15.-19.09.2025
Munich / Germany
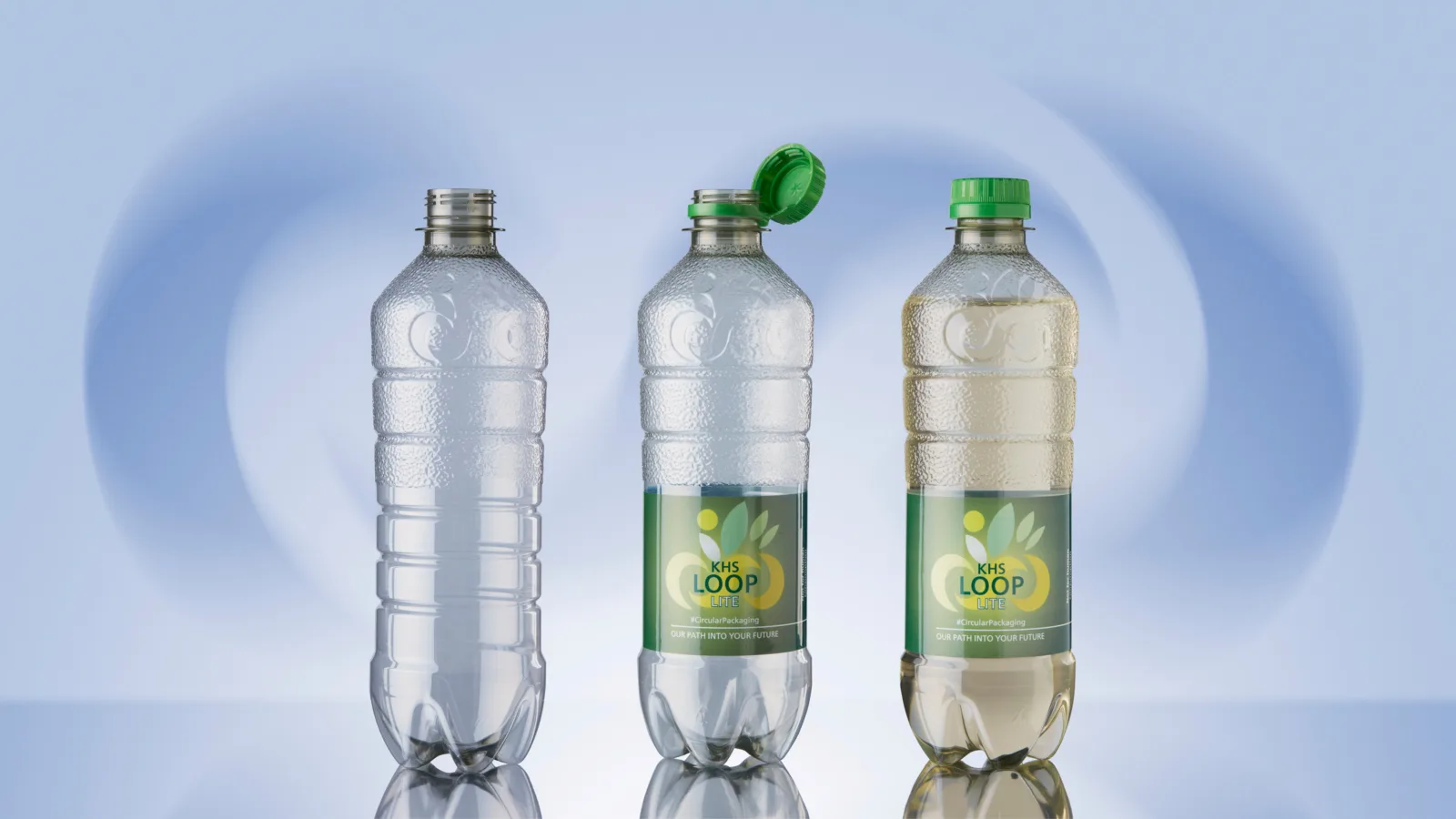
Faster, better, lighter
Since its launch over 20 years ago, Plasmax product protection has been a real success story. So that it stays that way, KHS is investing in its continuous further development for higher capacities, increased efficiency and longer shelf lives.
