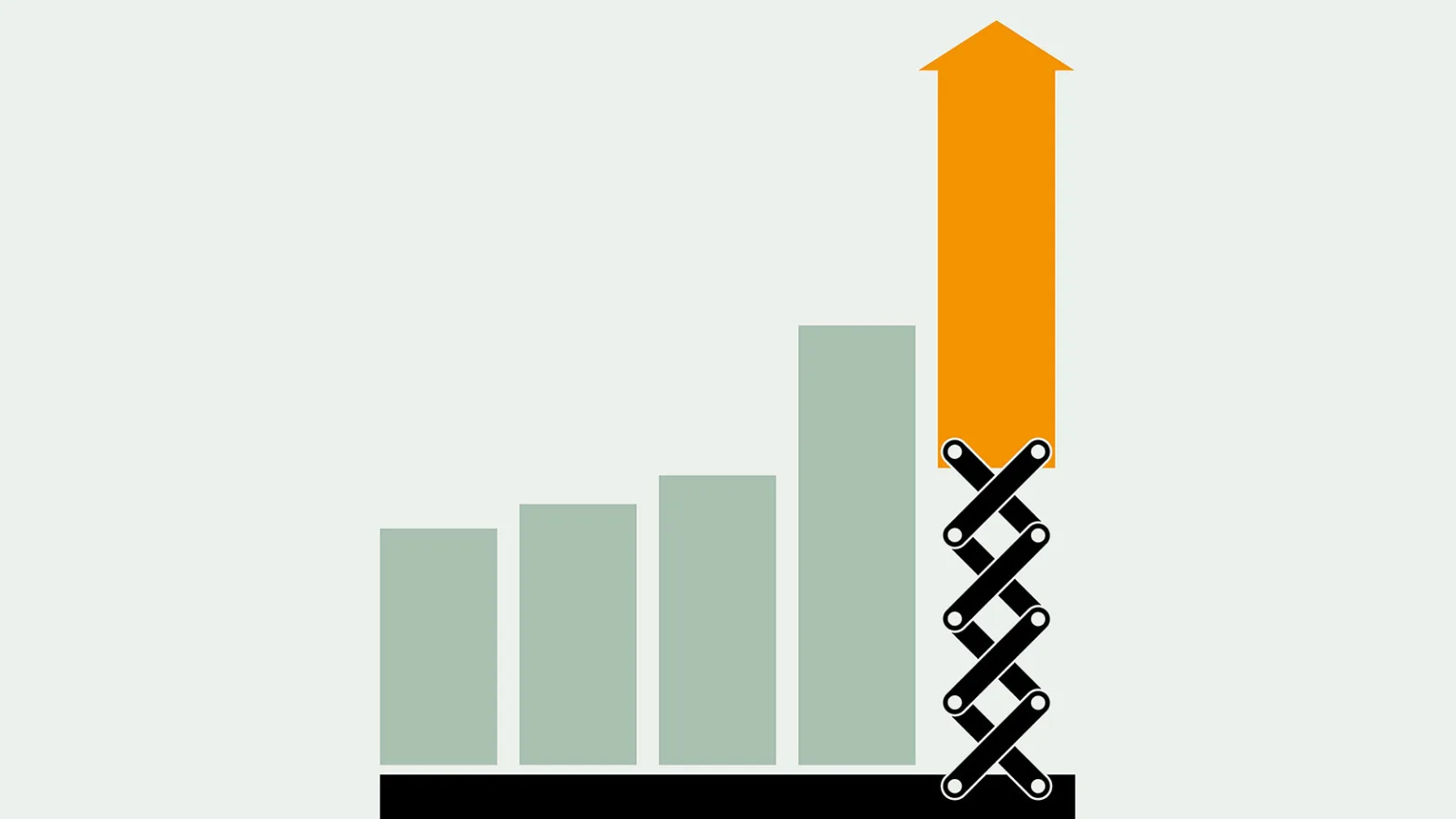
Sound investment
When KHS invests, it helps to achieve greater sustainability in every respect – especially regarding economy but also society and the environment. Taking three totally different projects as an example, we show why this is good for customers, employees and the company itself.
