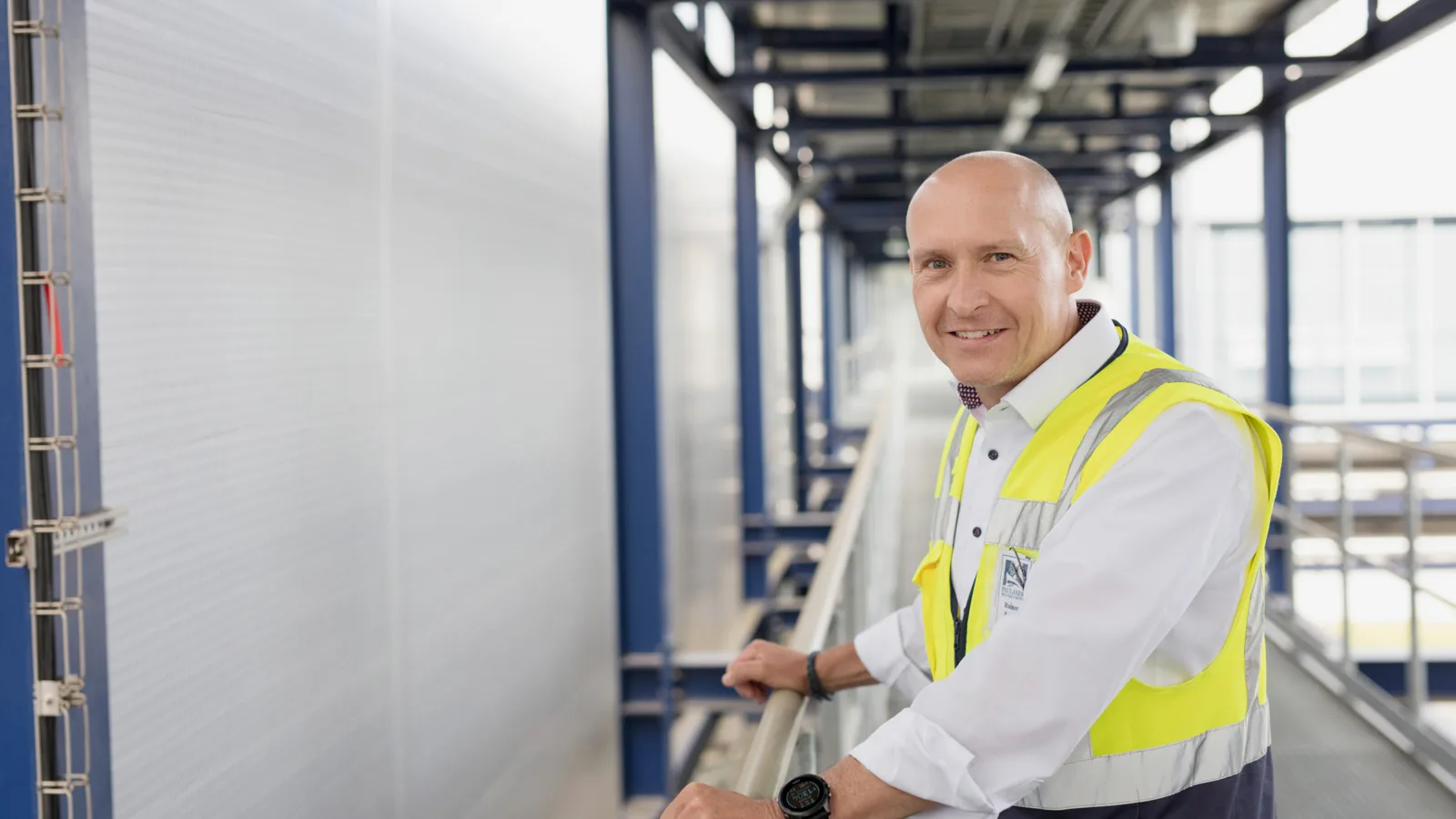
Gut gerüstet für die Zukunft
Mit modularen Servicepaketen und individuellen Vereinbarungen – wie mit der Paulaner Brauerei in München-Langwied – sorgt KHS dafür, dass seine Linien bei Getränkeabfüllern reibungslos und effizient laufen. Das vermeidet ungeplante Betriebsausfälle und unkalkulierbare Folgekosten.
Ziel eines jeden Getränkeherstellers ist es, seine Produktionslinie maximal effizient zu betreiben. Dafür muss das Equipment reibungslos und zuverlässig laufen. Ungeplante Maschinenstopps, die zu Unterbrechungen im Abfüllprozess führen, sollen idealerweise verhindert werden, um potenzielle Folgekosten und -schäden zu vermeiden. Denn ein Produktionsausfall wirkt sich negativ auf die Gesamtleistung aus, treibt die Verbrauchswerte in die Höhe, senkt die Ressourceneffizienz und schmälert den Gewinn.
Um dem entgegenzuwirken, müssen Linien regelmäßig und im besten Fall vorausschauend gewartet werden. „Im Vergleich zu einem konventionellen, reaktiven Service, der erst bei konkreten Ausfällen auf den Plan tritt, kann die Produktivität mit präventivem Service um bis zu vier Prozent gesteigert werden“, erklärt Miriam Seilkopf, die bei KHS das Thema Serviceverträge verantwortet.
