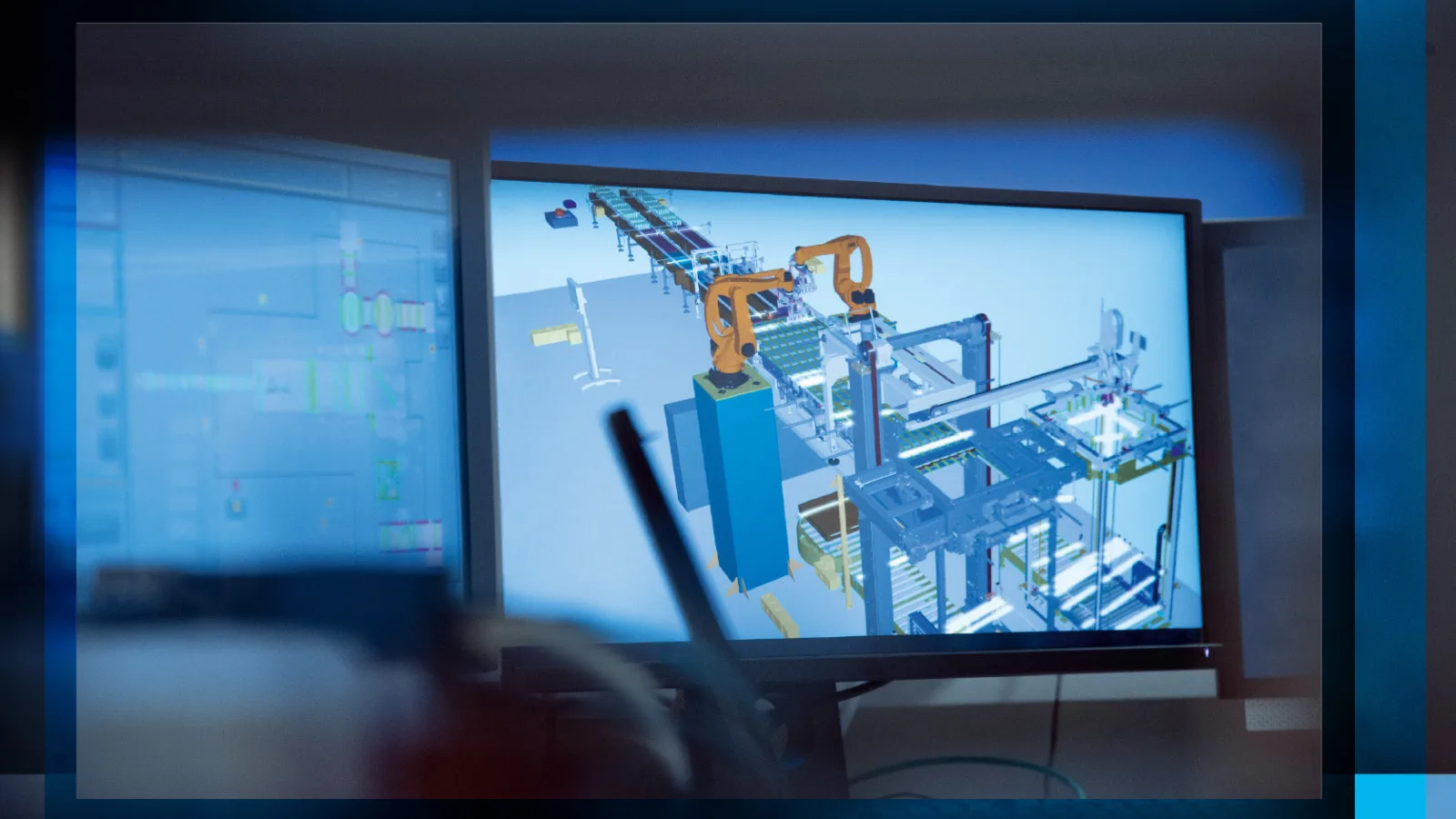
Wie ein Ei dem anderen
Industrie 4.0 ist heute in aller Munde. Die KHS-Experten am Standort Worms lassen den Worten Taten folgen: Seit Jahren schon wird hier die virtuelle Inbetriebnahme praktiziert – aber das ist bei weitem nicht alles, was Digitalisierung leisten kann.
Die Digitalisierung ist nicht weniger als eine industrielle Revolution, die Unternehmen vor große Herausforderungen stellt. Anders als die drei vorausgegangenen Industrialisierungswellen Mechanisierung, Massenproduktion und Automatisierung findet Industrie 4.0, wie die digitale Transformation auch genannt wird, nicht mehr im realen Raum, sondern zunehmend in der virtuellen Welt riesiger Datenmengen statt. Waren früher erst die Dampfmaschine, dann das Fließband und schließlich der Einsatz von Elektronik für massive Umwälzungen verantwortlich, müssen heute gleich mehrere Megatrends wie Automation, Konnektivität, Mobilität, Globalisierung und Sicherheit miteinander vereint werden. Mit Hilfe digitaler und smarter Technologien werden Produktionsprozesse Schritt für Schritt vernetzt und automatisiert, damit Maschinen, Produkte, komplette Anlagen und – nicht zuletzt – Menschen effizienter miteinander kommunizieren und zusammenarbeiten.
