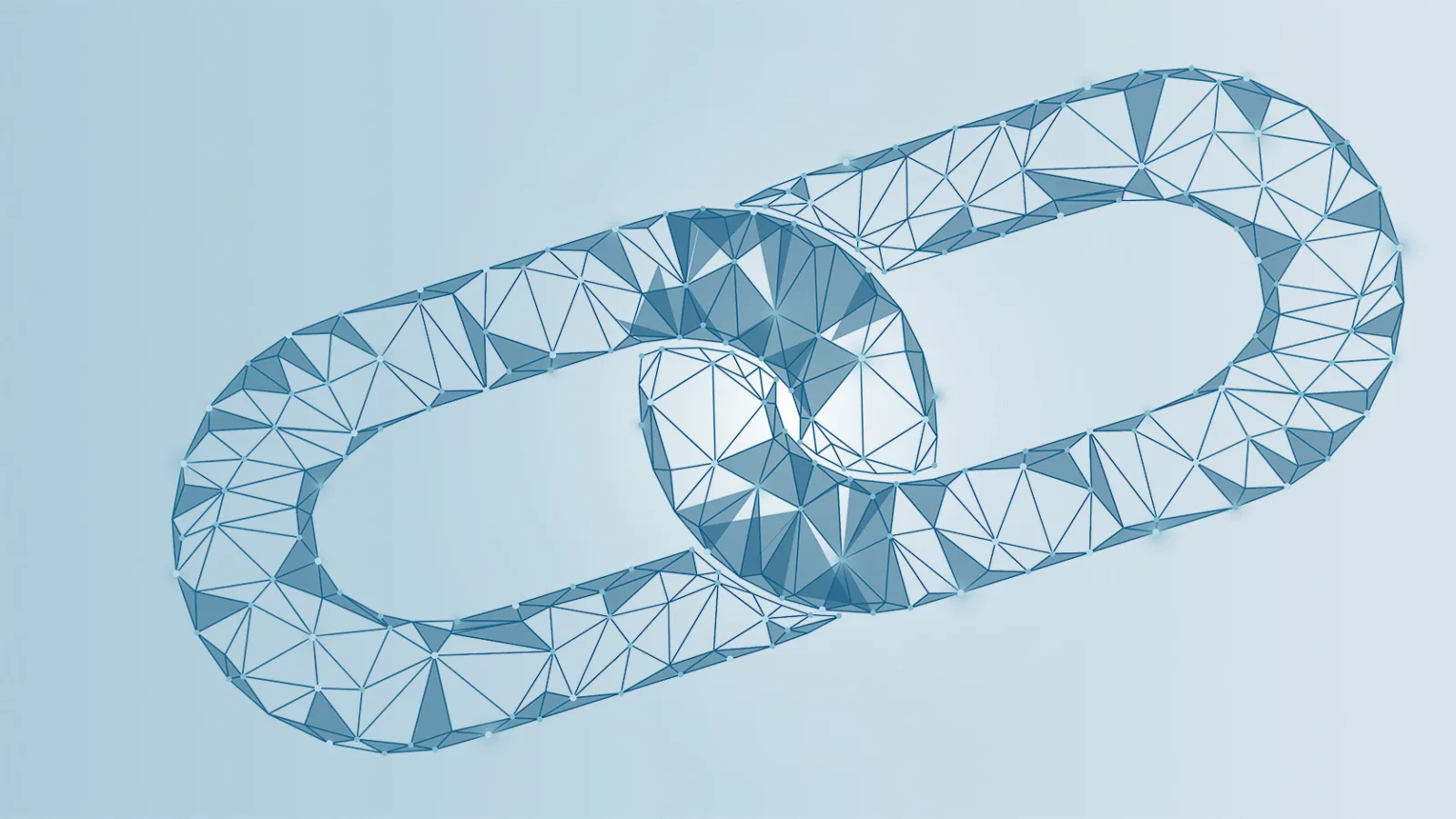
Resilient to crisis
Digital communication and processes can never fully replace personal contact or the human factor. Just how helpful virtual systems and solutions can be, however, becomes particularly clear when face-to-face encounters are suddenly rendered impossible by the current pandemic.
