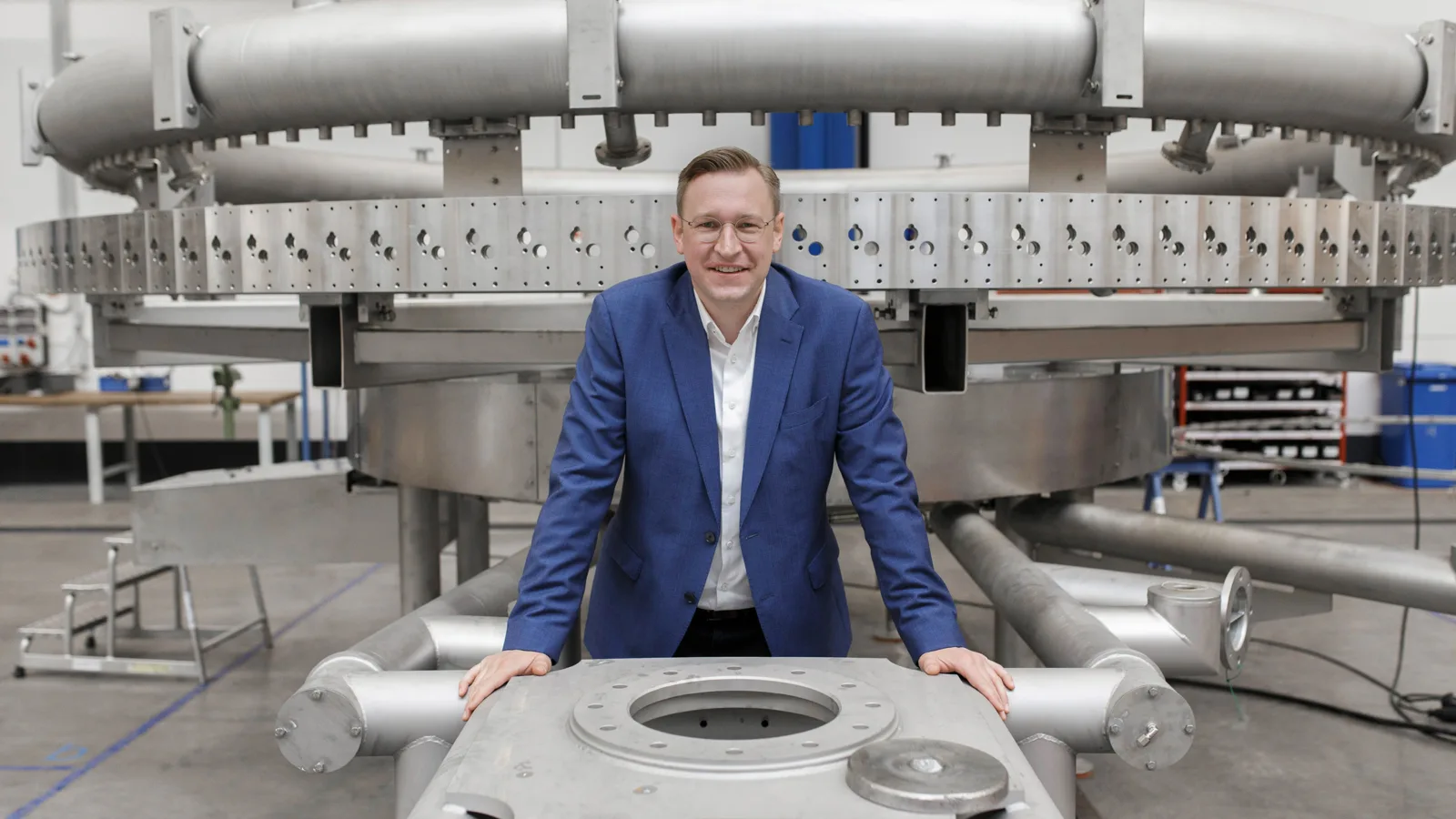
On course
As head of the Filling Technology Product Center in Bad Kreuznach Tim Steinhauer encourages and requires initiative and responsibility from his employees. For the food engineer the people at KHS and their respective potential take priority across all levels of hierarchy and national boundaries.
The Weihenstephan campus at the TU Munich is one of the top venues for anything to do with beer and milk – and the perfect place to combine science with nature and technology. This is also what Tim Steinhauer thought when he decided to study technology and biotechnology of food here. “My family runs an artisan bakery in a village close to Bad Kreuznach. This, together with the fact that I grew up in the Nahe wine region, has kept me grounded. It’s also why I’m interested in high-quality food and beverages.”
