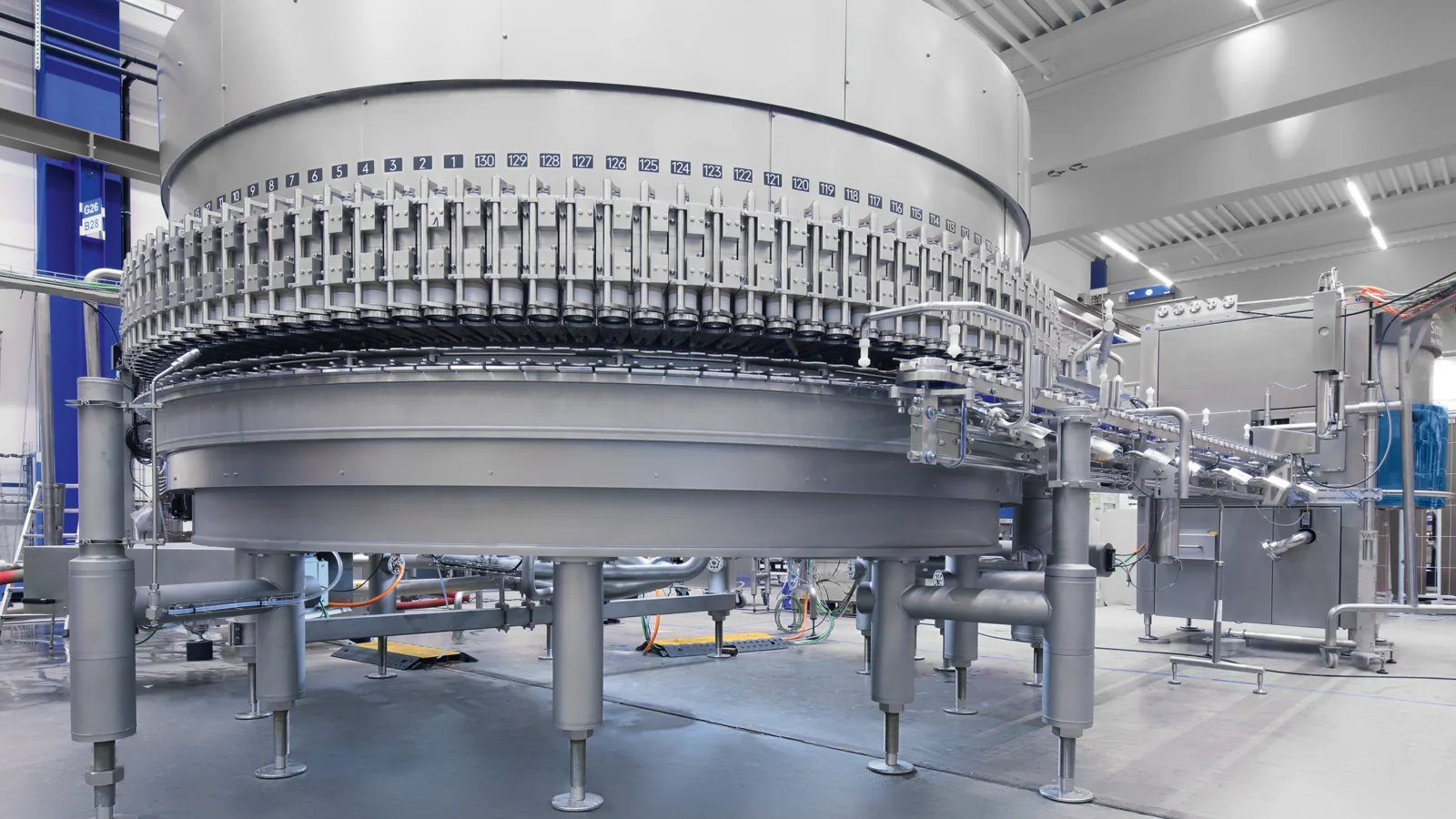
Generationswechsel bei der Dose
Mit der modularen Plattform für KHS-Dosenfüller bietet KHS neben hoher Flexibilität und optimierter Hygiene vor allem Zukunftssicherheit. Die neue Füllergeneration ist auf lange Sicht für künftige Anforderungen von Markt und Getränkeindustrie gewappnet.
