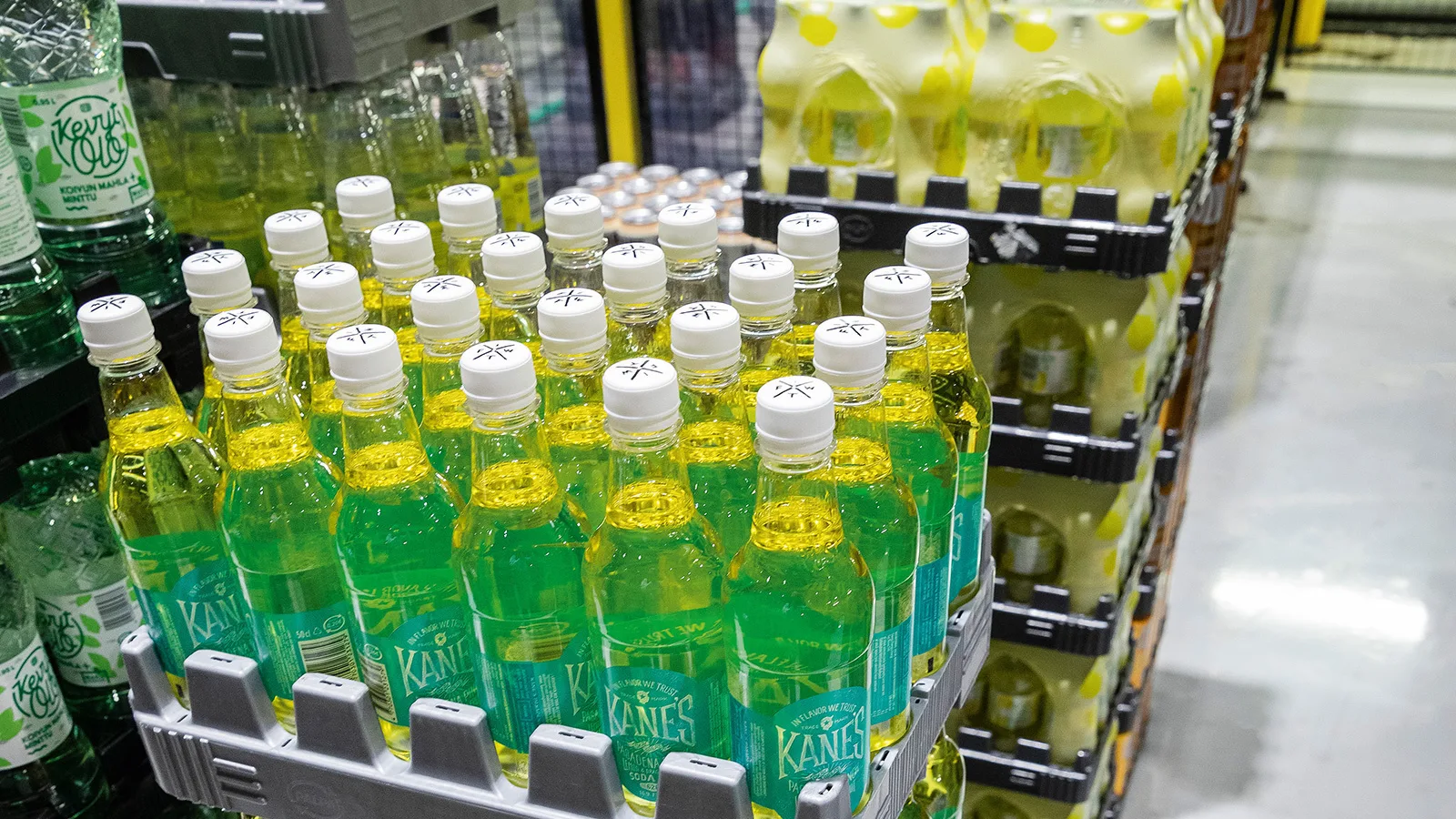
Anpassungskünstler
Eine fast unüberschaubare Vielzahl verschiedenster Produkte füllt die finnische Olvi-Gruppe ab – entsprechend komplex und vielfältig ist das Verpackungssortiment. Seit über zehn Jahren verlässt sich der Getränkehersteller dabei auf KHS, die jeden dafür erforderlichen Umbau möglich machen.