When KHS claims to be a reliable partner to its customers, trust is a major factor. The global companies in the beverage industry in particular attach the greatest importance to receiving cooperative support and wish to partner powerful systems suppliers who also offer them a long-term perspective. In order to establish these prerequisites, investments in the future viability of the company are essential. “Thanks to a satisfying course of business and a stable growth rate, which we can be very pleased with, we have the necessary resources that enable us to cope with future demand,” explains Martin Resch, CFO (Finance, Procurement and IT) for KHS. “Throughout all of our production sites we’re continuing to invest in modern and efficient production, expansion of our infrastructure in our growth regions and thus ultimately in customer satisfaction.”
Optimized processes, more satisfied customers
This ranges from the site concept for Bad Kreuznach to the refurbishment of the design engineering departments and the introduction of flow production in Worms. Whether a sales and service hub is set up in Kenya, a new training center built in South Africa or offices and warehouses erected in Australia, all over the world initiatives are in place to optimize processes and improve customer orientation. KHS doesn’t only have measures like these in its sights, however; the satisfaction of its employees is also of tantamount importance to the company, with personnel of course also benefiting from better working conditions and a pleasant working environment. Last but not least, by taking such action KHS is also boosting its appeal as an employer: a crucial factor when recruiting specialist workers.
By way of example, this edition of ‘KHS competence’ focuses on three larger projects in which the company is currently engaged and which will have an impact on its future processes and business – each in its own particular way.
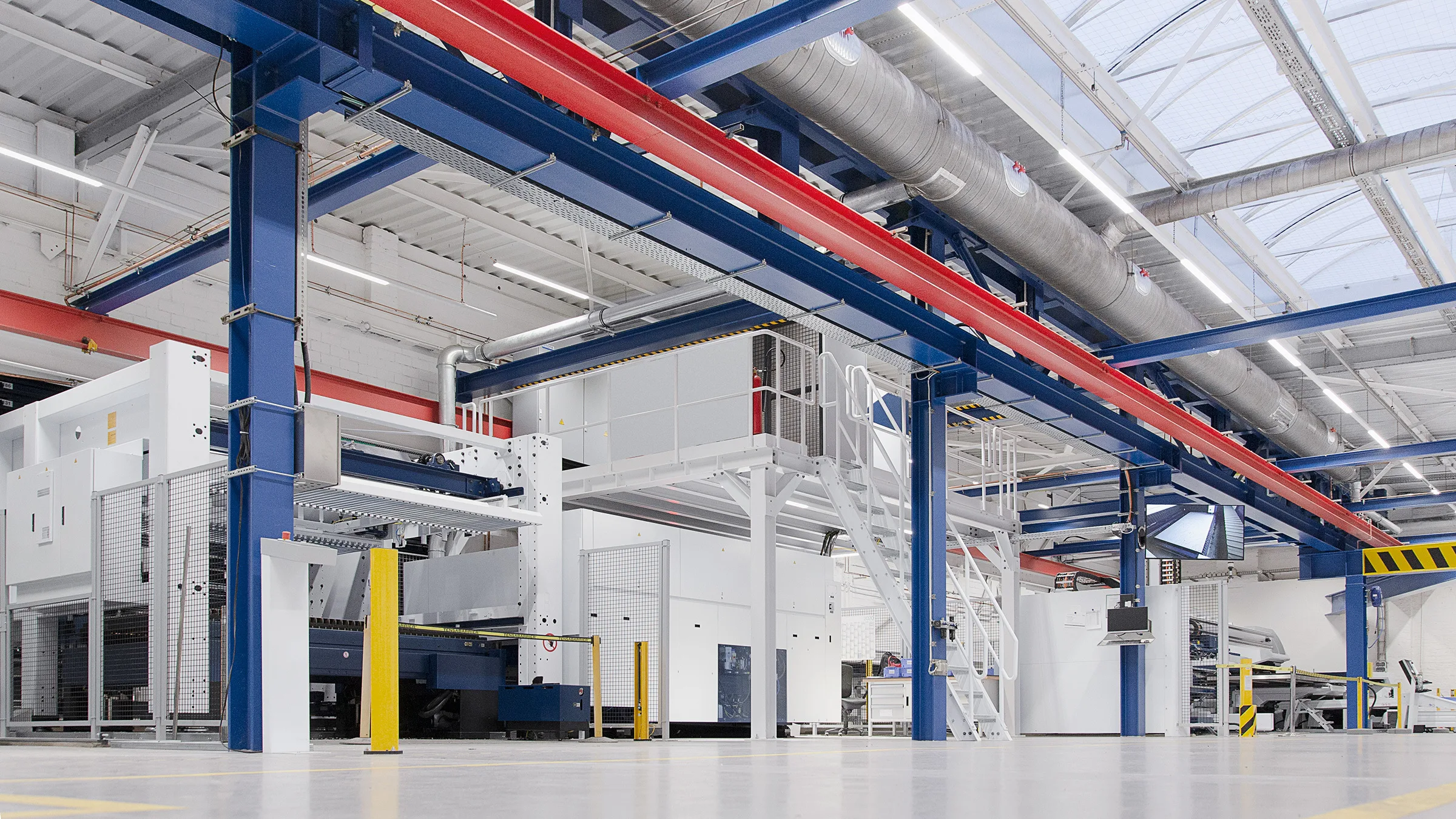
Around €6 million have been invested in the extensive modernization of the Sheet Metal Manufacturing Department in Dortmund alone and for new, state-of-the-art technology.
