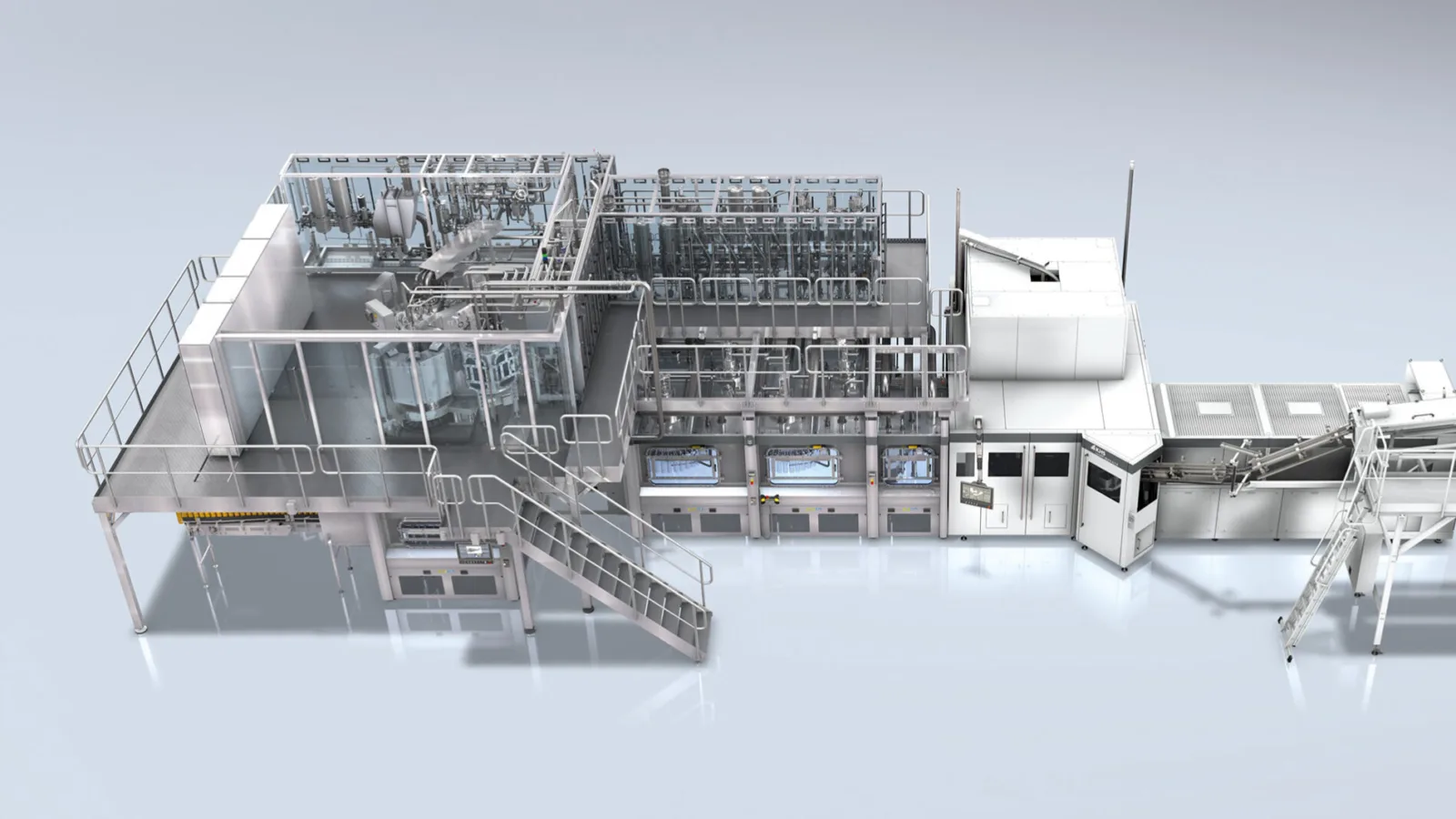
Alto rendimiento, mayor seguridad
Con su nuevo bloque aséptico para la esterilización de botellas, KHS establece estándares en materia de seguridad e higiene. Las empresas envasadoras de bebidas no tienen que renunciar al rendimiento: gracias a una llenadora rotativa, la solución en bloque comienza con un rendimiento tres veces mayor con respecto a la llenadora lineal.