Als die heute unter dem Namen Olvi bekannte Brauerei 1878 im idyllisch am Porovesi-See gelegenen Städtchen Iisalmi gegründet wird, gibt es in ganz Finnland 78 Brauereien. 143 Jahre später ist sie die einzige noch unabhängige und in finnischem Eigentum befindliche. Entsprechend wird die Unternehmensgeschichte von der erfolgreichen Entwicklung, Herstellung und Vermarktung einer Vielzahl an unterschiedlichen Biersorten und Erfrischungsgetränken geprägt, was zu einem rasantem Wachstum geführt hat – besonders seit dem Börsengang von 1987. Heute ist die Olvi-Gruppe außer in Finnland auch in den drei baltischen Staaten Estland, Lettland und Litauen sowie in Belarus mit ihren Produkten und eigenen Produktionsstätten vertreten. Insgesamt erwirtschaftet die Gruppe im Jahr 2019 mit einem Ausstoß von 718 Millionen Liter einen Umsatz von 409 Millionen Euro, rund 41 Prozent davon im Heimatmarkt.
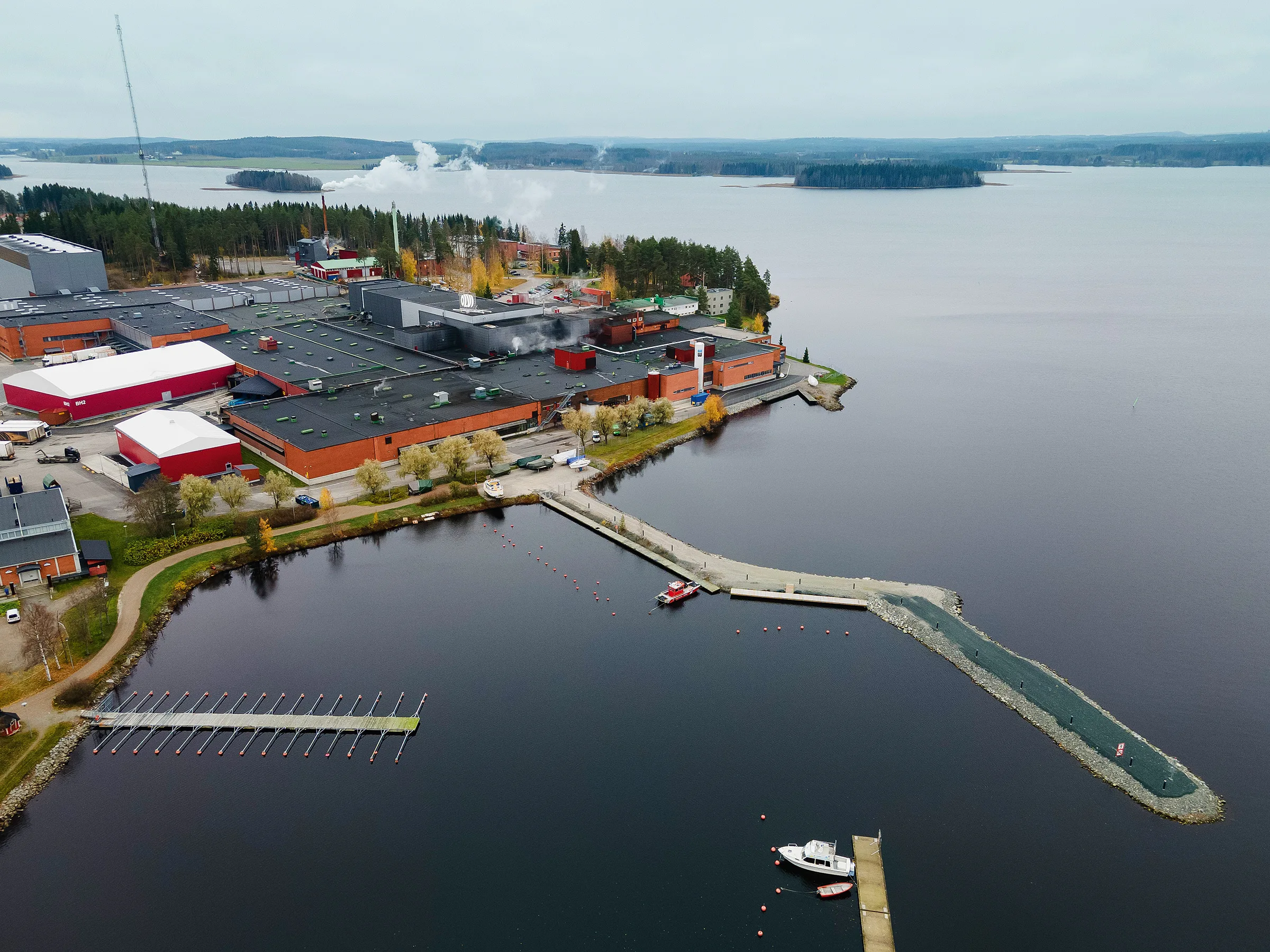
Inmitten der unberührt wirkenden finnischen Natur am Porovesi-See liegt das Hauptquartier der Olvi-Gruppe.