Insbesondere der sogenannte digitale Zwilling ermöglicht die Verlagerung in den virtuellen Raum, indem er alle Phasen des Lebenszyklus eines Produktes verfolgt und abbildet. Sämtliche Produktionsprozesse und Produkte lassen sich dadurch virtuell simulieren. Auf dem Bildschirm erscheinen alternative, optimierte Fertigungsabläufe und steigern die Effizienz der Produktionslinien.
Eine der wichtigsten Voraussetzungen dafür ist die Durchgängigkeit des Engineerings über die gesamte Wertschöpfungskette, um sogenannte Datenbrüche an den Schnittstellen der Ingenieursdisziplinen Mechanik, Elektrik und Software zu vermeiden. Anders als heute vielfach üblich, wird dabei nicht sequenziell, also nacheinander und separat gearbeitet. Im Idealfall arbeiten alle Bereiche übergreifend parallel an der Umsetzung eines Projekts und nutzen ein gemeinsames Datenmodell – die Basis für den digitalen Zwilling, der eine Anlage virtuell bis in jedes Detail abbildet und exakte Simulationen erlaubt.
»Durch Ausweitung der virtuellen Inbetriebnahme wollen wir Durchlaufzeiten weiter reduzieren und Fehlerkosten senken.«
![]()
Head of Product Center Palletizing, KHS
Herausforderung gemeinsame Daten
Für einen Anlagenbauer wie KHS, der nicht nur eine enorme Vielfalt verschiedenster Maschinen herstellt, sondern bei dem die Bereiche Entwicklung und Konstruktion auch noch geographisch auf viele Standorte verteilt sind, stellt das eine große Herausforderung dar.
Schon seit 13 Jahren beschäftigen sich die KHS-Ingenieure des Product Centers Palletizing in Worms mit der virtuellen Abbildung von Maschinen und Anlagenteilen sowie deren Simulation. Insbesondere im Bereich von Logistikanlagen wie Palettierern oder Transporteuren bietet sich die Durchführung einer Simulation oder einer virtuellen Inbetriebnahme an. Gestartet ist man mit der Evaluierung verschiedener Tools, gefolgt von ersten Projekten im Bereich von Palettentransportanlagen sowie Be- und Entladung von Kegs. Im Jahr 2015 wurden bereits mehr als 70 verschiedene Hardware-in-the-Loop-Projekte realisiert, mit denen das Verhalten und der Materialfluss von Anlagen simuliert und das Steuerungsprogramm getestet werden können. Seit 2016 ist KHS Brasilien Teil des Projekts und übernimmt die Erstellung von 3D-Maschinenmodellen.
„Unser Ziel ist es, mit der Ausweitung der virtuellen Inbetriebnahme Durchlaufzeiten weiter zu reduzieren und Fehlerkosten zu senken“, erklärt Stefan Diesner, Head of Product Center Palletizing. Um den Umfang der Ersparnis abzuschätzen hilft es, sich die Zehnerregel zu vergegenwärtigen. Diese besagt, dass die Kosten für die Fehlerkorrektur um den Faktor zehn ansteigen, je später ein Fehler im Prozess entdeckt wird. Kann also ein Fehler erst in der Werksinbetriebnahme gefunden und ausgeräumt werden, ist der finanzielle Aufwand zehnmal höher als wenn die Korrektur schon in der Softwarekonstruktion während der virtuellen Inbetriebnahme erfolgt.
