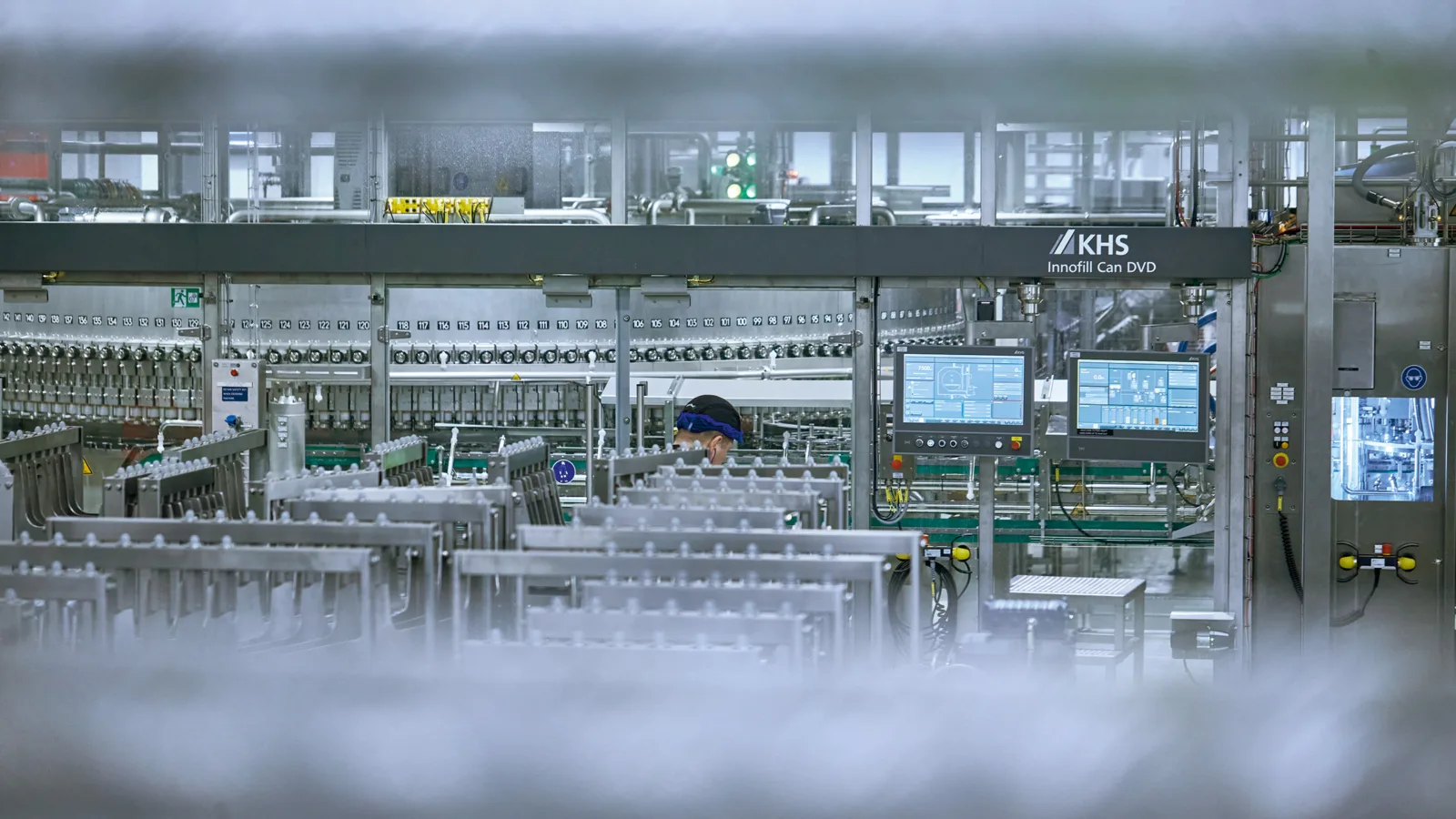
“¡Cada lata es importante!”
Para KHS, la fábrica de bebidas más grande de Europa en Wakefield, Reino Unido, ha sido un socio de confianza en el envasado y embalaje de latas durante años. Al comienzo de la crisis del Corona, el embotellador de Coca-Cola pudo beneficiarse particularmente de la calidad de la cooperación con KHS.