Modular, konfigurier- und erweiterbar: Diese Eigenschaften zeichnen die gemeinsame Plattform der neuen Füllergeneration von KHS aus. Nachdem die Technologie in den letzten zwei Jahren sukzessive für Glas und PET umgesetzt wurde, ist sie ab sofort für Dosenfüller im Markt erhältlich. Somit können jetzt auch in dieser Behältersparte anspruchsvollste Kundenwünsche nach maximaler Anpassungsfähigkeit und Zukunftssicherheit noch besser erfüllt werden.
Mehrfache Zeitersparnis
Von der Neuentwicklung eines gemeinsamen Baukastensystems für alle Füllertypen profitieren die Abfüller gleich mehrfach: Die Teilegleichheit sorgt für bessere Verfügbarkeit, wodurch Füller schneller ausgeliefert werden können. Vor Ort können Montage und Inbetriebnahme nach vereinfachten beziehungsweise synchronisierten Standards in deutlich kürzerer Zeit erfolgen. Und die wartungsfreie Antriebstechnik verringert sowohl Reinigungsaufwand als auch -zeit. Das gleiche gilt für die Wartung, die durch den einheitlichen Aufbau der Füller vereinfacht und verkürzt wird.
Angesichts immer vielfältigerer Getränkesortimente gewinnt Flexibilität in der Abfüllung zunehmend an Bedeutung: Eine wichtige Voraussetzung dafür ist die Wahl des richtigen Materials für die Faltenbalgabdichtung an jedem Füllventil. „Mit PTFE* (Teflon) haben wir einen Werkstoff, der sich ausgezeichnet reinigen lässt“, sagt Manfred Härtel, Product Manager Filling bei KHS in Bad Kreuznach. „Damit haben unsere Ventilabdichtungen eine erheblich längere Lebensdauer. Das ermöglicht doppelt so lange Überholungsintervalle bei Wartungen.“ Hinsichtlich der wachsenden Portfolios der Kunden punkte das Material vor allem damit, dass es so gut wie keine Aromastoffe aufnehme – anders als die üblichen Dichtungen aus Elastomeren wie EPDM**, die sich bei der Produktion regelrecht wie ein Schwamm vollsaugten. Wenn beim nächsten Produkt der Abfüllsequenz ein Konzentrationsgefälle vorliegt, gibt das EPDM die Aromen wieder frei. Um diesen unerwünschten Effekt zu verhindern, muss man