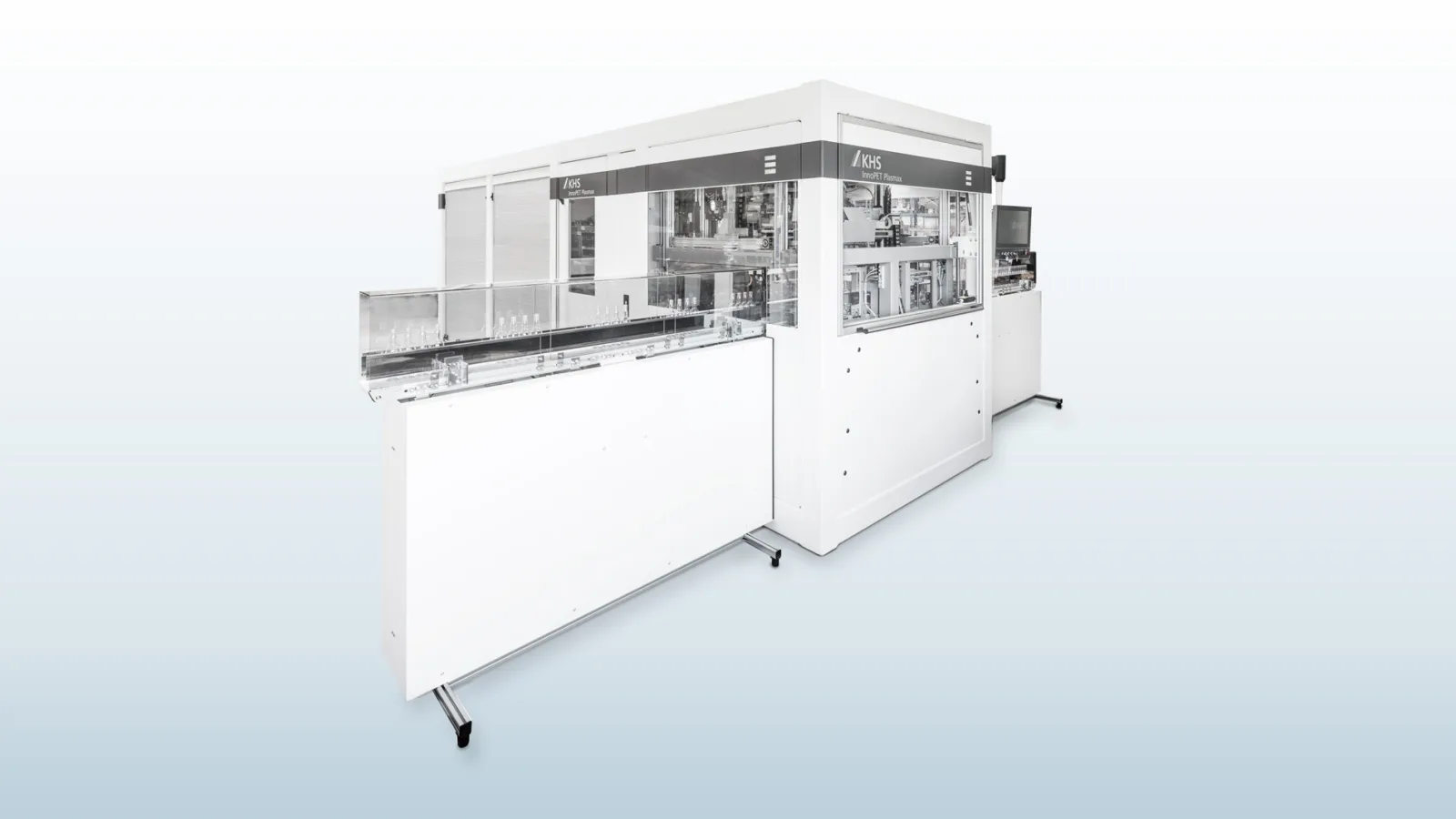
Great protection for small batches
For the very first time Plasmax FreshSafe PET® coating technology from KHS is now available for the low capacity range.
