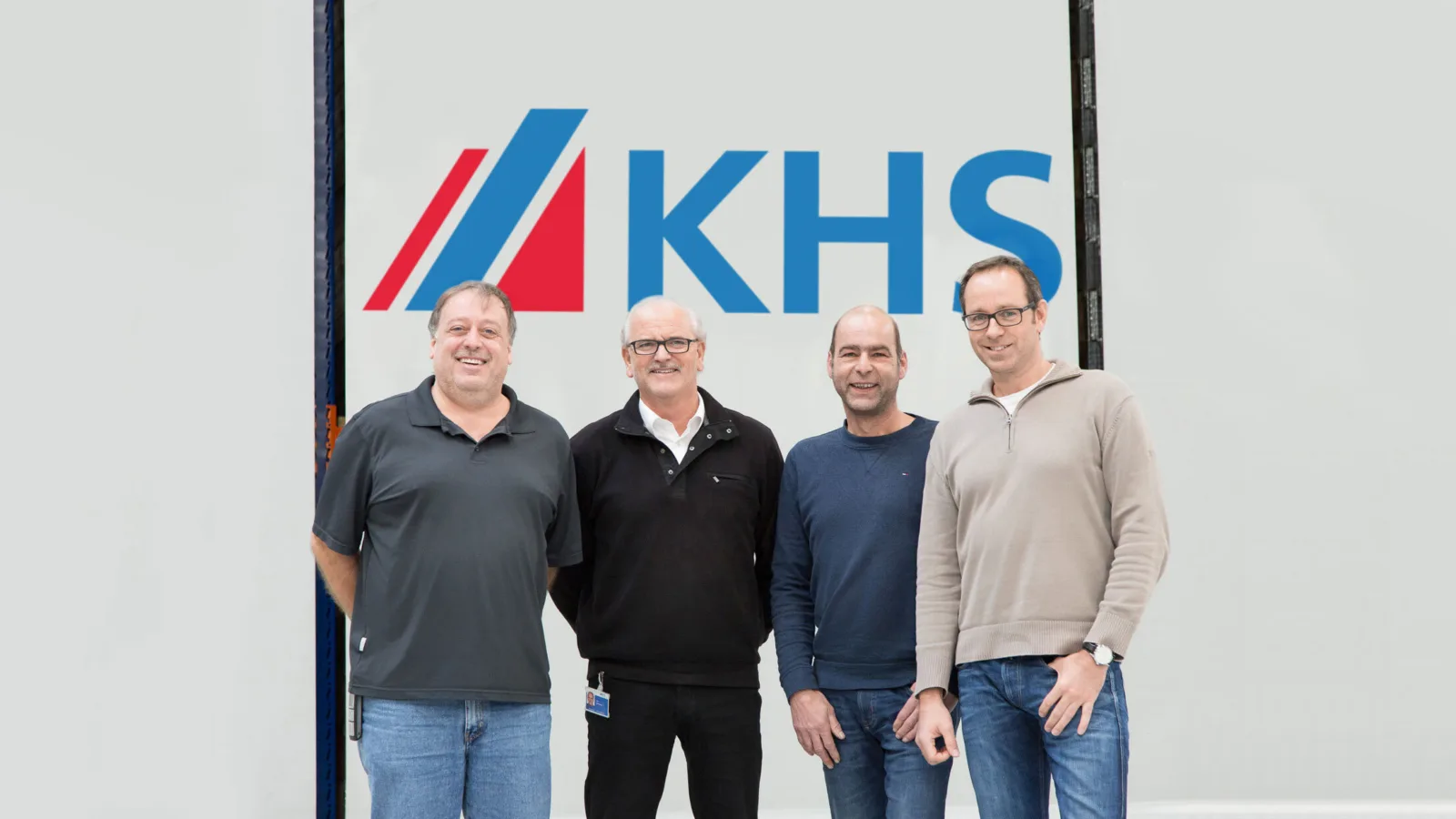
Notes from the Isles
Replacing control units and drives can considerably lengthen the service life of lines and systems.
One example from Great Britain shows just how great a role the conversion specialists from KHS play – with the help of their English service colleagues in the British Isles.
Machine control units from manufacturers such as Allen-Bradley and Siemens undergo constant further development. This presents system users with a huge challenge as they endeavor to always keep up to date. At the latest when the controllers of a machine are no longer supported by the manufacturer after ten or more years and spare parts are no longer available, it’s high time for a conversion. Situations like these are diligently monitored by the service engineers from KHS. As part of KHS’ comprehensive consultancy service they assume responsibility for their customers in this respect, specifically informing clients during normal maintenance intervals as to when replacement equipment is necessary and prudent.