seine Produktion nach dem Aroma ausrichten. Dazu beginnt man die Woche zum Beispiel mit einem Mineralwasser und beendet sie mit der Abfüllung eines geschmacksintensiven Produktes wie einem Energydrink. „Mit unseren Füllventilen wird der Aromatransfer nahezu vollständig vermieden – das schenkt dem Kunden mehr Freiheit für seine Planung“, betont Härtel.
* PTFE = Polytetrafluorethylen (Teflon)
** EPDM = Ethylen-Propylen-Dien-Kautschuk
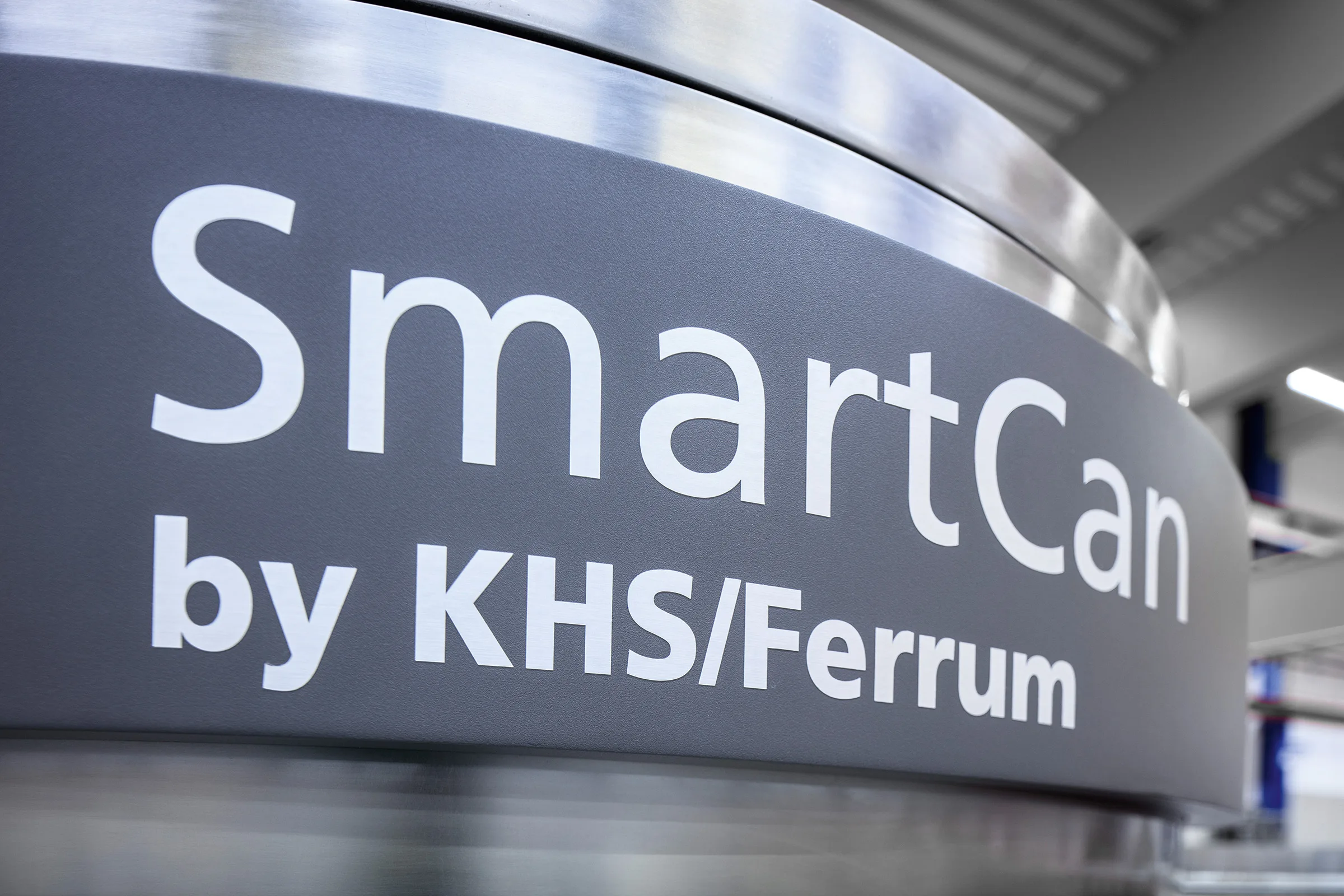
Die effiziente Blocklösung umfasst einen KHS-Füller der neuen Generation sowie einen Ferrum-Verschließer der FS-Baureihe.
Saubere Details
Ein großer Pluspunkt der neuen Entwicklung ist die weiter optimierte Hygiene: Dazu trägt maßgeblich die pneumatische Tulpenführung bei, die anders als bei der mechanisch mit Hilfe von Rolle und Kurve erfolgenden Absenkung keine Schmierung erforderlich macht. Das vermeidet neben Verschleiß vor allem Spritzwasser. Ein Highlight ist die optionale Hygieneverkleidung: Dank hochgezogener Mantelbleche sowie einer niedrigeren Decke wurde der Produktraum um das Füllerkarussell deutlich verkleinert: Dem sogenannten Donut-Prinzip folgend, umschließt die Einhausung dieses ringförmig und reduziert das Volumen des Hygienebereichs um bis zu 40 Prozent. Das sorgt für eine optimale und gezielte Umströmung der sensiblen Zone mit Sterilluft, mit der die offenen Dosen vor „unreiner“ Hallenluft geschützt werden. Zugleich reduziert sich die Zahl der benötigten HEPA-Filter***. Trotz der kompakteren Bauweise wird es für die Bediener dabei keineswegs eng: „Jede Stelle des Füllers, die im Rahmen von Wartung, Instandhaltung oder Formatwechsel einen Handgriff erfordern könnte, ist leicht zugänglich“, betont Härtel. Grundsätzlich wolle man manuelle Eingriffe auf ein Minimum begrenzen, da sie das größte Hygienerisiko darstellten. Deshalb seien möglichst viele Funktionen direkt automatisiert worden – von klar definierten Reinigungszyklen und automatischen CIP-Kappen bis hin zur bereits genannten Tulpenführung.