Example 01
Boosting efficiency at KHS headquarters
One of the largest planned investments with a volume of around €20 million concerns KHS’ headquarters on Juchostrasse in Dortmund – as the name of the associated project reveals. JUDO 2020 is the umbrella term for what are in effect seven sub-projects encompassing many departments of the company from Purchasing through IT to Quality Management, to name but a few. The project was triggered by the KIT development project initiated in 2015 which aimed to consolidate KHS’ conveyor technology. The to date (physically) separate container and pack conveyor series have now been merged to form a uniform, configurable module and standardized wherever possible.
The objective was to significantly increase the product’s profitability and boost efficiency during order processing. “This not only called for fundamental changes to and automation in the design engineering but also the creation of a suitable workspace,” explains Matthias Köster, JUDO 2020 project manager. “We wanted to combine all aspects of the physical goods and services we provide under one roof – from machine assemblies through system installation to shipping.” The construction of a new production shop approximately 4,300 square meters in size – which alone amounted to an investment of about €4 million – wasn’t the only measure which had to be taken under the auspices of KIT, however.
Modern sheet metal manufacturing
One of the larger sub-projects centered on the modernization of the Sheet Metal Manufacturing Department, in which around €6 million were invested. The department’s production shop, one of the oldest on the company premises, was given a new floor and new roof during an extensive refurbishment. The main features of the revamped machine park include a fast, energy-efficient fiber laser, a combined punching/laser machine and a larger, fully networked sheet metal warehouse. Coupling of CAD* and CAM** data by IT is now also state of the art, automating much of the production planning in sheet metal manufacturing.
* CAD = computer-aided design or the support of design engineering tasks by a computer.