Si se requiere la máxima seguridad al llenar bebidas sensibles en botellas PET, las llenadoras asépticas lineales de KHS ya han demostrado su eficacia en el mercado. Es lógico que para un mayor rendimiento, el proveedor de sistemas de Dortmund presente también una llenadora aséptica rotativa que establece nuevos estándares en términos de propiedades higiénicas. El fabricante de máquinas y equipos apuesta deliberadamente por la esterilización de botellas que, a diferencia de la esterilización de preformas, también se puede combinar con el sistema de recubrimiento PET FreshSafe de KHS, que proporciona una protección adicional al productoen el caso de bebidas sensibles. Con este proceso, los envases se esterilizan inmediatamente antes del proceso de llenado. Esto proporciona una mayor flexibilidad y mayor disponibilidad en el cambio de formato que con la esterilización de preformas, donde la esterilidad del bloque se interrumpe cuando se cambian los moldes de estirado-soplado. Además, la esterilización de botellas permite una manipulación fácil y cuidadosa de envases ligeros.
Nuevo diseño de llenadora
La nueva llenadora rotativa Innofill PET ACF-R se ha combinado con la máquina de estirado-soplado InnoPET Blomax Serie V, de bajo consumo energético. En comparación con las llenadoras lineales, que pueden procesar hasta 14.000 botellas por hora, el bloque aséptico InnoPET BloFill ACF-R resultante alcanza actualmente una producción de hasta 36.000 botellas de 1 litro por hora. En el futuro, el bloque estará disponible incluso con una capacidad de producción de hasta 48.000 botellas de 500 mililitros por hora. La nueva solución alcanza dentro del contenedor una esterilidad correspondiente a log 6, lo que corresponde a una reducción de gérmenes del 99,9999 %.