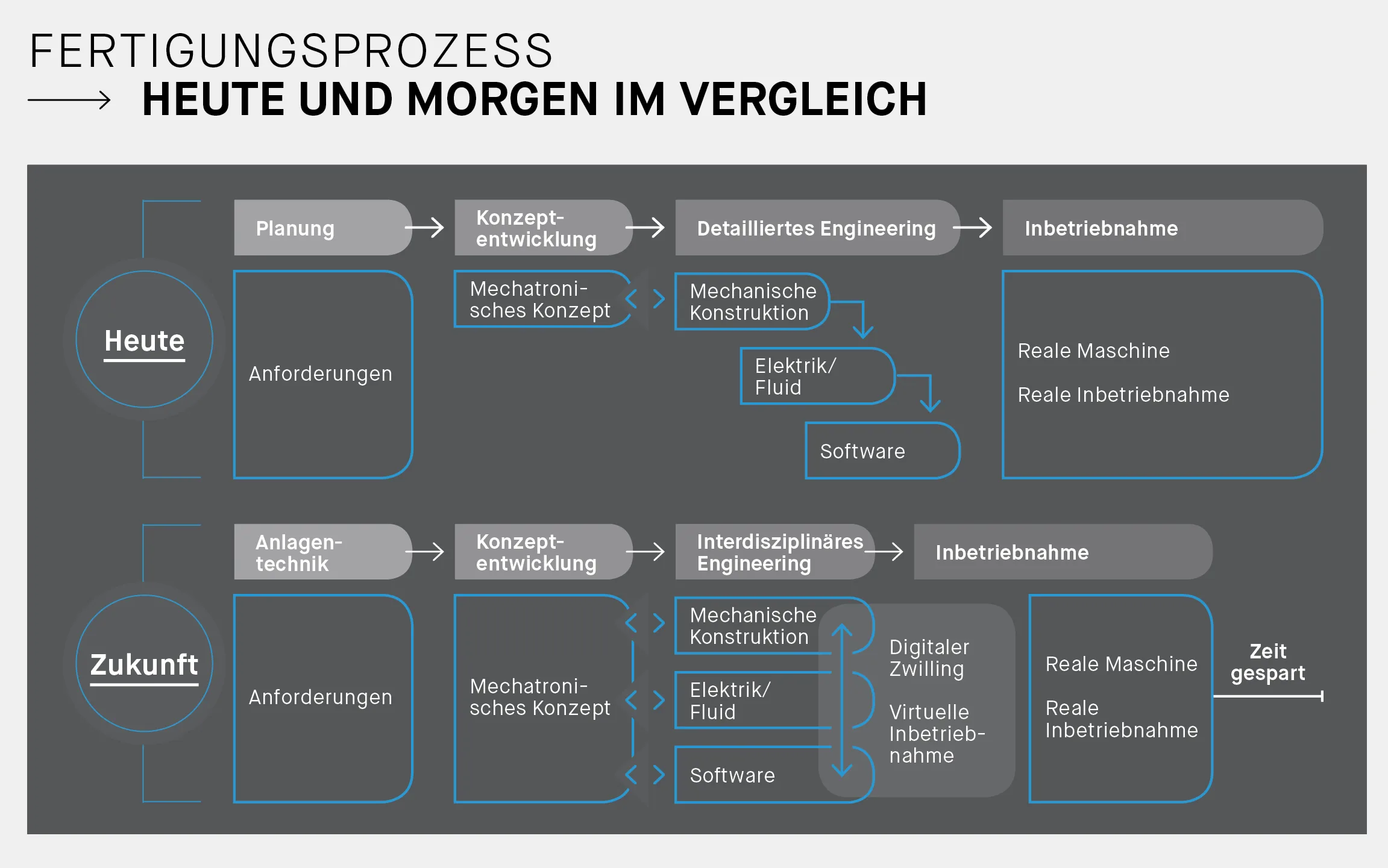
Aufwand reduzieren
Ein weiteres Ziel der aktuellen Arbeit ist es, den Aufwand für die Realisierung der virtuellen Inbetriebnahme zu reduzieren. Eine Grundvoraussetzung hierfür ist die Datenkonsistenz. „Bei der virtuellen Inbetriebnahme haben wir das Thema Datendurchgängigkeit selbst in der Hand“, erklärt Diesner. „Alle Daten werden in unserem Werk erzeugt und vorgehalten, bisher allerdings noch in unterschiedlichen Systemen. Hier sind weitere Schritte erforderlich, bevor diese Daten in einem Werkzeug für „Virtual Engineering“ einschließlich der Simulation effizient und bidirektional zur Verfügung stehen. Ist das erst einmal geschafft, können wir nach Kundenanforderungen konfigurierte oder angepasste Maschinenkonstruktionen schnell und effizient am Bildschirm in Betrieb nehmen.“
In Worms blickt man derweil nach vorn: Die virtuelle Inbetriebnahme ist ein erster Schritt hin zur Digitalisierung von Anlagen der Getränkeindustrie und zum echten digitalen Zwilling. Dieser wird in Zukunft noch deutlich mehr leisten können als die virtuelle Inbetriebnahme zu ermöglichen. Dafür muss der digitale Zwilling jedoch mit weiteren Informationen versorgt werden, zum Beispiel mit Daten zu Umbauten bei KHS-Kunden oder Betriebsdaten aus der Produktion – ein Weg, der auch künftig spannende Herausforderungen bereithält.

* PG-los = ohne Programmiergerät (Laptop), da vor Ort keine Programmmkorrekturen erforderlich sind.
** CAD = Englisch: Computer-aided Design, bezeichnet die Unterstützung von konstruktiven Aufgaben mittels Computer.
*** CAE = Englisch: Computer-aided Engineering, umfasst alle Varianten der Rechner-Unterstützung von Arbeitsprozessen in der Technik.