** CAM = computer-aided manufacturing or the support of manufacturing tasks by a computer.
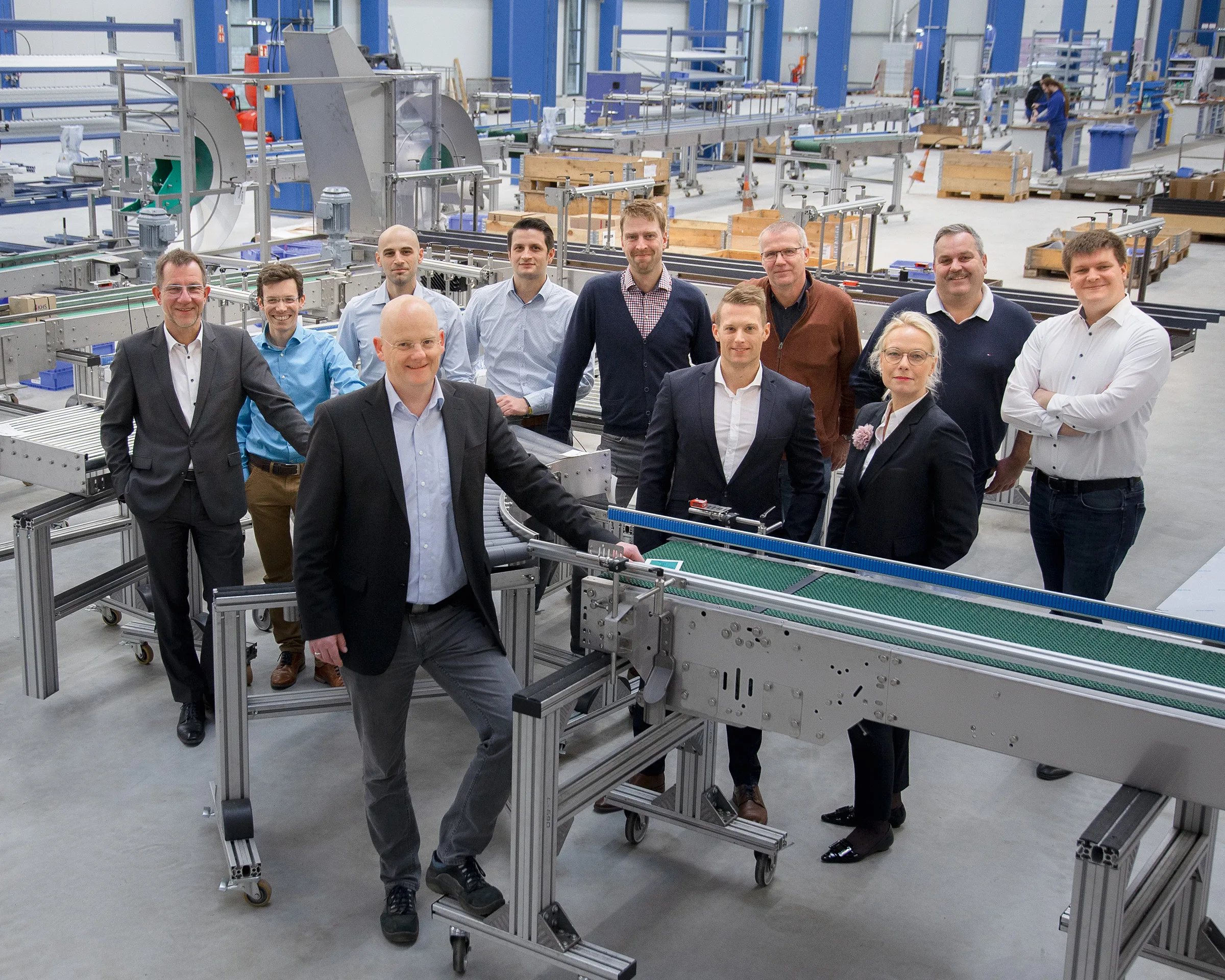
The JUDO 2020 project team consists of representatives from many different company departments – from Purchasing through IT to Quality Management.
Another department involved in JUDO 2020 was Industrial Engineering whose task is to apply the latest principles – from paperless production through a new system for fine assembly control to worker self-tests. “Unlike in the construction of big machines such as bottle washers, where comparatively few systems are built each year, a huge variety of conveyors is manufactured in large numbers with short lead times,” is how Köster characterizes the particular challenges posed by this project. “In order to manage this and increase efficiency in order processing, we need an extremely sophisticated system.”
