
As good as new
Bottle washers are among the KHS systems with the longest service lives. This example at Aqua Römer in Mainhardt illustrates how older machines can be given a new lease of life with regard to technology, economy and ecological friendliness.
The long service lives of KHS plant engineering are virtually legendary: machines that have been in operation 30 years and more are not uncommon - some have even been running for over 50 years. This of course makes their owners happy – but can also cause a few headaches. In particular this is the case when suppliers such as control system suppliers discontinue components. Although the Dortmund systems supplier stocks spare parts for its components well beyond the usual life cycle, sometimes replacements are at some point simply no longer available. A new investment then often seems unavoidable. For bottle washers in particular this involves a huge amount of effort which far exceeds the mere cost of procurement. Their vast dimensions make them some of the biggest machines on a filling line. If they have to be replaced, not one but several heavy goods vehicles are dispatched and during ingress various constructional measures are often called for – including opening up the roof of the production shop – plus the use of special cranes.
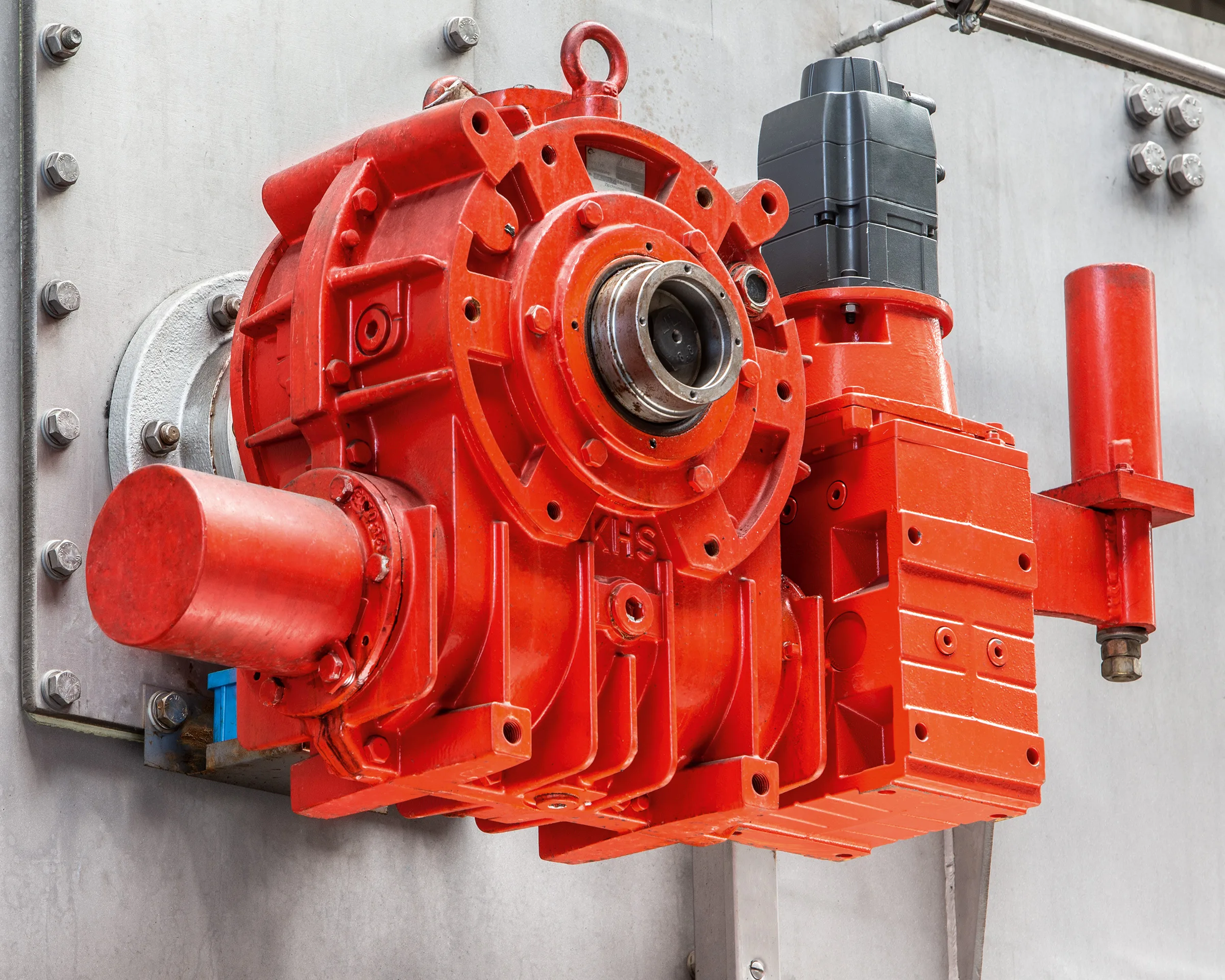
During the conversion at Aqua Römer new servomotors were installed in the existing gears.
