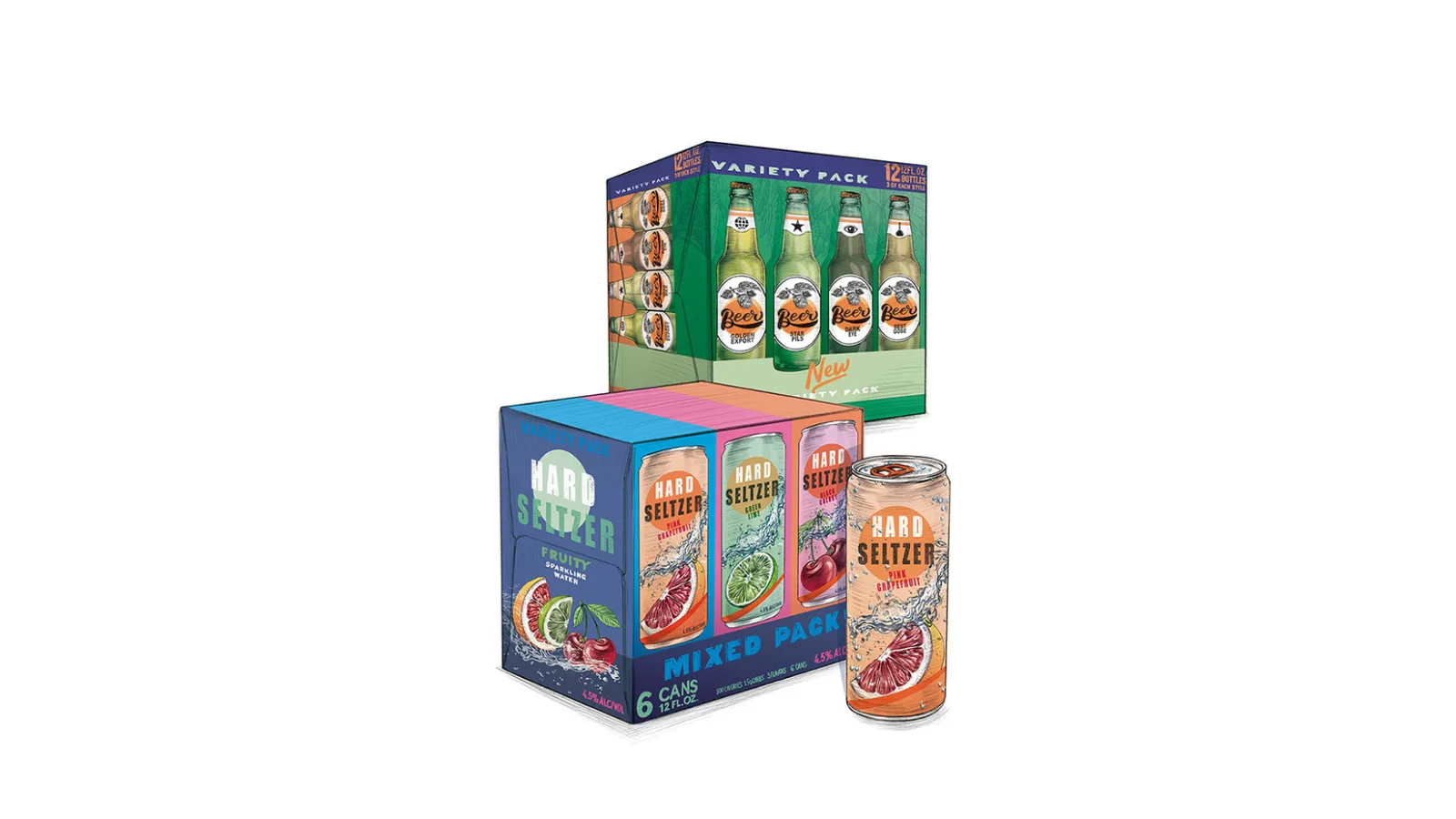
Con muchos colores
Diferentes sabores de una bebida en el mismo embalaje exterior: el Variety Pack ofrece al consumidor este valor añadido. Gracias a una nueva configuración de máquinas probadas de KHS, el embalaje cada vez más popular ahora se puede crear de una manera altamente automatizada.