Interface-intensive undertaking
When building this assembly system in the new, completed Hall 22 Industrial Engineering was chiefly assisted by Supply Chain Management. “Regarding the scope of the project and number of the company departments involved, JUDO 2020 is an unusually large, very complex and particularly interface-intensive undertaking, to which many departments have contributed,” Köster sums up. “The great commitment shown by all those involved, clear goal orientation, intensive, interdepartmental cooperation and consistent, agile project management were the key factors behind the success of this project. Coordinating all this is of course a challenge which goes way beyond the normal call of duty.” In the end the team’s efforts were well worthwhile, however, with the project keeping to both the set schedule and budget.
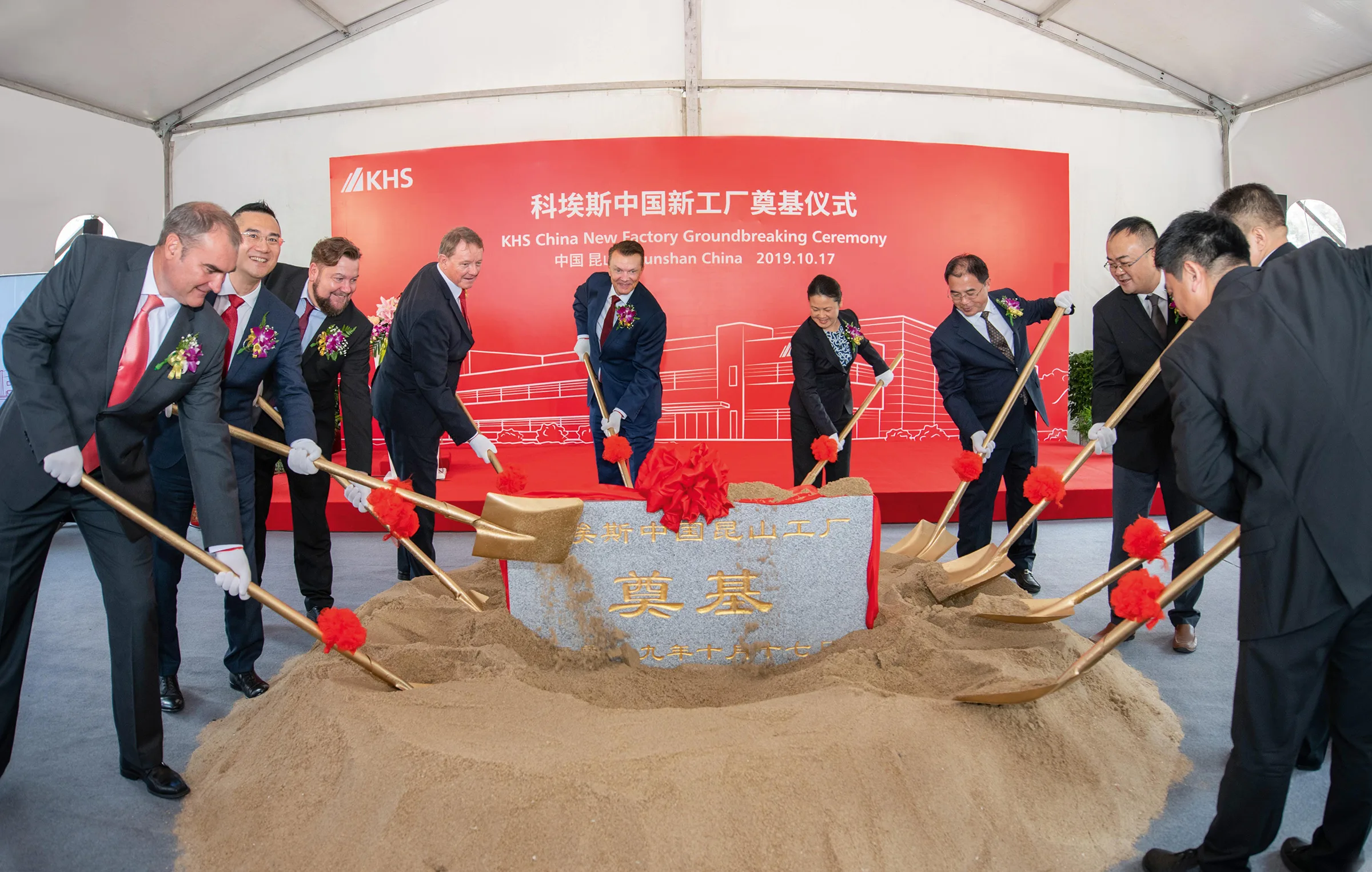
The foundation stone for the new KHS China factory near Shanghai was ceremoniously laid in October 2019.