Für die unterschiedlichen Bedürfnisse seiner Kunden bietet der Dortmunder Systemanbieter verschiedene Servicemodule an, die zu Paketen konfiguriert werden können (siehe Grafik „Modular“). „Die einzelnen Bestandteile sind dabei individuell kombinierbar, sodass unsere Kunden genau von den Leistungen profitieren, die für sie relevant sind und gleichzeitig über maximale Kostentransparenz verfügen“, betont Seilkopf. Auch wenn grundsätzlich alle Kombinationen möglich sind, empfiehlt KHS die drei aufeinander aufbauenden Servicepakete Basic, Advanced und Comfort.
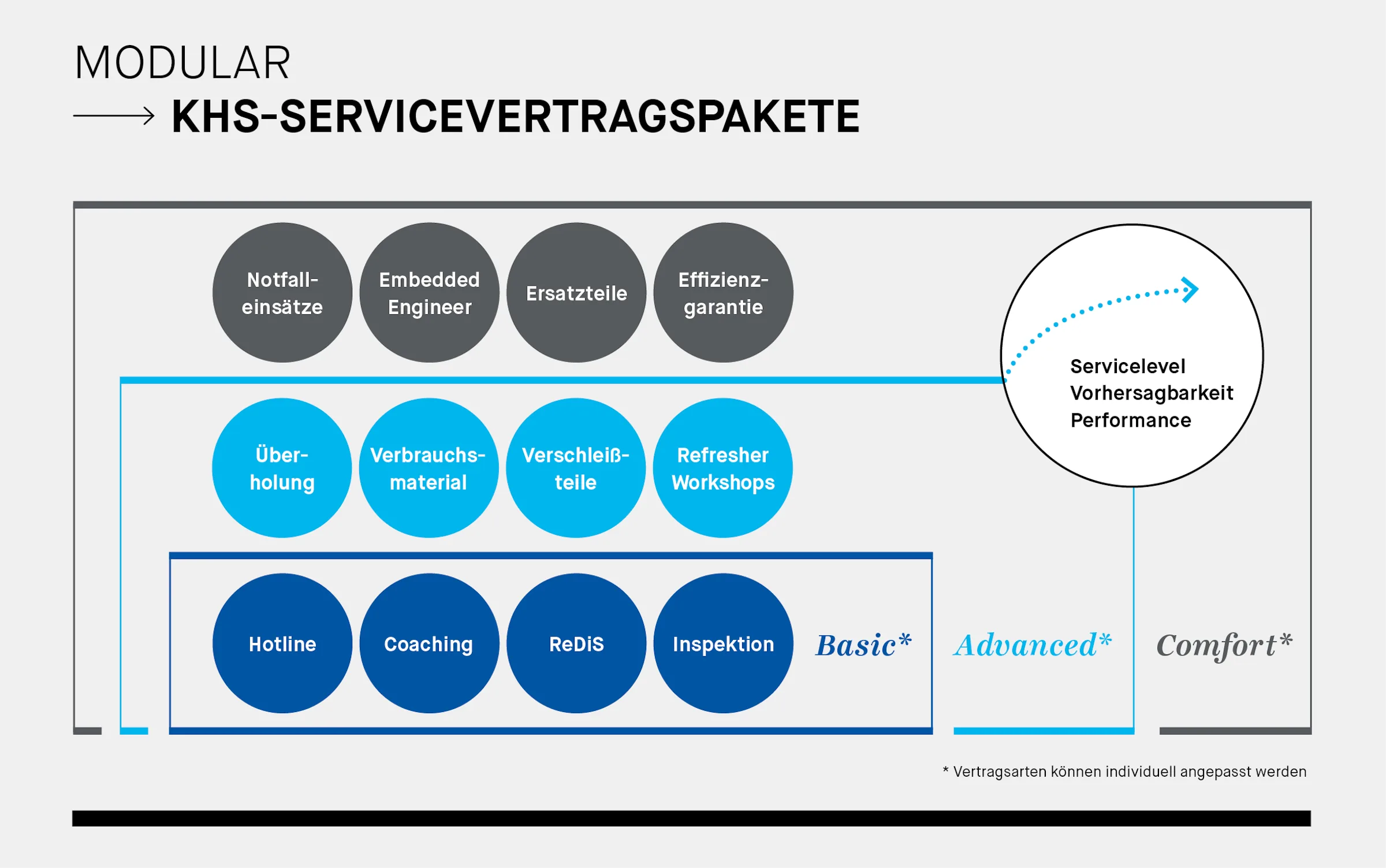
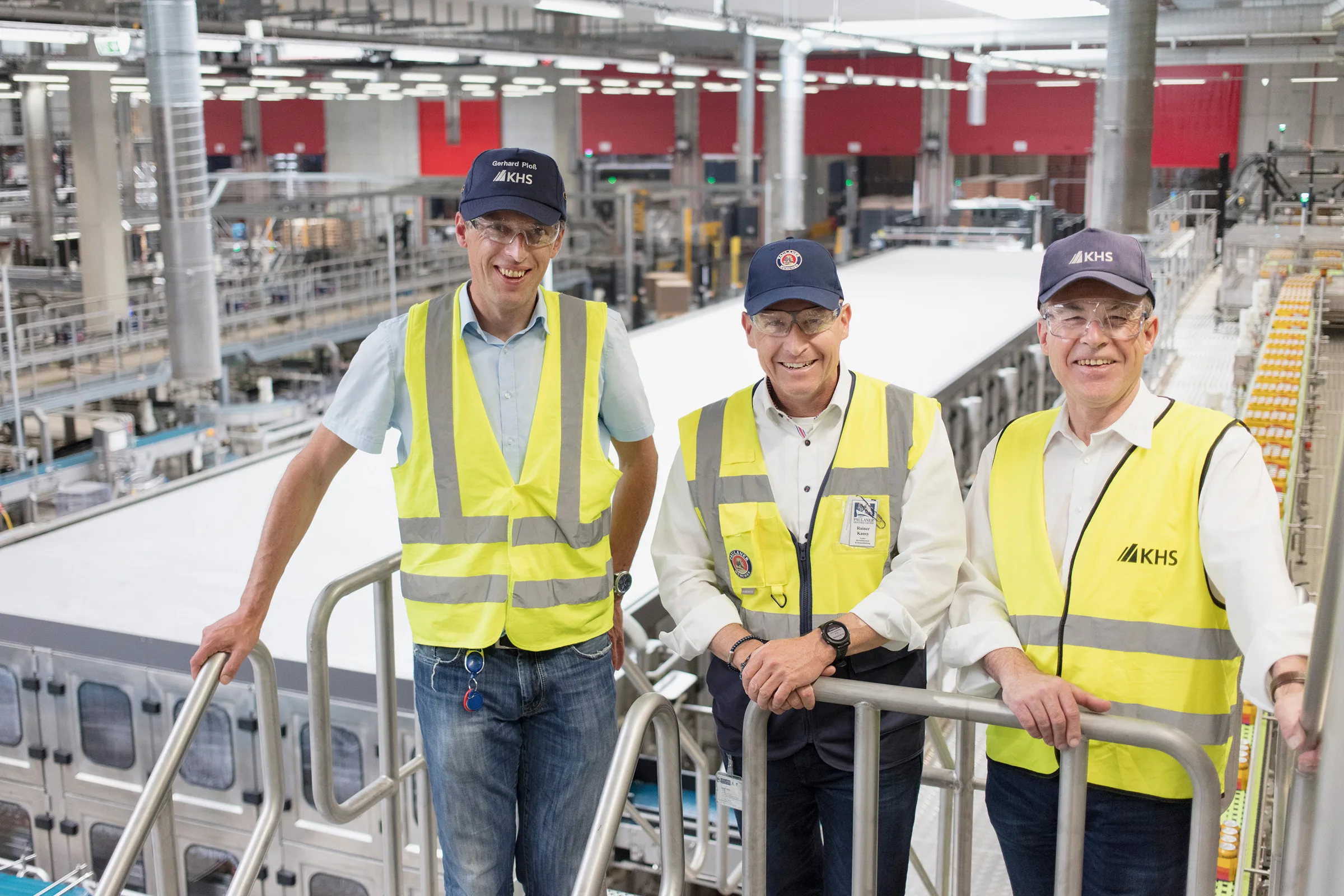
Direkter Draht, kurze Wege: Rainer Kansy (Mitte) mit Gerhard Ploß (links), KHS-Gebietsinspektor Bayern, und Jürgen Thielen, Head of Service bei KHS im Business Center Zentraleuropa.
Schnelle Abhilfe
Im Basic-Paket liegt der Fokus einerseits auf schneller Abhilfe im Bedarfsfall: Das 24/7-HelpDesk und ReDiS beispielsweise sind zwei Tools, die helfen, ungeplante Stillstände möglichst kurz zu halten. Über die Hotline etwa stehen rund um die Uhr Fachexperten für technischen Support und Fragen zu Ersatzteilen Rede und Antwort. Mit ihrer Expertise sorgen sie für unkomplizierte und möglichst sofortige Fehlerbehebung. Und ReDiS, der Remote Diagnostic Service von KHS, ermöglicht die schnelle und präzise Online-Problemerkennung mittels Maschinen- und Systemferndiagnosen. Zudem erlaubt er die Installation und Inbetriebnahme von Bauteilen, die Optimierung von Softwarekonfigurationen