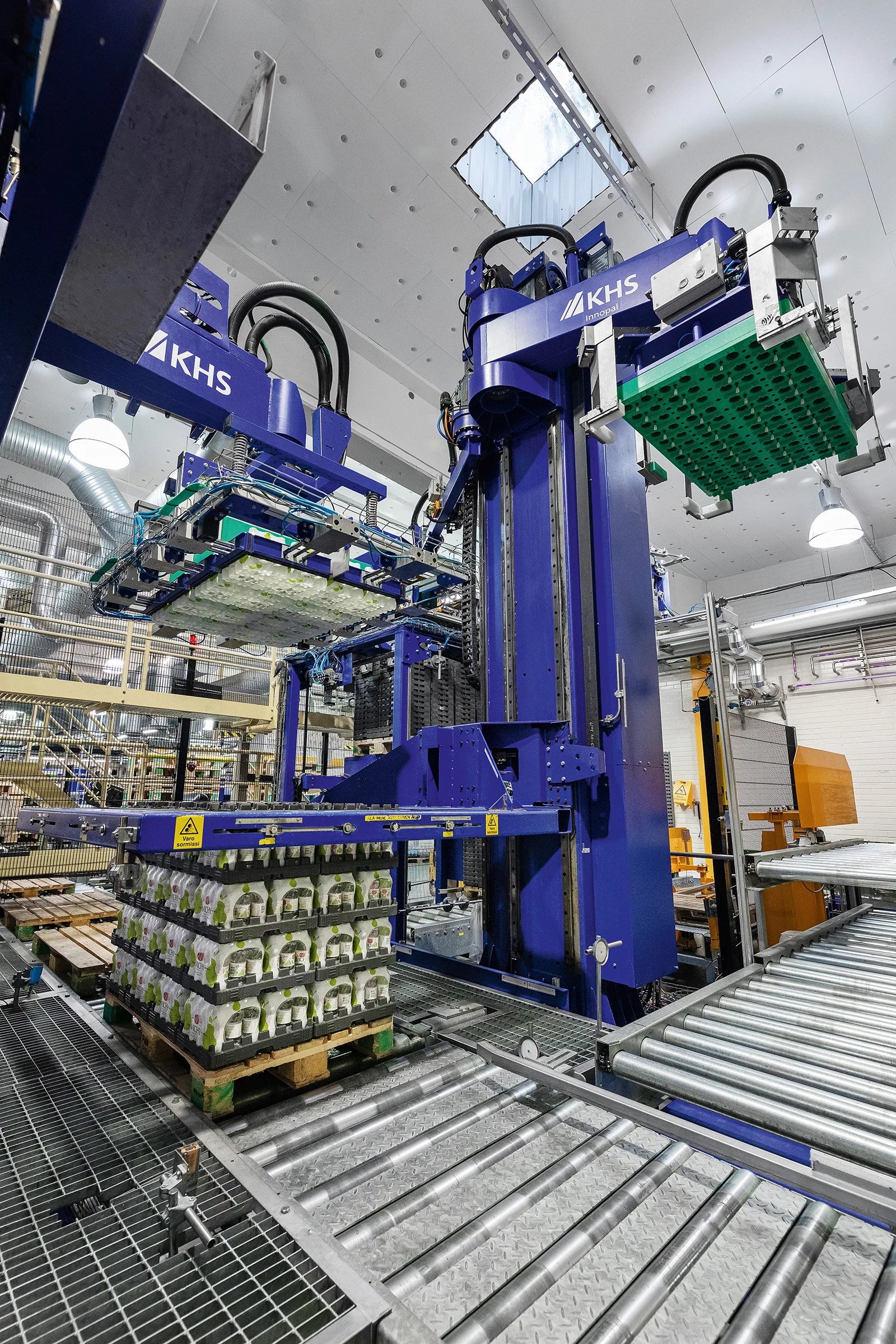
Zu den 18 Umbauten, die von KHS seit 2010 im Trockenteil vorgenommen wurden, zählt auch der Austausch von Flaschenköpfen mit KUKA-Roboter-Steuerung.