A finales del siglo 19, la ciudad de Wakefield, en el norte de Inglaterra, se convirtió en uno de los centros de industrialización británica. Anteriormente, la ubicación había sido considerada el principal proveedor de cebada y malta de Gran Bretaña, pero ahora se han establecido aquí hilanderías de lana, fábricas de ladrillos y de máquinas con fuertes conexiones con la industria minera en rápido crecimiento. Varias cervecerías también formaron parte de la vida económica local, por lo que hoy el lugar puede enorgullecerse de una cierta tradición en la producción de bebidas. En este aspecto, se renuevan las construcciones: Desde 1989, la ciudad, que junto con Leeds, Bradford y Huddersfield es una de las áreas urbanas más densamente pobladas del país, y alberga la fábrica de refrescos más grande de Europa. Allí, en uno de los cinco sitios de producción británicos, Coca-Cola European Partners (CCEP) llena hasta 10.000 latas y hasta 1.800 botellas PET de refrescos por minuto, las 24 horas del día, los siete días de la semana. Eso corresponde al 45% del volumen total que CCEP produce en Gran Bretaña o, en términos absolutos, 176 millones de unidades de ventas* o alrededor de mil millones de litros de productos terminados.
La planta tiene un total de ocho líneas de envasado; en cinco de estas se procesan latas con un volumen de 330 y 500 mililitros, en las tres líneas restantes se envasan botellas PET en tamaños de 500 mililitros y de 1 litro a 2,25 litros, con un total de alrededor de 300 SKUs**. El embotellador independiente de Coca-Cola más grande del mundo coopera con KHS como socio tecnológico: El fabricante de máquinas y equipos con sede en Dortmund es responsable de cuatro de las cinco llenadoras de latas y de dos líneas completas de latas. Estas dos líneas 4 y 5 se instalaron y pusieron en funcionamiento en el plazo de un año. Después de que la línea 4 fuera un éxito completo en términos de disponibilidad y eficiencia desde el primer día, el embotellador contrató a KHS para una segunda línea de enlatado. El corazón de ambos equipos es la llenadora de latas de DVD Innofill Can, aquí con una producción de hasta 120.000 latas por hora cada una.
* En el sistema Coca-Cola, una unidad de ventas consta de 24 unidades de botellas de 8 onzas líquidas, que corresponde a 5,678 litros
** SKU = Stock Keeping Unit, unidad o artículo en stock
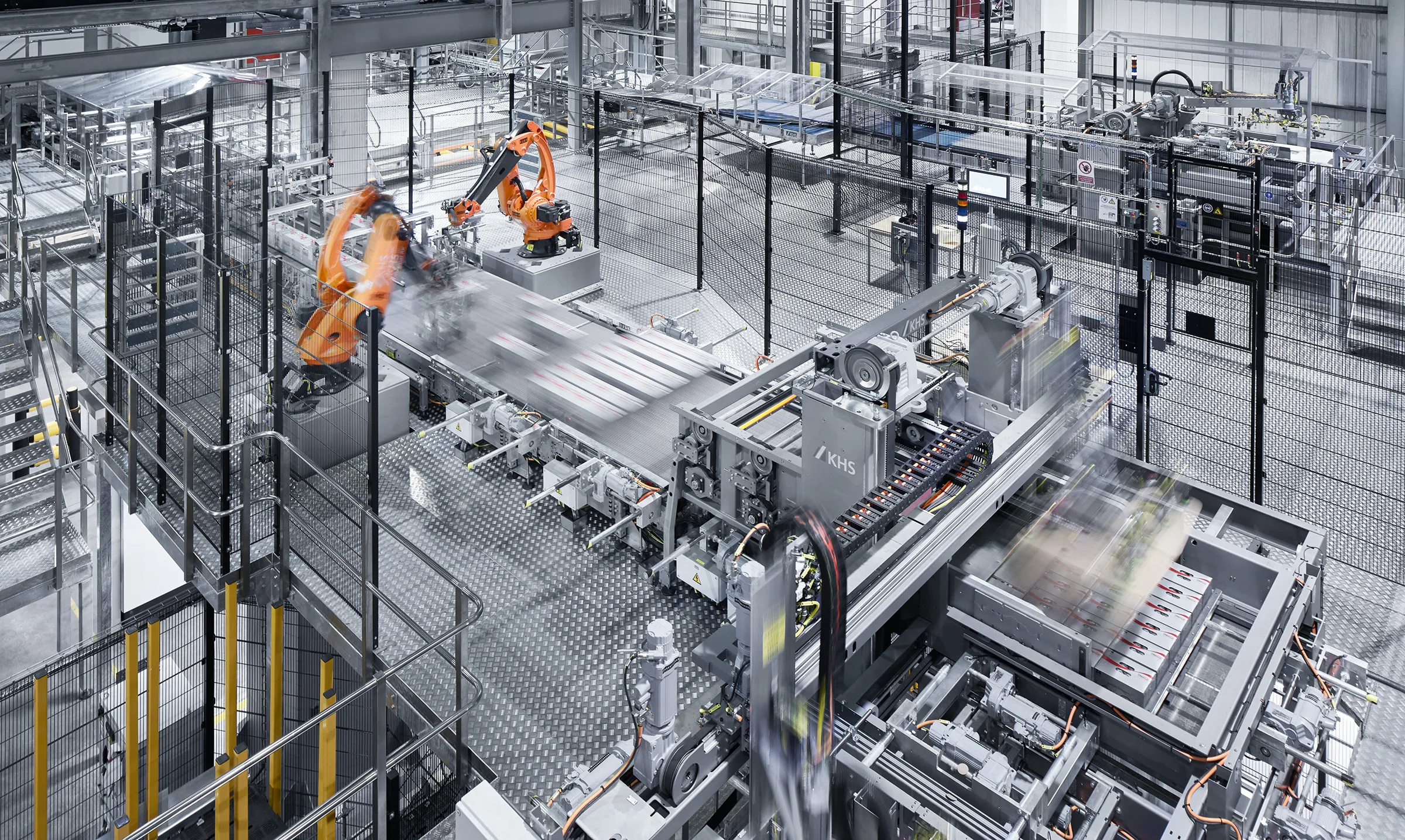
Los robots ponen la “última mano”: El paletizador de KHS procesa cajas de cartón FullyEnclosed, que en CCEP en el Reino Unido están ganando importancia en comparación con los embalajes de film retráctil.
Flexibilidad requerida