oder die Installation von Updates. Ein Beispiel für eher präventive Maßnahmen des Basic-Pakets sind Inspektionen: KHS-Servicetechniker erheben anhand maschinenspezifischer Checklisten den aktuellen Status von Maschinen und identifizieren frühzeitig die erforderlichen Verschleiß- und Ersatzteile. Liegt übermäßige Abnutzung vor, analysieren sie deren Ursachen und unterbreiten entsprechende Vorschläge für Anlagenoptimierungen. Für den bestmöglichen Anlagenbetrieb sorgt das Modul Coaching: Mittels Training on the Job wird sichergestellt, dass ein umfassender Know-how-Transfer von den KHS-Technikern zum Bedienerpersonal erfolgt.
Zum Advanced-Paket gehört zusätzlich zu den Inspektionen der Bereich Überholungen. Sie haben einerseits einen zustandsbezogenen Effekt, der im Austausch der Verschleißteile besteht, die bei der Inspektion erkannt wurden. Vorbeugend wirkt andererseits die Durchführung regelmäßiger Überholungsarbeiten. Im unmittelbaren Anschluss an diese Wartungsarbeiten erfolgt die Wiederinbetriebnahme der Anlage.
Ergänzend zum Coaching-Modul des Basic-Pakets können in einem Refresher-Workshop Schulungsinhalte wiederholt sowie auf den Bedarf des Kunden abgestimmt gemeinsam Prozesse optimiert oder Fehleranalysen durchgeführt werden.
Über die eigentlichen Austauscharbeiten im Rahmen der Überholung hinaus kann das Advanced-Paket die Verschleißteile selbst sowie Verbrauchsmaterial enthalten. Erstere werden je nach Betriebsstunden und aktuellem Zustand der Maschine pünktlich geliefert.