Una tendencia de embalaje que originalmente vino de los EE. UU. ahora está ganando terreno en un número creciente de otros países: el llamado Variety o Rainbow Pack. Contiene bebidas de diferentes tipos, lo que permite al consumidor probar una variedad de diferentes tipos de productos en envases secundarios. Este pack se usa principalmente para bebidas de alto precio, como cervezas premium, bebidas energéticas o Hard Selzer. Los beneficios para los fabricantes de bebidas son obvios: Por ejemplo, puede presentar a sus clientes diversas variantes de productos como parte de un lanzamiento al mercado.
Existe una gran cantidad de soluciones diferentes para la producción de los packs que, sin embargo, antes estaban reservadas para el rango de bajo rendimiento debido a una proporción variable de actividades manuales, y eran asumidas por las empresas de preparación de pedidos. El proveedor de sistemas de Dortmund KHS presenta ahora una configuración del equipo que, gracias a su grado de automatización, hace posible el Variety Pack por primera vez en el rango de alto rendimiento y, por ejemplo, permite el procesamiento de hasta 120.000 latas por hora. Se trata de un sistema de embalaje que separa los envases que ya se han colocado en bandejas y palets en la propia línea de producción, y los vuelve a colocar en packs mixtos.
Para ello, las latas de bebida se alimentan al sistema de embalaje desde el almacén clasificadas por tipo en plates y bandejas.
»La línea de embalaje se puede combinar con cualquier línea existente que esté equipada con una enfardadora de bandejas«.
![]()
Referente de Ventas, KHS
¿Cómo se preparan los paquetes de variedades?
Paso 1
Dos robots despaletizan los diferentes tipos, mientras que los empujadores separan las bandejas en filas individuales.
Paso 2
Luego, dos desencajonadoras al vacío levantan las latas de la bandeja y las colocan en posiciones separadas en la cinta transportadora.
Paso 3
Desde aquí, las latas ingresan a la máquina enfardadora una al lado de la otra en una vía, con un sabor diferente en cada vía. Allí, los envases se agrupan finalmente en packs de 4, 6, 8, 12, 18 ó 24 unidades u otros envases mixtos, y se embalan en cajas de cartón cerradas.
Paso 4
