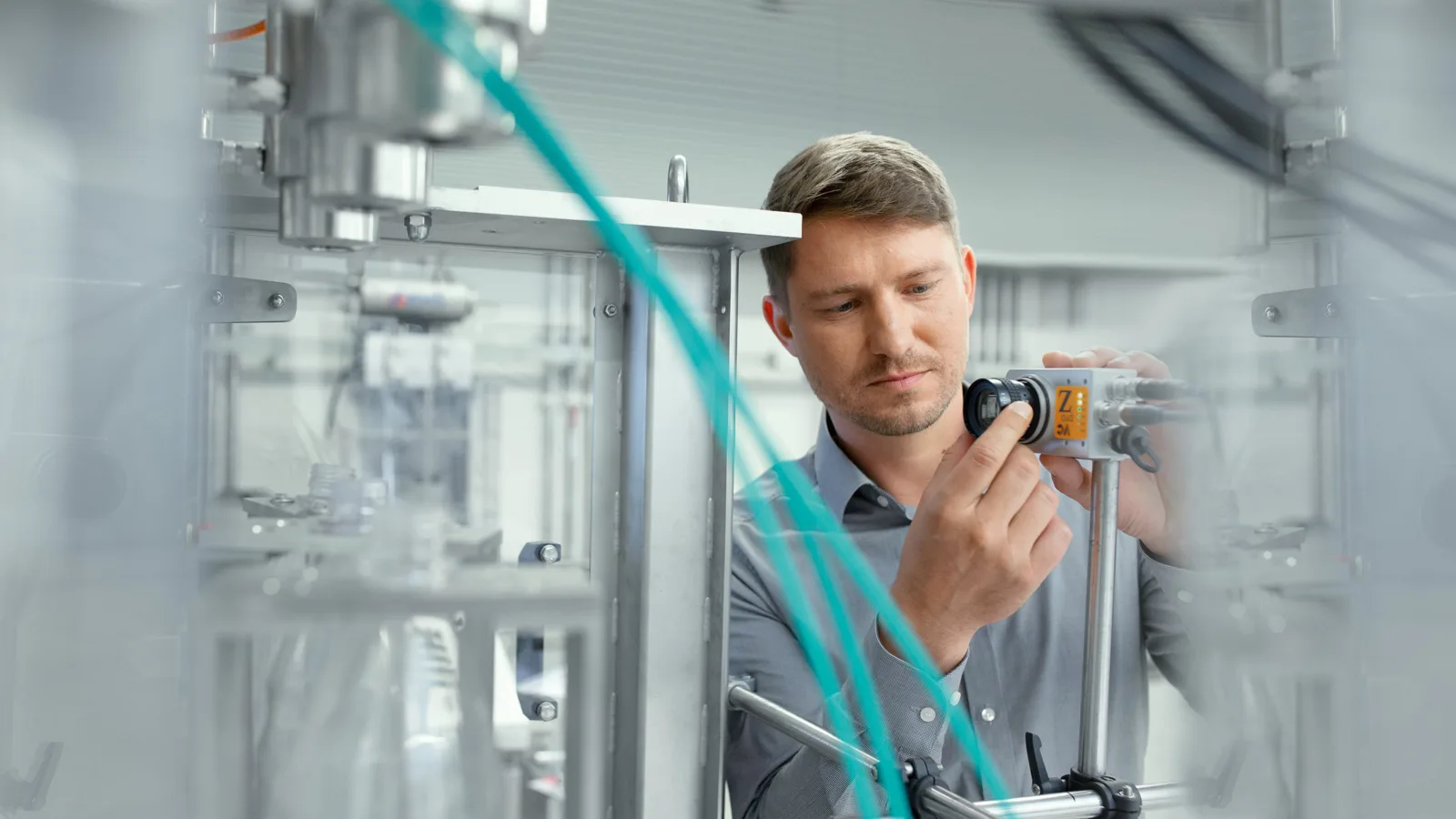
So füllen wir morgen
Wenn Jochen Ohrem in Bad Kreuznach ein Forschungsprojekt initiiert, darf man gespannt sein: Was dann im Verbund mit leistungsstarken Partnern entsteht, ist oft innovativ und weichenstellend – so auch im Fall des intelligenten Füllerventils.