*** HEPA-Filter = High Efficiency Particulate Air: Schwebstofffilter zur Abscheidung von Partikeln mit einem Durchmesser kleiner 1 µm, z. B. Bakterien, Stäube oder Aerosole
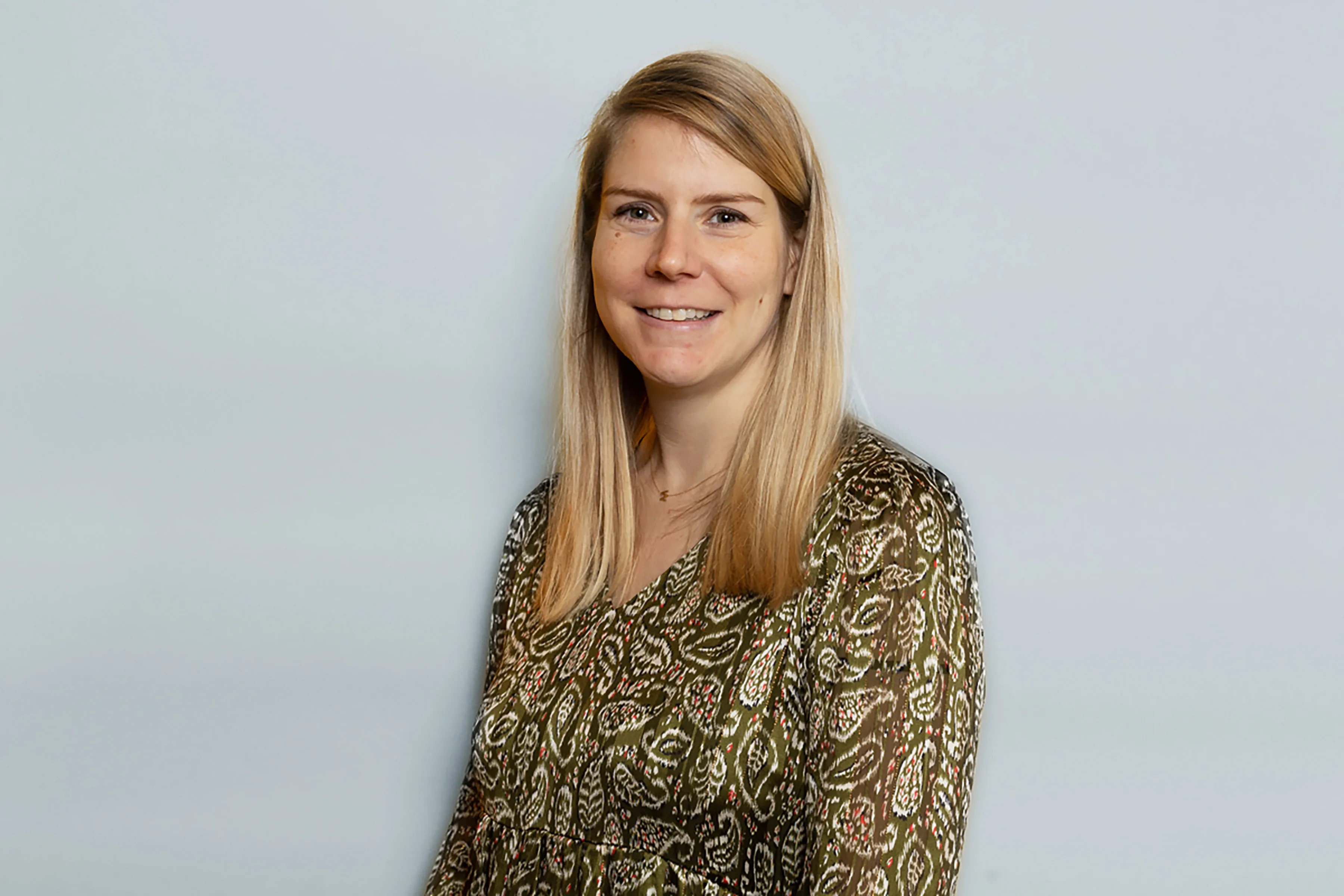
Karolien Tilkin, Group-Commercial-Capex-Managerin, Konings Drinks B.V.