Example 02
Expanding capacities in China
Another example can be found in Asia: in order to also meet the growing demand for Aquablocks*** in the high-capacity range on the rapidly growing market in China, KHS is investing about €10 million in a completely new factory here. At the German Industrial Park in Kunshan, a sizeable settlement of German high-tech companies about 40 kilometers from Shanghai, a plot of land measuring approximately 20,000 square meters has been procured.
*** Aquablock = block system for the water segment specially configured by KHS for the Asian market.
As opposed to the previous strategy of providing standardized PET systems for still water only in the low- and medium-capacity range, KHS China also aims to cater for the high-capacity range in the near future – and is going for diversification. “When our new production facilities are finished, we’ll be able to build machines with an output of up to 81,000 bottles per hour,” states William Wu, managing director of KHS China. Up until now the maximum capacity was 50,000 bottles every 60 minutes. “We can also expand our portfolio to include not just water-only lines but also carbonated soft drinks,” he smiles. He sees further sales potential in spirits producers and the food sector, such as with bottlers of soy sauce.
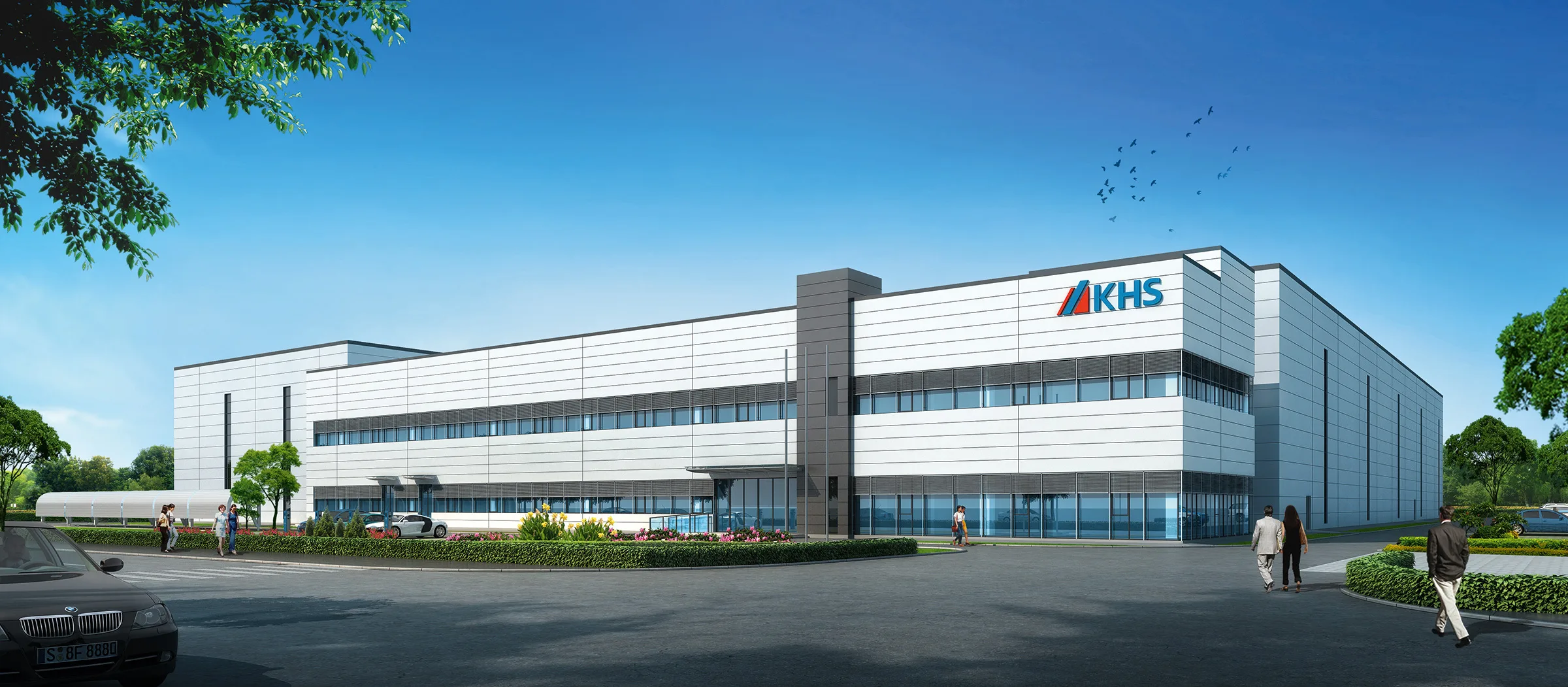
KHS’ China’s new production site is being built on a plot measuring about 20,000 square meters at the German Industrial Park in Kunshan.
Triple capacity
The machines constructed locally will primarily include DuoBlocks comprising InnoPET Blomax Series V stretch blow molders and fillers or TriBlocks which also have a labeler. Further products from the KHS product portfolio are to be added in the future. They’ll mainly be sold on the Chinese market – and beyond should the need arise. All told, Wu reckons that capacities in China will have almost tripled by 2022 compared to the output to date. Technologically speaking, both the factory and the machines comply with the latest German standards. This includes the company shouldering its ecological responsibilities as a green factory in a China which is becoming increasingly environmentally aware. Using renewable energies such as solar heat and photovoltaics or rainwater saves on resources and cuts emissions.