Riesige Vielfalt
Zum ausgedehnten Sortiment gehören neben Bier unter anderem Cidres, Hard Seltzer*, Fruchtweine, Softdrinks, Wasser und Fruchtsaftgetränke. „Wie in der übrigen EU gibt es auch in Finnland immer vielfältigere und neue Kategorien“, beschreibt Olvis Operations Director Lauri Multanen den wichtigsten Trend in seiner Branche. „Wir entwickeln zum Beispiel laufend neue Energydrinks, Sport- und Wellnessgetränke. Zwar erzielen wir das größte Volumen mit Bier. Das stärkste Wachstumssegment sind jedoch solche Produkte mit Zusatznutzen.“ Die ansteigende Zahl an Produktmarken schlägt sich natürlich auch in einer zunehmenden Verpackungsvielfalt nieder. Hinzu kommen sich ändernde Bedürfnisse und Gewohnheiten der Konsumenten: „Die Nachfrage nach kleineren PET-Flaschen in Multipacks, zum Beispiel in 24er-Packs, wächst – trotz der Plastikdiskussion der letzten Jahre“, stellt Multanen fest. „Das Thema Recycling gewinnt jedoch an Bedeutung – nicht zuletzt im Zusammenhang mit den EU-Verordnungen: Wir verfolgen diese Entwicklung sehr aufmerksam und arbeiten gemeinsam mit unseren Zulieferern an zukunftsfähigen Lösungen, auch in Hinblick auf das Thema Tethered Caps (siehe dazu auch Artikel „Deckel drauf?“). Schließlich verstehen wir uns als Vorreiter in unserem Markt und gehen proaktiv mit dessen Herausforderungen um.“
* Hard Seltzer = Ein alkoholisches und vergleichsweise kalorienarmes Getränk, das kohlensäurehaltiges Wasser, circa fünf Prozent Alkohol (aus Fermentierung) und häufig Fruchtgeschmack enthält.
Einer dieser Zulieferer ist KHS, der mit Olvi durch eine langjährige Zusammenarbeit verbunden ist. Von den insgesamt sechs Linien im Stammwerk in Iisalmi – zwei PET-, zwei Dosen-, eine Keg- und eine Einweg-Glas-Linie – sind drei mit KHS-Innopack-Kisters-Verpackungsmaschinen bestückt. Eine der beiden PET-Linien stammt komplett von KHS. Sie wurde 2007 durch den Dortmunder Systemanbieter installiert und in Betrieb genommen. Auf ihr können bis zu 18.000 Flaschen pro Stunde verarbeitet werden.
