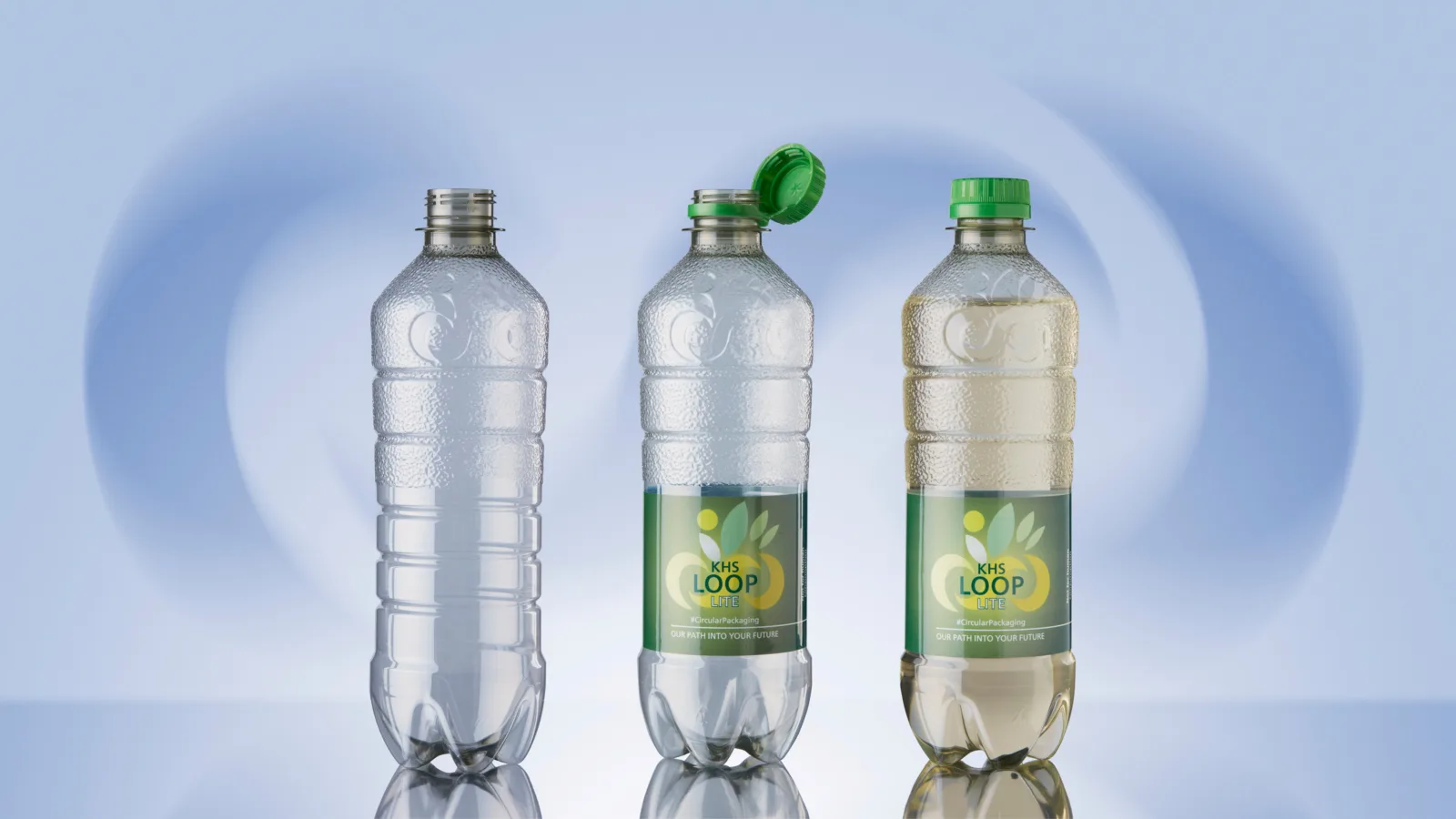
Schneller, besser, leichter
Seit seiner Einführung vor über 20 Jahren ist der Plasmax-Produktschutz eine echte Erfolgsgeschichte. Damit das so bleibt, investiert KHS in seine kontinuierliche Weiterentwicklung zu höheren Leistungen, gesteigerter Effizienz und längerer Haltbarkeit.