»We’ll be able to build machines with an output of up to 81,000 bottles per hour at our new production site.«
![]()
Managing Director, KHS China
Local service
When the factory opens in July 2021, KHS China won’t only be busy manufacturing machines but will also take on a number of other tasks. “During the initial phase we’ll be a production center which can deliver faster to our Chinese customers,” Wu stresses. “Merely by eradicating the need for shipping from Europe and customs formalities here in China we can then install and commission our lines in just three to four months instead of the previous five or six. At the same time we’ll be providing a full localized service which can supply spare parts at short notice thanks to our extensive warehouse.” In the ensuing second phase KHS China will then considerably expand its previous function as a procurement platform and second source for Purchasing in Germany; goods and raw materials bought here will be used not only for the production of the local KHS portfolio in Asia but also for projects worldwide. In a third and final phase KHS’ Chinese colleagues consider it their mission to further extend their portfolio of goods and services regarding the design of containers and system controls, for instance – yet, as Wu knows, they are still several steps away from achieving this ultimate goal.
Example 03
Digitalized supply of spare parts
One investment project that the clear majority of customers will directly profit from is KHS Connect. This digital customer center aims to facilitate and accelerate the exchange and flow of information and standardize this worldwide. The focus here is on global customers, for example, with their very specific requirements regarding worldwide access to data and information. Various cultural aspects are important here, such as the extensive use of digital media on the Asian market which customers wish to integrate into their work processes and which call for an improved online shop. The project is also geared towards employees within the KHS cosmos: the various colleagues need different information when working with their respective customers. KHS Connect ensures that the relevant information is available as and when needed – simply and globally.