Retrofits in a matter of days
For some time now KHS has offered various conversion packages which can put off replacements like the aforementioned for many years. These can be used to bring old bottle washers – regardless of whether they are for glass or PET bottles – into line with the technological and ecological state of the art – with comparatively little effort. “In essence bottle washing technology hasn’t changed in decades,” explains Matthias Jansen, head of the Technical Support Service Division at KHS. “The principle behind the process engineering is the same as it was in the 1980s. What has changed over the years is the energy and water consumption which has dropped significantly.” With upgrades such as the capacity-dependent fresh water controller, LESS, ECO carriers and ECO chains practically all older machines can be retrofitted within the space of a few days and adapted to meet current standards.
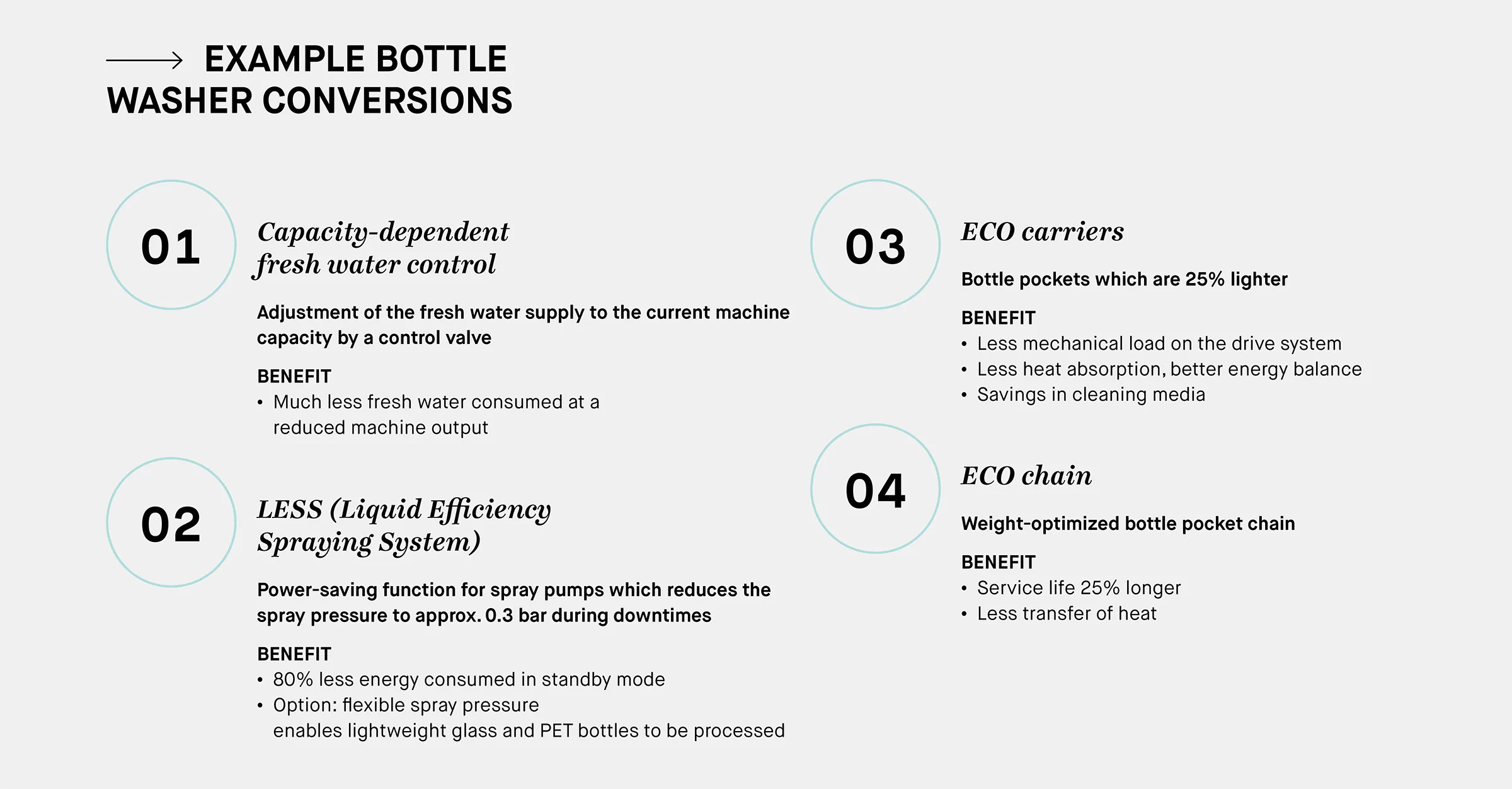
Beyond the service packages and standard measures on offer KHS Service employees also endeavor to cater to the individual requirements of the specific customer and develop tailor-made solutions accordingly. “Sometimes it’s not just about the water consumption and heating costs of the machine itself,” says Jansen. “Sometimes we’re asked how the heat from the bottle washer can be used in other process steps or to heat the production shop, for instance. Or maybe a cooling tower can be connected up to reduce the amount of water used.” Jansen and his team quickly find practical solutions for problems like these – and often also for other more unusual requests.
