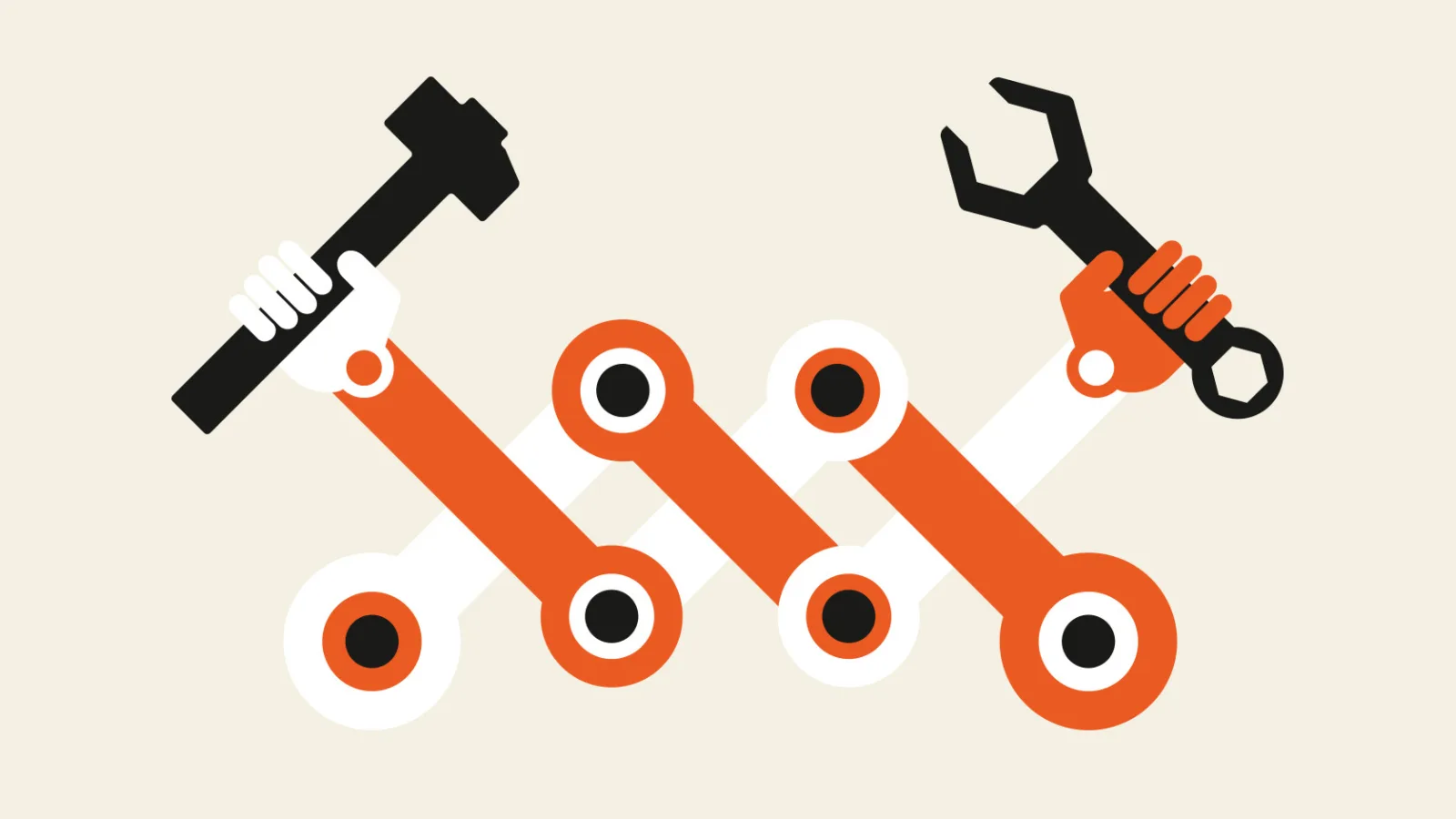
Life-sustaining measures
Unlike mechanical components, in the age of Industry 4.0 the lifetime of an electronic component is growing ever shorter. The following article illustrates what KHS’ Standards Department and Service Division are doing to help customers operate their lines reliably in the long term.
