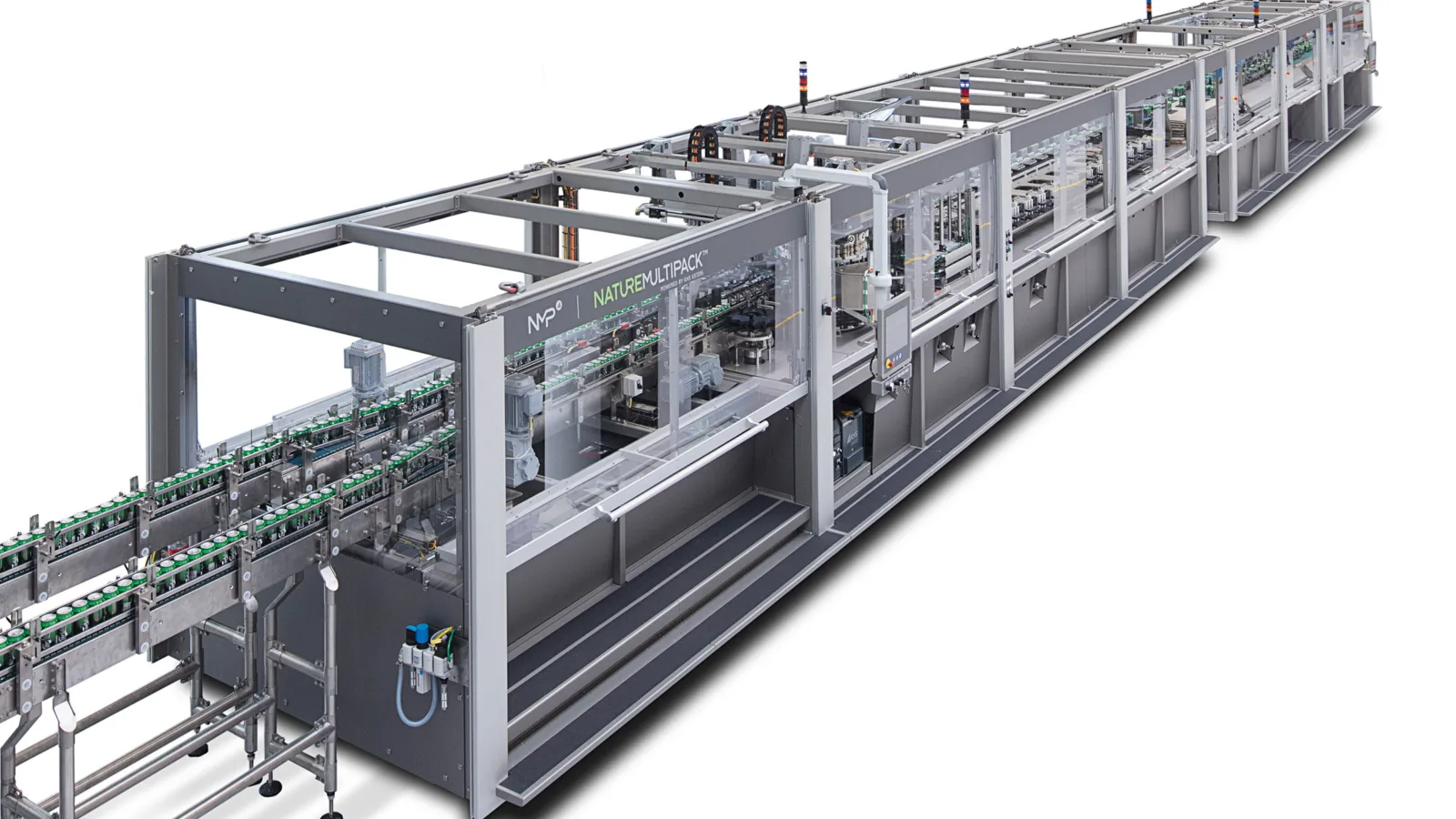
¡Tempo, Tempo!
El Nature MultiPack™ de KHS une envases de bebidas, en lugar de con film retráctil, con puntos adhesivos fácilmente removibles para formar un pack estable, y ahorra hasta un 90% de material de embalaje. Ahora esta solución, una de las innovaciones de envasado más sostenibles de los últimos años, también está disponible para el envasado de alto rendimiento.