Rund 100 InnoPET Plasmax-Maschinen sind heute weltweit im Einsatz oder in Beauftragung. Jährlich versehen sie über 12 Milliarden PET-Flaschen mit einer hauchdünnen, glasähnlichen Innenbeschichtung: Die wegweisende Barrieretechnologie von KHS erzählt eine einzigartige Erfolgsgeschichte. Bei ihrer Markteinführung 2003 galt sie noch als exotische Lösung für sensible Nischenprodukte, die üblicherweise in Glas abgefüllt werden mussten. Heute erfreut sie sich rasant steigenden Zuspruchs besonders bei multinationalen Abfüllern kohlensäurehaltiger Erfrischungsgetränke. Dafür gibt es gute Gründe.
Das beginnt etwa mit der Leistung der Beschichtungsmaschinen: Mit einer Kapazität von 12.000 Flaschen pro Stunde gestartet, hat diese sich seitdem verfünffacht: In diesem Jahr ist die erste Anlage in Betrieb genommen worden, die bis zu 60.000 Behälter pro Stunde produziert. Und damit sei ein Ende keineswegs in Sicht, erklärt Philipp Langhammer, Product Manager Barrier Technology bei KHS: „Wir entwickeln unsere Prozesse laufend weiter, um in Zukunft noch höhere Leistungen zu erzielen.“
50 Prozent mehr Leistung
Zwar sei das Verfahren mit drei Prozessschritten und vier verschiedenen Gasen vergleichsweise anspruchsvoll. Andererseits biete es dadurch mehr Stellschrauben, um die Abläufe zu steuern und zu beschleunigen. „Gegenüber Lösungen unserer Marktbegleiter ist die Abscheidungszeit für uns kein limitierender Faktor. Wir haben die Leistung zuletzt um bis zu 50 Prozent erhöhen können – auf ein und derselben 80-Kavitäten-Plattform und mit nahezu identischer Barriereleistung.“ Es komme bei Plasmax nicht auf die Dicke der Siliziumoxidschicht an, sondern darauf, dass diese lückenlos sei. KHS gelinge das mit nur wenigen Atomlagen, die innerhalb kürzester Prozesszeit ein optimales Ergebnis erzielten.
Barriereschutz-Alternativen des Wettbewerbs auf Acetylen-Basis erfordern dagegen dickere Schichten. Deren Abscheidung dauert vergleichsweise länger und setzt damit der Leistung Grenzen. Zudem entsteht durch den Kohlenstoff eine von vielen Getränkeherstellern nicht gewünschte bräunliche Färbung der Flaschen. Die wegweisende Beschichtungstechnologie von KHS hingegen ist vollkommen transparent – ein glasklarer optischer Vorteil.