This was recently the case at Premier Foods, for instance, one of Britain’s biggest food producers. At its production site in Worksop in the British Midlands, where Bisto gravy granules are made and packaged, among other products, in the past year two KHS Kisters tray shrink packers, both about 15 years old, have been equipped with new Allen-Bradley Kinetix drives including servomotors. In principle this type of conversion is routine. However, in this case it was the first time that the KHS engineers had to integrate a Kinetix 5700 controller, the latest generation of Rockwell drives, into existing plant technology.
Step-by-step overhaul
The previous device was replaced by an RSLogix 5000 controller with an L82E processor. Besides replacing the controller the conversion naturally came with a new control panel and a newly installed 15-inch KHS ClearLine HMI operator panel: an energy-efficient industrial PC with a touchscreen and RFID access control. The overhaul also included replacement of all existing servomotors with Kinetix VPL motors and the appropriate gears.
Uwe Bartholemy, head of Technical Support for Spare Parts and Conversions at the KHS Service Division in Kleve, gives us more details about the project. “Before submitting our offer to Premier Foods, which also contained the electrotechnical specifications, we had a good look at the machines in question on site in Worksop.” KHS engineer Wilhelm Schnatz examined the mechanical equipment, with KHS electromechanical engineer Heinz-Dieter Heek responsible for the electrical equipment. Both then checked and clarified the details in the offer and schedule. They were assisted by their English colleagues who together with them recorded the current state of the machines prior to conversion. As in many other cases, the engineers noted that the machines were no longer in their original state. “Here, the customer had installed a monitor in the control cabinet to oversee the line,” Heek remembers. “In this case we agreed that the assemblies added by the customer in the interim would have to be reinstalled by the customer once we’d finished the conversion.”
Proximity to the customer
Service in Britain: KHS’ British service center at the KHS production site in Solihull near Birmingham employs 13 service engineers, seven of whom are electronics engineers. The team caters for the entire KHS portfolio and is headed by Alan Watt who has been with the company for 24 years. Among the tasks his department performs are modifications and conversions. Watt attaches great importance to the basic and further training of his engineers, most of which is carried out in Germany; at the time of writing, for example, two Solihull engineers are being specially schooled to work with Allen-Bradley control systems. The service team enjoys close, long-standing relations with customers both large and small, the two biggest clients being Coca-Cola European Partners (CCEP) GB and Britvic, Great Britain’s bottler of Pepsi products. Britvic is currently benefiting from the services of an embedded engineer during the commissioning of its three new canning lines.
Thoroughly tested
After the contract had been awarded, the new control cabinets and control panels were built at the KHS factory in Dortmund, with the plant in Kleve simultaneously working on the software. As soon as the hardware had been delivered to Kleve, the machine was assembled and commissioned at the factory to thoroughly test all of its functions, such as the emergency stop circuit, safety doors, power connection, individual drives and tunnel and dancer controllers. “Once everything’s working properly, the main job really starts,” states Bartholemy, the man responsible for conversions at KHS in Kleve, and lists the many tasks his colleagues had to complete once on site at Premier Foods. “The control cabinet on the existing system first had to be disconnected and all redundant cables removed. The new control cabinet was then brought in and the safety switches installed by the customer and all other conversion parts checked. The next step was to lay the cables for the servos and safety circuit. We then dismantled the mechanical parts before placing the new control cabinet in position and connecting it up. Finally, the new motors, gears and pneumatic equipment were installed before the system was checked and commissioned.”
“Our British service engineers receive most of their basic and further training in Germany.”
![]()
Service Manager, KHS UK
Having an engineer – in this case Karl Janssen – support the conversion process at the customer’s site is only necessary when new technology is used for the first time. The aim is to quickly enable local service personnel to carry out conversions themselves. “We already had English service engineers working with us on our second visit,” explains Bartholemy. “On our third visit our English colleagues were so well versed in the process that they could do much of the work themselves – or at least knew exactly who was best qualified for the job.”
For the service engineers from Kleve converting the controllers on existing lines is routine. Bartholemy and his colleagues have done this about 200 times, he estimates, at locations all over the world. “We have branch offices in the USA, Australia, Brazil and Spain,” he says. The manufacturers of the drives make sure that he and his team are never out of work. “Both Siemens and Allen-Bradley launch completely new systems to market every eight to ten years. Spare parts are then perhaps available for the old ones for a period of about ten years or so but then the components are discontinued. If a control system then fails, the line user has a problem. This is why we proactively offer conversions.”