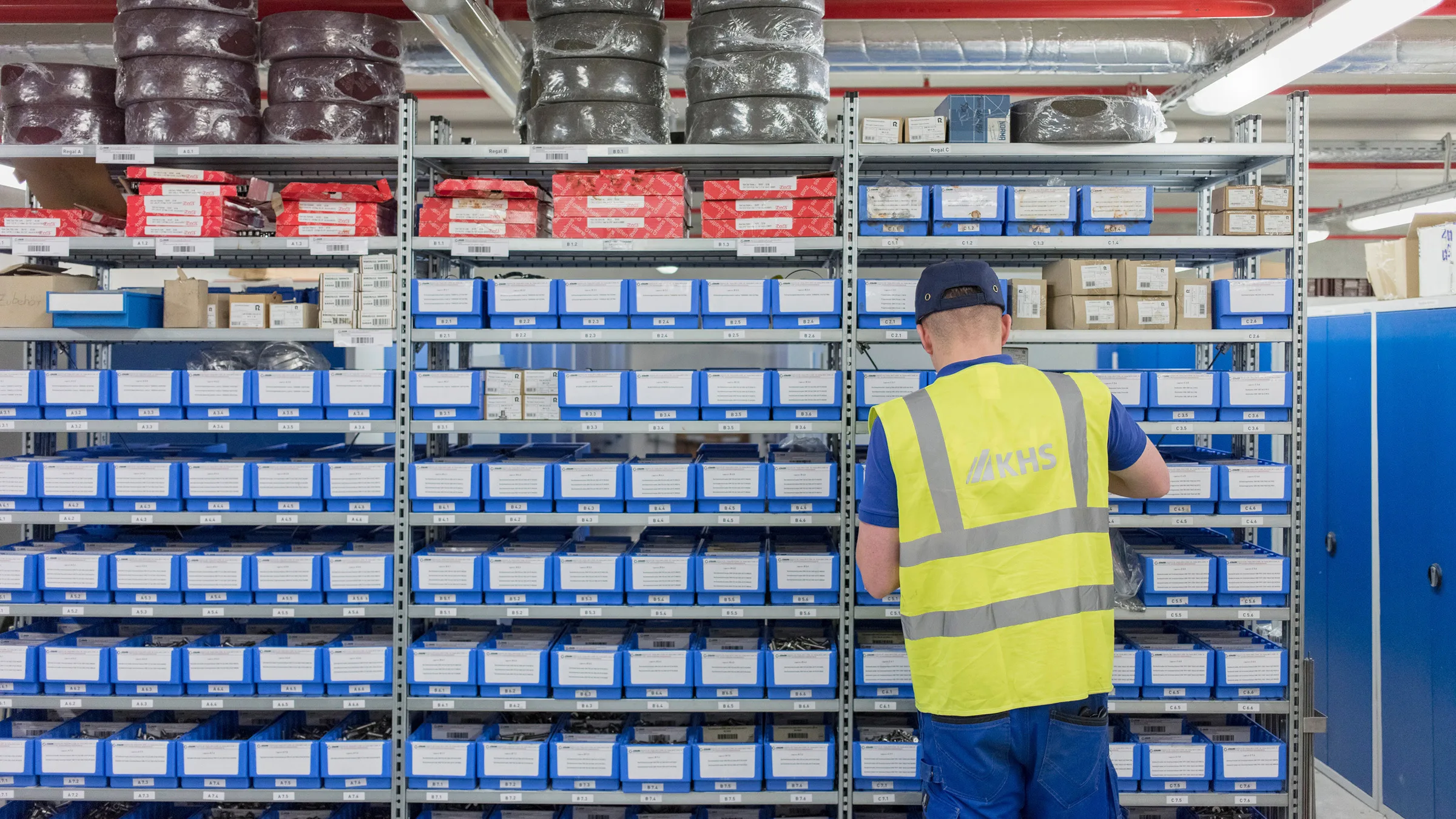
Zu den Schlüsselvoraussetzungen für minimale Ausfallzeiten gehört, dass möglichst alle kritischen Ersatzteile vor Ort sind.
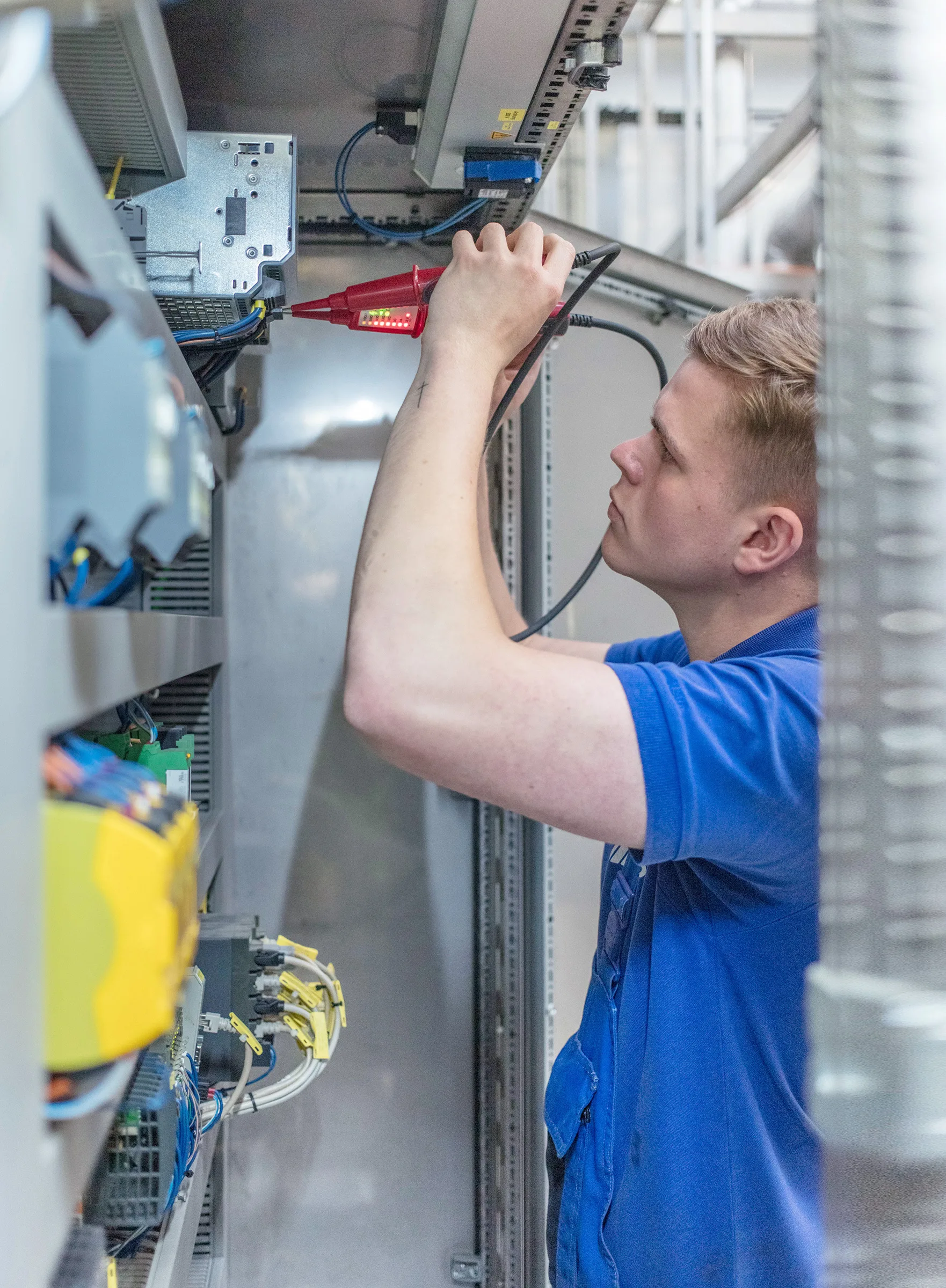
KHS-Servicetechniker wie Konstantin Snytko überprüfen vor Ort den aktuellen Status der Maschinen und identifizieren die erforderlichen Verschleiß- und Ersatzteile.
Bestmögliche Performance
Mit dem höchsten Servicelevel des Comfort-Pakets schließlich sichern sich Getränkehersteller nachhaltige Maschinen- oder Linieneffizienz, bestmögliche Performance und Vorhersagbarkeit. Dafür sorgen etwa Embedded Engineers, erfahrene KHS-Techniker, die für die gesamte Vertragsdauer permanent beim Kunden vor Ort im Einsatz sind. Neben der Übernahme zeit- und zustandsorientierter Instandhaltung machen sie Verbesserungsvorschläge für die täglichen Wartungsarbeiten und Formatänderungen, unterstützen das Bedienpersonal bei der Fehleranalyse und -beseitigung oder zeigen Optimierungspotenziale im Betriebsalltag auf. Eine der Schlüsselvoraussetzungen für minimale Ausfallzeiten ist die maximale Verfügbarkeit von Ersatzteilen: Das Modul Empfohlene Ersatzteillisten (RSPL) stellt auf der Basis der jahrzehntelangen Erfahrung von KHS sicher, dass alle kritischen Ersatzteile vor Ort vorrätig sind – der genaue Umfang kann dabei selbstverständlich individuell vereinbart werden.