“El objetivo de nuestra inversión era, por supuesto, aumentar la capacidad”, dice Michail Skarpathiotakis, director de proyectos senior en la sede de CCEP en Uxbridge, cerca de Londres. “¡Cada lata es importante”! Sin embargo, la atención se centró sobre todo en los multipacks de cartón, que están disponibles en una variedad de formatos, desde cuatro hasta 30 envases. En el contexto de la crisis del Corona, en la que la gente pasa más tiempo en casa, las ventas de estos embalajes están creciendo actualmente a un ritmo de dos dígitos. Las enfardadoras Innopack Kisters Wraparound y de termocontracción, que están integradas en las dos líneas, son igualmente eficientes y fiables.
Como embotellador que se esfuerza por conseguir los niveles de stock más bajos posibles en vista de un enorme surtido de productos, la empresa concede gran importancia a la máxima flexibilidad en la producción. Esto requiere sobre todo un rápido cambio de formato. El hecho de que la nueva línea 5 esté ocupada con cambios de formato o con limpieza alrededor del 40% del tiempo disponible, dice menos sobre la duración de los cambios que sobre su número. Cuando se le preguntó cuántos cambios hubo, Kerry Morgan-Smith, Gerente de Operaciones en el sitio de Wakefield, responde con una sonrisa: “Demasiados”. Pero en vista de las necesidades cada vez más individuales de los consumidores, este es el único camino a seguir.
»Junto con KHS hemos logrado instalar dos líneas completas en sólo 12 meses«
![]()
Gerente de Operaciones, CCEP Wakefield
Hombro a hombro: Ferrum y KHS
El proveedor de sistemas de Dortmund KHS y la empresa suiza Ferrum, que se especializa en cerradoras de latas, están intensificando su cooperación a largo plazo: Suponiendo que las autoridades antimonopolio den el visto bueno, KHS será un accionista minoritario de Ferrum Packaging AG, fundada en la primavera de 2020. Junto con sus empleados, la filial estadounidense de Ferrum Packaging AG también se hará cargo al mismo tiempo del negocio de KHS en EE. UU., y lo integrará en la oferta conjunta. El objetivo es la comercialización global e integral de productos comunes: Si todavía existe una cerradora Ferrum en una línea de enlatado de KHS, ya se está trabajando en la unión en bloque de la llenadora y la cerradora por una sola fuente. Con tiempos de cambio de formato más cortos y fases de limpieza más rápidas, se desea lograr un TCO más bajo. Además, se optimizará aún más el entorno higiénico de los equipos. Ya se están preparando ofertas de servicios, como revisiones conjuntas de los equipos y la integración del sistema de mantenimiento remoto ReDis de KHS.