Durante el desarrollo se prestó especial atención a la llenadora aséptica, que presentó un diseño completamente nuevo. Una característica clave fue la limitación de hasta 4 estrellas más pequeñas para la introducción de peróxido de hidrógeno (H2O2) así como la activación y secado con aire estéril. Se utilizan en lugar del carrusel grande empleado anteriormente. Las ventajas de esta tecnología simplificada son valores de consumo más bajos y, debido al diseño modular y al menor requerimiento de espacio, una instalación y mantenimiento más económicos. “La zona estéril debe estar encapsulada y aislada de la nave de llenado”, explica Manfred Härtel, Jefe de Producto de Llenado de KHS. “Para carruseles grandes, se requiere una barrera líquida para crear una separación del aire del ambiente. Esto no es necesario para nuestra versión con estrellas pequeñas, lo que hace que la máquina sea mucho más fácil de configurar y operar”.
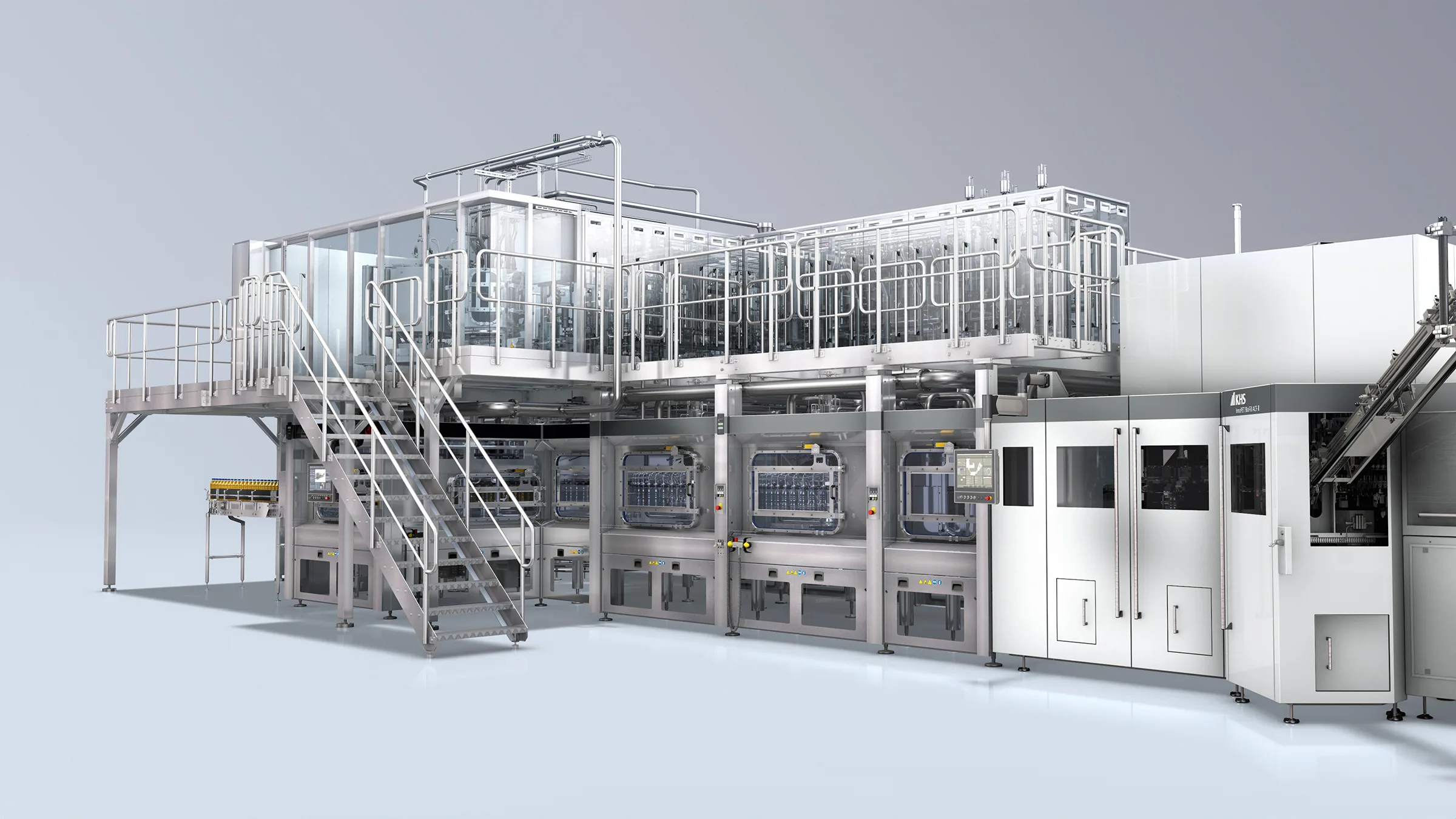
Un punto destacado del nuevo bloque rotativo es el cambio automático de formato: no se requieren intervenciones manuales del operador y no se interrumpe la esterilidad interna de la llenadora.
En khs.com encontrará más información sobre nuestro nuevo y particularmente potente bloque aséptico Innofill PET ACF-R.
Alto estándar de higiene
La InnoPET BloFill ACF-R está distribuida espacialmente en dos niveles: a nivel del suelo se encuentra una máquina de estirado-soplado, el módulo de esterilización, el carrusel de la llenadora y el servotaponador de 2 vías. Sobre una plataforma se encuentran la tecnología de proceso con el módulo de servicio, la preparación de H2O2, la producción de aire comprimido estéril, la esterilización de las tapas, así como el colector de válvulas.
Antes de llegar a la sala aséptica de la llenadora, las botellas PET pasan por una esterilización externa e interna. Aquí los productos sensibles se introducen en los envases y luego se cierran con el servotaponador. En el área higiénica se crea una sobrepresión mensurable mediante aire esterilizado de generación propia. Esto crea un flujo de aire estéril tanto en la dirección de esterilización de las botellas, como sobre el taponador, para su expulsión a través de una esclusa. Luego los envases se controlan cualitativamente para detectar fugas y el nivel de llenado antes de avanzar hacia el sector seco de la línea.