Desarrollada originalmente por KHS para envases PET, la máquina de envasado Innopack Nature MultiPack™ se diseñó inicialmente para un rango de rendimiento de hasta 45.000 botellas por hora, más un 20% de sobrecapacidad. Sin embargo, rápidamente se hizo evidente que el concepto sostenible de unir envases de bebidas con puntos adhesivos en lugar de un film retráctil para formar un pack que sea estable para el transporte pero fácil de desmontar para el consumidor, también era de interés para el segmento de las latas. En estrecha colaboración con el Grupo Carlsberg, la solución se introdujo con éxito en varios países europeos con el nombre “Snap Pack” como un pack de cuatro, seis y ocho unidades de latas. La elección del adhesivo adecuado, en particular, planteó desafíos a KHS: Se tuvieron que realizar numerosas pruebas para determinar qué adhesivo era el más adecuado para las distintas pinturas que los fabricantes de latas aplican a sus envases.
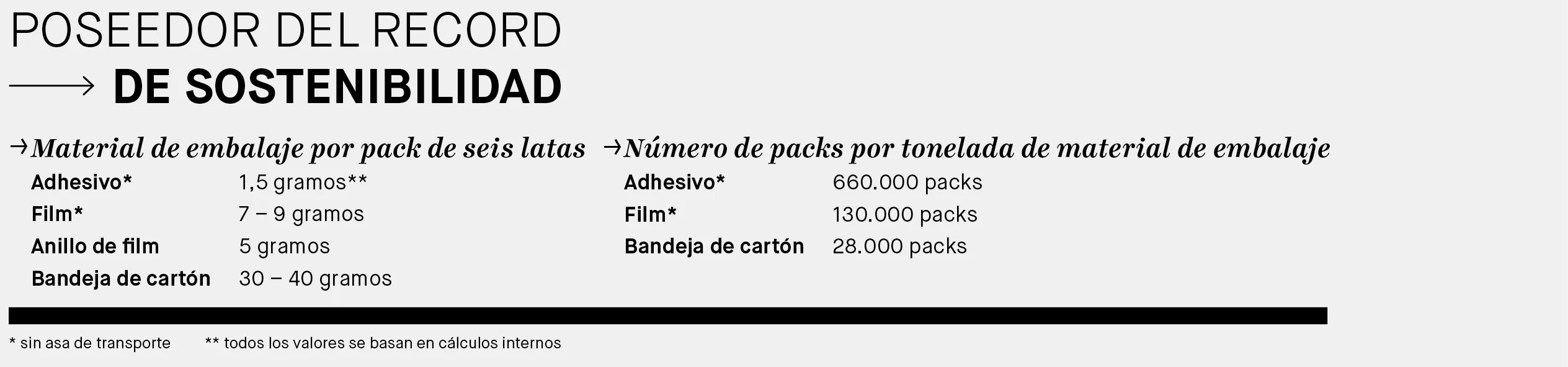
Apto para alto rendimiento
Sin embargo, surgió un desafío mayor con la velocidad de la máquina: Dado que las latas se llenan con una capacidad de más de 100.000 unidades por hora, el rango de rendimiento hasta entonces aplicable era demasiado lento. Por lo tanto, la instalación de dos máquinas en una línea era solo una solución provisional: Por un lado, debido al doble de espacio ocupado (una máquina tiene casi 25 metros de largo) y, por otro lado, debido al coste de inversión duplicado. Por lo tanto, Christoph Georg von Aichinger, Gerente Global de Cuentas de Producto NMP, enfatiza lo importante que es no solo considerar CAPEX*, sino también incluir OPEX**, es decir, los costes operativos corrientes, en el proceso de toma de decisiones. Según cálculos internos, el Nature MultiPack™ genera costes de 20 a 25 euros por 1.000 packs, en comparación con los transportadores de cartón con hasta 50 euros por cada 1.000 piezas. “Naturalmente, los mayores costes de inversión se amortizan durante un cierto período de tiempo”, explica von Aichinger. “A plena capacidad, el equipo puede amortizarse durante el primer año”.
* CAPEX = Capital Expenditure, Costes de Inversión
** OPEX = Operational Expenditure, Costes operativos
Un aspecto importante, especialmente para las ventas, es que el innovador concepto de embalaje Nature MultiPack™ aborda muchas áreas de un fabricante de bebidas: Desde la compra, siguiendo por la producción, hasta las ventas y el marketing. Para todos estos, especialmente los dos últimos mencionados, era importante transmitir las ventajas del sistema. “Las grandes empresas tienen una agenda estratégica con la que suelen perseguir tres objetivos”, explica von Aichinger: “En primer lugar está la sostenibilidad mediante el ahorro de energía y la reducción del consumo de agua, además de disminuir la huella de CO₂; en segundo lugar viene el deseo de crecimiento y, en tercer lugar, obtener el mayor margen posible. Nature MultiPack™ es una solución que sirve a los tres enfoques”. Aichinger sabe que las empresas medianas administradas por sus propietarios también se están volviendo cada vez más accesibles a innovaciones de este tipo. “Sus jerarquías planas le permiten tomar decisiones más flexibles. Recientemente vimos esto en la cervecería belga Martens, por ejemplo. En principio, después de algunas discusiones, pudimos llegar a un acuerdo”, dice feliz el vendedor de KHS (ver también el artículo “Desde 1758 la cerveza del futuro” ).