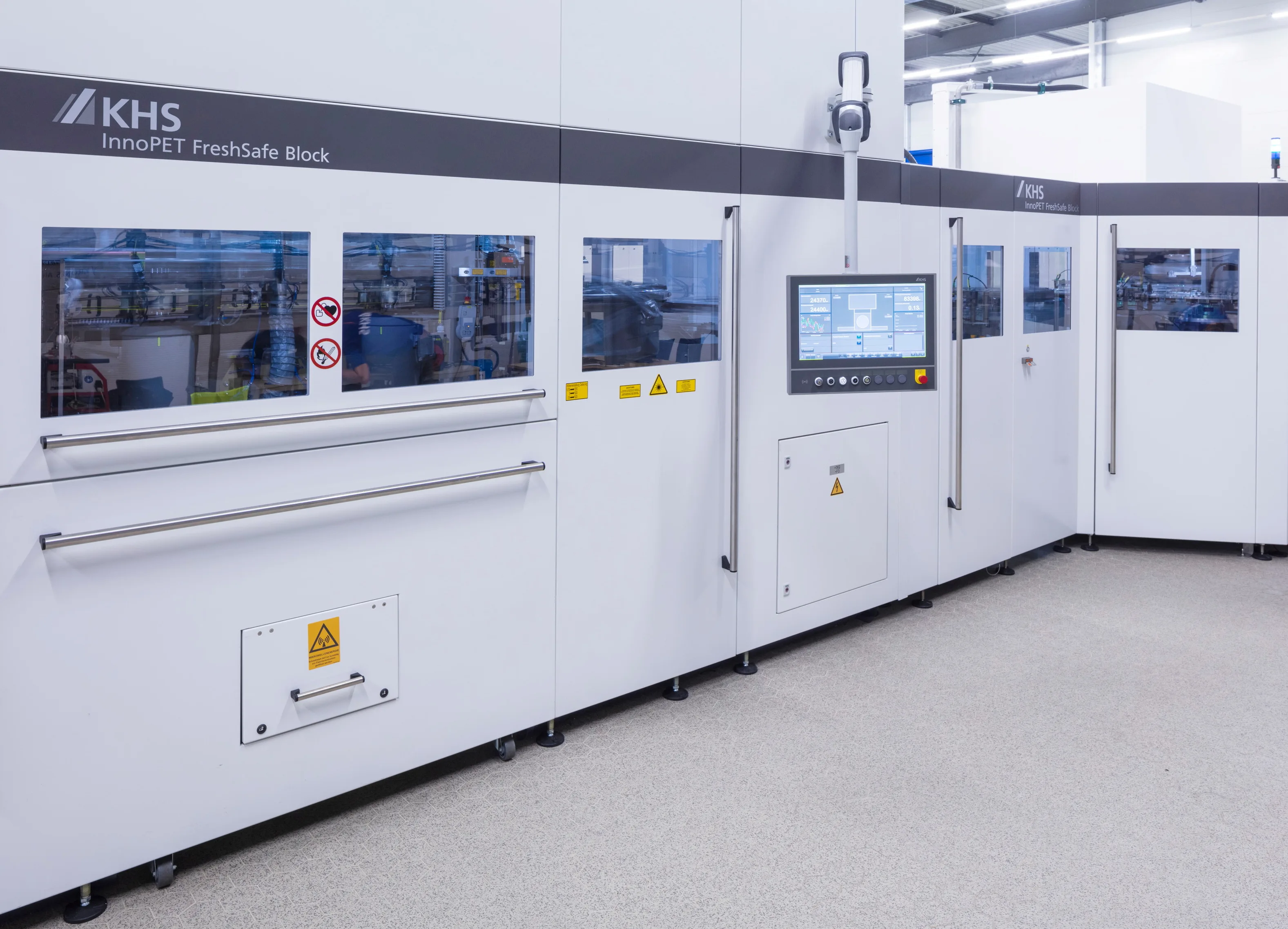
Bei VILSA-BRUNNEN im niedersächsischen Bruchhausen-Vilsen im Einsatz: Die allererste Plasmax-Maschine der neuesten Generation, eine InnoPET Plasmax 80ER.
TCO-getriebene Technologie
Für das Plasmax-Verfahren spricht außerdem, dass nach der Beschichtung keine losen Partikel in der Flasche verbleiben. Das macht den Rinser überflüssig, der bei anderen Lösungen zum Ausspülen der Behälter benötigt wird. In diesem Zusammenhang spart die KHS-Technologie damit nicht nur eine Maschine, sondern auch Ressourcen wie Wasser und Luft ein.