Ohnehin wird Individualität im Zusammenhang mit dem Serviceverträgen großgeschrieben, wie Seilkopf erneut unterstreicht. „Selbst wenn ein Kunde sich für ein bestimmtes Servicepaket entschieden hat, kann er selbstverständlich individuelle Leistungen zubuchen. Mit steigender Komplexität wachsen auch die Ansprüche der Abfüller.“
Ein gutes Beispiel für solche individuell gestalteten Partnerschaften ist die im Jahr 2015 im Westen Münchens neu erbaute Paulaner Brauerei. Hier sind sechs Linien von KHS in Betrieb. Dabei handelt es sich um drei Mehrweg-Glaslinien, davon eine für Flaschen mit Bügelverschluss, mit einer Kapazität von jeweils bis zu 50.000 Flaschen pro Stunde, die mit verschiedenen Verpackungsoptionen vom Sixpack über Kartonage bis zum Kasten überzeugen. Hinzu kommen eine Einweg-Glaslinie für den Export, eine Keg-Linie für bis zu 1.000 Fässer pro Stunde und eine Dosenlinie für ursprünglich bis zu 30.000 Behälter pro Stunde. Letztere wurde 2021 durch eine neue und mit einer Kapazität von bis zu 90.000 Dosen pro Stunde deutlich leistungsfähigere Linie ersetzt.