Los packs Fully-Enclosed más pequeños se vuelven a colocar en las bandejas previamente vaciadas. Estas avanzaron a través de la línea paralelamente a las latas y, por lo tanto, pueden reutilizarse. No se requiere embalaje de transporte adicional para packs más grandes, ya que estos tienen la estabilidad necesaria para el paletizado y van directamente al paletizador.
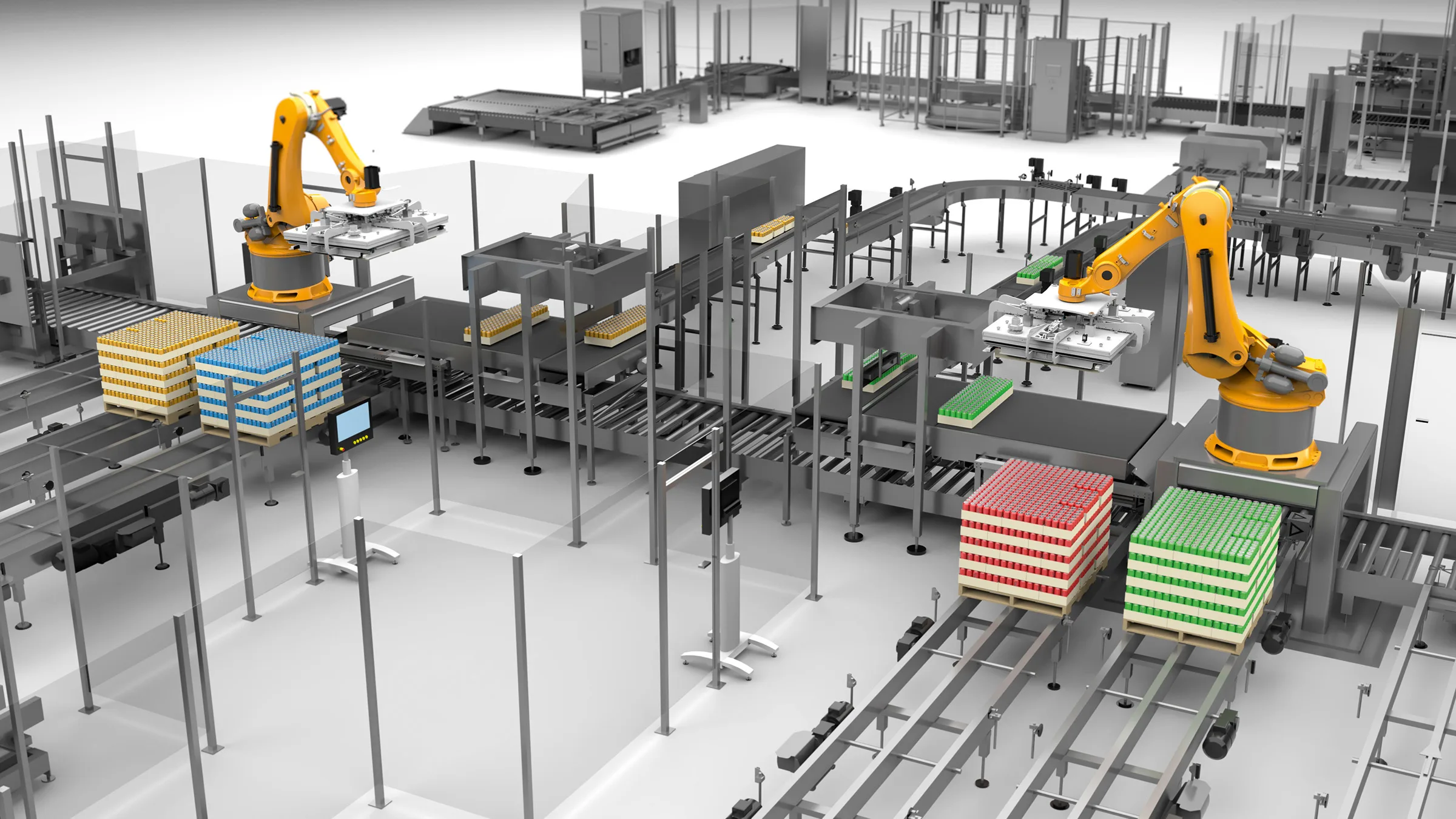
Paso 1: Dos Innopal RK despaletizan las latas y bandejas con un cabezal de sujeción por vacío desarrollado para este fin.
Nuestro video muestra paso a paso cómo se ensamblan los variety packs en el sistema de emblaje de KHS.
Hasta seis sabores
Dependiendo de la configuración del sistema de embalaje, son posibles diferentes mezclas de dos, tres, cuatro o seis sabores. “El encanto de nuestra solución es que utilizamos nuestro Innopack PPZ”, explica Nils Schneider, responsable como director de ventas de KHS por el Variety Pack. “Estas son aplicaciones que han sido probadas en la industria de envases retornables, que hemos convertido para este propósito y las hemos equipado con piezas de formato recientemente desarrolladas. El uso de tecnología conocida también ofrece la ventaja de que no se requiere capacitación especial para el operador. Y el cambio entre los embalajes de diferentes tamaños de un lote a otro no es más complejo que un cambio de formato normal”.
Según Schneider, hay tres argumentos verificables a favor de la solución fuera de línea que es independiente de la producción: “En primer lugar, se requerirían inversiones mucho más altas para procesar los tipos respectivos desde cuatro llenadoras diferentes directamente en una enfardadora Fully-Enclosed. En segundo lugar, todas las llenadoras tendrían que funcionar con la misma velocidad, eficiencia y estabilidad. Una sola falla, independientemente del motivo, provoca que toda la línea se detenga. En tercer lugar, los envases podrían colocarse sueltos sobre palets y, por lo tanto, podría prescindirse de la máquina desencajonadora del sistema de embalaje. En este caso, habría que instalar un paletizador adicional para envases sueltos en la línea existente. Las latas de bebidas restantes no se podrían vender sin un procesamiento adicional si, por ejemplo, hubiera un excedente de uno o más tipos como resultado de cualquier interrupción”.En resumen, según Schneider, lo que habla a favor del sistema desarrollado por KHS es que el sistema de embalaje se puede combinar con cualquier línea existente, la mayoría de las cuales ya están equipadas con enfardadoras de bandejas.
