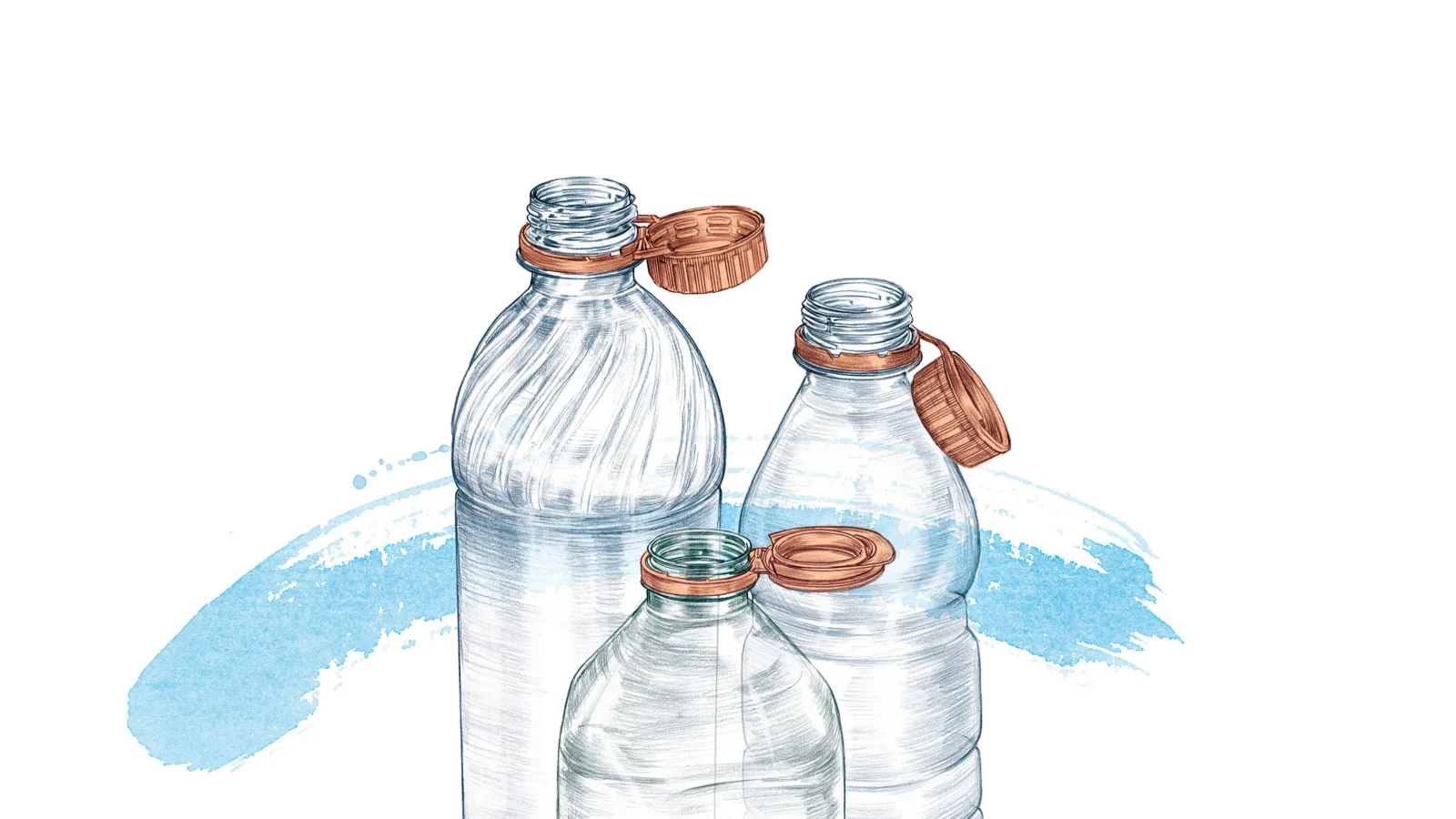
Forming an attachment
The EU’s Single-Use Plastics Directive presents beverage producers with a number of challenges, starting with the introduction of new caps tethered to non-returnable PET bottles. KHS’ team of experts has thus taken a look outside the box and is supporting its customers with competent, proactive advice.
The tethered caps directive is part of the Single-Use Plastics Directive passed in 2018 by the European Union, the chief objectives of which are to force a circular economy low in CO₂ emissions and to cut down on the amount of plastic waste. To achieve this, all plastic packaging on the EU market is to be recyclable by 2030 and consumption of single-use plastics is to be considerably reduced. This has given rise to a number of bans and directives designed to curtail the use and promote recycling of non-returnable products made of plastic.
