarrollo de Tecnología de Llenado en KHS. “Si entra mucho oxígeno en la cerveza mientras se llena, el resultado de la formación de espuma es correspondientemente pobre”, afirma. “En general, con la máquina de llenado perfeccionada, logramos una absorción de oxígeno tan baja, que antes solo era posible con un consumo enorme de CO2”.
Presentada por primera vez como prototipo en la última BrauBeviale en noviembre de 2019, la nueva llenadora modular Innofill Glass DRS ECO de KHS hace tiempo que llegó a la práctica. El primer ejemplar de este tipo se encuentra en la fábrica de cerveza OeTTINGER en Mönchengladbach desde mediados de 2021 y está causando gran entusiasmo en el gerente técnico, Jürgen Brunacker. “La nueva llenadora de KHS nos permite llenar con tan baja absorción de oxígeno que nuestro producto no se ve afectado de ninguna manera. De esta forma no existía anteriormente”.
Una de las razones de su satisfacción es sin duda el exclusivo sistema KHS-ECO, un proceso especial de evacuación y barrido de CO2 para botellas de vidrio. Durante el proceso de evacuación previa, antes de efectuar un barrido con una cantidad exactamente dosificada de CO2, se extrae el aire y, por lo tanto, el oxígeno. El proceso optimizado de KHS es muy eficaz en comparación con los métodos convencionales utilizados hasta ahora que, por ejemplo, prevén dos barridos con el gas: Permite el envasado en una atmósfera casi de un 100% de CO2, por lo que la cerveza casi ya no puede absorber oxígeno. En un segundo paso, la inyección de alta presión inmediatamente antes del taponado de las botellas, mejora aún más la situación. Esto produce una formación de espuma que desplaza la pequeña cantidad de aire del cuello de la botella y debajo de las tapas corona. Para lograr un resultado excelente, es importante que ambos pasos estén bien coordinados, explica Jonathan Lorenz, Jefe de Desarrollo de Tecnología de Llenado en KHS. “Si entra mucho oxígeno en la cerveza mientras se llena, el resultado de la formación de espuma es correspondientemente pobre”, afirma. “En general, con la máquina de llenado perfeccionada, logramos una absorción de oxígeno tan baja, que antes solo era posible con un consumo enorme de CO2”.
»Hasta ahora, una absorción de oxígeno tan baja solo era posible con un consumo gigantesco de CO₂«.
![]()
Gerente de desarrollo de técnicas de envasado, KHS
Más informaciones sobre nuestra eficiente llenadora de botellas de vidrio Innofill Glass DRS y sus opciones apropiadas, se pueden encontrar en khs.com
Enemigo de la cerveza
El oxígeno conduce a la oxidación de la cerveza y, por lo tanto, se considera su enemigo natural y de todos los cerveceros: Por un lado, el gas limita la vida útil de la bebida y, por otro lado, afecta el sabor. Qué tan alto puede estar presente en la botella depende de varios factores: Por un lado, el lugar donde se transporta la cerveza y el período de tiempo en que se consume juega un papel; por otro lado, está la cuestión de los requisitos de calidad y sabor. Los productos destinados a la exportación, por ejemplo, tienen requisitos de vida útil más altos que los que se consumen en muy poco tiempo en un gran festival popular.
“Cuanto menos oxígeno se quiere en la botella, más CO2 se debe usar”, enfatiza Lorenz. “En ciertos mercados esto llega tan lejos que se utilizan 1.600 gramos de CO2 por hectolitro de cerveza para lograr una absorción de oxígeno de 40 ppb*, un lujo caro. A modo de comparación: en Alemania, los valores entre 80 y 200 ppb se consideran normales”.
* ppb = partes por billón. Por ejemplo, 1 ppb corresponde a 1 µg por 1 kg.