Sostenible en todos los aspectos
Además de la producción y la eficiencia, los esfuerzos de sostenibilidad en CCEP también están batiendo récords: La empresa establece estándares en términos de prevención de residuos, consumo de energía y recursos, así como en reciclaje: Como todos los sitios de producción británicos, Wakefield también sigue el lema “Zero Waste” (cero residuos), lo que significa que ningún desperdicio termina en los vertederos. Todos los embalajes son reaprovechables en un 100%. “Creo que en ningún lugar de Europa el debate sobre el plástico es más intenso que aquí en Inglaterra”, dice Andy Carter, Director de Ventas de KHS para Gran Bretaña e Irlanda. “En nuestros medios, la contaminación del medio ambiente con residuos plásticos, especialmente los mares, es omnipresente. Esto ha llevado a que los consumidores otorguen gran importancia a este tema”. En el Reino Unido, la lata de bebida goza de una popularidad superior al promedio: Mientras que en Alemania las botellas PET contribuyen con el 81% a la mezcla de embalajes de CCEP y la lata solo tiene una participación del 5%, la proporción para los británicos es del 46 al 35%. Esto los convierte en los líderes europeos en el uso de latas.
Sin embargo, el embotellador está reaccionando a la creciente sensibilidad de los consumidores respecto a los plásticos: “Desde octubre utilizamos un 50% de material reciclado en nuestras botellas PET ”, enfatiza Morgan-Smith. “Eso corresponde a una cantidad anual de 21.000 toneladas. Y estamos trabajando para aumentar aún más esa proporción”. El comportamiento de compra del embalaje secundario también ha cambiado: “Hemos notado que la proporción de embalajes de cartón completamente cerrados está creciendo, a expensas del embalaje de film retráctil”.