Around 100 InnoPET Plasmax machines are now in operation or have been ordered worldwide. Each year, they apply a wafer-thin interior coating similar to glass to over 12 billion PET bottles. The pioneering barrier technology from KHS tells a unique story of success. On its market launch in 2003, it was still considered an exotic system for sensitive niche products that usually had to be filled into glass containers. It’s now enjoying rapidly increasing popularity, especially with multinational bottlers of carbonated soft drinks or CSDs. And there are good reasons for this.
These begin with the capacity of the coating machine, for instance: with an initial output of up to 12,000 bottles an hour, this has since increased five-fold. This year, the first system went into operation that produces a maximum of 60,000 containers per hour. And there’s no end in sight by any means, says Philipp Langhammer, barrier technology product manager at KHS. “We’re constantly developing our processes further so that we can achieve even higher outputs in the future.”
50% more capacity
With three process steps and four different gases, the procedure is admittedly rather complex. However, this provides more points where adjustments can be made to control and speed up these processes. “Compared to the machinery built by our market competitors, the coating time isn’t a limiting factor for us. We were recently able to increase the capacity by up to 50% – on the very same 80-cavity platform with practically identical barrier performance.” With Plasmax, it’s not the thickness of the silicon oxide coating that’s important but the fact that this is complete – without any gaps or holes. KHS manages this with very few atomic layers that produce a perfect result within an extremely short processing time.
Alternative, acetylene-based barrier protection systems from the competition require thicker coatings, the deposit of which takes longer and thus limits the output rate. What’s more, the carbon colors the bottles brown, something lots of beverage producers don’t want. The pioneering coating technology from KHS, on the other hand, is completely transparent, providing what’s literally a crystal-clear optical benefit!
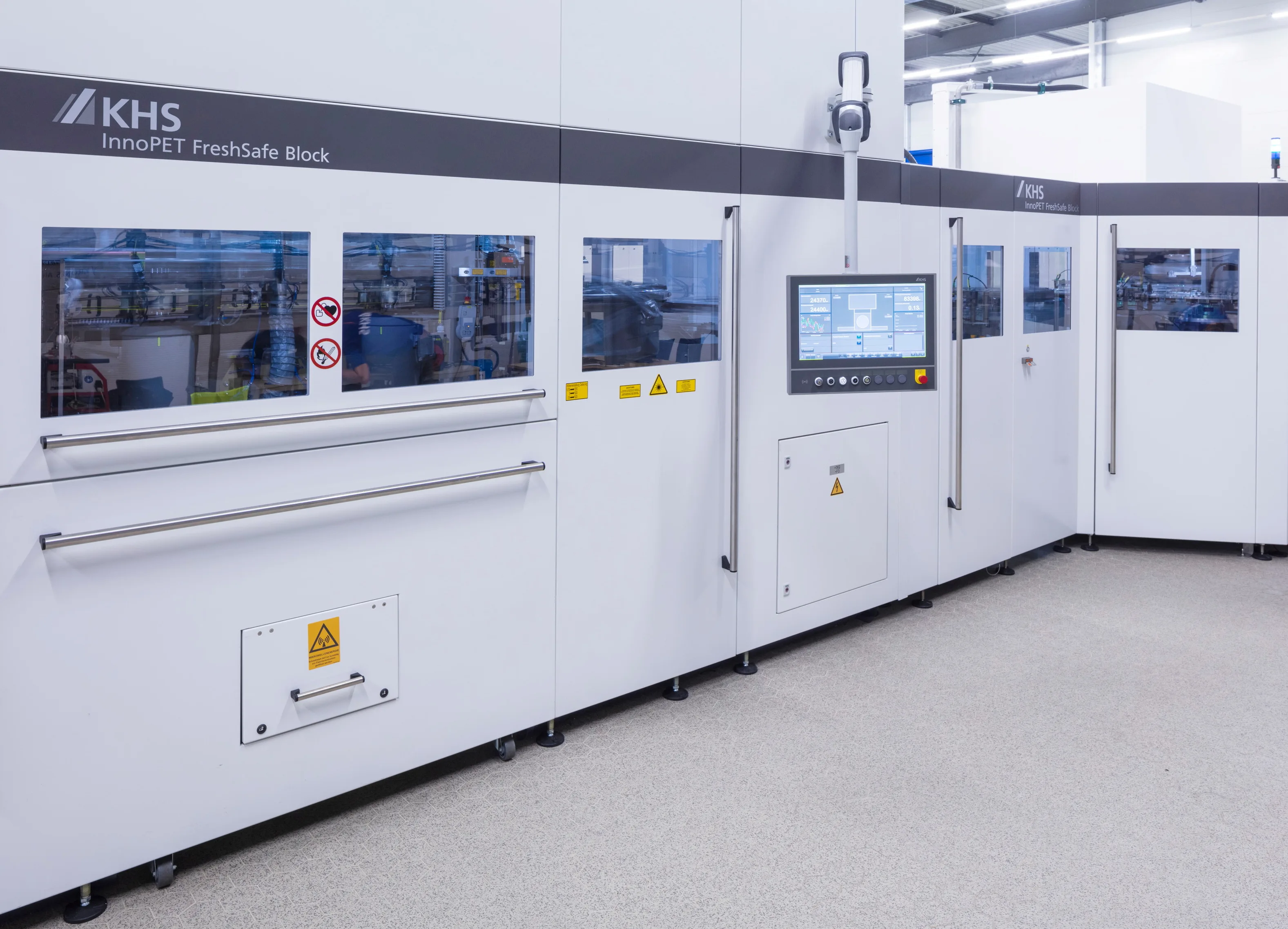
In operation at VILSA-BRUNNEN in Bruchhausen-Vilsen in Lower Saxony, Germany: the very first latest-generation Plasmax machine, an InnoPET Plasmax 80ER.