„Unsere KHS-PET-Linie ist ein echtes Arbeitstier“, erklärt Pekka Kääriäinen, Technical Manager bei Olvi in Iisalmi. Das gilt besonders für den Füller-Verschließer-Block und die Mischanlage, findet er. „Aber eigentlich ist die gesamte Linie besonders belastbar und zuverlässig. Schließlich läuft sie an sieben Tagen in der Woche rund um die Uhr. Und von den insgesamt 400 SKUs**, die unsere Gruppe produziert, entfallen rund 90 auf diese Anlage. In den letzten acht Jahren haben wir die Linienauslastung um rund 30 Prozent und den Wirkungsgrad um 20 Prozent steigern können, obwohl an den Maschinen selbst – außer dem Austausch des Bedienpults sowie der Servoantriebe für den Füller – keine wesentlichen Veränderungen vorgenommen wurden“, betont Kääriäinen. „Mit den üblichen Stellschrauben wie zum Beispiel der Verkürzung der CIP-Reinigungszeiten lassen sich zwar gewisse Effekte erzielen. Die größte Effizienzsteigerung haben wir jedoch durch die Verkürzung unserer Umrüstzeiten erreicht, indem wir unser Bedienpersonal – auch unter Einsatz der Trainingskompetenz von KHS – intensiv geschult und die Planung der Formatwechsel optimiert haben.“ Angesichts des Portfolios und eines vergleichsweisen kleinen Markts zählen die Flexibilität und die Geschwindigkeit der Umstellungen aus Kääriäinens Sicht zu den wichtigsten Erfolgsfaktoren.
** SKUs = Stock Keeping Units, Artikel
»Bei der Entwicklung unserer 30 Flschenformate haben uns die Bottles & Shapes™- Experten von KHS unterstützt.«
![]()
Operations Director, Olvi-Gruppe
Wachsende Komplexität
„Als die Anlage vor 14 Jahren gebaut wurde, hatten wir mit Olvi das Wachstum gleich mitgeplant“, erinnert sich Gunnar Bartel, bei KHS als Service Inspector für Skandinavien und das Baltikum zuständig. „Ursprünglich sind wir im Trockenteil zum Beispiel mit zwei Palettentypen und beim Belader mit 25 Formationen gestartet – heute sind das fünf beziehungsweise 82.“ Die gestiegene Komplexität resultiert unter anderem aus speziellen in Skandinavien üblichen Kunststoffdisplays, die entweder mit losen Flaschen oder mit Vierer-, Sechser- und Zwölferpacks bestückt werden. Darüber hinaus kommen für die Belieferung kleinerer Verkaufseinheiten wie Tankstellen und Kioske auch Dollys*** zum Einsatz. Außerdem nutzt Olvi weitere Packgrößen, die immer wieder im Rahmen von Promotion-Aktionen angeboten werden, um die Nachfrage zu erhöhen.
*** Dolly = rollende Mehrweg-Ladungsträger mit Grundmaß von 400 mal 600 Millimeter (Format Viertel-Palette)
Seit 2010 haben Gunnar Bartel und sein Team bislang 18 Umbauten im Trockenteil vorgenommen. Dazu zählen etwa der Austausch von Flaschenköpfen mit KUKA-Roboter-Steuerung, oder ein Hilfsroboter für die Verarbeitung von Zwischenlagen. Es wurden Stellplätze für verschiedene Packköpfe nachgerüstet, damit die Umbauzeiten minimiert werden konnten. Für die vielfältigen Flaschenformen mit ihren unterschiedlichen Durchmessern wurden zudem entsprechende Packköpfe wie zum Beispiel ein Multigreifkopf bereitgestellt, um zu ermöglichen, dass jede erdenkliche Gebindevariante palettiert werden kann.