This means that in the future converters and the food industry will also profit from low container weights coupled with perfect barrier properties.
In practice PET containers are most notably lauded for their extremely low weight and exceptional robustness – or ‘unbreakability’, to quote the word frequently used in conjunction with these receptacles when they first came onto the market. These are properties from which the entire value chain benefits – from filling through logistics to the retail trade. Plastic bottles mean prevention of broken glass and lower costs for transportation, with consumers appreciative of this safe and practical form of packaging. In order that easily perishable or particularly taste-sensitive foods can also be packed with all the benefits, however, the barrier properties of the PET container have to be improved.
Wafer-thin layer of glass
Not until KHS launched the Plasmax barrier coating process in 2003 was it possible to combine the low weight and robustness of the plastic bottle with the perfect barrier properties of a glass bottle – without forfeiting full bottle-to-bottle recyclability. In this procedure wafer-thin silicon oxide (SiOx) is deposited on the inside of the PET container, creating a protective layer of chemically pure glass. This guards sensitive products against the penetration of oxygen and carbonated beverages from the loss of carbon dioxide. As the layer is not very thick in the special Plasmax process it remains flexible yet inseparably bonded to the PET.
The taste of sensitive products is retained by the patented Plasmax coating and shelf lives are considerably lengthened – an important consideration when dealing with high-quality fruit juices, for example. For other beverages, too, among them wine, beer or soft drinks, and liquid foods such as pasta sauces and salsa the interest in using PET as a packaging material is growing through this process.