TCO-driven technology
Another feature in Plasmax’ favor is that after coating, no loose particles remain in the bottle. This renders the rinser, needed to wash out the containers on other systems, completely superfluous. In this respect, the KHS setup not only does away with an entire machine but also saves on resources such as air and water.
“Besides the higher output, this is another example of how we’re adopting a TCO-driven approach with our barrier protection technology,” smiles Langhammer. The total cost of ownership for the KHS barrier coater amounts to about only half of that for multilayer bottles that are more elaborate to produce and less easy to recycle.
Reduced complexity
“Longer service lives and maintenance intervals for valves, for example, also cut costs,” Langhammer explains. “We’re continuously investing to reduce the level of complexity. Among other things, this includes saving on wear parts such as seals. At the same time, we’re also working with one of our suppliers to develop pumps that can clean themselves and thus also have longer lifetimes.”
“With Plasmax, KHS is an enabler for small, cost-effective packaging formats that offer the best possible protection.”
![]()
Barrier technology product manager at KHS
Key benefit: long shelf lives
The total operating costs for beverage producers are of course extremely relevant, emphasizes Langhammer. “Besides the technology, what's key to our customers is that this generates a completely new form of packaging: here, KHS is an enabler for small, cost-effective packaging formats that offer the best possible protection.” These formats are especially critical because of their surface/volume ratio: a soft drink in a 200-milliliter bottle without any coating whatsoever would keep for less than a month. Special markets with hot, dry summers and seasonal peaks in demand could then barely be supplied.
“In contrast, depending on specifications we can now achieve shelf lives of six months with our barrier technology. This allows bottlers to pre-produce sufficiently large quantities of warehouse stock in advance and ship these to the regions where they’re needed in time. First, this saves extra shifts having to be worked during the high season. Second, thanks to the storage option, approximately 30% more beverages can be produced on a KHS line than on a standard PET line without coating.”