Im Zuge der fortschreitenden Digitalisierung ist seit einigen Jahren der Begriff Industrie 4.0 in aller Munde. Waren es zunächst politische Kreise, die das Ziel verfolgten, Deutschland als Technologiestandort zu etablieren und zukunftsfähig zu machen, hat sich zunehmend auch die Industrie selbst des Themas angenommen. Schließlich haben sich als dritte Kraft Universitäten und Fachhochschulen eingeklinkt, um aus ihren technologischen Innovationsideen im Schulterschluss mit der Wirtschaft praktische Anwendungen zu entwickeln. Das geschieht häufig in Form von Förderprojekten, die zum Beispiel das Bundesministerium für Bildung und Forschung (BMBF) ausschreibt und mit bis zu 50 Prozent bezuschusst.
An solchen Forschungsprojekten beteiligt sich auch KHS, um die Digitalisierung in der Getränkeindustrie voranzutreiben. Eines davon betraf konkret die Abfüllung. Dafür wurden zunächst der Status Quo des Füllprozesses gezeigt sowie ein Szenario geschaffen, wie dieser sich im Rahmen von Industrie 4.0 sinnvoll weiterentwickeln kann. Jochen Ohrem, in Bad Kreuznach als Expert of R & D Management tätig, erklärt das Ziel des Projektes: „Als wir 2015 gestartet sind, ging es darum, die Flexibilität sowie die Energie- und Ressourceneffizienz von Produktionsprozessen mit Hilfe einer intelligenten Steuerung und Vernetzung auf eine neue Stufe zu heben. Besonderes Augenmerk sollte dabei auf die beiden Aspekte Elektronik und Sensorik gerichtet werden.“ Entsprechend anspruchsvoll klang dann auch der Titel des Projekts: DnSPro – ,Dezentral kooperierende, sensorbasierende Subsysteme für Industrie-4.0-Produktionsanlagen‘.
»Man kann mehr erreichen, wenn man auch mal ‚Out-of-the-Box‘ denkt«
![]()
Expert of R&D Management bei KHS
Zur Person: Jochen Ohrem
Der promovierte Chemiker aus Frechen studierte Bioingenieurwesen in Aachen sowie Anlagen- und Verfahrenstechnik in Köln. Im Mittelpunkt seines Studiums stand das Thema Prozessanalysentechnik, dem er sich auch im Rahmen seiner Dissertation intensiv widmete. An der Verfahrenstechnik reizt ihn insbesondere die Kommunikation zwischen den vielen verschiedenen Disziplinen, beispielsweise Elektronik, Regelungstechnik, Messtechnik, Chemie und Mechanik. Seit 2014 ist er bei KHS beschäftigt. Zu seinen ersten Aufgaben im Unternehmen zählte es, Förderprojekte des BMBF zu identifizieren und entsprechende Konsortien zusammenzustellen. Seit 2018 koordiniert der 38-Jährige das R & D-Management von KHS, eine Stabsstelle, die eng mit den Entwicklungsabteilungen des Unternehmens zusammenarbeitet.
Eines für alles
Dahinter steckte die Aufgabe, selbstlernende Füllventile zu gestalten: Bisher kommen je nach Getränk und Behälter rund 20 verschiedene Füllventilvarianten mit hoher Varianz zum Einsatz. Das sollte sich ändern, betont Ohrem: „Wir wollten ein einziges Ventil entwickeln, dass alle möglichen Produkte in alle Behälter füllen kann, ohne dass der Bediener Umstellungen vornehmen muss. Dafür haben wir cyber-physische Systeme (CPS)* genutzt, dank denen das Ventil selbst herausfindet, wie es ein bestimmtes Getränk optimal und möglichst schnell in einen bestimmten Behälter einfüllt.“
*cyber-physische Systeme (CPS) = Verbund softwaretechnischer Komponenten mit mechanischen und elektronischen Teilen, die über eine Dateninfrastruktur kommunizieren.
In diesem Zusammenhang dient eine Kamera als Sensor. Während des Füllprozesses werden Blaseneinschlag und Schaumbildung beobachtet und ausgewertet, um ein Überschäumen und den daraus folgenden Produktverlust zu verhindern. Mit Hilfe von Mikrocontrollern und der Auswerteelektronik der Kamera wird das Füllventil je nach Füllstand über einen Schrittmotor unterschiedlich weit geöffnet, zunächst in „Trainings“ mit selbstständig durchgeführter Entleerung und Befüllung. Im Mittelpunkt stand dabei das „Erlernen“ mehrerer Fähigkeiten: Selbstkonfiguration, Analyse und Selbstdiagnose sowie schließlich Selbstoptimierung. Einfach ausgedrückt: Durch den Einsatz selbstlernender künstlicher Intelligenz tritt minimaler Bedien- und Wartungsaufwand an die Stelle mechanischer Komplexität und manueller Eingriffe.