KHS’ understanding of sustainability goes far beyond energy and resource efficiency, however. “With our range of services we ensure that our customers can operate their machines for as long as possible. Therefore we of course have to make sure that spare parts are available in the long term, especially where electrical components are concerned.” One classic example of this is the replacement of the programmable logic controller. This is necessary where the Simatic S5 version is still in use, long outdated and now actually discontinued by Siemens.
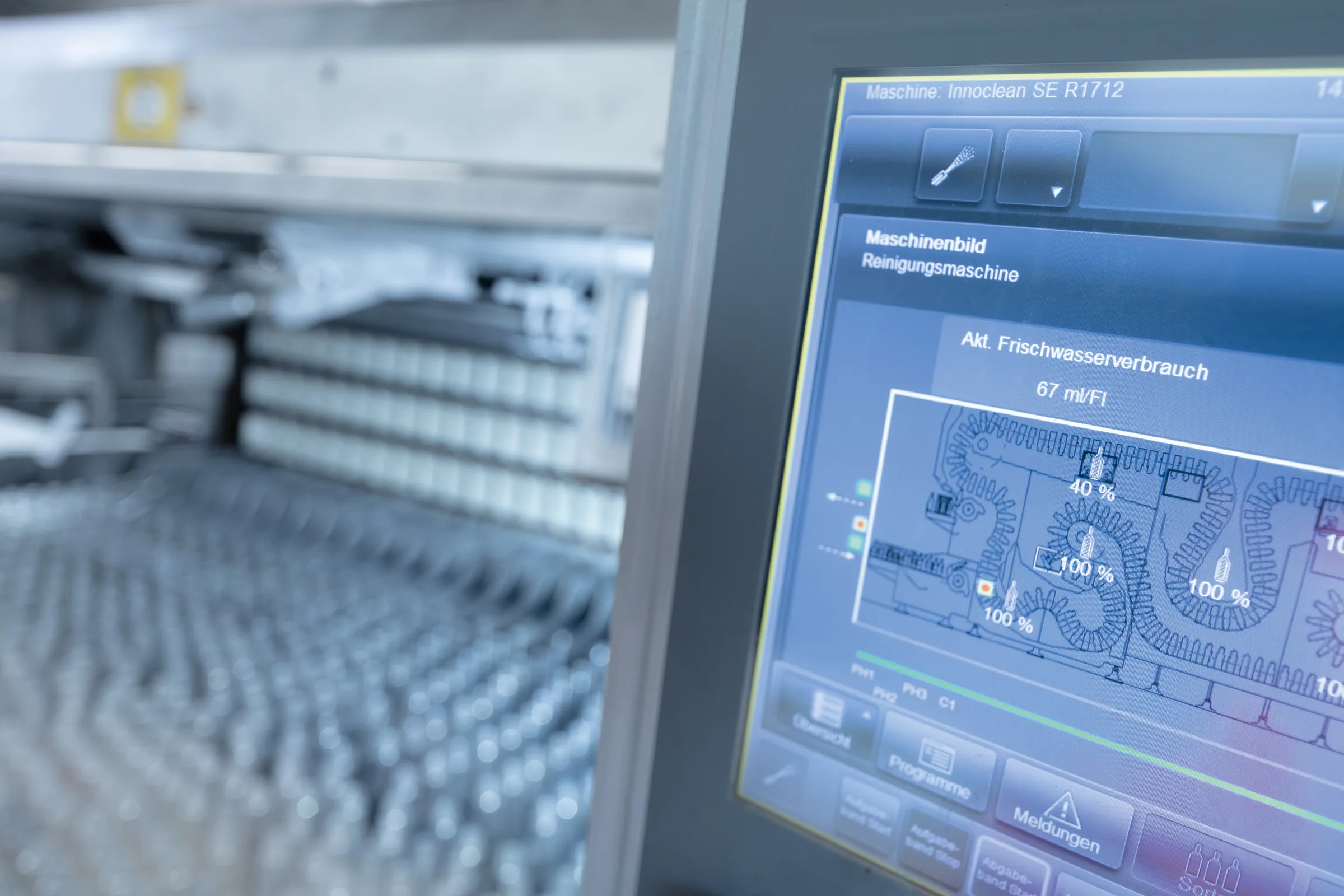
The 15-inch screen on the upgraded HMI 1.5 clearly shows the amount consumed by the capacity-dependent fresh water supply, reduced to 40%.
HMI upgrades: Future proof
Many older operator consoles have been discontinued by the manufacturer. In order to also ensure trouble-free operation of machines in the future and avoid unplanned downtimes, with considerable production loss as a result, KHS provides customized conversions for all KHS HMIs and their predecessors.
Definitely worthwhile
Technological upgrades like the above are only feasible if the machine has been regularly serviced and its structure is still intact. Conversions are then definitely worthwhile as the expenditure for these is a mere fraction of what investment in a new machine would cost. “For this customers then have a machine standing in their production shop within one to two weeks whose performance data is up to the minute,” Jansen promises.