„Neben dem höheren Output ist das ein weiteres Beispiel dafür, dass wir mit unserem Barriereschutz einen TCO-getriebenen Ansatz verfolgen“, stellt Langhammer zufrieden fest. Im Vergleich zu den in der Herstellung aufwändigeren und weniger einfach zu recycelnden Multilayer-Flaschen betragen die Gesamtbetriebskosten bei der KHS-Lösung nur rund die Hälfte.
Komplexität reduziert
„Kostensparend wirken sich darüber hinaus die längeren Standzeiten und Wartungsintervalle etwa von Ventilen aus“, erklärt Langhammer. „Wir investieren kontinuierlich, um Komplexität zu reduzieren. Dazu zählt etwa das Einsparen von Verschleißteilen wie Dichtungen. Zugleich arbeiten wir gerade gemeinsam mit einem unserer Zulieferer daran, Pumpen zu entwickeln, die sich selbst reinigen können und somit ebenfalls längere Standzeiten erzielen.“
„Mit Plasmax ist KHS der Enabler für günstige, kleine Verpackungsformate mit dem bestmöglichen Schutz.“
![]()
Product Manager Barrier Technology bei KHS
Schlüsselvorteil lange Haltbarkeit
Natürlich seien die Gesamtbetriebskosten für Getränkehersteller hochrelevant, betont Langhammer. „Für unsere Kunden aber steht neben der Technologie im Vordergrund, dass diese eine komplett neue Verpackungslösung generiert: KHS ist hier der Enabler für günstige, kleine Verpackungsformate mit dem bestmöglichen Schutz.