Steinhauer has been head of the Filling Technology Product Center at KHS since September 2021 – another rung up the career ladder. Parallel to his PhD in food and bioprocess engineering, in 2015 he came back from Bavaria to his old home. “I found out from a friend, who himself works for KHS, that the company was looking for graduates in my specialist discipline here. I applied and was privileged to take part in a really exciting trainee program for experts and young executives that lasted almost two years. During this time I came to know the various KHS sites and lots of colleagues the world over.” What made the biggest lasting impression on him was his three-month stay at the KHS factory in Brazil. “In some respects, this huge country wasn’t so well financially situated back then. However, the people there have the unique ability to make the best of everything and find workarounds quickly and pragmatically when things are lacking,” says Steinhauer. “In my perception, as a country of immigration Brazil appropriates everything that enters it from outside and is extremely creative. This is great fun.” From this example we could learn to simply get on with things, have the courage to try things out and handle mistakes differently, he believes. The same also applies to his working environment at KHS.
»With the local-to-local ap-proach successfully practiced by KHS we shorten our sup-ply chains and in doing so optimize our delivery times.«
![]()
Head of the KHS Filling Technology Product Center in Bad Kreuznach, Germany
Career ladder to the top
After his time as a trainee, the food engineer started working in process technology where he managed various projects for a year before taking over the Beverage Technology Department and three laboratories that chiefly provide consultancy services for customers. From 2020 Steinhauer ran the Process Technology Product Center before becoming head of Filling Technology just one year later to replace a colleague about to enter retirement. This role swap with his predecessor was supported by a special knowledge transfer process. “This ensures that expertise and knowledge of customers and suppliers are gradually transferred to the ‘new’ person in the post by the previous senior expert leaving the company. Incidentally, this is a method we don’t just apply to managerial staff but also on the shop floor where lots of older personnel are now retiring as a result of the change in our demography.”
Steinhauer had a clear aim on taking up his new position: he wanted to make his department more resistant to what’s known as VUCA*, where traditional systems of management quickly reach their limits. “The current upheavals such as climate change, digitalization and our changed world order are impacting our operations much faster than they used to and challenging us in a very different way. Flexibility and adaptability are the skills we need both now and in the future – for the latter even more so.”
* VUCA = acronym for volatility, uncertainty, complexity and ambiguity that describes the difficult general conditions in corporate management.
Specifically, Steinhauer plans to drive product development in his department in order to better meet customer demands for efficiency and flexibility. As he knows that this can only be successful in conjunction with the people he works with, he encourages flat hierarchies and defines joint fields of action together with his team, within which his employees can then creatively contribute for the good of the company. Steinhauer hopes that this style of management will speed up implementation as many people are involved in the process right from the beginning. “If I’m successful, the whole team, KHS and our customers are the winners.”
About the person: Tim Steinhauer
After finishing his degree in biotechnology and food technology and his PhD at the TUM School of Life Sciences in Weihenstephan, Steinhauer trained at KHS in his home town of Bad Kreuznach. Longer periods abroad took him to customers in Argentina and the company production site in Brazil, among other places.After holding various positions in the process technology laboratory, he was made head of this department in 2020. The 36-year-old was then appointed to run the Filling Technology Product Center in 2021.
Local-to-local approach
Internationality plays a key role in ensuring success: in the past, new technologies were developed in Germany and rolled out from here to the rest of the world. The KHS production sites in Brazil, Mexico, the USA, India and China are now involved in development work. “This works really well and boosts local confidence,” Steinhauer smiles. Not only are KHS’ development activities globally networked, however. “By standardizing our fillers and launching the corresponding product platforms we’re making decentral production easier. Our factory in Brazil builds fillers for the whole of South America, for instance, while our plants in India and China manufacture for the Asian markets. With this local-to-local approach we shorten our supply chains and in doing so optimize our delivery times. At the same time we make our transportation routes more climate-friendly and are less prone to disruption.”
When he was a little boy, Tim Steinhauer wanted to be a captain on a sail ship. He has since realized his dream – albeit on a more modest scale – by crossing the Atlantic on a smaller sailing yacht in 2013, for instance. “This was a formative experience, especially regarding the crew dynamics among people who at first were total strangers. As soon as a workable sense of trust has been built up, however, it’s amazing what a team is suddenly capable of. We mastered storms in extremely borderline situations, for example, without much needing to be said.”
At the moment, sailing and indeed any kind of travel are still slightly restricted by Steinhauer’s family situation (his toddler isn’t yet two), so the 36-year-old instead indulges in his other hobbies in the little free time he has at his disposal: hiking, cycling and – something also very close to home – singing in a local men’s chorus.