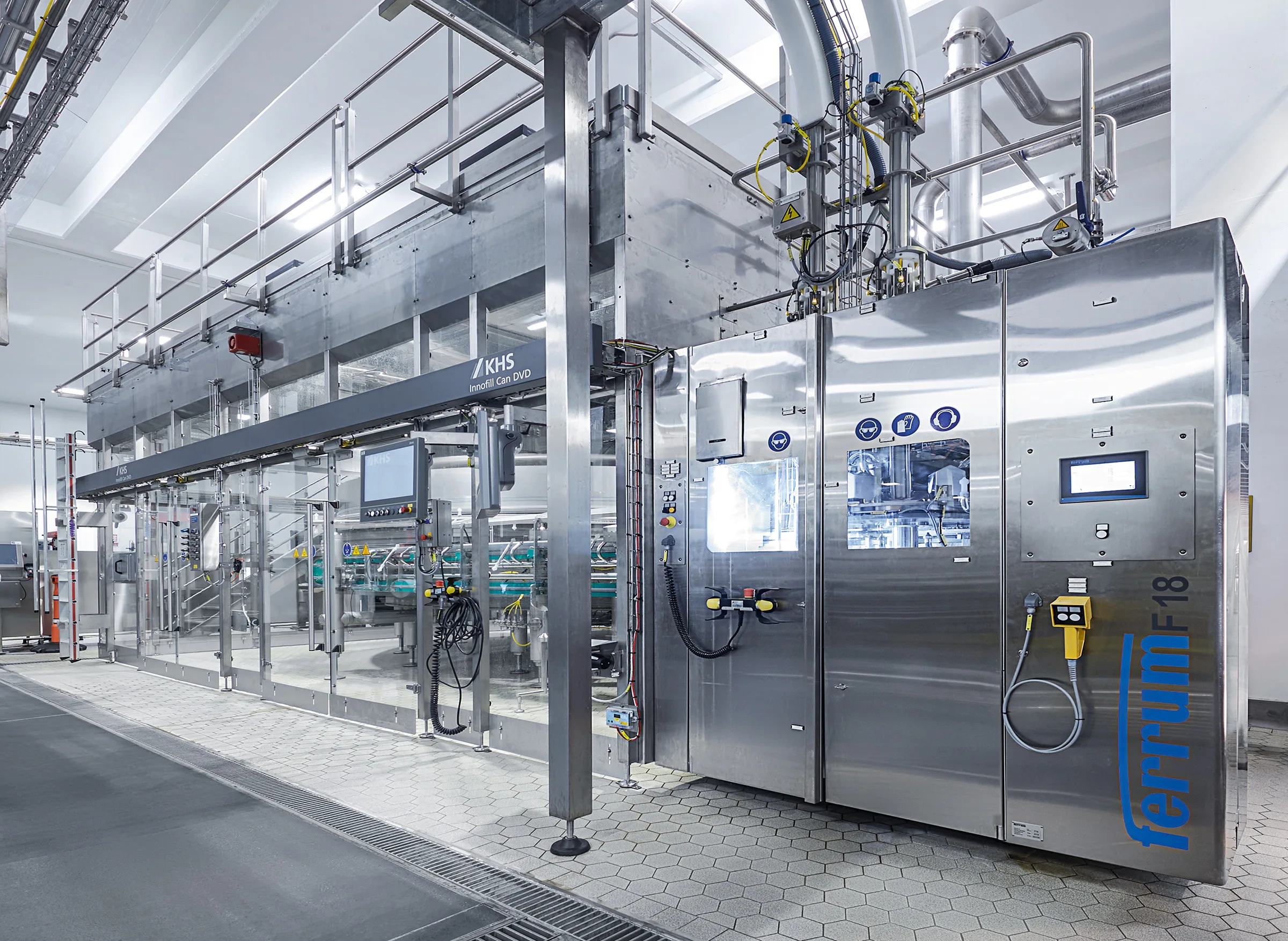
En términos de suministro de energía, la planta de Wakefield está en camino de volverse autosuficiente: “Hemos invertido un millón de libras en la construcción de una planta de cogeneración”, informa Morgan-Smith. “Con esto generamos energía renovable in situ y contribuimos a ahorrar 1.500 toneladas de CO2 al año. No muy lejos de la planta también operamos un parque fotovoltaico del tamaño de 12 campos de fútbol, que abastece a la fábrica con energía solar. Esto significa que cubrimos alrededor del 15% de nuestro consumo total de electricidad y podemos reducir significativamente nuestra huella de CO2”. El 100% de nuestra propia demanda ahora está cubierto por fuentes renovables. CCEP también juega en la liga principal cuando se trata de reducir gradualmente el consumo de agua: Se utilizan alrededor de 1,3 litros de agua por cada litro de producto terminado, una cifra que en los últimos 15 años se ha reducido a la mitad.
En lo que respecta al consumo de materiales, también se concede una gran importancia al manejo sostenible: “En el pasado, hemos ejecutado sistemáticamente con éxito programas de reducción del peso de nuestras latas y botellas”, dijo Morgan-Smith. “Por ejemplo, en 1994 nuestra botella PET de 500 mililitros pesaba 36 gramos, hoy solo pesa 19,9 gramos”.