En la esterilización externa, un gran número de boquillas fijas evita la formación de una pulverización incompleta. Cuando se transfiere a la esterilización interna, la zona del cuello de las botellas también se esteriliza especialmente. “Lo especial de nuestro esterilizador es que prescindimos de las habituales estrellas entre las diferentes estrellas de procesamiento”, explica Härtel. “Para que esto funcione, se diseñó de tal manera que no se necesitan estrellas intermedias, sino que es posible un acoplamiento directo. Para evitar colisiones, también hemos equipado las lanzas para la esterilización interna con una guía controlada”. Esto se consigue mediante brazos móviles que sumergen las lanzas pulverizadoras en las botellas PET y las levantan de nuevo. “Como resultado, las innovaciones garantizan una pequeña zona aséptica y un alto estándar de higiene. Junto con el reducido número de estrellas y accionamientos, también se reduce significativamente el área total de instalación. Otra característica de calidad de nuestra esterilización de botellas es que después de 24 horas quedan menos de 0,5 ppm de H2O2 residual dentro de las botellas“, afirma satisfecho.
Solución limpia
Las barreras contra líquidos en el carrusel de llenado protegen la sala higiénica cerrada contra la influencia del entorno. Se utiliza H2O2 líquido en una concentración de aprox. un 30 %, así como agua adicional,con el fin de prevenir la liberación de peróxido de hidrógeno a la atmósfera y garantizar la seguridad en el lugar de trabajo. Además, ya no son necesarios manguito de limpieza ni tapas CIP, ya que toda la sala aséptica se limpia con la misma sosa cáustica y/o ácido para la limpieza interior y exterior. La última sirve para eliminar los residuos minerales que podrían dar lugar a la formación de depósitos críticos para la esterilidad. Gracias al proceso adaptado, el tiempo de limpieza CIP se reduce significativamente. Para minimizar el consumo, los medios son recolectados y devueltos al sistema para ser reacondicionados antes de la próxima limpieza CIP.
La llenadora aséptica modular está diseñada para adaptarse a diferentes sistemas actualizados de llenado de PET de KHS, gracias a su flexibilidad. Estos sistemas varían la velocidad según la fase de llenado respectiva y determinan el nivel de llenado mediante medición del flujo. El estándar actual son válvulas con sistema de chorro libre para las bebidas generalmente sin dióxido de carbono en el proceso aséptico. Como alternativa, se pueden utilizar sistemas que permiten el procesamiento de fibras y pulpas. En el futuro, también se envasarán de forma estéril productos con contenido de dióxido de carbono, como por ejemplo, las bebidas gaseosas de zumo de frutas.
“Como resultado, las innovaciones garantizan una pequeña zona aséptica y un alto estándar de higiene”.
![]()
Gerente de Producto de Envasado, KHS
Numerosos aspectos destacados
Al igual que el carrusel de llenado, el taponador, que también opera en atmósfera aséptica, está equipado con una doble barrera de gas para lograr el mejor aislamiento posible. Las tapas de cierre, dispuestas en filas apiladas, se transportan a la zona aséptica compacta para su esterilización. Aquí se realiza, en una especie de “sistema de revólver”, la esterilización con de H2O2 vaporizado tanto en el interior como en el exterior desde todos los ángulos, así como la activación y el secado. Posteriormente, son dirigidas hacia abajo hasta el taponador a través de un alimentador cerrado.
Como otro punto destacado del nuevo bloque rotativo, Härtel destaca el cambio automático de formato, que, si no se produce un cambio de boca, elimina la necesidad de intervenciones manuales del operador y, por lo tanto, evita la interrupción de la esterilidad interna. Esto evita la necesidad de una limpieza y esterilización completa del módulo de llenado. Con solo presionar un botón en el HMI, varios servomotores ajustan, en tan solo 3 minutos, por ejemplo, las curvas de entrada y salida de la llenadora, la guía del fondo de las botellas en el taponador y las barandas. Para mantener la esterilidad, se utilizan fuelles y barreras de vapor. Si se debe cambiar el diámetro de la boca de las botellas, esto puede realizarse opcionalmente de forma manual.
“Con nuestra nueva solución aséptica hemos logrado combinar máxima seguridad con un rendimiento excepcional”, resume Härtel, y se complace al constatar que con esto, KHS demuestra una vez más su gran competencia en tecnología de llenado en lo que respecta al envasado estéril.