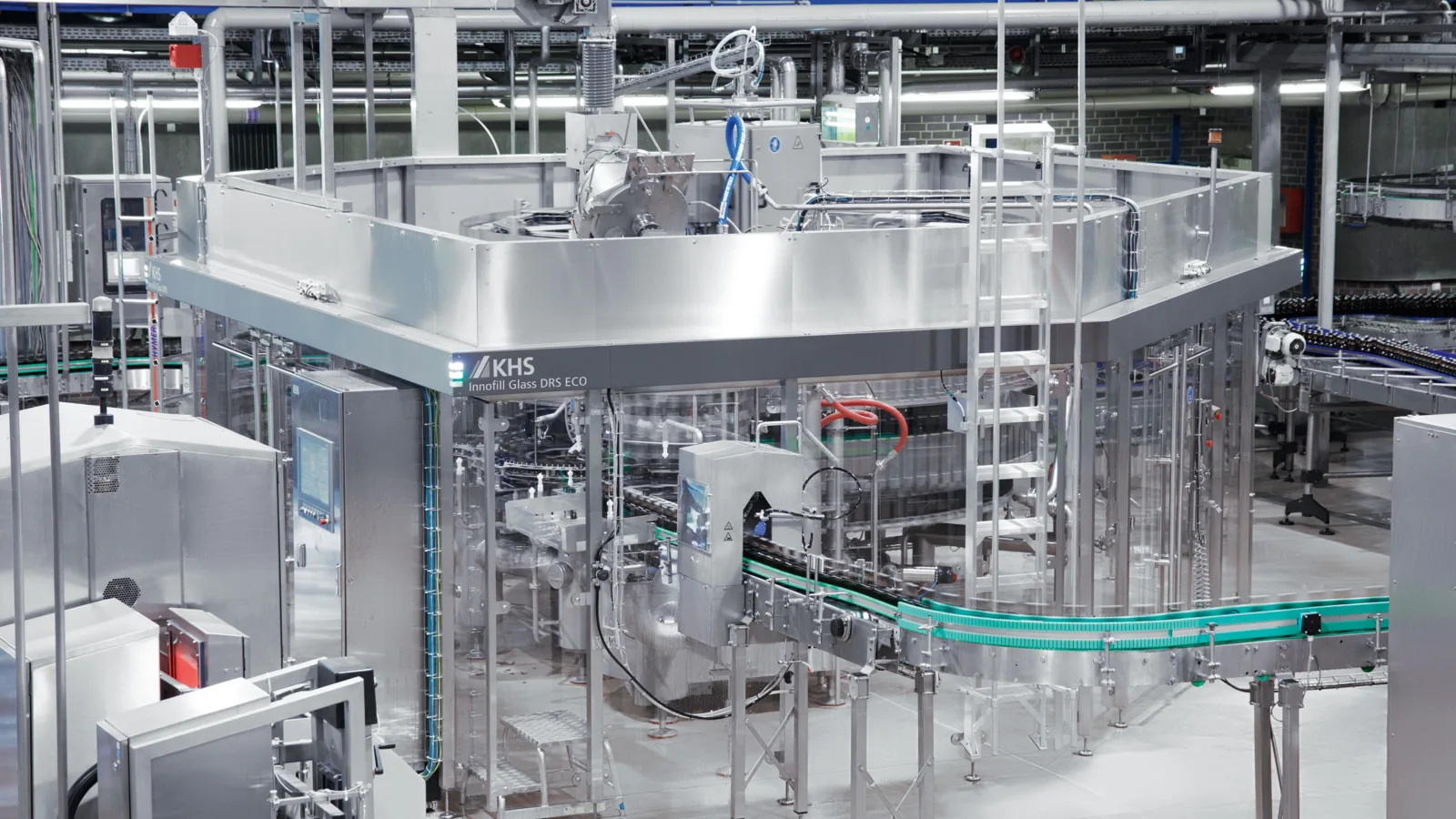
Low-oxygen zone
The new Innofill Glass DRS ECO from KHS lets less oxygen into beer – and in doing so needs less and not more CO2 than its predecessor. With it, even seasoned brewers are now discovering the taste of their products anew.