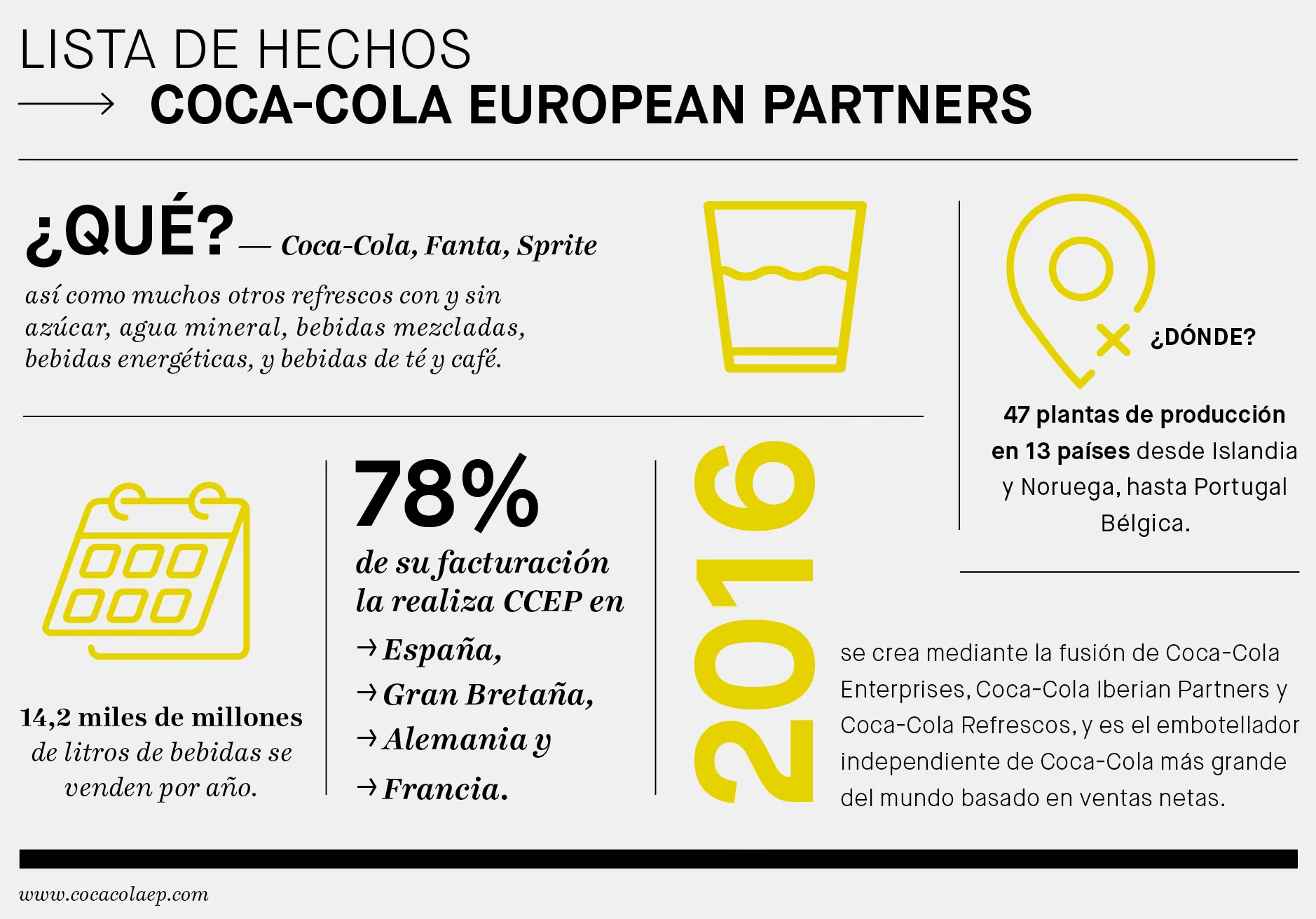
Reincidentes
Como para todos los proyectos del sistema Coca-Cola, KHS naturalmente tiene que someterse al proceso de cotización habitual. El Grupo cuenta con una plataforma de licitación muy sofisticada que incluye un cuadro de mando integral con parámetros técnicos, comerciales, cuantitativos y cualitativos. KHS logró el mejor resultado en este cuadro de mando y, por lo tanto, proporcionó evidencia de que sus máquinas también alcanzan los objetivos de productividad, financieros y técnicos establecidos para la línea 5.
Una vez aceptada la oferta, surgió un obstáculo impredecible, como recuerda Skarpathiotakis: “De repente nos enfrentamos al Covid-19 durante la fase de preparación. Por supuesto, fue un momento muy desafiante para todos nosotros” dice Andy Carter: “La industria de alimentos y bebidas se consideró de relevancia sistémica. No obstante, tuvimos que hacer un gran esfuerzo burocrático para demostrar la necesidad del proyecto y permitir que nuestros colegas cruzaran repentinamente fronteras cerradas en toda Europa. Durante este período difícil, tuvimos que crear un entorno protegido, reforzar el distanciamiento social y organizar el alojamiento y las comidas para los empleados. Todos nos unimos y encontramos soluciones pragmáticas muy rápidamente”. Para ello, a veces fue necesario trabajar de noche: “Una vez, los guardias fronterizos británicos me llamaron desde Calais en Francia a las dos de la mañana para comprobar si los compañeros que esperaban allí estaban realmente autorizados a entrar al país”.