The following three directives are of particular relevance to the beverage industry – and especially to all bottlers of carbonated soft drinks, still water and aseptic beverages:
- From July 2024 all caps on single-use PET bottles holding up to three liters must be firmly attached to the bottle thread as tethered caps.
- From 2025 77% of all beverage bottles are to be collected by type in recovery systems, with this figure rising to 90% by 2029.
- From 2025 all one-way PET bottles must contain a minimum of 25% recyclate. From 2030 this percentage increases to 30.
So that these directives can enter into force in the various member states, they must be incorporated or adapted into the respective national law. This process, which on the one hand gives the individual EU states a certain legislative scope, also means that on the other it often takes months for the countries to reach a uniform agreement on important standards. This causes uncertainty among beverage producers who have to economically realize the new norms.
Time is running out
The longer it takes for the directive to become national law, the less time bottling plants have for the cost-efficient and sustainable implementation. And even if national transition periods can delay the introduction of tethered caps to some extent, they can’t stop it all together. It’s thus all the more important that all of the parties involved – from cap and preform manufacturers to tool manufacturers – integrate the new regulations into their own value chains with an eye to creating as much added value as possible. Saving on resources and lowering the amount of CO₂ equivalents used are relevant in this context. This is why beverage producers primarily focus on reducing the weight of bottle caps and threads. The further development of these and agreement on new standards are the logical consequence of the directive. This has also led to the first consumer tests being run on relevant markets that provide significant information on the acceptance of the new closures. The new cap must ultimately not be allowed to spoil the drinking experience: the handling of the new cap must be compatible with the drinker’s present intuitive habits when opening a beverage bottle so that consumers grow used to the new principle within a very short space of time. Tying the cap to the message of sustainability – namely that these types of cap no longer end up polluting the environment and our oceans – can undoubtedly prove supportive here. After all, consumers are paying increasing attention to the ecofriendliness of beverage packaging; according to several studies, they would even change supermarkets if a different one sold more environmentally friendly packaging. Bottlers who take a clear stance on this issue can win retailer and consumer trust and strengthen their market position.
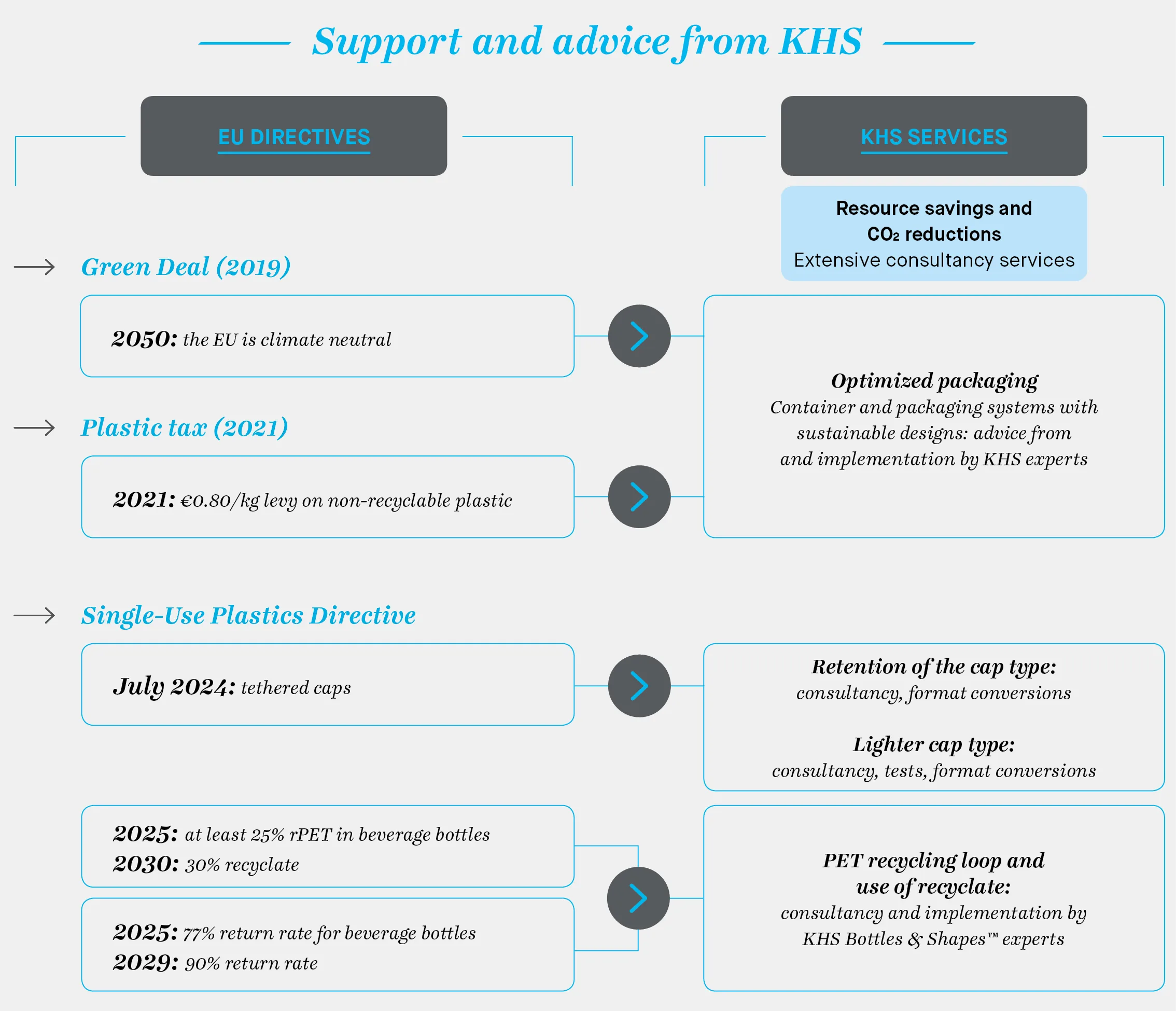
Even if not all of the general conditions have yet been finalized at the time of writing, those beverage producers affected by the new directive must already start thinking about alternative solutions that allow them to adjust their production facilities to the new laws on time.
From direct talks with its customers, KHS knows that all of them are feeling a certain time pressure yet are partly still unsure as to which decisions must be made by when to implement the directive in good time and avoid unnecessary expenditure. There are basically two options available:
Retain the present cap type
Most cap manufacturers offer suitable tethered cap variants that match the caps currently in use. With these cap variants, beverage bottlers meet the minimum legal requirements. Savings in weight are not to be expected here; however, the time and effort required for conversion are manageable.