March 2020: the coronavirus has now also reached Europe; borders that were otherwise open are successively being closed. KHS engineers are at the Borgloon plant operated by Belgian contract filler Konings, busy delivering and installing a new KHS non-returnable glass filler. At a time of global insecurity, they tirelessly and literally give their all right up to the last minute in order to finish the project before the borders are finally shut. “Being there for the customer – for us – in this difficult situation shows full commitment,” states Konings CEO Joris Brams, visibly impressed in a self-made video posted on social media. “We’d like to express our heartfelt thanks to KHS for the fact that their colleagues, separated from their families, turn up here day after day to do their job.” Brams also stresses that on its seventh KHS line at the Zonhoven plant Konings is now filling disinfectant for hospitals and schools into PET bottles 24/7 in place of the usual alcopops.
Committed service personnel
This example from Belgium is just one of many that show how KHS personnel are surpassing themselves during the crisis and responsibly completing their tasks in uncertain circumstances. But what’s happening where this isn’t possible at the moment due to lockdowns and travel restrictions? A missed service on a production system can have dire consequences: downtime, production stops, loss of productivity and turnover and considerable extra expenditure to maintain production capability can threaten a company’s very existence.
KHS is countering the effects of the pandemic with a number of measures that were in place long before the start of the current crisis. Remote systems were originally devised to shorten reaction times or avoid unnecessary travel. They enable trouble-free maintenance of machines without a KHS service engineer having to be physically present on site. With shutdowns in place, this has taken on a totally new significance.
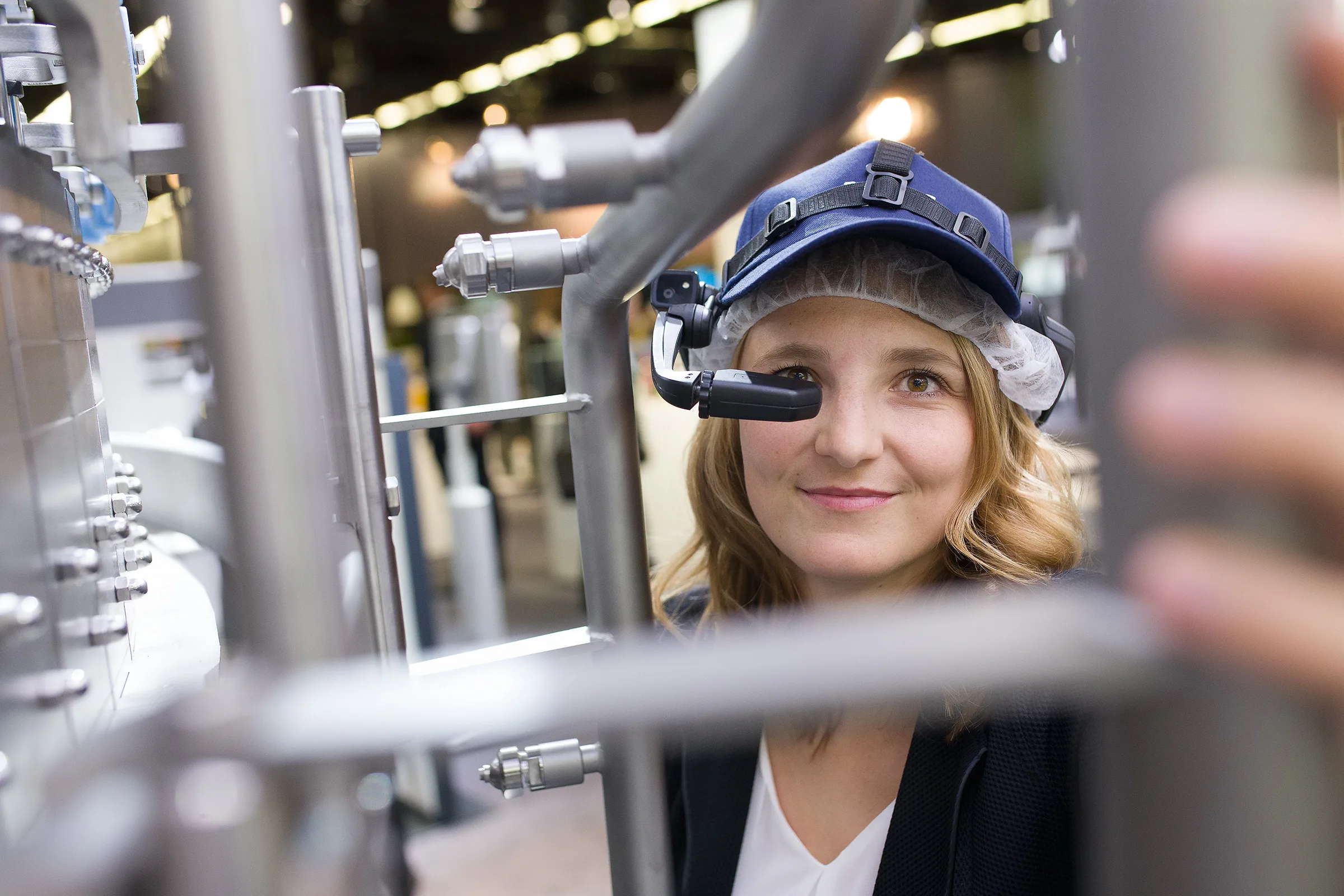
Wearing data goggles the operator has both hands free to carry out the necessary work.