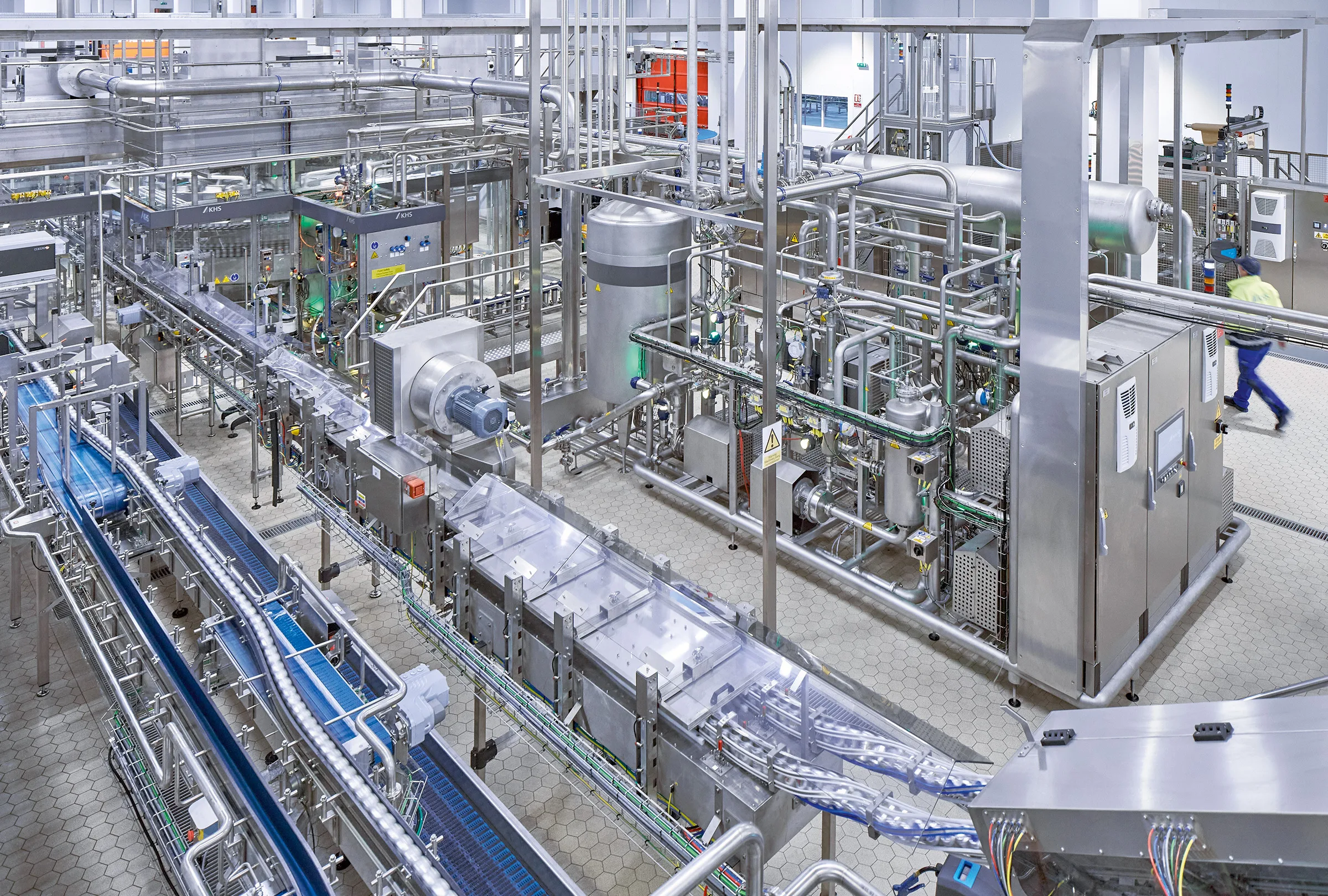
Layout sofisticado: A la derecha se encuentra el equipo de mezcla KHS Innopro Paramix C, en la parte delantera las latas vacías que se alimentan a la llenadora, a la izquierda el transporte de las latas llenas y cerradas que se conducen a la enfardadora.
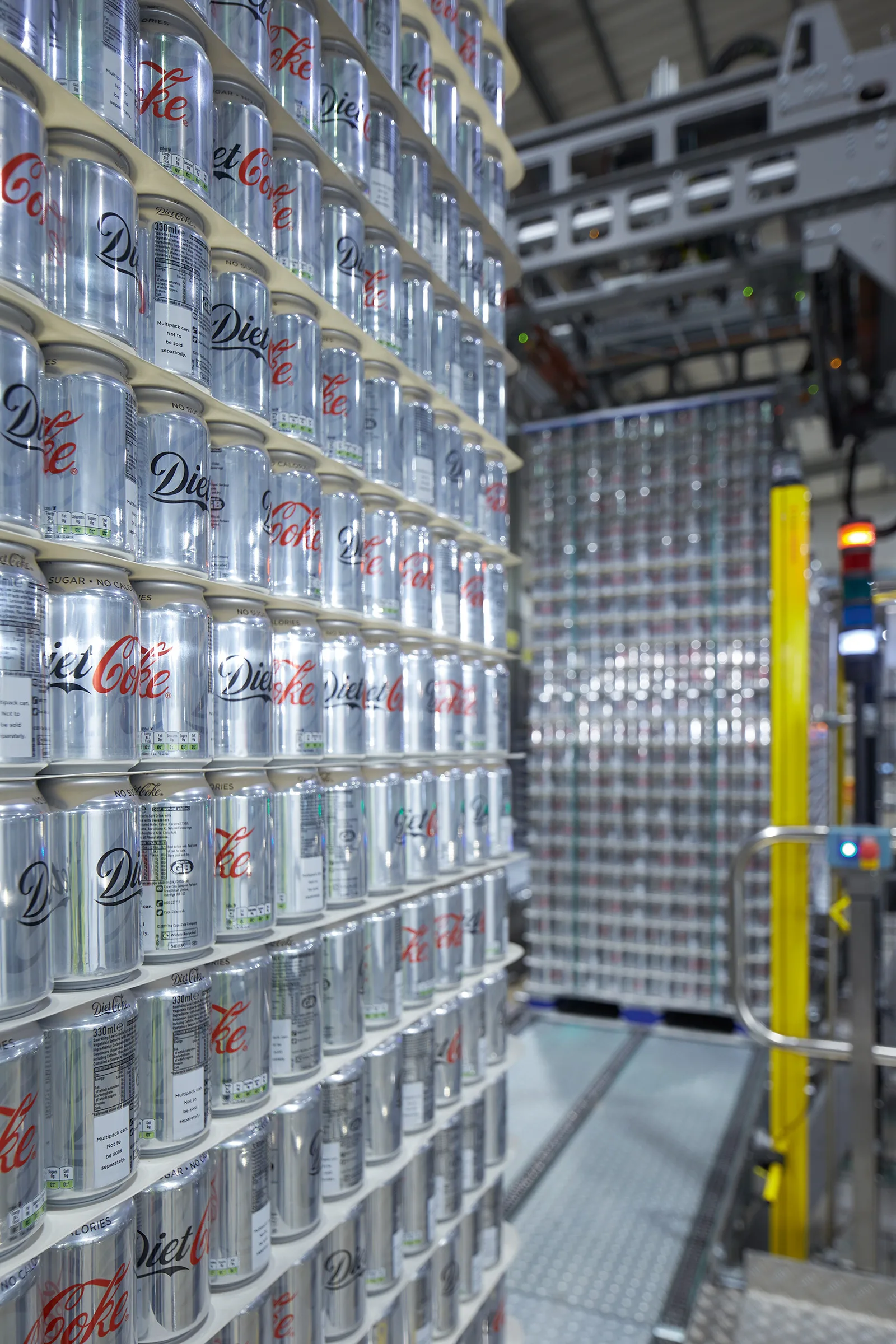
Dos tercios de las bebidas vendidas por CCEP en el Reino Unido son bajas en calorías o sin calorías, más que en el resto de Europa.
Sin embargo, antes de que se pudiera implementar el proyecto, primero se debió encontrar un consenso entre la planta de Wakefield y la sede de CCEP: Algunos de los colegas en el sitio se mostraron inicialmente escépticos sobre la presencia de ingenieros e instaladores extranjeros durante la pandemia. La sede central, por otro lado, quería avanzar en la instalación según lo planeado. “Como uno de los pocos socios contractuales a los que se les concedió acceso a las instalaciones de la fábrica durante el cierre, KHS tuvo que actuar como modelo a seguir”, explica Skarpathiotakis. “Eso funcionó de manera excelente”.
»Todos podemos estar realmente orgullosos de lo que juntos hemos logrado aquí«.
![]()
Gerente Senior de Proyectos, CCEP GB
En khs.com encontrará más informaciones sobre nuestra llenadora de latas Innofill Can DVD, así como videos con ejemplos de aplicaciones específicas.
Instalación durante el cierre de emergencia