“ Gerade diese seien aufgrund des Oberfläche-Volumen-Verhältnisses sehr kritisch: So wäre zum Beispiel ein Softdrink in einer gänzlich unbeschichteten 200-Milliliter-Flasche weniger als einen Monat haltbar. Speziell Märkte mit trockenen, heißen Sommern und saisonalen Nachfragespitzen könnten so kaum versorgt werden.
„Mit unserer Barrieretechnologie erreichen wir demgegenüber je nach Spezifikation inzwischen eine Haltbarkeit von einem halben Jahr. Dies ermöglicht Abfüllern, frühzeitig ausreichend hohe Lagerbestände vorzuproduzieren und rechtzeitig in die Regionen zu liefern, wo sie gebraucht werden. Das erspart zum einen Extraschichten während der Hauptsaison. Zum anderen können aufgrund der Möglichkeit zur Bevorratung auf einer KHS-Linie jährlich rund 30 Prozent mehr Getränke als auf einer Standard-PET-Linie ohne Beschichtung produziert werden.“
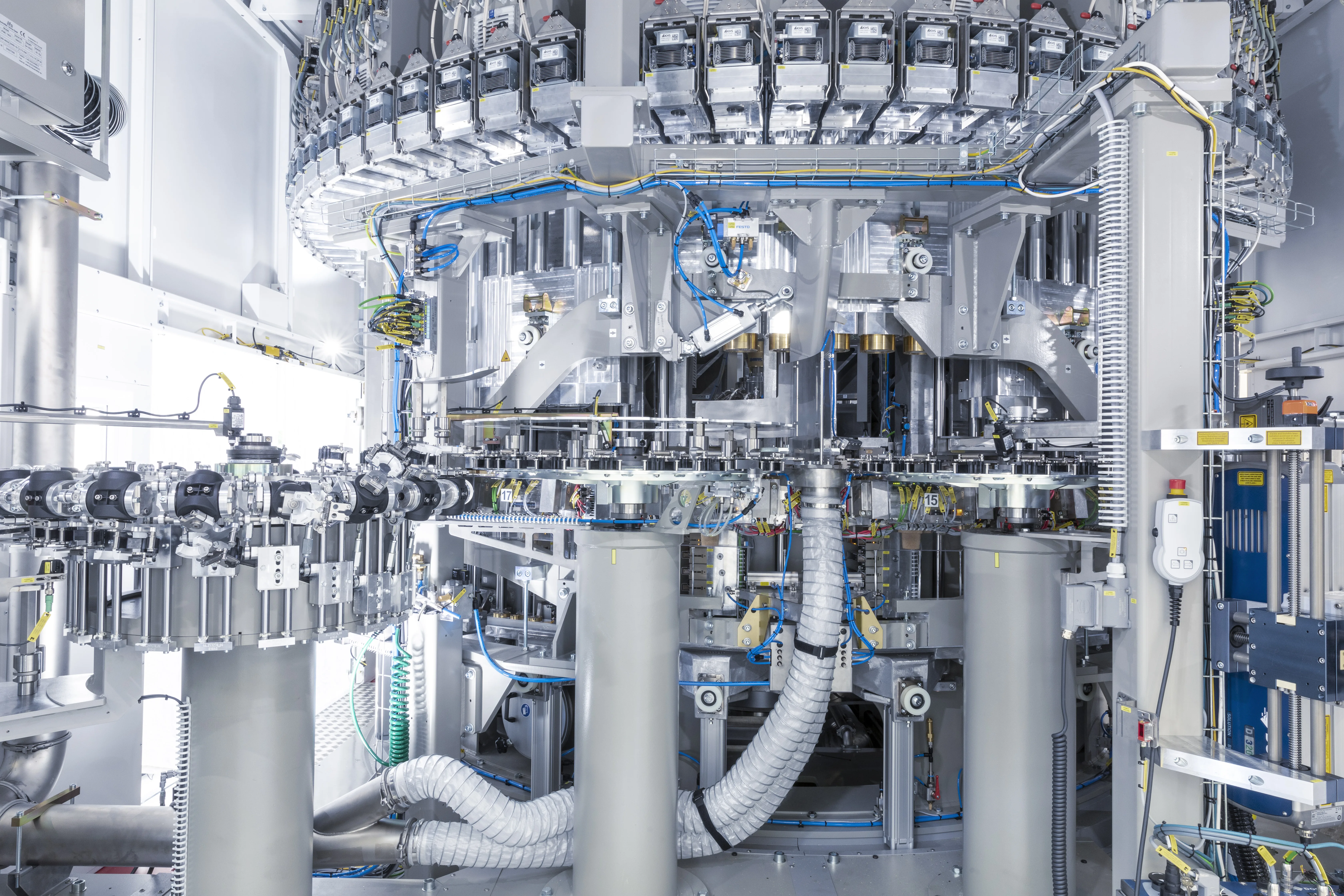
Nach erfolgter Beschichtung im Plasmax-Modul werden die Flaschen in einer Wendeeinheit gedreht, bevor sie an den Füller übergeben werden.
Alleskönner
Kohlensäurehaltige Erfrischungsgetränke und Wasser bewahrt die Universalbarriere einerseits vor allem als passiver Schutz vor CO2-Ausgasung. Bei sensitiven Getränken wie Fruchtsäften, Energydrinks, Tees, Wein oder Bier geht es andererseits darum, einen Sauerstoffeintrag in die Flasche zu verhindern, unter dem die Qualität der Produkte leidet.