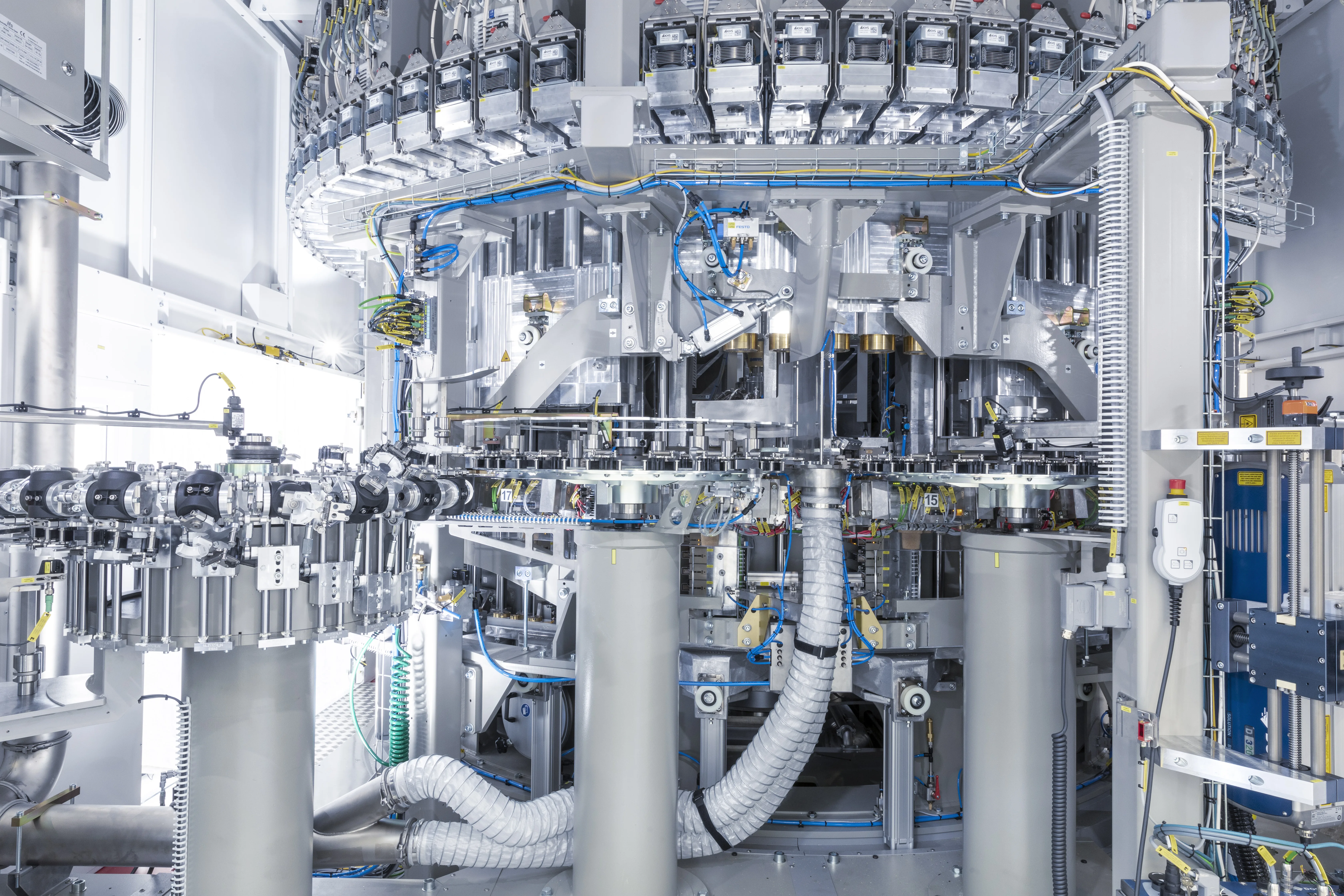
After being coated in the Plasmax module, the bottles are rotated in a turning unit before traveling on to the filler.
All-rounder
On the one hand, the universal barrier chiefly provides passive protection to carbonated soft drinks and water against the loss of CO2. On the other, oxygen pickup in bottles of sensitive beverages such as fruit juice, energy drinks, teas, wine and beer is prevented so that product quality doesn’t suffer.
Competitors provide what are known as scavengers for active protection. These are additives that are evenly distributed in the plastic as barrier protection. Scavenger bottles are now easier to recycle than multilayer containers. “However, we’re noticing that these additives don’t mix well with recyclate,” states Langhammer. “This is a restriction Plasmax doesn't have. FreshSafe PET containers can be bottle-to-bottle recycled and made entirely from rPET. This is why we refer to this as completely circular barrier technology.”