First presented as a prototype at the last BrauBeviale to date in November 2019, the new modular Innofill Glass DRS ECO filler from KHS has long established itself in practice. The first example of its kind has been up and running at OeTTINGER Brewery in Mönchengladbach, Germany, since the middle of 2021 and has technical plant manager Jürgen Brunacker totally enthused. “The new KHS filler enables such low-oxygen filling that there’s no detrimental effect on our product whatsoever. There’s never been anything like it in this form before.”
One reason for his satisfaction is undoubtedly KHS’ unique ECO system, a special evacuation and CO2 purging process for glass bottles. Here, during pre-evacuation air – and thus oxygen – is first removed by vacuum from the containers that are then purged with a precisely dosed amount of CO2. As opposed to the conventional methods common in the past that require double purging with the gas, the optimized KHS process is highly effective. It permits filling in an almost pure CO2 atmosphere so that the beer picks up practically no more oxygen. This is further supported by the second stage in the process: high-pressure injection immediately before the bottles are capped. The procedure causes foaming that displaces the tiny amount of remaining air from the bottle neck and under the domed crown cork. In order to achieve an excellent result, it’s essential that both steps are well coordinated with one another, explains Jonathan Lorenz, head of Filling Technology Development at KHS. “If a lot of oxygen already enters the beer at the filling stage, subsequently the foaming result is poor,” he says knowledgeably. “All told, oxygen pickup as low as this on our further developed filling machine only used to be possible with a huge CO2 consumption.”
»Oxygen pickup as low as this only used to be possible with a huge CO₂ consumption.«
![]()
Head of Filling Technology Development, KHS
You can find more information on our efficient Innofill Glass DRS glass bottle filler and the various available options on khs.com