To date, however, Plasmax technology was only available for the high and medium capacity range. Designed for large product lines, the InnoPET Plasmax 20Q with its 20 quadruple coating stations is capable of outputting up to 40,000 PET bottles an hour holding 500 milliliters. The InnoPET Plasmax 12D with 12 double coating stations finishes up to 12,000 PET bottles per hour with a protective layer of glass.
Plasmax technology is now also available for block systems. On the InnoPET FreshSafe block the coating unit is blocked with a stretch blow molder – a setup which the Eckes-Granini Group, one of the biggest producers of fruit beverages in Germany, recently invested in at its plant in Bad Fallingbostel. A number of InnoPET FreshSafe TriBlocks are also in successful production on the market, blocks which include a filler in addition to the above two machines.
At drinktec 2017 the Dortmund systems supplier recently presented a compact version of its InnoPET Plasmax plant engineering in the InnoPET Plasmax 2Q, making its highly efficient coating technology available for smaller batches in the low capacity range for the first time ever. With its two quadruple coating stations it processes PET containers with a volume of between 80 milliliters and 1.5 liters and a neck diameter of up to 38 millimeters. The system outputs 1,800 0.5-liter containers per hour. There is also a parallel InnoPET Plasmax 4Q version available with four quadruple coating stations and an output of 3,600 500-milliliter containers an hour.
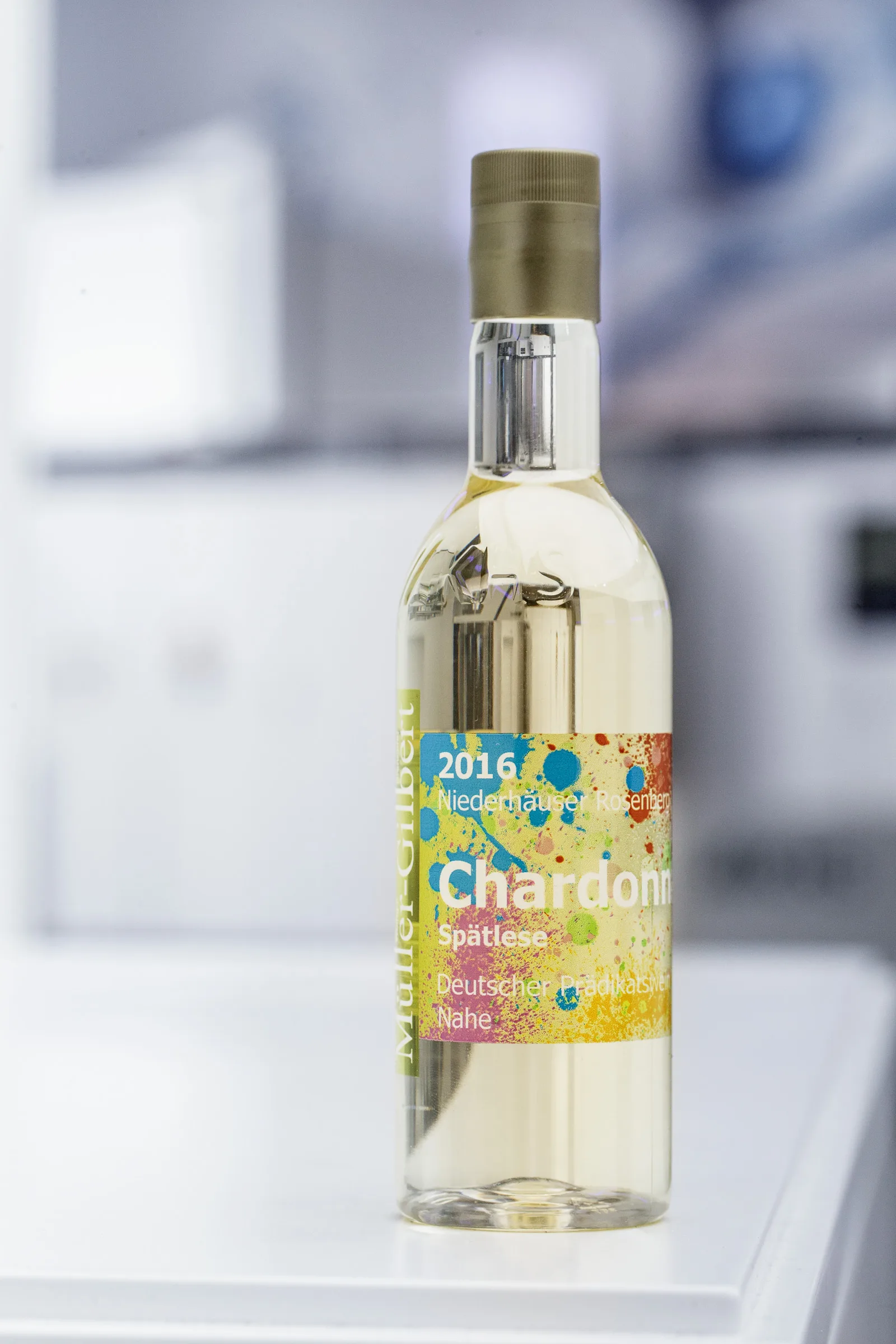
A wafer-thin layer of pure glass also protects sensitive products such as wine from oxidation.
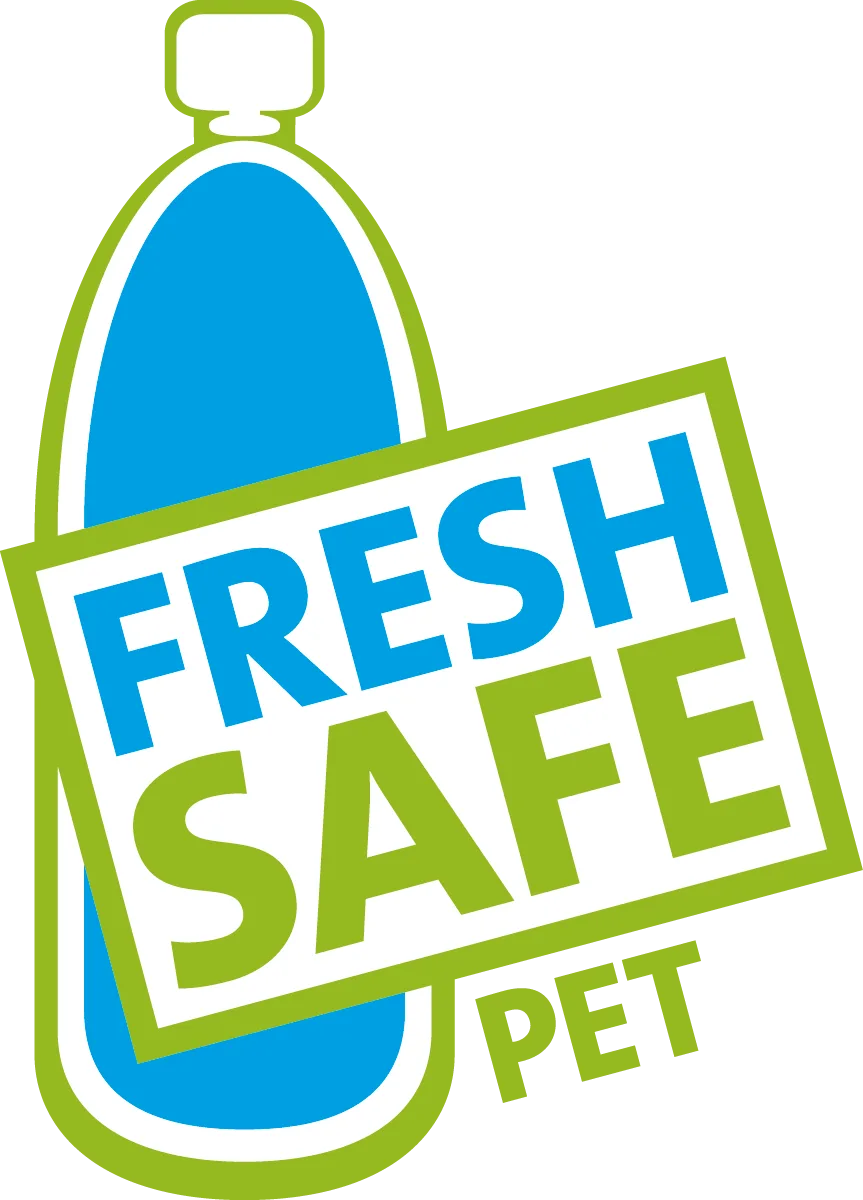
The FreshSafe PET® logo stands for top-quality barrier protection for sensitive beverages and liquid foods.
High-tech coating on a small scale
- Coating of PET containers for high-quality fruit juices, wine, beer and soft drinks, salsa and pasta sauces
- Practical for the pilot production of food and beverages
- Ideal system for converters
- Two or four quadruple coating stations
- 1,800/3,600 0.5-liter containers coated per hour
Two target groups