La instalación comenzó una semana después de la imposición del cierre de emergencia en Inglaterra. Dadas las difíciles circunstancias, el proyecto también fue un gran desafío técnico: “Junto con KHS, logramos instalar dos líneas en solo 12 meses”, dice Morgan-Smith. “Nunca lo habíamos hecho anteriormente; por lo contrario, pasan al menos tres o cuatro años entre estos proyectos. De cero a cien, y eso en medio de la pandemia. Realmente fue un golpe de suerte trabajar con un equipo tan comprometido y destacado, en el que todos y cada uno de nosotros nos enfocamos en nuestras necesidades como cliente”. KHS también ha trabajado con otros equipos de proyectos en su carrera y conoce las dificultades que pueden surgir, por ejemplo, debido a diferentes mentalidades o barreras idiomáticas. Sin embargo, la cooperación con KHS, y aquí incluso menciona a varios empleados del equipo por su nombre, fue, por el contrario, extremadamente armoniosa, muy agradable y completamente fluida.
Al final, la dirección de la empresa tenía razón: No hubo ninguna infección porque todos los involucrados se adhirieron a reglas de higiene y distanciamiento extremadamente estrictas con la mayor disciplina posible. La instalación y la puesta en marcha se pudieron realizar sin problemas y sin demora. Desde el primer día, la nueva línea demostró ser extremadamente eficiente y superó incluso las más altas expectativas. Al final, todos están extremadamente satisfechos con el resultado exitoso del proyecto. “Todos podemos estar realmente orgullosos de lo que hemos logrado juntos aquí”, dice Skarpathiotakis, y Kerry Morgan-Smith se ríe: “Cómo logramos eso, es algo que hasta el día de hoy no lo sé...”