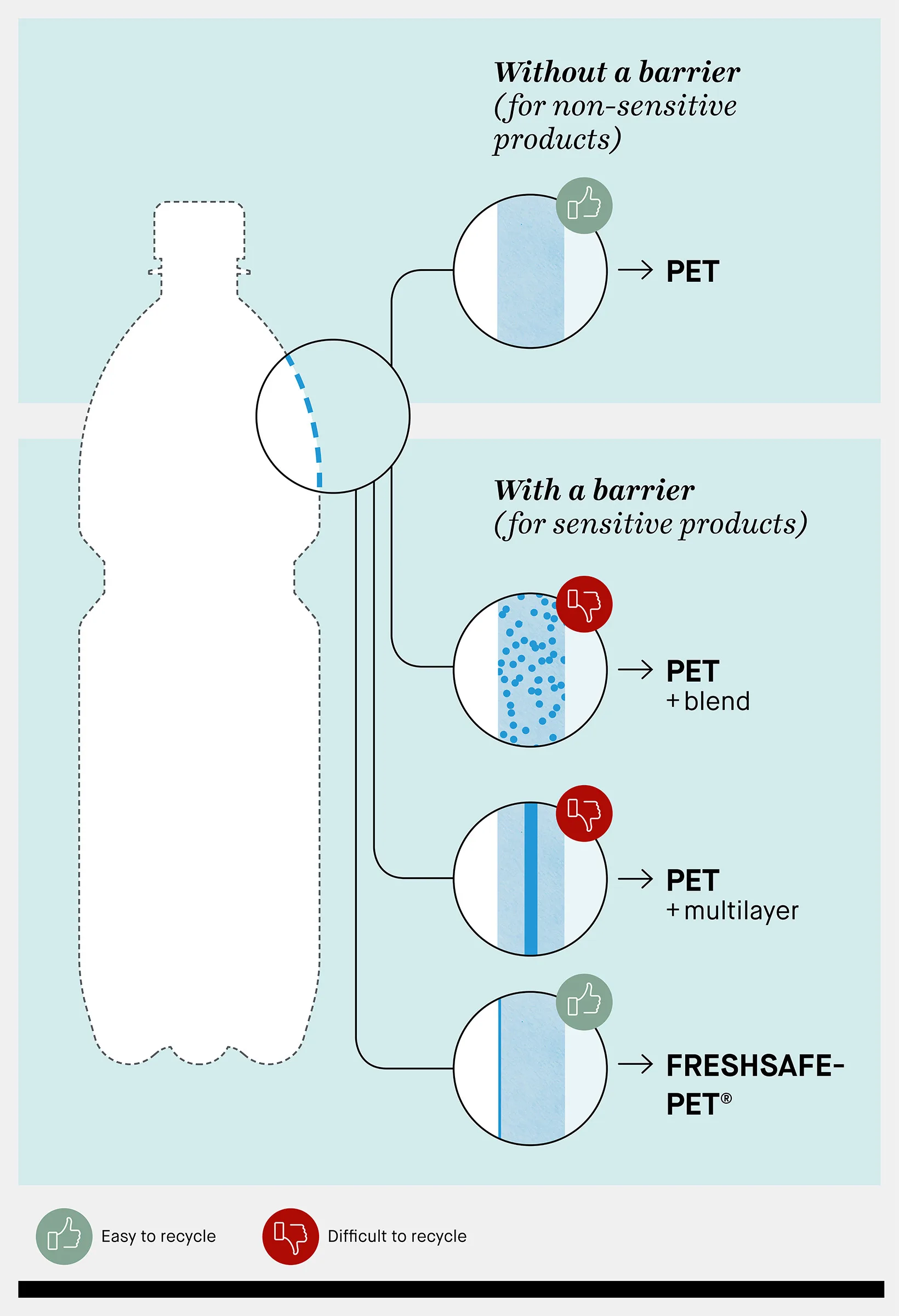
Recyclability – One-way PET bottles: PET bottles without a barrier coating (for non-sensitive products) produce 100% pure PET in the recycling process. In plastic bottles with barrier protection (for sensitive products) the additives are practically inseparable from the PET – except with FreshSafe PET®. Here, the protective layer is simply washed off during the recycling process.
Full portfolio integration
Parallel to its increase in output, the KHS technology has chiefly developed further regarding its block and line compatibility. “With our InnoPET FreshSafe block, we’re now fully integrated into the entire portfolio,” Langhammer confirms. “Plasmax either comes blocked with our stretch blow molder to form an InnoPET FreshSafe Block or is available as an InnoPET FreshSafe TriBlock with an additional integrated filler.”
To meet the fast-growing demand for its proven barrier technology, the Dortmund systems provider has successively increased capacity, reduced construction periods and optimized material flow. This ensures that even more coating machines and FreshSafe blocks can be built each year. “After all, we don’t want anything to stand in the way of our continuing success story,” Langhammer concludes.