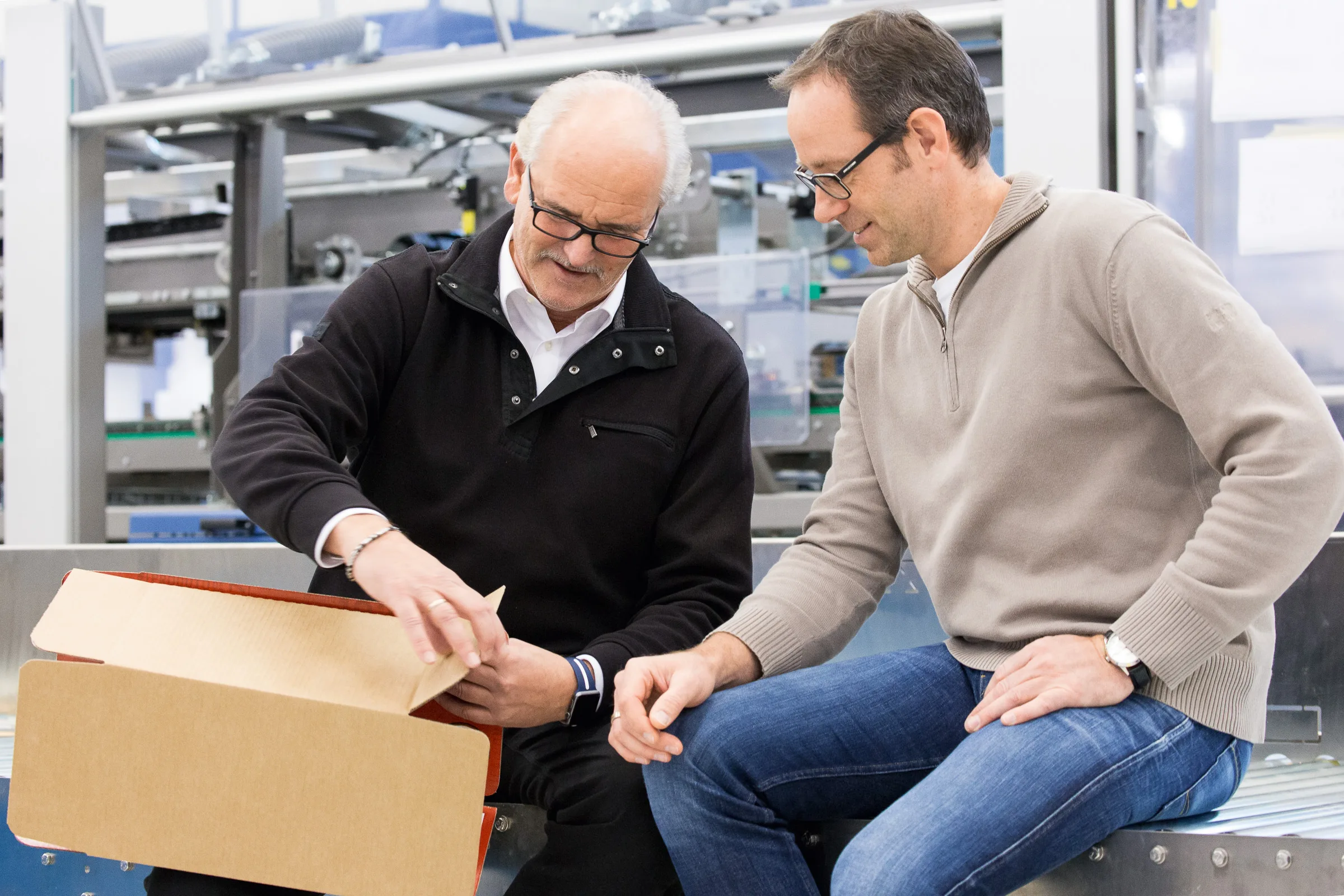
Once everything has been thoroughly tested in Kleve, the machinery is dismantled, packed up and set off to its destination in Worksop in the United Kingdom.
After just a short time Premier Foods was able to resume production. In the meantime a few formats were further optimized and all remaining work completed, meaning that the company now benefits from the current industrial standard, uncomplicated procurement of spare parts and simpler operation. And not just that – the machines have already been made fit for future requirements; the converted lines have been prepared for connection to the KHS ReDiS remote diagnostics system and new functions can be added to the control unit and servotechnology in the future with very little effort indeed.