Beer’s natural enemy
Oxygen causes beer to oxidize and is thus the natural enemy of beer and brewers. On the one hand, the gas limits the beverage’s shelf life, and on the other, it spoils its taste. How much of it is allowed to be in the bottle depends on various factors. Firstly, the beer’s ultimate destination plays a role here, as does the period within which it’s to be drunk; secondly, there’s the question of how much store is set by quality and taste. Products destined for export, for example, make higher demands of the shelf life than those that are to be consumed within a short space of time at a big public fair.
“The less oxygen I want in the bottle, the more CO2 I have to use,” Lorenz emphasizes. “In some brands this calls for 1,600 grams of CO2 to be used per hectoliter in order to achieve an oxygen pickup of 40 ppb* – a costly luxury. By way of comparison, in Germany values of between 80 and 200 ppb are considered normal.”
* ppb = parts per billion. 1 ppb is the equivalent of 1 µg per kilogram, for example.
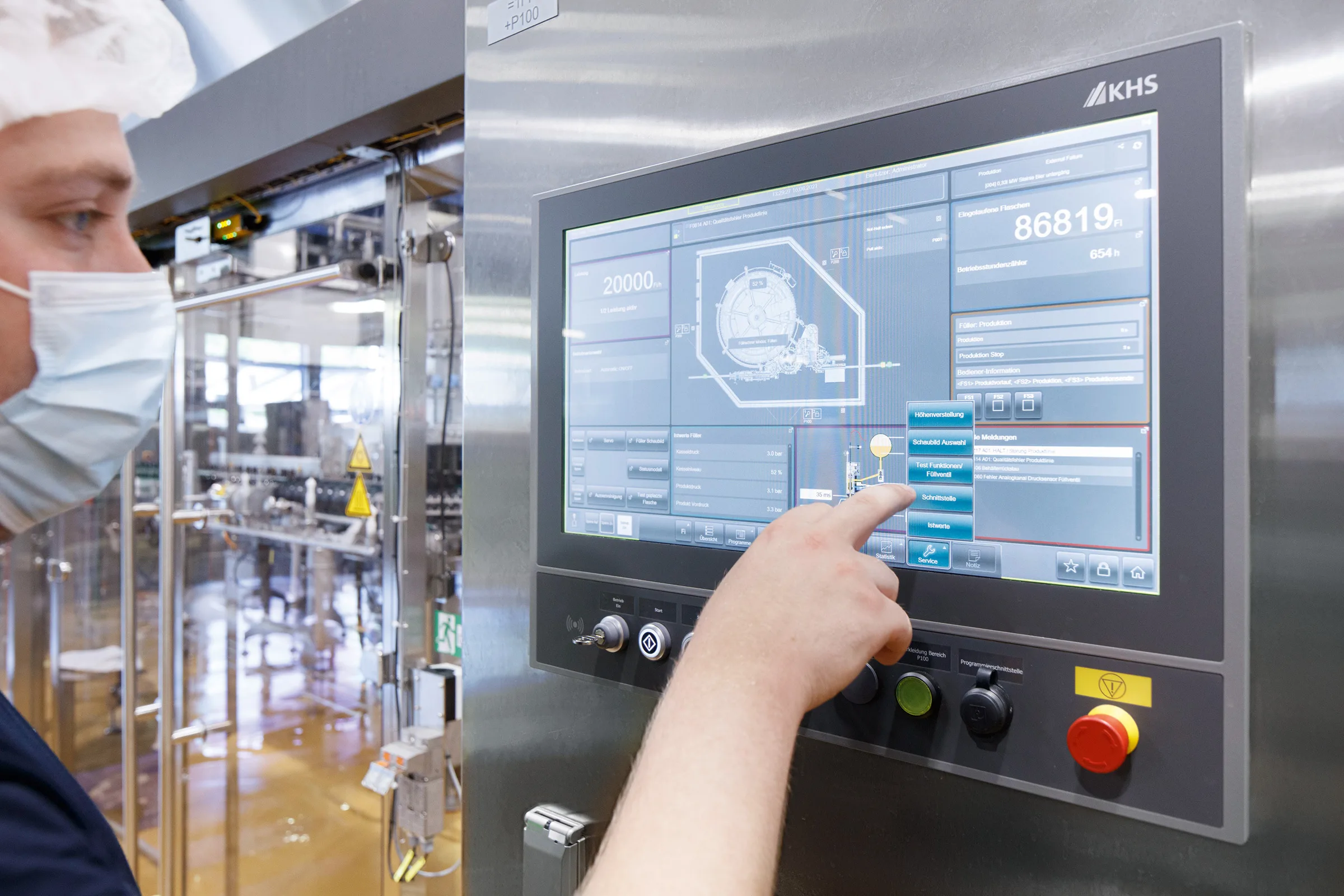
The low oxygen pickup in the beer can be regulated by the amount of CO₂ used.
Sensationally low O2 levels
Brunacker confirms that CO2 is an expensive commodity. “The less used per filled bottle, the more effective my brewing process. Lower oxygen pickup means better product quality – but this calls for more CO2 and thus results in higher costs. On the new KHS filler these two points are in perfect harmony.” And the experienced brewer knows what he’s talking about. OeTTINGER Brewery has been a second home to him since he was a little boy, as the headquarters in Oettingen in Bavaria were where his father also worked as a master brewer for many decades. For a very low oxygen pickup of 40 ppb, for instance, the Innofill Glass DRS ECO only needs 110 grams of carbon dioxide per hectoliter of beverage – and at 160 grams the O2 content drops to a sensationally low 20 ppb. “Achieving these values is a real quantum leap,” smiles Jonathan Lorenz, equally pleased with the result.