Parts built into KHS machines are discontinued by component manufacturers on a regular basis. This means that in the foreseeable future they will have to be replaced by new parts that have usually been technically upgraded and are in keeping with the state of the art – a completely normal process caused by further technological development which forces both KHS and its customers to act.
According to the German Mechanical Engineering Industry Association (VDMA) the lifetime of an electronic component has now been whittled down to just two years. Other parts such as gear motors are usually available for longer; here, it can take ten years for a successor model to come onto the market. New parts are not merely the result of technical advance, however; modifications to legislation can also make changes necessary – for example if a new European energy efficiency class is introduced for certain drives, meaning that the old motors can no longer be used. This is where KHS Service comes into play, whose principle aim is to safeguard the long-term supply of spare parts throughout the often lengthy service life of its machines, this not seldom amounting to 30 or 40 years. If a component is discontinued, parts must then be replaced accordingly to make sure that the machine continues to function and operation runs smoothly at the respective beverage producer’s plant.
»We can always see which machines are affected. We can thus approach our customers proactively and inform them well in advance.«
![]()
Head of the Standards Department at KHS
Proactive customer support
“Last year, for example, we had around 1,700 discontinuations,” states Klaus Thatenhorst, head of the Standards Department. “In about half of these cases these are relatively simple parts such as light barriers or temperature sensors which we can replace one on one. This is a completely automatic process and the customer often doesn’t even notice it as we automatically supply the new part as and when needed.” A functioning data management system must be in place for this to work. “Thanks to our structured, system-supported data pool we can always see which machines belonging to which customers are affected by which discontinuation. This allows us to address these companies proactively and advise them of the necessity of adapting their machinery well in advance."
Thatenhorst places particular emphasis on adopting a timely approach. After all, for the remaining 50% of discontinuations simple part replacement isn’t enough. Here, conversions are needed which require additional engineering effort. Besides the complexity of the task the number of affected machines also plays a role; depending on how high this is, discontinuation of a major component may keep KHS’ service personnel busy for several years.
Sophisticated solutions
One such case is the discontinuation of the KUKA KR C2 controller which affects two series of KHS palletizers, for instance. “Replacing this will occupy us for the next four to five years,” says Matthias Jansen, head of the Technical Support Service Division at KHS. Robot specialist KUKA has told machine and system manufacturers that its control unit will only be available until 2024. “Sadly, it’s not usual for manufacturers of bought-in parts to give us so much advance notice,” Jansen observes. “We often have to find solutions for our customers very quickly. But when we have such a long lead time, we can be a little more relaxed when planning which changes have to be made to the machine and wiring diagram in order to replace the discontinued controller with a new system. And this fits in with our aim of proactively offering customers a sophisticated and economically viable alternative before a part fails and production grinds to a halt.”
“If an entire filling line stops because someone’s failed to notice that a simple electronic component that perhaps costs just a few euros is no longer available, this can be a time-consuming and very costly business,” stresses Klaus Thatenhorst.