»Anders als reaktiver Service kann präventive Wartung die Produktivität um bis zu vier Prozent steigern.«
![]()
Gruppenleitung Line Solutions
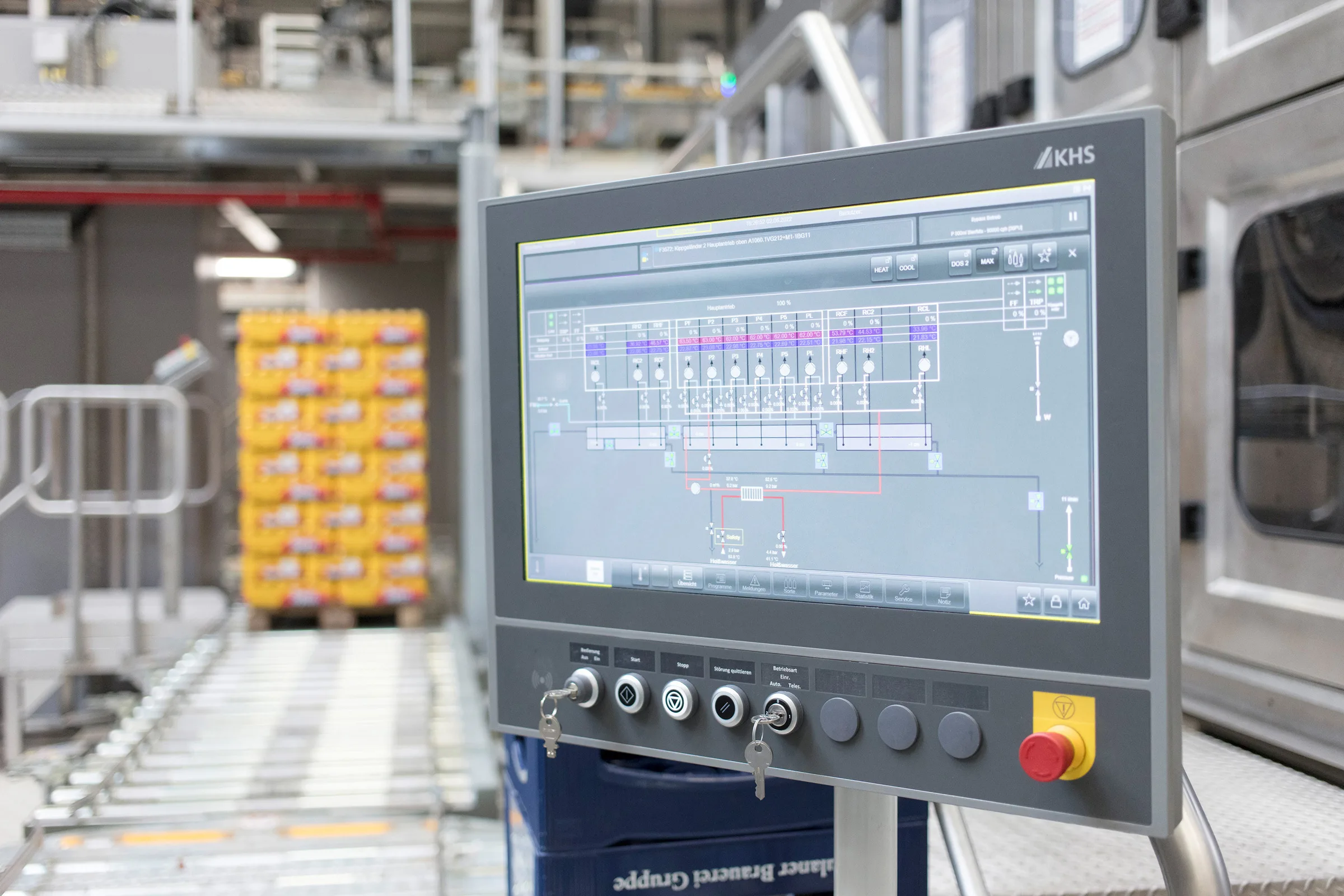
Serviceverträge sorgen dafür, dass am Ende der Linie die fertig verpackten Produkte zuverlässig an die Logistik übergeben werden können.
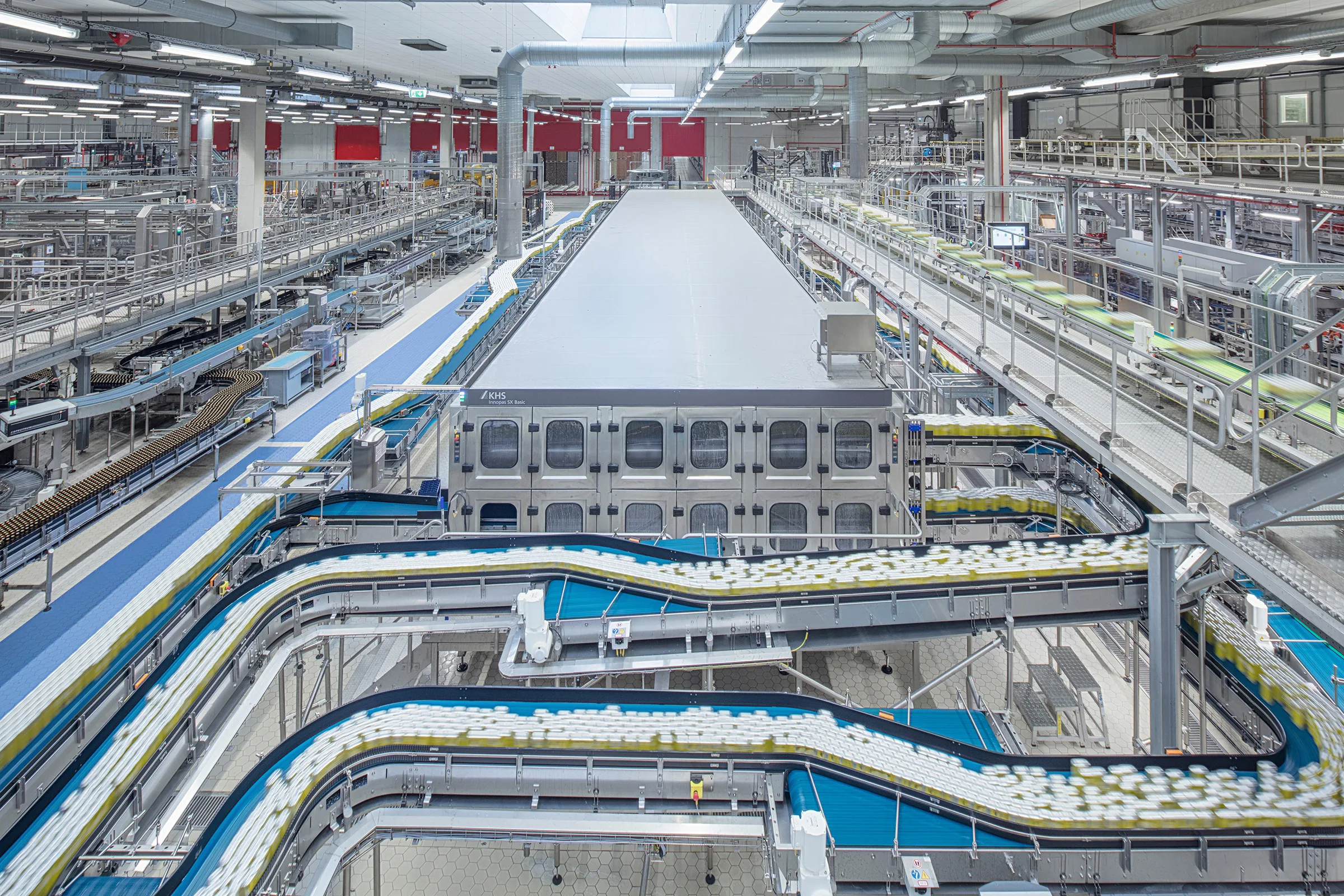
Komplexe Abfülltechnik – hier zum Beispiel ein Pasteur bei Paulaner – sollte regelmäßig gewartet werden.
Know-how-Transfer
„Beim Umzug vom ehemaligen Standort am Nockherberg nach Langwied war uns bewusst, dass wir hier nicht einfach aus dem Bus steigen und dann alles wie von selbst läuft“, erinnert sich Rainer Kansy. Bei der Paulaner Brauerei Gruppe ist er als Leiter Betriebstechnik für Investitionen, Instandhaltung, Engineering, Energieversorgung sowie Entsorgung zuständig und leitet ein Team von rund 60 agil organisierten Mitarbeitenden. „Im Rahmen der Inbetriebnahmen haben wir uns seinerzeit für einen All-inclusive-Servicevertrag mit einer Laufzeit von zunächst fünf Jahren entschieden, der dann um zwei weitere Jahre verlängert wurde. Wir wollten einen Partner an unserer Seite haben, der die neuen Anlagen mit uns hochfährt und auf Leistung bringt.“ Kern der Vereinbarung waren die ganzjährige Unterstützung inklusive jährlicher Überholung sowie aller Ersatzteile – von KHS inklusive der im Zusammenhang mit den Linien gelieferten Handelsware. Dazu gehörte die Vor-Ort-Präsenz von Servicetechnikern – in der Startphase insgesamt zehn Personen, nach dem erfolgreichen Anlaufen zunächst fünf und zuletzt drei. „In dieser Zeit haben wir mit KHS sehr erfolgreich einen intensiven