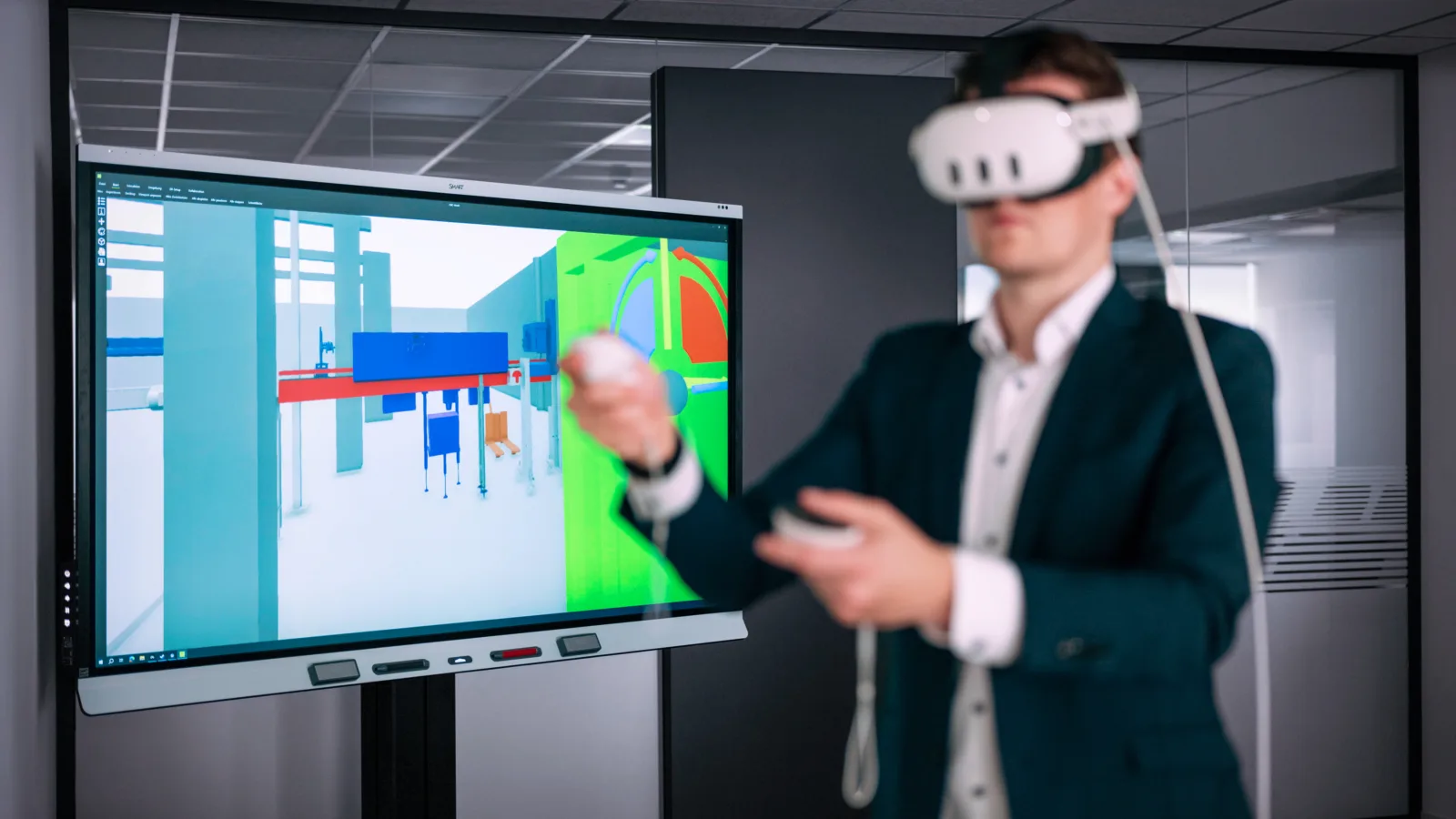
3D line design in real time
More precise planning, simpler handling and quicker results: KHS exploits new technologies for virtual line design.
KHS is taking 3D line design up to a new level: a new generation of mobile laser scanners and technically optimized VR goggles minimizes possible sources of error and provides results in real time. “Beverage producers can now gain a detailed 3D impression of their line within a very short time indeed, one that’s virtually integrated into their real production environment,” says Patrick Bürger, Head of Plant Design at KHS. “This simplifies project planning as early as at the offer stage and greatly improves planning security.”
Obstructions identified in good time
Some customers only have outdated or incomplete plans of their production shops. This can lead to a number of unpleasant surprises. “In the worst case, ventilation systems, columns or similar structures suddenly pop up during installation, thus hampering the ingress of our lines and machines,” explains Bürger. KHS directly eliminates this source of error at the initial planning stage by performing laser scans. These survey and record all interfering contours and potential obstructions with absolute precision.