Remote maintenance
This is of course where Remote Diagnostic Service ReDiS should be mentioned, the system of remote maintenance for KHS lines and machines. It allows engineers at KHS headquarters to quickly, easily and securely access registered KHS components worldwide through a network connection at any time. “This means that we can analyze and remedy line faults or transfer software updates and modified system parameters to the local system,” explains Ingo Hackler, head of Remote Services. “For us, ReDiS is an established model of success. We started developing the software for it at KHS as far back as in 2002; more than 2,500 customer projects are now already plugged into the system.”
By linking this to the web-based Innoline MES Basic Line Monitoring (BLM) module line efficiency can be assessed and possible errors pinpointed. In doing so, the system helps to make ramp-up more efficient and also facilitates quick identification of any weak points in the operation of the line for the customer.
»With data goggles our specialists can gain a clear picture of the situation on site according to the principle of ‘I see what you see’ and thus assist the operator.«
![]()
Head of Remote Services, KHS
Four eyes better than two
With today’s highly complex machines it’s often helpful to have additional support when troubleshooting. KHS has risen to this challenge with its Augmented Reality Service (ARS), an audiovisual solution. “Here, the operator wears data goggles,” Hackler tells us. “This enables our specialists to gain a clear picture of the situation on site according to the principle of ‘I see what you see’. To enhance visualization, KHS headquarters can clearly mark objects or display them to the operator who has both hands free and can carry out the necessary work in real time while our KHS expert looks over their shoulder – virtually, of course! We can also transmit images or entire video sequences and issue clear instructions through parallel audio communication.” ARS is compatible with data goggles produced by various manufacturers. During the restrictions imposed by the pandemic, format conversions could be performed at a customer plant in Greece in this manner, for example. The ramp-up phase on a returnable glass line in Mozambique could also be initiated using this technology and complete lines could even be installed and commissioned, such as a high-speed canning line in Nigeria.
KHS also proves itself to be a reliable partner with its 24/7 Service HelpDesk that’s available round the clock for spare parts inquiries, processing technical problems and help when machines stop. The number of personnel has been increased during the corona crisis – a precautionary measure that has turned out to be unnecessary thanks to the robustness of KHS’ plant engineering. Even in times of crisis the Dortmund system supplier’s machinery continues to run reliably and without any trouble. The supply of spare and wear parts is constantly assured – and thus the high availability of the machines.
Digital revolution advanced
The global pandemic has acted as a catalyst for the digitalization of the world’s industry; KHS is no exception. Dialog with customers especially is affected by social distancing measures and threatens to suffer further as a result of trade shows being postponed or canceled. In an attempt to prevent this, the KHS Service Division is holding a number of online expert panel meetings on specific topics in the future. The first in this series of Technical Talks was staged close to the original date of interpack in May 2020. Customers were invited to directly discuss with the specialists issues such as secondary packaging made of paper and lengthening the product life cycle of KHS packaging machines.
Regarding basic and further training, initiatives that had already long been triggered were accelerated in conjunction with Covid-19 distancing rules. Online training courses that adopt the blended learning* approach are now offered for certain topics, with the focus here on direct interaction with participants through webinars.
* Blended learning = combination of ‘classic’ learning methods with online channels to facilitate study, communication, the provision of information and knowledge management regardless of the place and time.
These courses are planned for the long term: both KHS and its customers will continue to profit from the cost and time benefits thereof long after the corona crisis is over.
On khs.com read more on how our remote diagnostic and remote maintenance services ensure that your lines run even more reliably.
KHS CONNECT- Prior to the global rollout
KHS is entering a new era in after sales: KHS East Africa is the first regional center to pilot the KHS Connect integration project, the company’s new central service hub for the digital supply of spare parts. The platform simplifies, accelerates and standardizes the global exchange and flow of information between the various KHS departments and between the customer and KHS. Further regional country portals, through which KHS’ service business can be processed locally, are to follow in the near future in Brazil, Mexico, Nigeria, Dubai, South Africa and China.