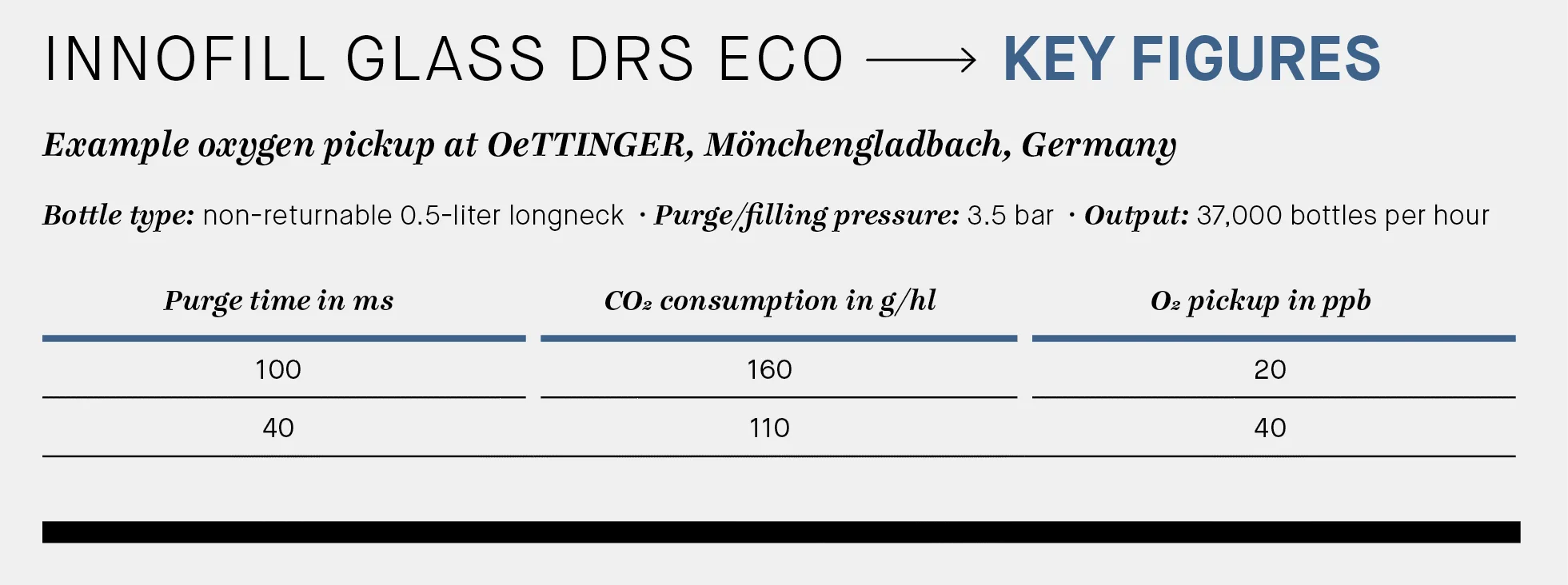
The exceptionally low oxygen pickup and savings of up to 60% in CO2 are not the only reasons why Brunacker and his colleagues are excited about their new filler. The Innofill Glass DRS ECO also has a number of other features that set it apart from the competition. One is the optional DIAS diagnostic assistance system that globally monitors all filling stations. This makes for additional safety and quality in the filling process, enabling faster troubleshooting and immediate response to broken bottles. This is further aided by a unique broken glass protection system that perfectly isolates any splinters of flying glass. “We not only benefit from DIAS when filling but also during cleaning,” Brunacker accentuates. “The system is extremely reliable!” In addition to continuous media monitoring during the cleaning process, he also likes the summary of his operational data and consumption values. “This allows me to immediately see if there any problems. I can set the machine so that it always runs at the same capacity with a constant media consumption or can specify alarm thresholds. These are huge advantages over a mechanical filler.”
Another option OeTTINGER went for is OPTICAM, a camera-assisted foaming control system. It registers even the tiniest deviations in the process and enables high-pressure injection to be adjusted fully automatically without the quality of the filling results being dependent on the operator’s current form or level of concentration. Automatic, infinitely variable height adjustment of the fill level probes ensures even foaming and – most importantly – extremely precise fill levels. By regulating the injection pressure, for instance, operators can define that there’s just one millimeter of product loss per bottle and not the previous two. This not only reduces the amount of beer loss, as Brunacker states. “After filling the bottle has to be rinsed off with water. The less beer foam it has, the easier it is to remove any product residue.”