Know-how-Transfer praktiziert“, sagt Kansy. „Dazu zählte besonders die Planung von Jahresüberholungen der kritischen und großen Aggregate. Wenn Sie sich vergegenwärtigen, dass alle unsere Linien zusammengenommen sicher über 100 Einzelmaschinen umfassen, können Sie sich vorstellen, was für eine anspruchsvolle Aufgabe das ist. Bei großen Komponenten wie der Reinigungsmaschine dauert es schon mal eine Woche, bis alles zerlegt und wieder zusammengebaut ist. Da müssen präzise und genau mit den Produktionsplänen abgestimmte sowie möglichst zeitsparende Timings entwickelt werden – mal für eine ganze Linie, mal für einzelne Maschinen –, immer so, wie es am besten passt.“
Neue Servicevereinbarung
Der bisherige Wissensaustausch schloss viele Schulungsthemen und zusammen entwickelte Verbesserungsmaßnahmen ein, zum Beispiel rund um die Optimierung der jeweiligen Wirkungsgrade. „Wir haben gemeinsam Ersatzteile gemonitort, um festzustellen, welche wirklich gebraucht werden und welche nicht“, stellt Kansy fest. „Aber jetzt, nach sieben Jahren, sind wir an einem Punkt, an dem unsere Techniker selbst weiterlaufen müssen, um noch besser zu werden.“
Aus diesem Grund setzte man sich 2022 erneut mit den Dortmundern an den Verhandlungstisch, um eine neue, dem zwischenzeitlich erreichten Status angemessene Servicevereinbarung zu treffen. Dabei verzichtet Paulaner in Zukunft auf die ganzjährige Unterstützung durch Servicetechniker vor Ort. Dennoch wird es weiterhin einen KHS-Koordinator geben, der als Schnittstelle zwischen der Brauereigruppe und den insgesamt fünf deutschen Standorten des Maschinen- und Anlagenbauers fungiert. Er wird auf dem Brauereigelände