Zur Person: Karolien Tilkin
Group-Commercial-Capex-Managerin beim belgischen Lohnabfüller Konings. Mit 6 Betrieben in 4 Ländern erzielte das Unternehmen 2021 einen Umsatz von 265 Millionen Euro. Als Teil einer neuen Greenfield-Anlage in Genk wurde jüngst der neue Füller-Verschließer-Block SmartCan by KHS/Ferrum angeschafft, der Ende Mai die kommerzielle Produktion aufnimmt. Der darin enthaltene Dosenfüller basiert auf der neuen Plattform.
Drei Fragen an Karolien Tilkin
Welchen Anteil haben Dosen an Ihrer Produktion und was füllen Sie darin ab?
Von rund 1 Milliarde Behälter jährlich sind circa 600 Millionen Dosen. Darin füllen wir jede denkbare Sorte von Getränk ab – still oder karbonisiert, alkoholfrei oder alkoholisch. Zugelegt hat hier zuletzt insbesondere die Kategorie der Energydrinks.
Was gab den Ausschlag für die Entscheidung für den neuen Füller-Verschließer-Block?
Als Co-Packer, der auf 18 Linien bis zu jeweils 70 verschiedene SKUs produziert, steht für uns Flexibilität natürlich an erster Stelle. Bei der Suche nach der bestmöglichen technischen Lösung punktete KHS mit seinem System für schnelle Formatwechsel. Und weil wir unseren Kunden immer 100 Prozent Qualität bieten möchten, hat uns die verbesserte Hygiene der neuen KHS-Plattform sehr beeindruckt.
Was schätzen Sie am Technologiepartner KHS besonders?
Wir arbeiten schon lange zusammen. Neben vielen Verpackungsmaschinen haben wir zum Beispiel kürzlich eine große Glaslinie im belgischen Borgloon realisiert. Mit der neuen Dosenlinie bauen wir nun unsere Beziehung zu KHS weiter aus – auch über die Installation und Inbetriebnahme hinaus. Ein wichtiger Teil unserer künftigen Kooperation ist es, Best Practices in unserem Betriebsablauf zu implementieren.
Bessere Hygiene, weniger Platzbedarf
Ein Ergebnis der immer höheren Hygienestandards ist, dass für die Sterilisation der abgefüllten und verschlossenen Dosen heutzutage kaum noch ein Tunnelpasteur benötigt wird. Die raumgreifenden Maschinen bedeuten erhebliche Investitionen sowie einen hohen Energiebedarf, der sich wiederum in beträchtlichen Betriebskosten niederschlägt. „Heute können wir dank des ausgereiften hygienischen Standards unserer Füller immer sensiblere Getränke abfüllen“, erklärt Härtel. „Inzwischen ist für viele Produktsorten eine Kurzzeiterhitzung völlig ausreichend. Die spart nicht nur enorm viel Platz, sondern verfälscht zudem aufgrund der Verweildauer der Getränke von nur wenigen Sekunden den Geschmack kaum.“
Flexibel ist die neue Plattform überdies hinsichtlich der Temperatur des Füllguts: So können beispielsweise Biere bei 20 und karbonisierte Erfrischungsgetränke bei 22 Grad Celsius warm abgefüllt werden. Dadurch bildet sich kein Kondenswasser und ein Aufweichen, Schimmelbildung oder Verunreinigung von Kartons oder Trays sind praktisch ausgeschlossen. Eine weitere Option ist die Heißabfüllung von Säften bei Temperaturen bis zu 95 Grad Celsius, ohne dass in den Dosen beim Abkühlen und Schrumpfen des Inhalts ein Vakuum entsteht und die Aluminiumwand eingedrückt wird. „Dafür tropfen wir unmittelbar vor dem Verschließen Stickstoff ein, der den Innendruck erhöht“, sagt Härtel.
Eine weitere Herausforderung, die von der neuen Füllerplattform gemeistert wird, sind schließlich die immer dünneren Wandstärken der Lightweight-Dosen und der damit verbundene geringere Topload. In diesem Zusammenhang erweist sich bei der Vorabdichtung der Behälter die pneumatische Anpressung als optimale Lösung, indem ihr Anpressdruck der jeweiligen Materialdicke und Stabilität der offenen Dosen angepasst werden kann.