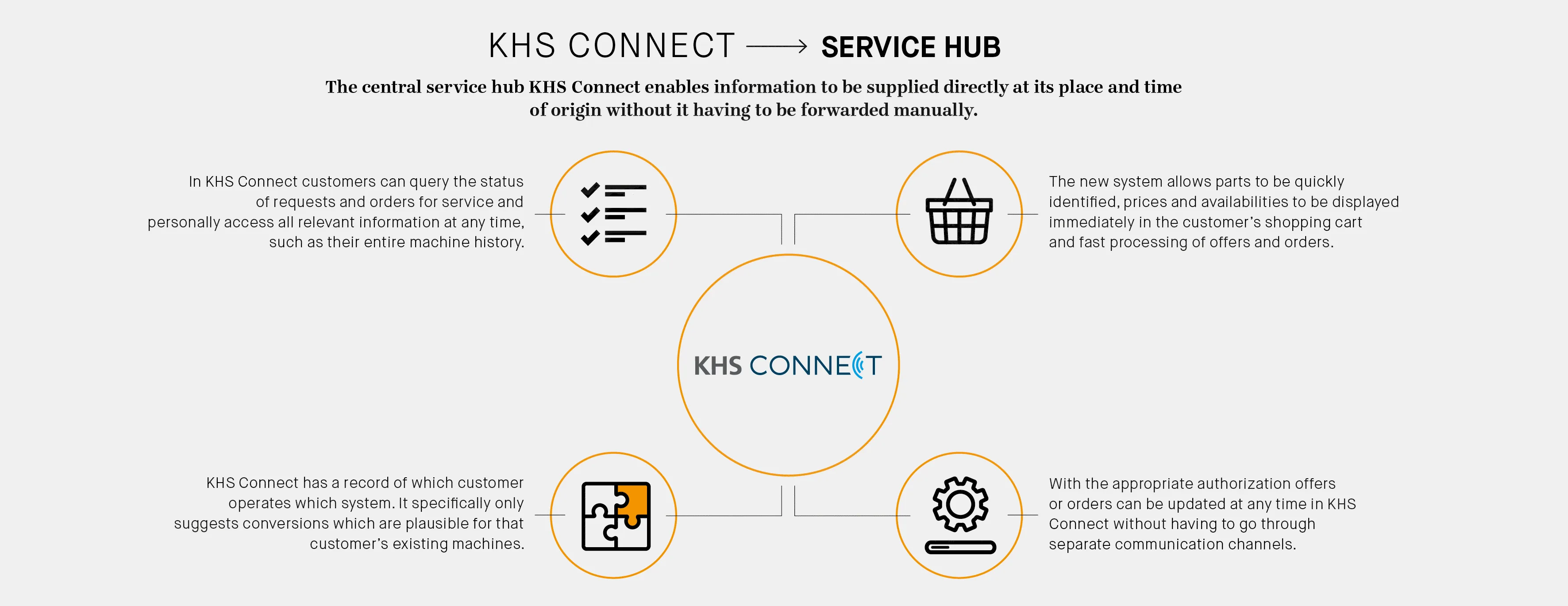
Worldwide rollout from mid-2020
“We started the project in 2017 when we set the first benchmarks and drew up the basic concept,” KHS Connect project manager Dagmar Swientek remembers. After the investment of around €5 million was approved in 2018, a suitable tool was identified and defined at the beginning of 2019. “Over the course of the last year we tested and implemented the system during global workshops and made the basic system functions, shop functions and contents available,” Swientek explains. “The first version of KHS Connect went live in December 2019. Since then we’ve been working on expanding the range of functions and optimizing the system in order to prepare for the worldwide rollout planned for the middle of 2020.” She’s extremely satisfied with the progress the project is making and is looking forward to offering customers and service personnel worldwide plenty of support in their daily work with KHS Connect.