In developing this system KHS had its potential clientele firmly in mind. “The new, compact InnoPET Plasmax machines focus on two target markets: firstly, food and beverage producers who wish to develop new markets through pilot production, and secondly, customers whose filling quantities were too low to date to enable them to profit from a technology already successfully established on the market,” explains Philipp Langhammer, product manager at KHS Corpoplast. “This includes converters in particular, who trade in empty containers. It’s usually not worthwhile for their customers, who often only need two to ten million containers a year to buy their own machine.” With the InnoPET Plasmax 2Q or 4Q bottle manufacturers can now also produce containers with a less volume and in smaller batches for these customers, such as PET wine bottles holding 187 milliliters. This is of especial interest to airlines, where owing to immense cost pressure every single gram of weight saved counts.
“With our new InnoPET Plasmax machines we can support our customers as they grow.”
![]()
Product manager for barrier technology, KHS
Compact and proven
The extremely compact machine is shipped fully assembled in a classic overseas container, allowing it to be quickly commissioned within a small area at its final destination. “We’ve transferred the processes on our high-performance machines to the new Plasmax 2Q and 4Q. This has enabled us to also make use of many of the proven components on our existing machinery,” states Langhammer. As on its big sisters, the new ClearLine HMI (human machine interface) permits exceptionally intuitive machine handling with gesture-based operation and a clear 21.5-inch display. This is where machine operators log on to the InnoPET Plasmax 2Q and 4Q easily by means of RFID access control, after which the data appears on the menu screen.
“With its new InnoPET Plasmax machines KHS is giving a market segment access to high-quality interior coating which up until now couldn’t use this technology as its capacity range was too high,” concludes Langhammer. “We are now able to support our customers right from the start as they grow.”