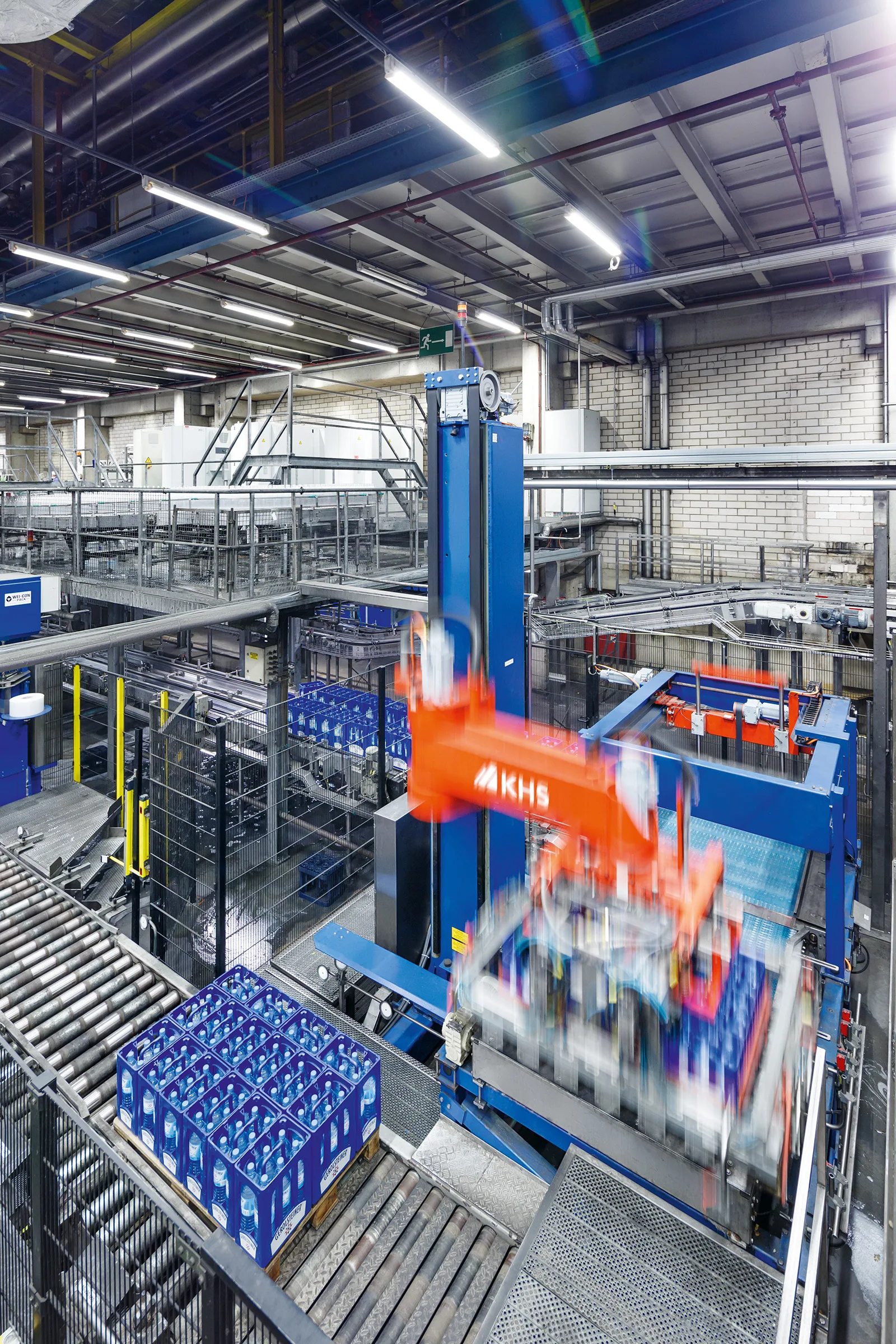
Gerolsteiner is just one KHS customer to profit from the replacement of the discontinued palletizer robot controller.
Conversion with added value
The KUKA controller example also demonstrates the sheer scope of the services offered by KHS’ Service Division when components are discontinued. Discontinuation management also entails maintaining a stock of spare parts for as long as possible. On the one hand, this means warehousing all remaining stocks of the previous control unit. On the other, old devices are collected from customers and the discontinued parts removed and refurbished. “By adopting these strategies we ensure that a machine can continue to function for a certain period,” Jansen explains. “However, at some point it has to be converted.” Here, too, there are several possible options. Depending on the system in need of a revamp, the machinery can simply be converted to the current KUKA or Siemens controller. However, in some cases it can be more economical to replace the drive technology together with the control unit.
A conversion, which for some customers initially means making an investment they haven’t budgeted for, always yields added value, however. “The KUKA controller, for example, is less prone to faults and much more streamlined,” Jansen tells us. “This means an increase in quality: the system supports a trouble-free production process and has a considerably longer service life.” A call to a customer telling him or her that a conversion is required is thus not to be treated as bad news but as good tidings. Firstly, KHS proactively provides a solution which gives customers reliability of supply and production capability. Secondly, KHS ensures that following conversion the beverage producer has a machine which is – to put it simply – better. In this respect discontinuation management is an extremely sustainable way of ensuring that robust production systems have a long service life – while keeping them state of the art.