Aqua Römer in Mainhardt in southern Germany is one such customer to benefit from a bottle washer makeover. The second of four lines at the mineral water and CSD bottling plant is a KHS returnable PET bottle line from 2001. It processes up to 24,000 bottles per hour in 0.5- to 1.5-liter formats. This amounts to about 25 million filled bottles per year, around an eighth of the total output Aqua Römer produces at three different facilities. “The reason we refurbished our bottle washer was because there were no more spare parts available for the frequency converter,” remembers Marc Böttler, head of Engineering at the Mainhardt plant. During the conversion to servo drives for the drive system it seemed prudent to also implement various measures to improve energy and media consumption. New ECO carriers, LESS and capacity-dependent fresh water sprays were thus installed. The operating system was also updated to the ClearLine HMI.
Sustainable in every respect
Böttler is very pleased with the results for two main reasons. “The 1.5-liter bottle sometimes used to fall over at the discharge; this no longer happens. And we can now circulate the bottles on the bottle washer and don’t have to run them back if there’s a disruption. The line generally runs much better.” Böttler is also delighted with the savings in energy and media which run to approximately €30,000 each year in this case, especially as his company has made it its goal to produce sustainably for many years. Aqua Römer was one of the first bottling plants in Baden-Württemberg to use returnable bottles made of PET, for example. In 2018 the bottler was even presented with the Reusable Systems Innovation Award by Environmental Action Germany (DUH) and the Foundation for Reusable Systems (SIM). For Böttler sustainability also means keeping a machine going for as long as possible. “I’m reckoning on being able to use our bottle washing machine for at least 15 more years.”