Interdisziplinäres Team
Neben KHS brachten insgesamt sechs weitere Kooperationspartner ihre jeweilige Expertise in das Projekt ein, das in diesem Fall durch das BMBF gefördert wurde: Chiphersteller Infineon aus Neubiberg stand als Spezialist für Elektronikhardware bereit, WIBU Systems aus Karlsruhe für das Thema Softwaresicherheit – bei der Vernetzung digitaler Komponenten ein enorm wichtiger Aspekt (siehe Artikel „Rundum sicher“ auf Seite 32). EPOS aus Duisburg schließlich steuerte elektronische Bauelemente und Schaltungen bei. Auf der wissenschaftlichen Seite wurde das Projekt von den IT-Spezialisten zweier Hochschulen begleitet – der Bochumer Ruhr-Universität sowie der Hochschule Ostwestfalen-Lippe in Lemgo. Koordiniert wurde der Verbund durch KROHNE Innovation aus Duisburg, als Lieferant für Sensorik und Messtechnik ein langjähriger Partner von KHS. „Das war ein sehr interdisziplinäres Projektteam“ erinnert sich Ohrem. „Als Anlagen- und Maschinenbauer fokussiert sich KHS naturgemäß eher auf Mechanik als auf Elektronik. Im Team ist es uns gemeinsam sehr gut gelungen, die Elektronikkompetenz einzubinden.“
Bei DnSPro stand das Thema Vernetzung klar im Vordergrund. Dazu zählen vor allem die vielfachen elektronischen Schnittstellen entlang der Automatisierungspyramide: Es gilt Verbindungen zu schaffen zwischen den Sensoren, Aktoren, Mikrocontrollern und dem Field Programmable Gate Array (FPGA)**. Diese müssen mit der Speicherprogrammierbaren Steuerung (SPS) und der darüber liegenden Bedienerebene (HMI) vernetzt werden, und der Zugriff durch das Web muss möglich sein.
**Field Programmable Gate Array (FPGA) = Ein integrierter Schaltkreis der Digitaltechnik, in den eine logische Schaltung geladen werden kann.
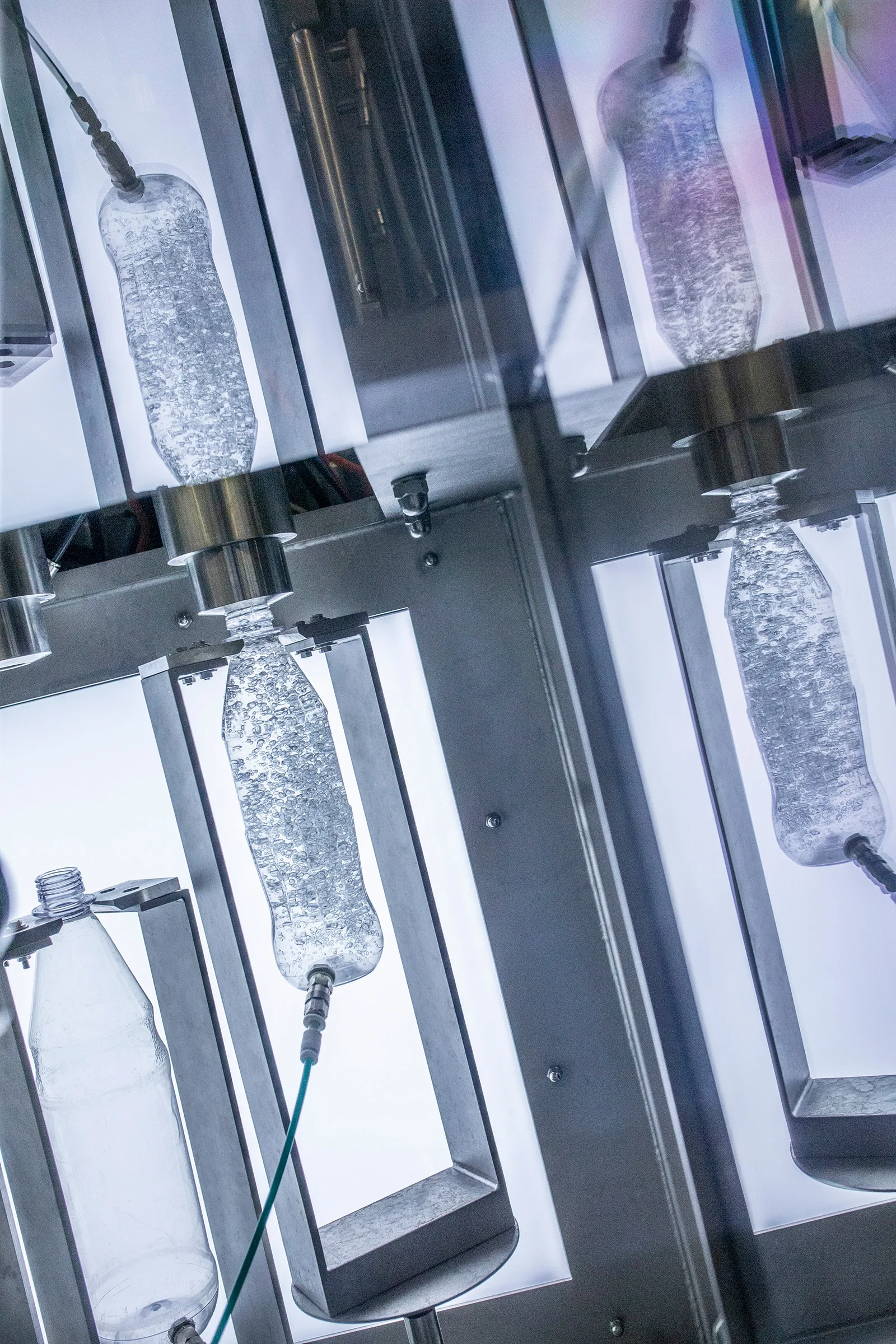
Bei der Abfüllung werden Blaseneinschlag und Schaumbildung von einer Kamera erkannt und ausgewertet.