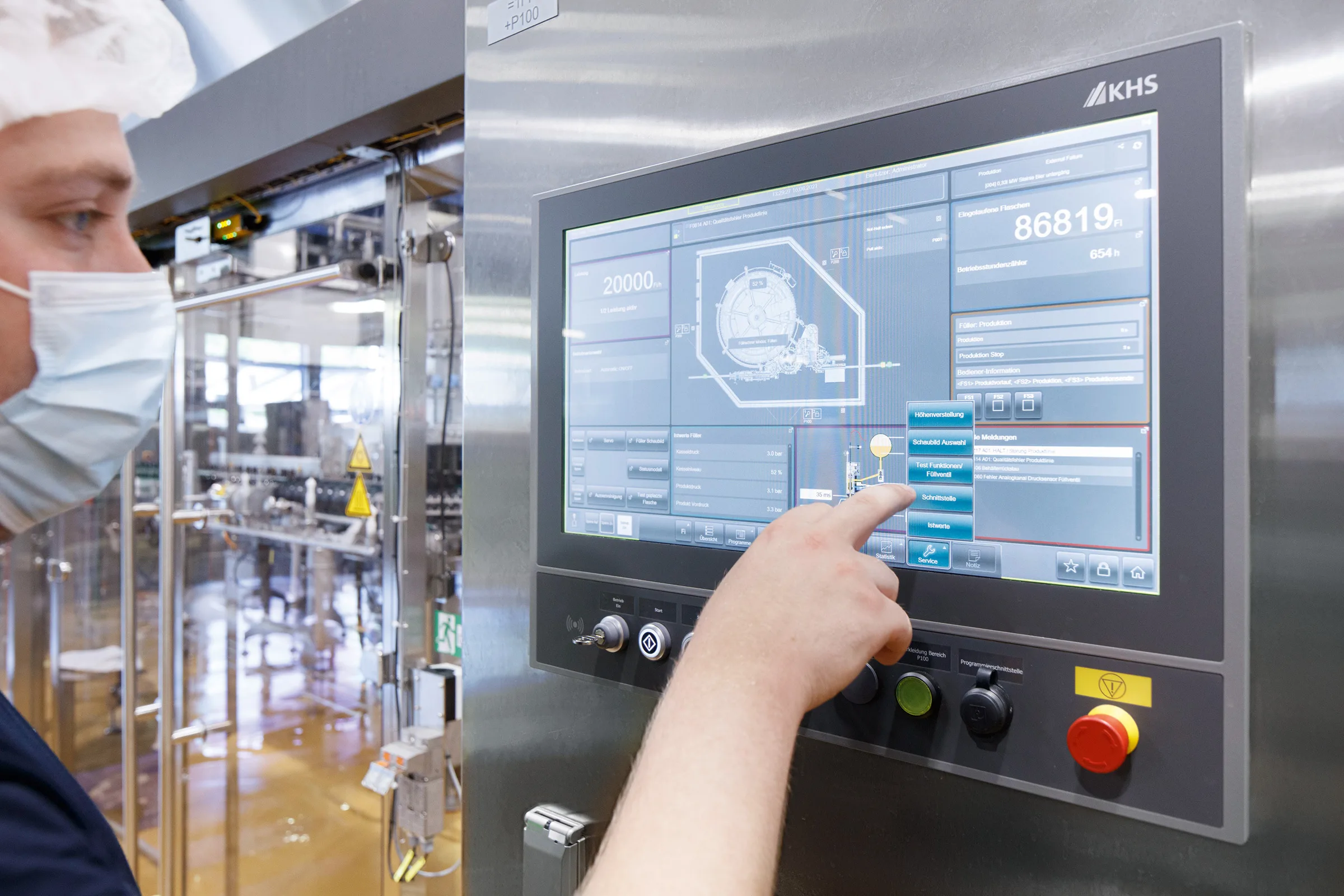
La cantidad de CO₂ utilizada se puede utilizar para controlar el bajo contenido de oxígeno de la cerveza.
Niveles de O2 sensacionalmente bajos
Brunacker confirma que el CO2 es un producto caro: “Cuanto menor es su consumo por botella llena, más eficaz es el proceso de elaboración. Una menor absorción de oxígeno significa una mayor calidad del producto, pero requiere más CO2 y, por lo tanto, mayores costes. Con la nueva llenadora de KHS, estos dos polos están en perfecta armonía”. Y el maestro cervecero sabe de lo que está hablando gracias a su padre, que también es maestro cervecero y ha trabajado durante décadas en la sede de Oettingen, Baviera, que era su segundo hogar. Para un contenido de oxígeno muy bajo de 40 ppb, por ejemplo, Innofill Glass DRS ECO solo necesita 110 gramos por hectolitro, y con 160 gramos el contenido de O2 alcanza un valor sensacionalmente bajo, de 20 ppb. “Alcanzar estos valores es un verdadero salto cuántico”, dice Jonathan Lorenz.