Change to a lighter cap type
By changing the geometry, the weight of both the cap and the thread is reduced and the legal requirements are more than satisfied. Cap manufacturers offer a range of cap variants for lighter closures that can be tested in advance during ongoing operation with relatively little effort. The weight saved lowers material costs and results in savings in costs and resources in the long term.
»We provide a sound basis for decision and flexible systems and solutions.«
![]()
Head of Service Sales, KHS
In line with the various other aspects of the Single-Use Plastics Directive and beverage bottlers’ corporate and sustainability policies, if desired KHS can also make a holistic assessment of a company’s current PET bottles with the aim of saving even more weight and increasing the amount of recyclate used up to 100%. KHS’ process engineers advise interested bottlers on the selection of preforms made of recycled PET and make sure that the bottles in the stretch blow molder retain their perfectly symmetrical and stable shape. The all-round approach adopted by the KHS experts also ensures that the preforms are fed gently to the stretch blow molder and that the caps are screwed onto the bottles without any problems in the capper. In view of the growing relevance of container recyclability and the demand for sustainable designs, further components such as caps, labels and glue are also closely examined.
Secondary packaging with savings potential
Furthermore, regarding secondary packaging KHS also offers other options for containers that are gentle on resources and cut emissions, such as packing them in paper or recycled film (up to 100%) or, as in the case of the KHS Nature MultiPack™, without any outer packaging whatsoever, with the containers held together by stable yet easy-to-remove dots of adhesive. What’s new is the Carton Nature Pack, where the pack is held together by a carton clip made of cardboard. In the packaging and palletizing section of the line KHS’ specialists make sure that a bottle whose geometry has been changed still fits into its pack formation and literally ‘goes with the flow’ in the packaging machine. Bottlers who, with the help of the Dortmund systems supplier, take a close look at the entire bottle and its secondary packaging will recognize plenty of potential for saving on costs and resources that also helps to make the overall production process more sustainable – and this to then be credibly communicated to the increasingly critical consumer.
Together with the bottler, economically and technically sophisticated systems from a single source are developed that can be easily implemented in practice – and whose scope and cost are based on the requirements and possibilities of the customer. We’re not talking about either/or scenarios here. Beverage producers who, for reasons of time and cost, wish to retain their specific cap type for the time being can later flexibly switch to a lighter cap variant, providing that the conditions for this are created now.
In this challenging situation, KHS presents a number of forward-looking options with its holistic consultancy program. The company provides its customers with a sound basis for decision and supplies flexible systems and solutions – especially to those clients who in view of the current uncertainty don’t yet know where their journey will lead them. In doing so, no aspect is overlooked or ignored – from the TCO to the final schedule for conversion.