„Durch ihre modulare Struktur ist die neue Füllerplattform extrem zukunftssicher“, betont Härtel. „Das Ziel, unseren Kunden mittel- und langfristig möglichst großen Handlungsspielraum einzuräumen, haben wir erreicht. Wer sich heute für einen KHS-Dosenfüller entscheidet, kann seine Maschine später einfach um zusätzliche Komponenten erweitern – ganz so, wie es der Markt oder die Produktpolitik des Getränkeherstellers erfordern.“
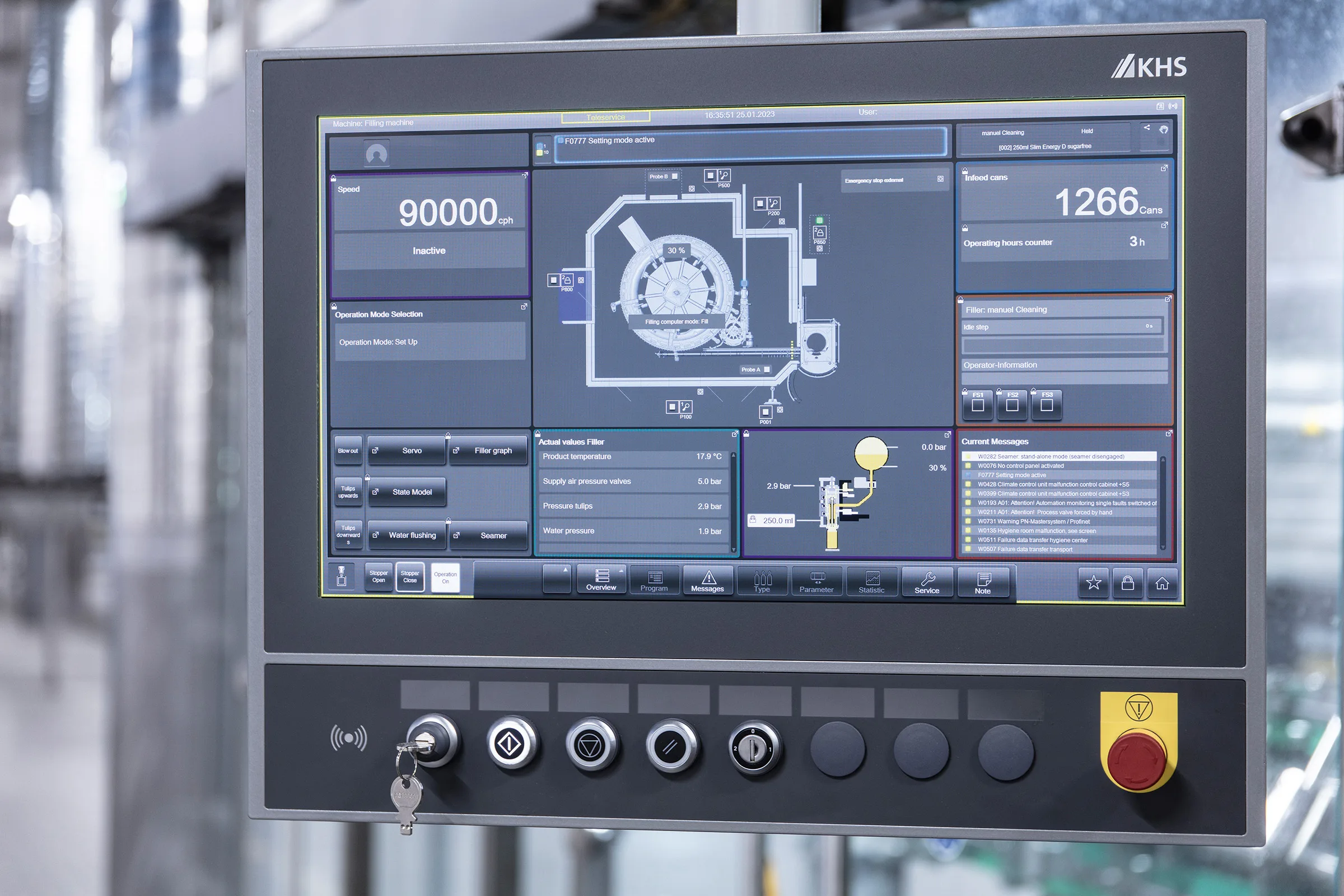
Das KHS HMI ermöglicht die gemeinsame intuitive Bedienung sowohl des Füllers als auch des Verschließers.