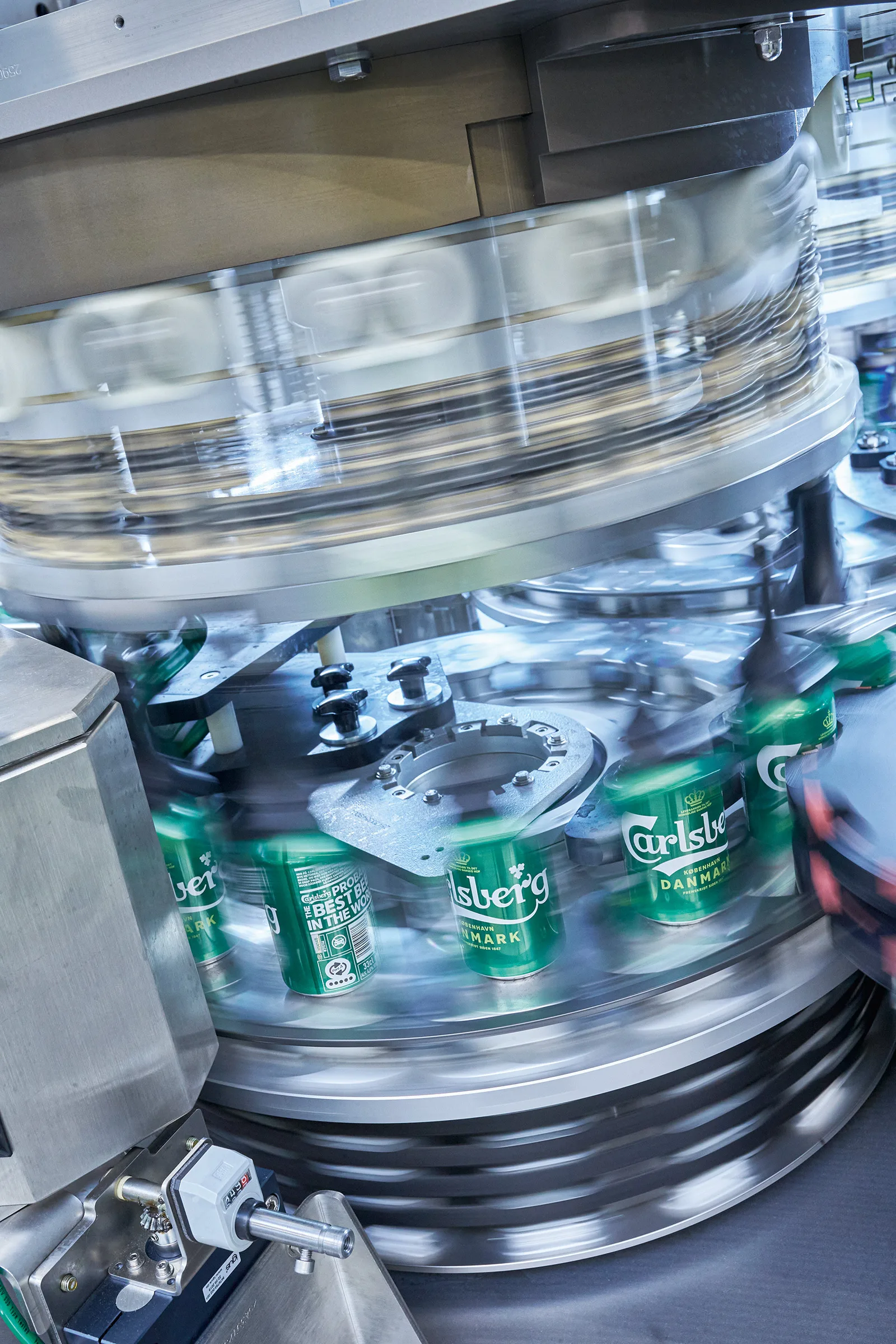
En el módulo de orientación de la máquina enfardadora, las latas de bebida se alinean en milisegundos para que los envases del pack formen una imagen continua uno al lado del otro.
