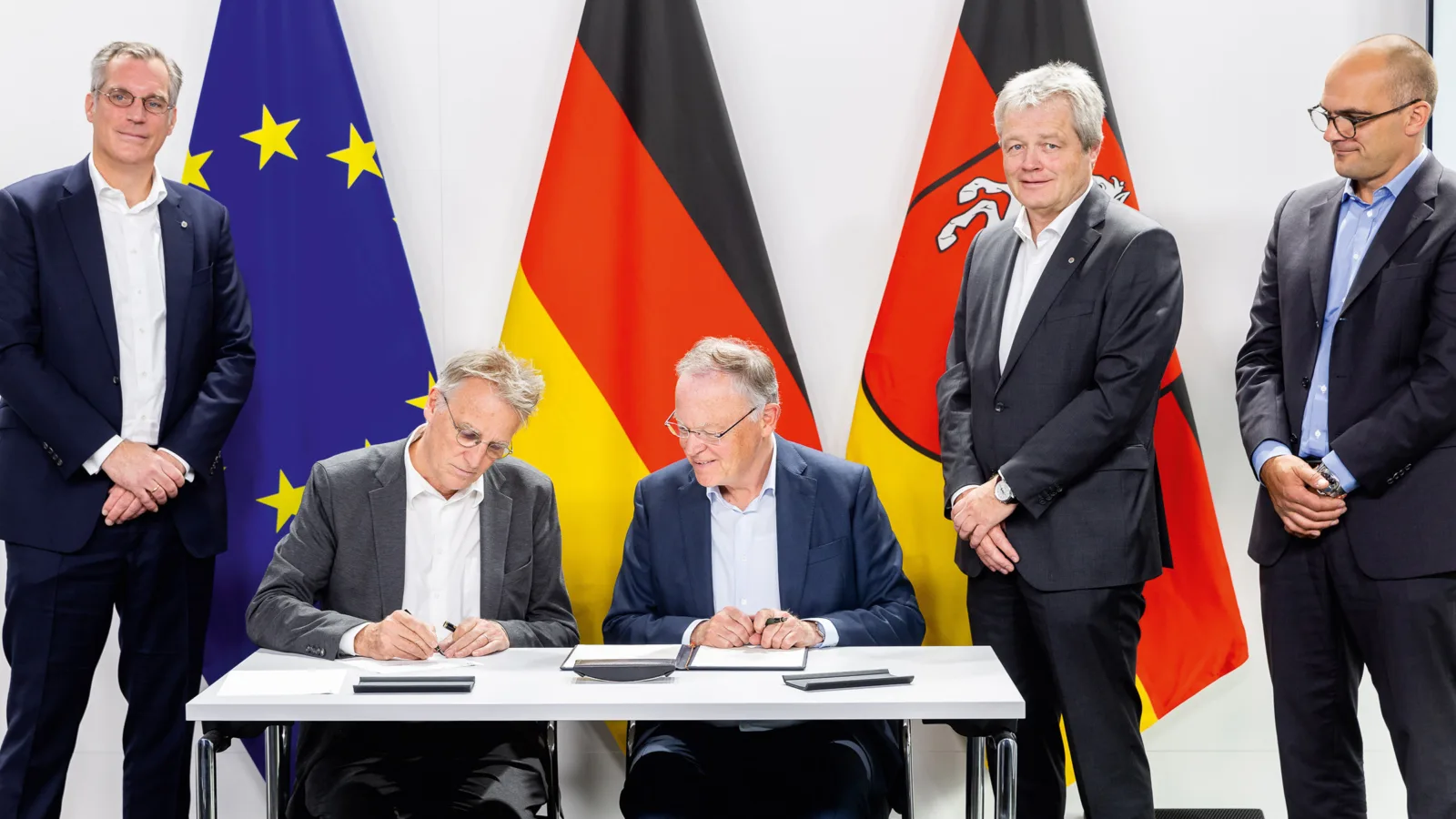
Green light for green steel
Stage one of the SALCOS® transformation program to receive €1 billion in public funding
With the commissioning of the first central plant components Salzgitter AG has taken a further key step in its SALCOS® Salzgitter Low CO2 Steelmaking transformation program designed to enable virtually CO2-free steel production. The go-ahead has now been given for the engineering, supply and erection of the first of three electric arc furnaces (EAF). The necessary technical infrastructure will first be put into place that includes dust extraction units with heat recovery, water management, electrical compensation to stabilize the network and material handling equipment for alloying agents and additives. Assembly of the EAF, an AC module with three electrodes and an annual capacity of around 1.9 million tons of crude steel, will then commence at the end of 2024. It will be capable of smelting sponge iron* and steel scrap in less than 50 minutes that will then be refined using the existing plants, cast in slabs**, rolled and processed. Production is scheduled to start at the end of 2025.
* Sponge iron = a porous product of the direct reduction of iron ore that has to be compressed or smelted before being processed to remove unwanted impurities such as slag.
** Slab = a semi-finished product in the form of a flat rectangular block created by casting and rolling steel that is usually used as a primary material for sheet and strip metal.
EU Commission permits state funding
Salzgitter AG is releasing equity funds amounting to €723 million for the first stage of its SALCOS® transformation program. In addition, public funding of €1 billion will be provided by the Federal Republic of Germany and the state of Lower Saxony. “We’re thankful for this vote of confidence from the political decision-makers,” says Gunnar Groebler, CEO of Salzgitter AG. “Substantial public funding and our own considerable capital resources enable us to further drive industrial decarbonization in Europe as a pioneer.”
The aim of SALCOS® is to convert the integrated steelworks entirely to low-CO2 crude steel production by 2033 by building two direct reduction plants and three electric arc furnaces. This will gradually replace the previous coking coal process with a new hydrogen-based method that will cut around 95% of the group’s annual CO2 emissions. This is the equivalent of eight million tons – or about 1% of Germany’s total emissions of carbon dioxide.