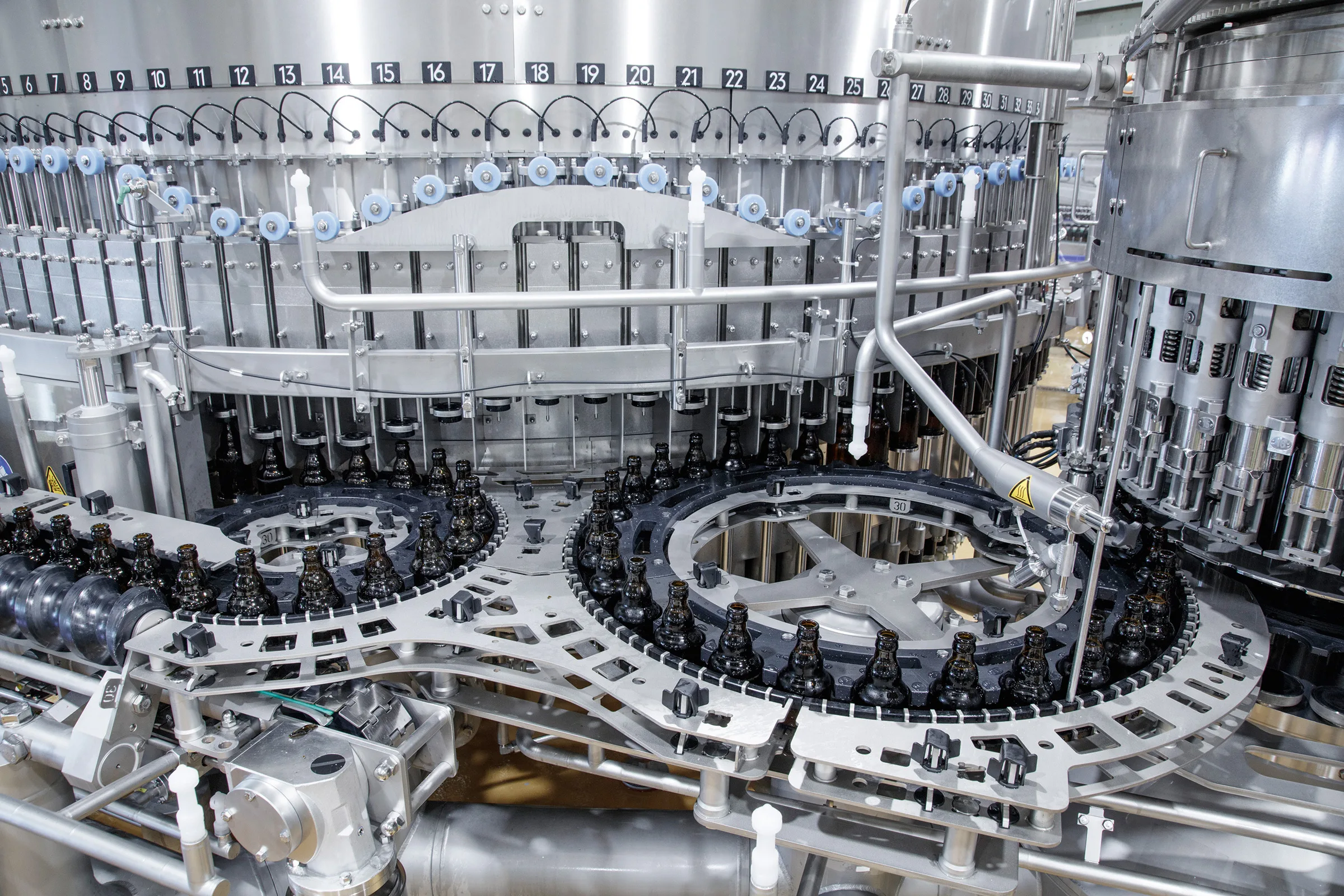
The new KHS glass filler has a number of features that set it apart from previous systems – from its innovative diagnostic system to the automatic CIP caps.