Koordinierungsaufgaben übernehmen und administrative Tätigkeiten ausführen. Dazu zählt vor allem das Ersatzteilmanagement, für das KHS ein Konsignationslager unterhält – keine 200 Meter von den Abfülllinien entfernt. „Das Lager ist bei unserer Größe ebenso unabdingbar wie ein direkter Ansprechpartner vor Ort“, findet Kansy. „Selbst wenn sich Videokonferenzen immer mehr durchsetzen – in unserem Bereich, wo sich alles schnell bewegt und dreht, sind sie kein Ersatz für den persönlichen Kontakt.“
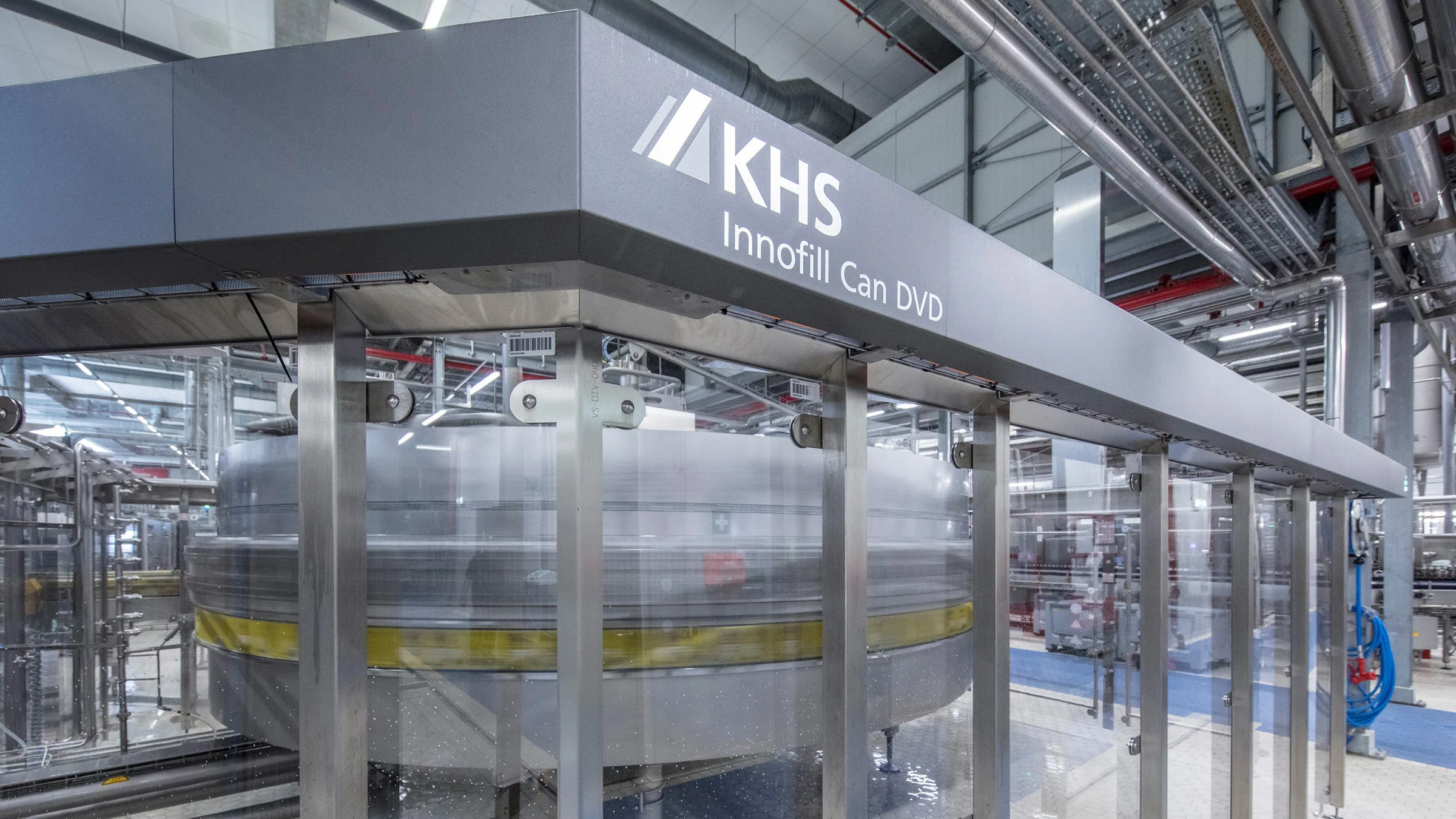
Mit präventivem Service lassen sich Betriebsausfälle bestmöglich verhindern – wie im Fall des KHS-Dosenfüllers bei Paulaner.
Jede Minute zählt
Ein schneller Draht und kurze Wege seien das A und O der engen Partnerschaft, betont auch Jürgen Thielen, Head of Service im Business Center Zentraleuropa. „Man hofft natürlich immer, dass Situationen wie ein technisch bedingter Maschinenstillstand nicht eintreten“, sagt er. „Aber wenn es trotzdem einmal passiert, zählt jede Minute. Dann setzen wir als KHS alles in Bewegung, um der Brauerei zu helfen, sei es am Wochenende oder mitten in der Nacht.“ Wie gut das funktioniert, bestätigt Kansy: „Es hört sich vielleicht komisch an, aber ich bin dann am zufriedensten mit unserer Zusammenarbeit, wenn wir wirklich mal einen Worst Case haben und KHS uns in solchen Situationen mit ihrer Reaktionsgeschwindigkeit und Unterstützung überzeugt." Teil dieser Unterstützung ist die im neuen Servicevertrag vereinbarte Vollanbindung an das Online-Kundenportal KHS Connect. Sie erlaubt es Paulaner, in Echtzeit Lagerbestände und Preise einzusehen oder Bestellungen auszulösen.