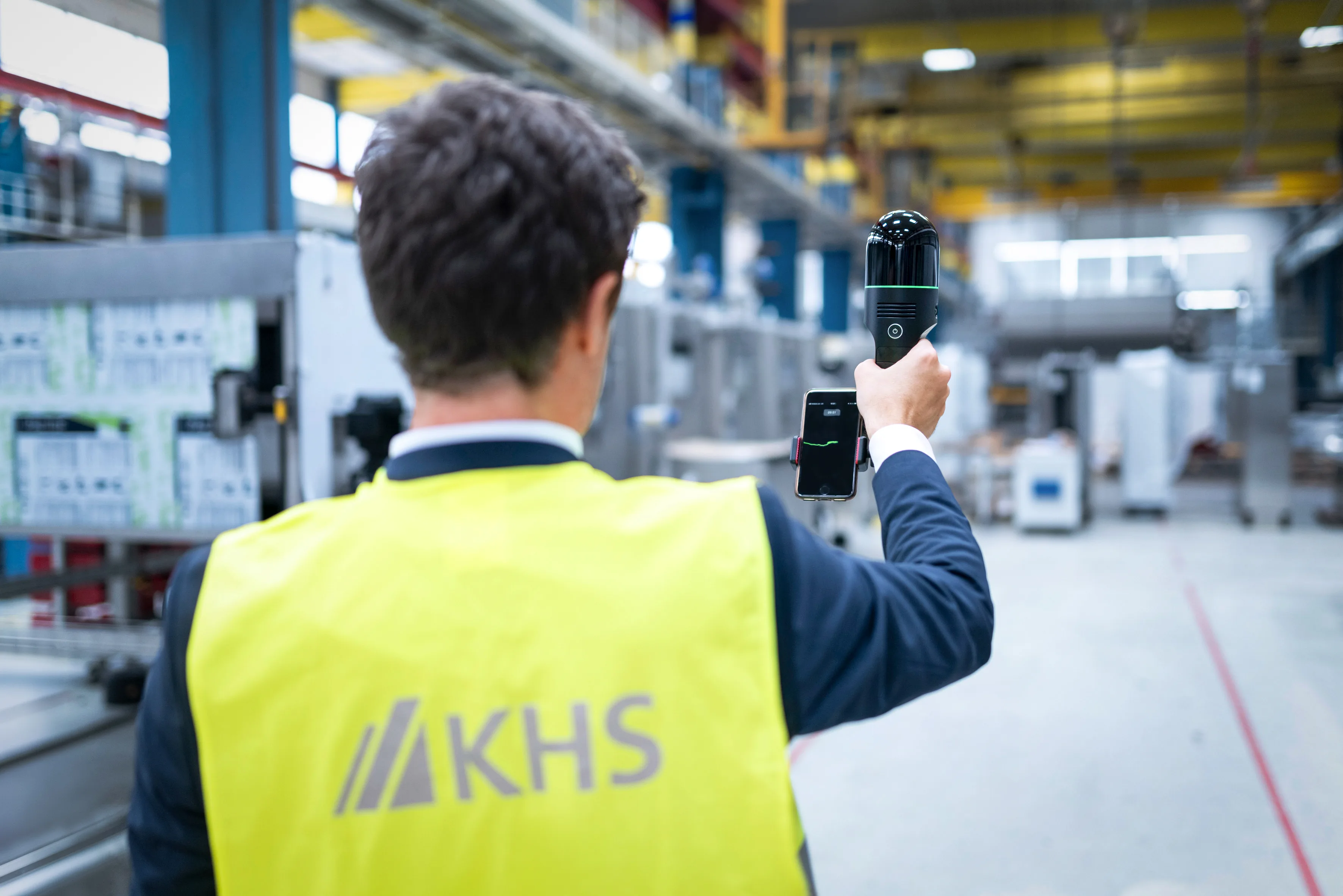
Much easier operation: you simply hold the laser scanner in your hand like a smartphone and make your way around the hall.
Mobile and efficient
Up until very recently, KHS used stationary laser scanners mounted on a tripod. In order to record the space available throughout the entire hall, the scanners had to be frequently moved around and the device readjusted each time. With their intuitive operation, the new generation of laser scanners considerably simplifies this process. “You simply hold the scanner in your hand like a smartphone as you make your way around the hall. The scanner takes 270° pictures of the surroundings. We now only need about a fifth of the time on site we used to, including post-processing,” Bürger states. “The result is a scatterplot that depicts the area exactly as it is.”
Readily available
The new VR goggles with integrated tracking are also a mark of progress. “We only need the goggles, two joysticks and a laptop to display the data. This means that the setup is much simpler and available much more quickly,” Bürger continues.
The same applies to conversion of the data recorded by the scanner to a VR-compatible format. “Processing now only takes a few minutes instead of several weeks.” Any type of modeled KHS line can now be projected onto the VR goggles very quickly – directly from the laser scan to the scatterplot. “This lets our customers experience virtually what their potential new line or machine will actually look like and how it will fit into the existing space early on in the planning process.” This boosts planning security and builds up trust.
“To date, we’re one of the few to combine the scan in real time with 3D planning and incorporate this into initial customer presentations.”
![]()
Head of Plant Design, KHS
Laser scan and VR combined
This synergy of mobile laser scanners and VR goggles with integrated tracking is new to the industry, claims Bürger. “To date, we’re one of the few on the market to combine the scan in real time with 3D planning and incorporate this into initial customer presentations.” Various users in the German-speaking parts of the world have already put this method to successful use. “By the end of the year, we want to have implemented this worldwide, so that beverage producers at all of our sites can profit from the benefits,” Bürger concludes.