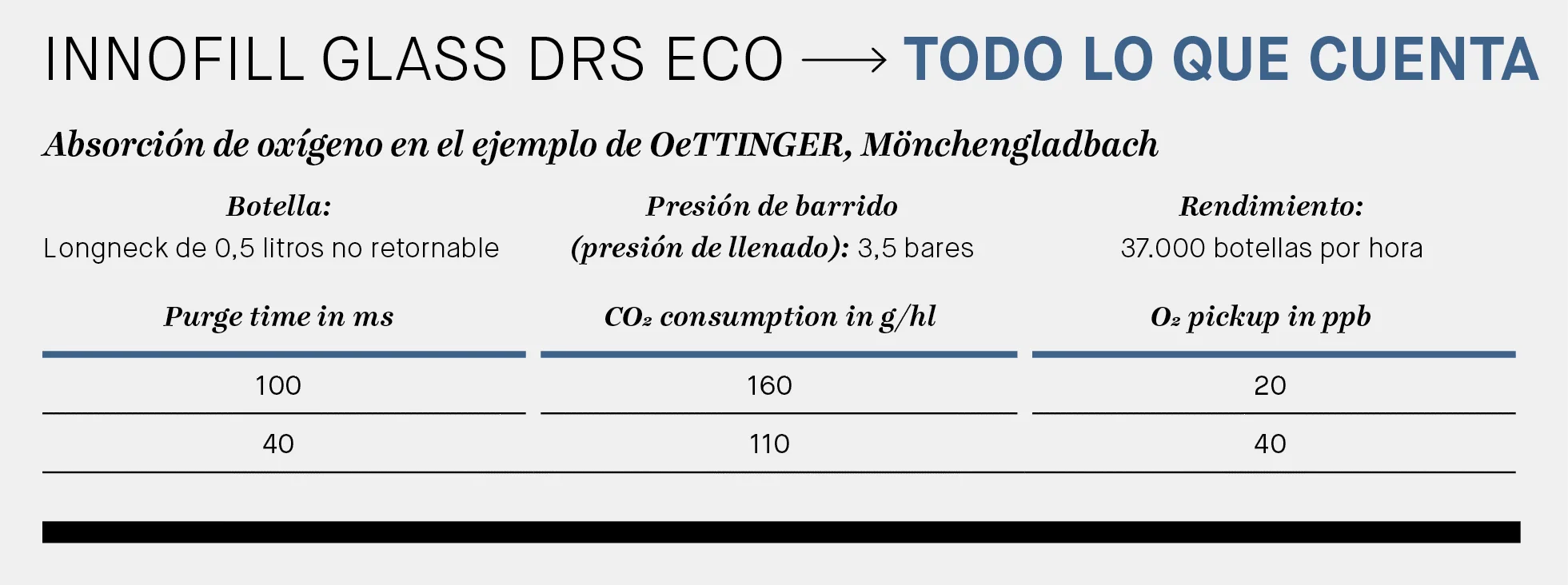
Sin embargo, la absorción extremadamente baja de oxígeno y el ahorro de hasta un 60% de CO2 no son las únicas razones por las que Brunacker y sus colegas están contentos con la nueva llenadora. Innofill Glass DRS ECO tiene otras características que lo diferencian de la competencia. Uno de ellos es el sistema de diagnóstico de asistencia (DIAS) opcional, que garantiza una supervisión completa de todos los elementos de llenado. Esto aporta seguridad y calidad adicionales para el proceso de llenado y permite una resolución de problemas más rápida, así como una respuesta inmediata en caso de roturas de vidrio. Esto está respaldado por una protección única contra la proyección de fragmentos, que garantiza un sellado óptimo contra las astillas de vidrio. “Sin embargo, no solo nos beneficiamos del llenado, sino también de la limpieza de DIAS”, enfatiza Brunacker. “El sistema es extremadamente confiable”. Además del monitoreo continuo de los medios durante el proceso de limpieza, le resulta muy útil conocer los datos operativos y los valores de consumo. “De esta manera veo inmediatamente si existe algún problema. Puedo configurar la máquina para que siempre ofrezca el mismo rendimiento con un consumo constante de medios, o puedo configurar umbrales de alarma. Estas son enormes ventajas respecto a una llenadora mecánica”.
Una opción por la que también ha optado OeTTINGER es OPTICAM, el control de espumado asistido por cámaras. Registra incluso las fluctuaciones más pequeñas en el proceso y permite que la inyección a alta presión se ajuste de forma totalmente automática, sin que la calidad del llenado dependa de la atención del operador. Para un espumado uniforme y, sobre todo, un nivel de llenado lo más exacto posible, se emplea el ajuste de altura automático y continuo provisto por los sensores de niveles de llenado. Regulando la presión de inyección, por ejemplo, se puede determinar que la pérdida de producto, que hasta ese momento era de dos mililitros por botella, sea de solo un mililitro. Esto no solo reduce la pérdida de cerveza, como afirma Brunacker: “Después del llenado, la botella debe ser enjuagada con agua. Cuanto menos espuma tenga, tanto más fácil es eliminar los restos de producto”.