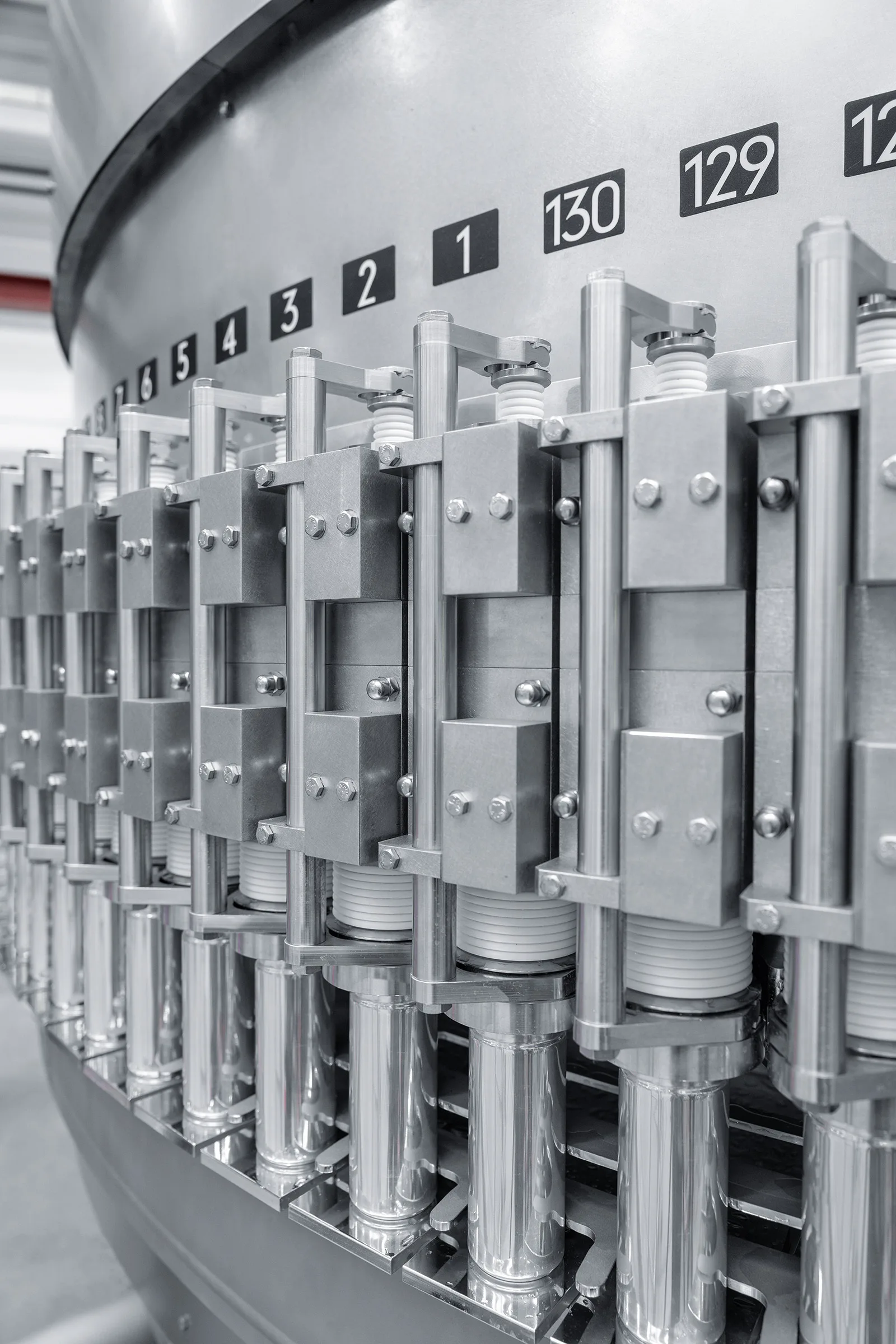
Mit der pneumatischen Tulpenführung können insbesondere Lightweight-Getränkedosen schonend verarbeitet werden.
Noch Fragen?
Manfred Härtel
Product Manager Filling, KHS GmbH, Bad Kreuznach
+49 671 852 2644 manfred.haertel@khs.com