Umsetzbar und marktfähig
Befragt, wie hoch die Wahrscheinlichkeit ist, dass aus dem Forschungsprojekt einmal ein vermarktbares Produkt wird, ist Ohrem um keine Antwort verlegen: „100 Prozent“, erklärt er. „Unter wissenschaftlichen Gesichtspunkten kann man einen solchen Spielplatz auch mal überdimensionieren und mit allem ausstatten, was machbar ist – auch wenn das später vielleicht kein Kunde in dieser Komplexität braucht oder bezahlen möchte. Aber wir prüfen natürlich ganz konkret, was in der Realität umsetzbar und marktfähig ist. Auf Basis verschiedener Aspekte unseres Prototyps haben wir bereits Entwicklungsprojekte gestartet, die sich mit deren Implementierung in der Praxis beschäftigen.“
Eines der abgeleiteten Themen, an denen momentan konkret gearbeitet wird, ist beispielsweise die dezentrale Steuerung für Abfüllmaschinen. Anstelle eines übergeordneten, zentral in der Maschine platzierten Füllrechners, der den Prozess aller Ventile steuert, kann diese Aufgabe künftig dezentral durch miniaturisierte Rechner an jeder Ventilgruppe oder jedem Ventil übernommen werden. So lässt sich im Füllventil jeweils ein Drucksensor platzieren, der den Druckverlauf dokumentiert und analysiert. Zugleich entstehen aufgrund des deutlich geringeren Verdrahtungsaufwandes sowohl Kosten- als auch Zeitvorteile, zum Beispiel bei der Inbetriebnahme.
Neben den konkreten Entwicklungsprojekten, die aus dem Testfüller abgeleitet wurden, sieht Ohrem aber einen weiteren zentralen Nutzen: „Für mich ist DnSPro ein regelrechtes Vorzeigeprojekt, wenn es darum geht, ein Hochschulforschungsthema in eine praktisch greifbare Anwendung zu überführen. Das zeigt sehr anschaulich, dass man manchmal mehr erreichen kann, wenn man auch einmal die Perspektive wechselt und ‚Out-of-the-box‘ denkt, statt seine Themen wie gewohnt Schritt für Schritt zu verfolgen.“