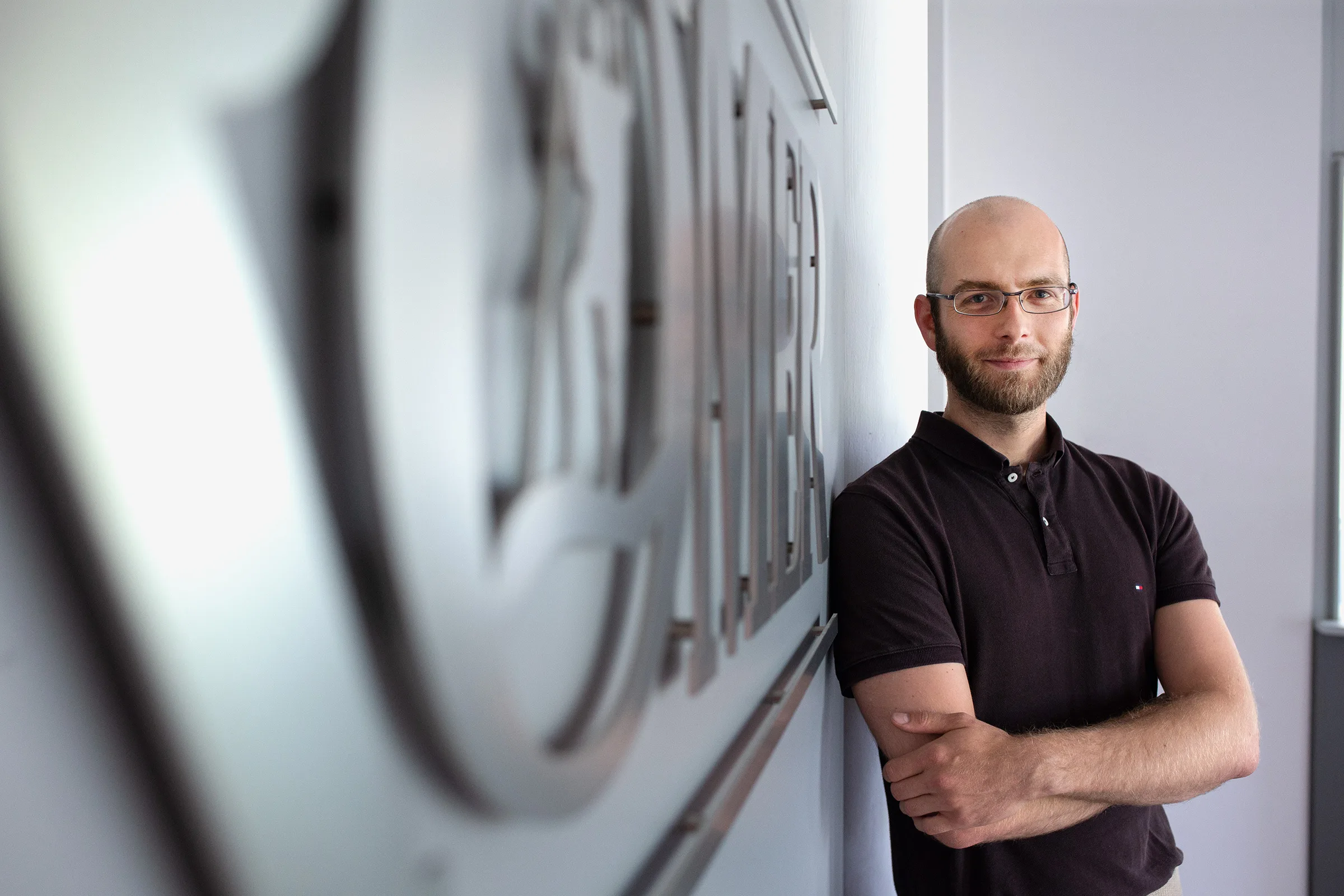
Marc Böttler at Aqua Römer is pleased with the conversion of his bottle washer which amounted to just a fraction of what a new investment would have cost.
KHS doesn’t just provide upgrades for bottle washers, however. “When developing new machines we always allow for the retrofitting of future functions and improvements,” Jansen concludes. “One example is the FullyEnclosed option for shrink packers, another our fillers with ECO valves and ECO vacuum pumps. Vice versa we also make sure that our latest innovations can be installed on older machines. The most important condition here is that the machines are modular.” This all goes to show that the proverbial durability of KHS systems is not just a legend but a tried-and-tested reality.