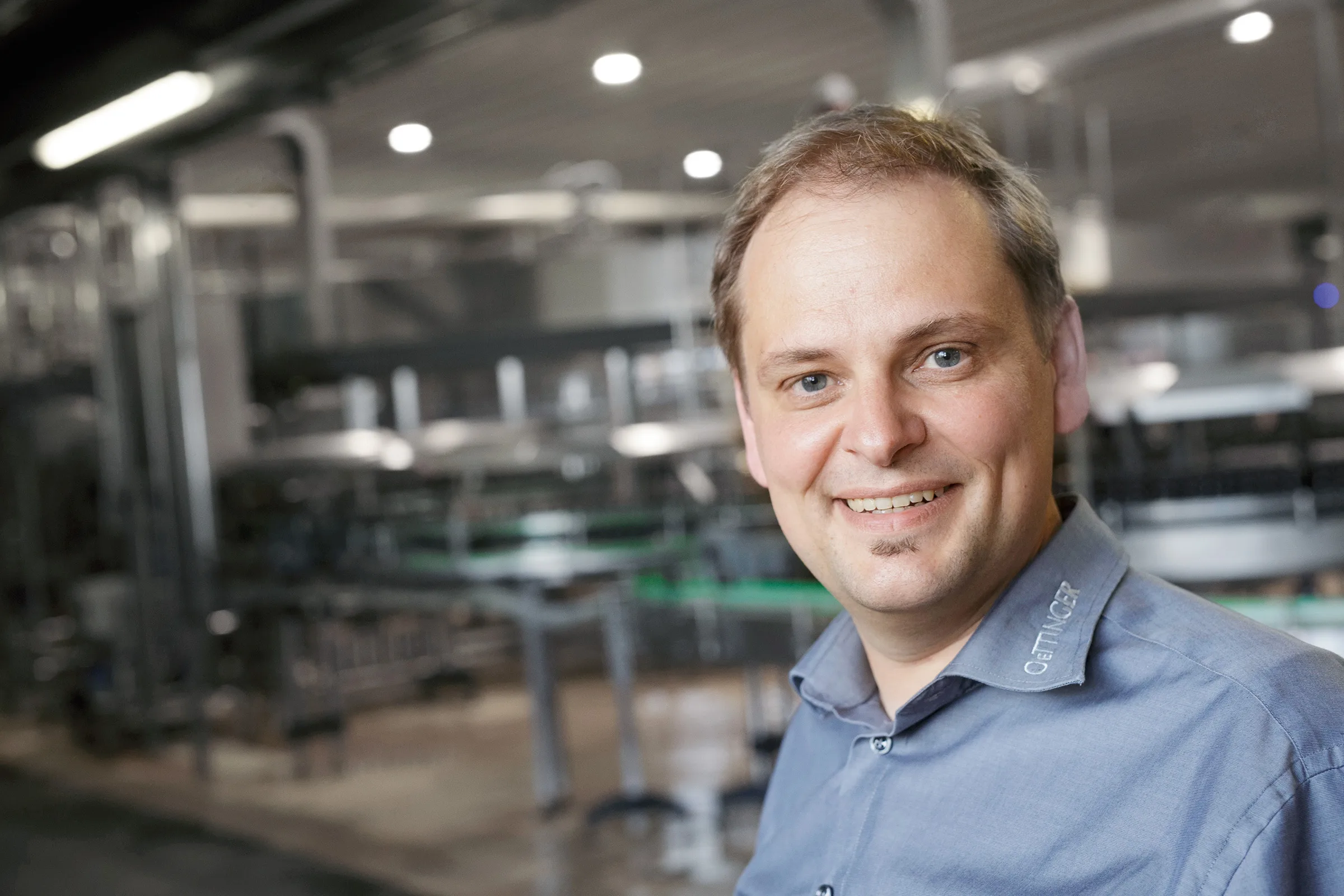
Jürgen Brunacker, technical plant manager for OeTTINGER in Mönchengladbach, Germany, is more than pleased with the low oxygen pickup and resulting good taste of his beer.
Quick and hygienic
Finally, Brunacker also finds the automatically activatable rinsing sleeves very practical. “We save an enormous amount of time as we no longer have to attach the cleaning caps by hand. And unlike on previous systems, where the CIP caps were hidden behind the filling element yet still came into contact with the product, KHS has now arranged these behind the carousel cladding. This means that they no longer have any contact with the filling process and are better protected. The entire construction is extremely compact,” he concludes happily.
Not only the technical plant manager is pleased. His colleagues in Mönchengladbach familiarized themselves with the new technology in a very short time indeed, he tells us. There was no ramp-up after commissioning. From day one of production the filler was operated at a capacity of 40,000 bottles per hour. Even during the night shifts the operators at OeTTINGER were able to run production without any KHS engineers having to be present. This had him completely enthralled – like so many other aspects of the Innofill Glass DRS ECO.