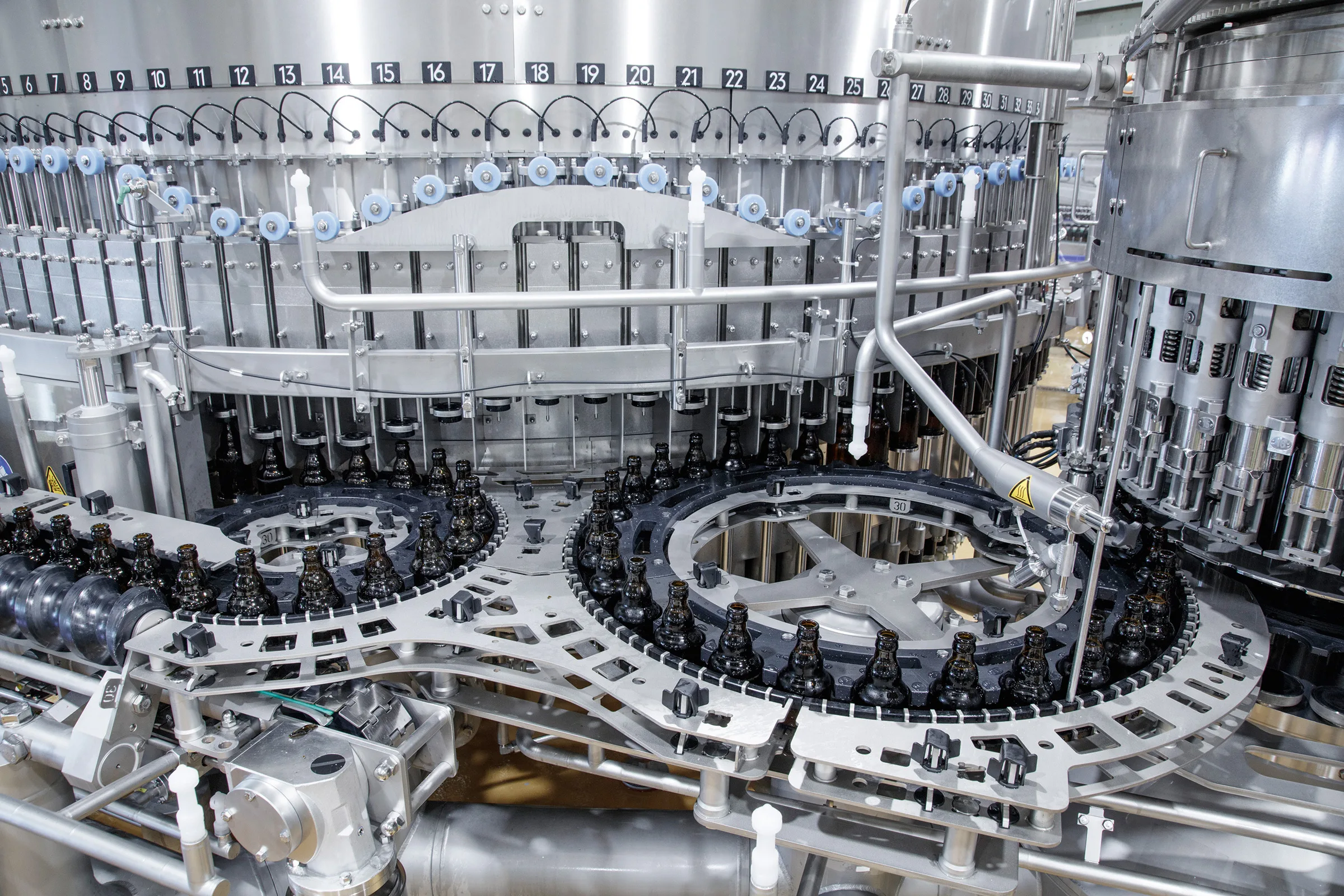
La nueva llenadora de botellas de vidrio KHS tiene una serie de características que la destacan de las soluciones conocidas anteriormente, desde sistemas de diagnóstico innovadores hasta tapas de CIP automáticas.