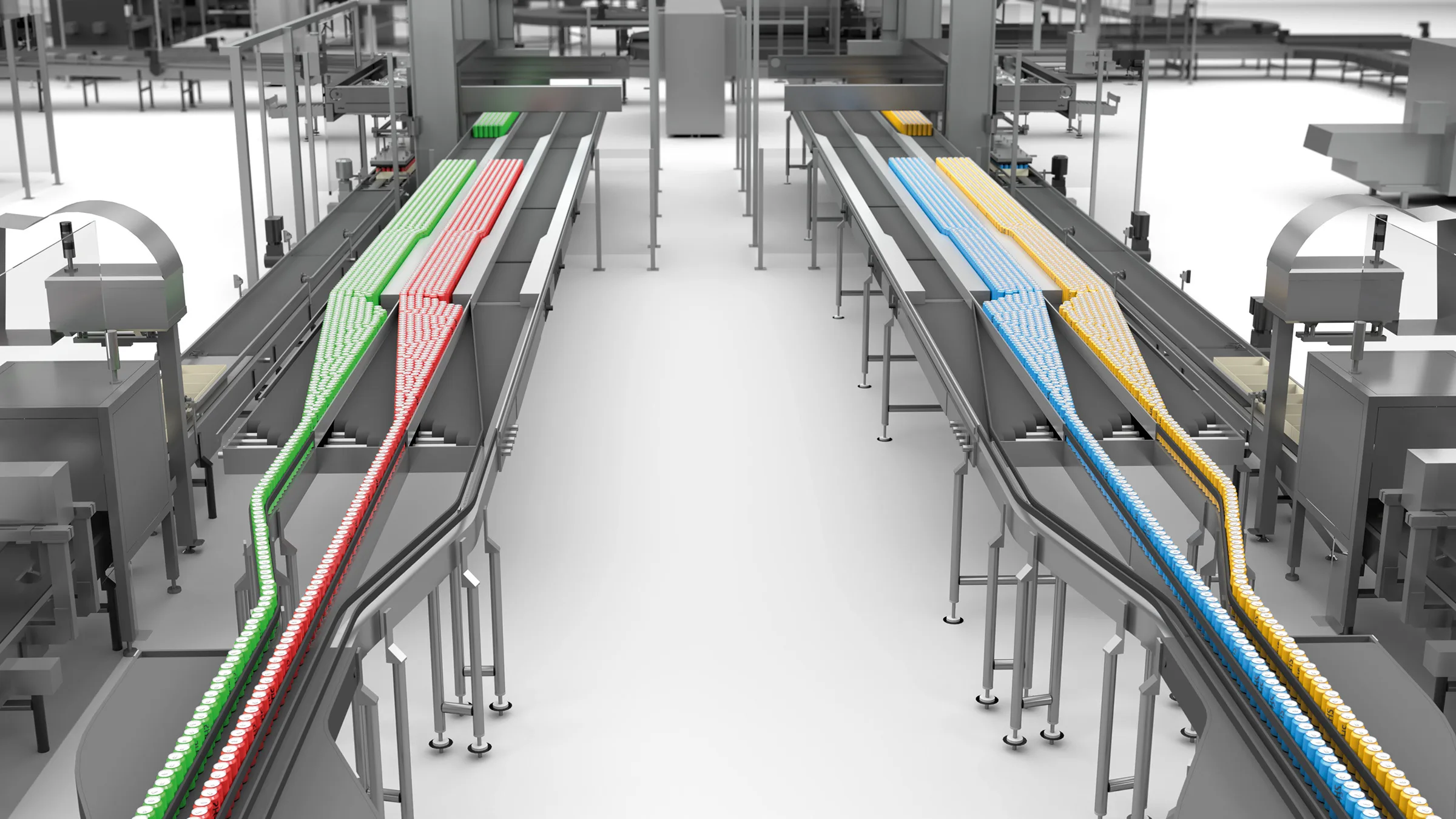
Pasos 2 y 3: Las latas retiradas de las bandejas en el fondo son colocadas en la cinta transportadora por la Innopack PPZ, clasificadas por tipo y transportadas desde allí en una sola vía.
Encontrará más información sobre el sistema de cambio de embalaje de KHS para Variety Packs en khs.com.
Configuraciones hechas a medida
KHS también ha desarrollado configuraciones de líneas para el rango de rendimiento medio a alto. En la variante de hasta 36.000 latas por hora, por ejemplo, un robot asume dos tareas al mismo tiempo: Por un lado el despaletizado y por otro lado el desembalaje de los envases de las bandejas. Esto proporciona una huella ambiental más compacta y menores costes de inversión.
Según Schneider, el embalaje en Variety Packs en el sector de alto rendimiento tiene demanda principalmente en el segmento de latas. En consecuencia, la máquina de embalaje se diseñó de tal manera que las latas se pueden colocar sueltas en las bandejas. A medio plazo ve potencial para botellas de vidrio. Con KHS, aquí no hay límites para la variedad, resume Schneider.