Innovaciones en serie
En la comercialización de la nueva tecnología, ayuda que KHS también ofrezca un mayor desarrollo del sistema anterior: La Innopack Nature MultiPack™ para el rango de alto rendimiento. Con sobrecapacidad puede procesar hasta 108.000 envases por hora, la capacidad nominal es de hasta 90.000 envases por hora. Dependiendo del formato, el equipo puede producir hasta 450 packs de cuatro unidades por minuto. Este aumento en el rendimiento es posible gracias a una serie de innovaciones técnicas que el Dr. Matthias Caninenberg, Director de Tecnología Nature MultiPack de KHS en Kleve, explica en detalle: “Las innovaciones comienzan con la velocidad de transporte, que, en comparación con la máquina anterior, hemos aumentado de 51 a 72 metros por minuto. Para no tener que duplicar la velocidad, lo que habría supuesto un trabajo adicional considerable, se redujo el paso en el módulo de separación. Esto significa que la distancia entre los envases fue reducida de 114,3 a 90 milímetros, e incluso a 80 milímetros tras el proceso de encolado. De esta manera, por la máquina pasan más unidades y así logramos nuestro rango de rendimiento objetivo”.
»Las innovaciones empiezan con la velocidad de transporte, que hemos aumentado de 51 a 72 metros por minuto«.
![]()
Director de tecnología Nature MultiPack, KHS
Orientación en milisegundos
En el módulo de orientación se modificó el carrusel completo: En lugar de los cuatro accionamientos anteriores, ahora hay seis accionamientos que giran tres placas en lugar de las cuatro anteriores. De esta manera se ahorra tiempo para alinear los envases. Durante la primera marcha de referencia, una cámara genera 400 imágenes de un envase mientras el mismo gira 360 grados alrededor de su eje longitudinal. Durante la producción, el envase se fotografía solo una vez. Con la ayuda de un algoritmo rápido, esta exposición individual se compara con las 400 imágenes tomadas previamente y se determina la posición actual de cada lata o botella PET individual. A partir de esto se calcula la corrección necesaria de la posición del envase, que un motor controlado realiza en milisegundos hasta que el envase tenga la orientación deseada. Esto es importante, por ejemplo, con referencia al punto de venta (PoS), pues los envases del pack deben formar una imagen continua uno al lado del otro.
En el siguiente módulo, los cabezales de aplicación se utilizan para “disparar” el 50% de los puntos de adhesivo sobre las latas o botellas a la izquierda y derecha. En el momento de la aplicación, el envase se detiene durante una fracción de segundo para fijar el punto adhesivo con la mayor precisión posible. Para ello, se rediseñó el carrusel y se ajustó ligeramente la posición de los cabezales de aplicación.
Una vez aplicados los puntos adhesivos, los envases acceden al módulo de compresión. “Aquí es donde el pack se une al presionar los envases entre sí. Esto sucede en menos de un segundo, siempre que el adhesivo esté blando”, explica el Dr. Caninenberg. En el desarrollo posterior de la máquina para la gama de alto rendimiento, la mayor parte del tiempo y la energía se emplearon para esta sección con el fin de lograr una producción de hasta 90.000 o hasta 108.000 botellas o latas por hora. Para ello, se prescindió de las estrellas de transferencia con dedos y el transporte de cadenas se cambió a correas dentadas. El nuevo diseño modular permite reducir a la mitad la distancia de pegado y acortar todo el equipo completo en tres metros y medio. El esfuerzo no solo valió la pena en términos de tamaño, dice el Dr. Caninenberg: “La unión es más tranquila y flexible, y el traspaso está sujeto a tolerancias más bajas”.