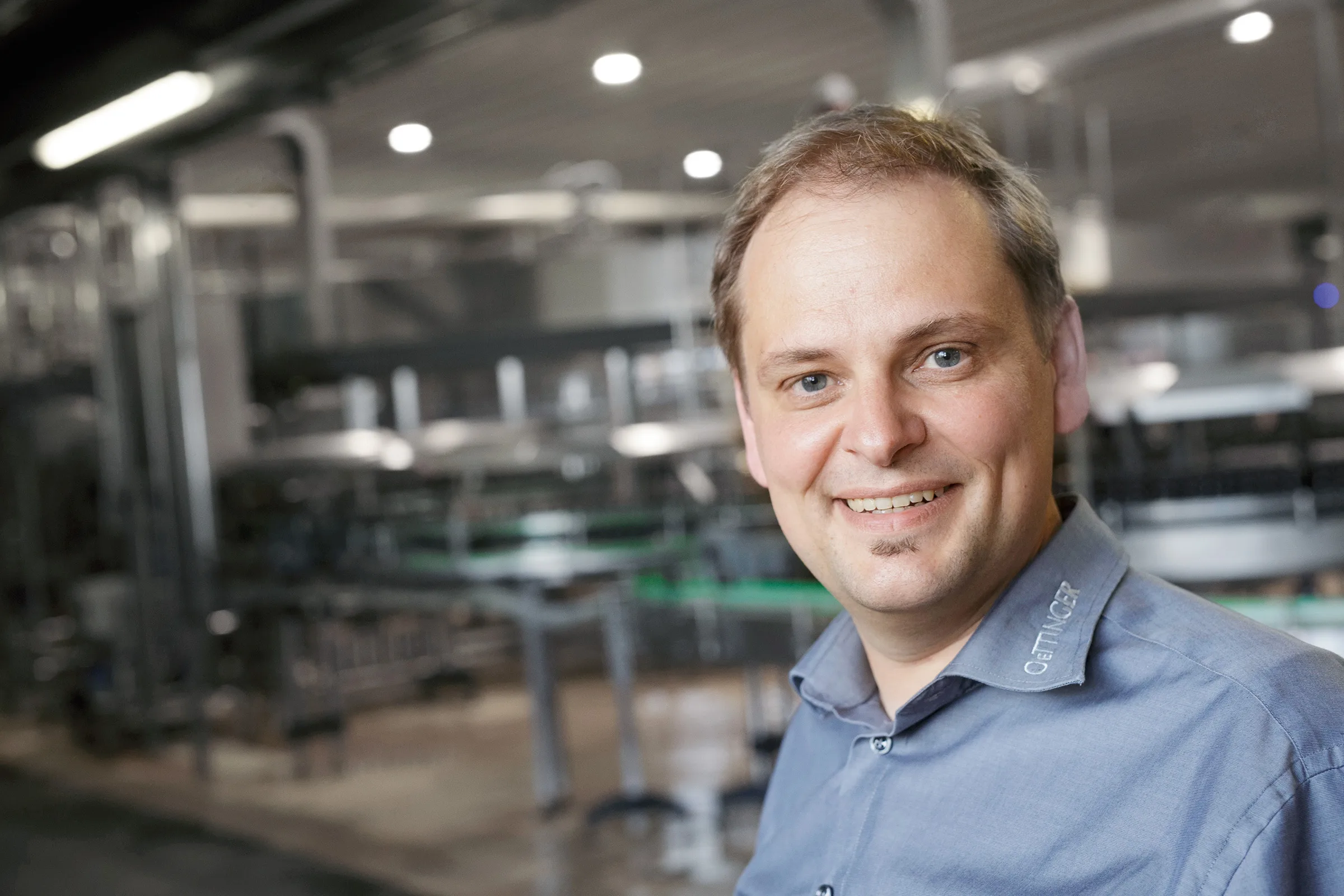
Jürgen Brunacker, gerente técnico de OeTTINGER en Mönchengladbach, está realmente entusiasmado con el bajo contenido de oxígeno y el correspondiente buen sabor de su cerveza.
Rápido e higiénico
Por último, a Brunacker le resultan prácticas los manguitos de limpieza de activación automática. “No tener que colocar las tapas de limpieza a mano es un gran ahorro de tiempo para nosotros. Y a diferencia de las soluciones conocidas anteriormente, en las que las tapas del CIP están ocultas detrás del elemento de llenado, pero que realmente entran en contacto con el producto, KHS las ha colocado detrás del revestimiento del carrusel. Esto significa que no tienen contacto con el proceso de llenado y están más protegidas. Toda la construcción es extremadamente compacta”, resume satisfecho.
Sin embargo, no solo el gerente técnico está satisfecho: Sus colegas de Mönchengladbach se familiarizaron con la nueva tecnología en muy poco tiempo, comenta. Luego de la puesta en marcha no se requiere un período de arranque (ramp-up). Desde el primer día de producción, la llenadora funcionó con un rendimiento de 40.000 botellas por hora. Incluso durante los turnos de noche, los operadores de OeTTINGER podrían haber realizado la producción sin la presencia de los montadores de KHS. Las posibilidades de la Innofill Glass DRS ECO lo asombraron, como a tantos otros.