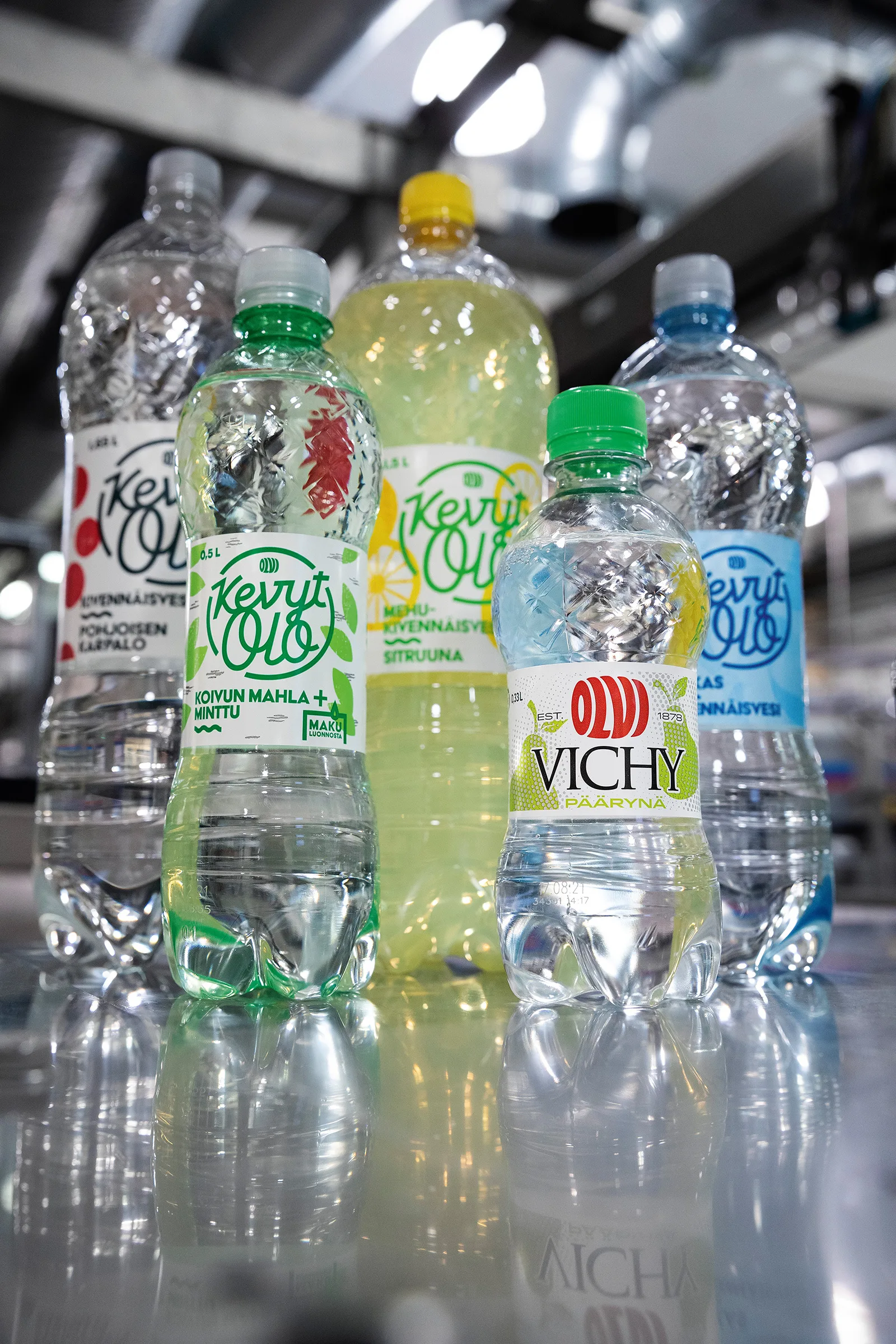
Jedes einzelne der 30 Olvi-Flaschenformate entstand unter Mitwirkung der KHS-Experten des Bottles & Shapes™-Programms.
Umfassender Service
Flexibilität ist auch im Nassteil gefragt: „Heute produzieren wir insgesamt 30 verschiedene Flaschenformate“, erklärt Multanen. „Bei der Entwicklung jedes einzelnen unterstützen uns die KHS-Experten des Bottles & Shapes™-Programms. Dabei haben wir immer sehr gute Erfahrungen gemacht – angefangen von dem Flaschendesign und den Prototypen, anhand derer wir unsere Entscheidungen treffen, bis hin zur Implementierung in der Linie. Dieser Service funktioniert ausgezeichnet – das schätzen wir sehr. Denn gerade angesichts unserer vollautomatischen Kommissionierung muss alles reibungslos ablaufen.“ Ein großes und immer wiederkehrendes Thema beschäftigt sich daher mit der Gewichtsreduzierung, die mit der Zeit zu umfangreichen Materialeinsparungen geführt hat: So wiegt beispielsweise eine 330-Milliliter-Flasche heute nur noch 15,8 Gramm – vor ein paar Jahren waren es noch 18,5 Gramm.
Entsprechend zufrieden fällt das Gesamturteil der Finnen aus: „Mit KHS haben wir einen verlässlichen Partner an unserer Seite, der sein Handwerk im Bereich der Getränkeverpackung mehr als versteht“, betont Multanen. „Wann immer wir technologische Unterstützung benötigen, ist KHS auch in Zukunft eine erste Adresse für uns.“