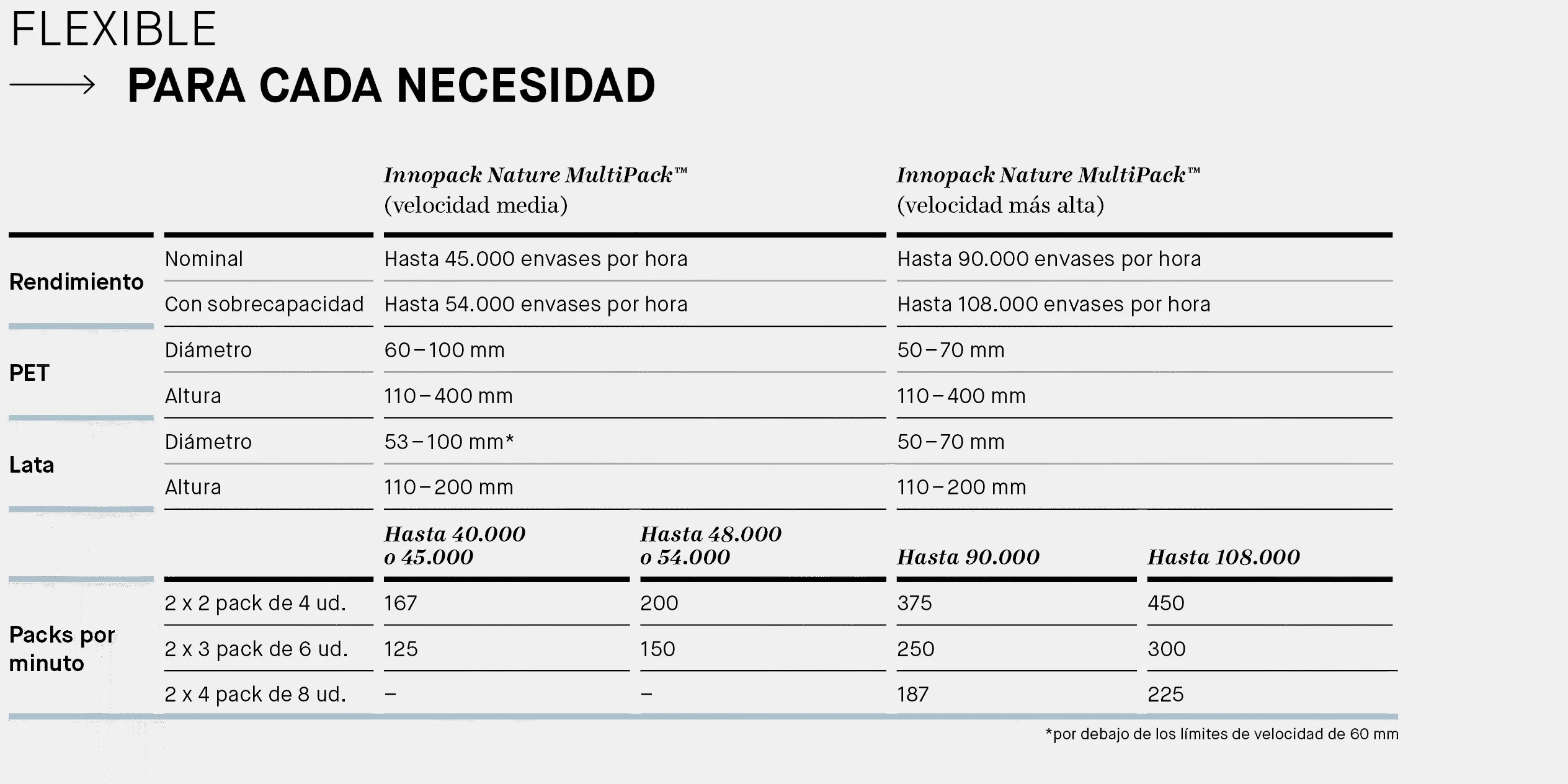
Puede encontrar más informaciones sobre nuestra máquina enfardadora Innopack Nature MultiPack™ en khs.com
Aplicador de asa propio de KHS
Después de la compresión, se efectúa el rechazo de los packs a los que no se les aplicó un punto adhesivo o se les aplicó incorrectamente. “Sin embargo, la tasa es tan baja que apenas vale la pena mencionarla”, enfatiza el Dr. Caninenberg. El secado con aire también puede contribuir a esto. Se trata de un módulo opcional que garantiza que no haya condensación en toda la máquina ni tampoco formación de condensado, un requisito previo importante para la calidad del proceso de encolado. A ello le sigue otra característica: después de que los packs se hayan dividido en tres hileras y se hayan girado 90 grados, se les aplica un asa en el módulo de aplicación de asas: “Esta es la primera vez que utilizamos un modelo desarrollado por KHS que puede manejar hasta 150 packs por minuto. En vista de los tres aplicadores instalados uno al lado del otro, la producción suma 450 packs por minuto. Con un pack de cuatro unidades de envases esto significa 108.000 envases por hora, que es el máximo que se puede procesar”. Opcionalmente, en el nuevo equipo pueden producirse también 300 packs con 6 envases cada uno, o 225 packs con ocho envases cada uno.
La flexibilidad es una prioridad absoluta, también en lo que respecta a la huella ambiental de la máquina enfardadora: “Si hay problemas con la longitud del equipo, el diseño también se puede girar en la mitad a 90 o 180 grados”, dice el Dr. Caninenberg con firmeza. Esto significa que la Innopack Nature MultiPack™ perfeccionada para el sector de alto rendimiento también se puede adaptar a condiciones espaciales complejas.