Für den aktiven Schutz bieten Wettbewerber sogenannte Scavenger an. Dabei handelt es sich um Additive, die als Barriereschutz im Kunststoff homogen verteilt sind. Inzwischen lassen sich Scavenger-Flaschen zwar einfacher recyceln als Multilayer-Behälter. „Wir beobachten allerdings, dass sich die Additive mit Rezyklat nicht gut vertragen“, sagt Langhammer. „Das ist eine Einschränkung, die es bei Plasmax nicht gibt. FreshSafe-PET-Behälter können sowohl Flasche-zu-Flasche recycelt als auch zu 100 Prozent aus rPET hergestellt werden. Deshalb sprechen wir hier von einer vollständig kreislauffähigen Barrieretechnologie.“
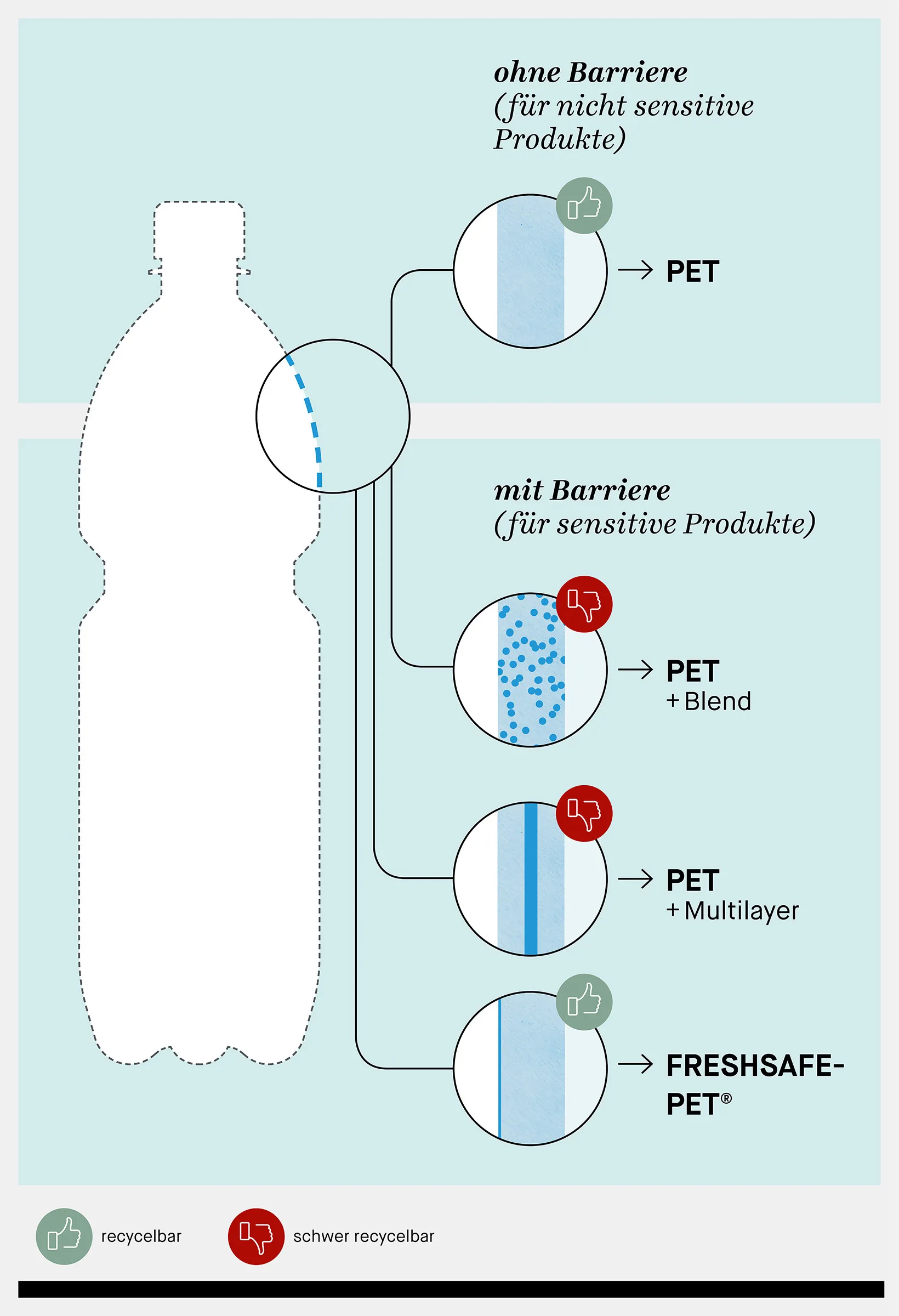
Recycelbarkeit – PET-Einwegflaschen: PET-Flaschen ohne Barriereschutz (für nicht sensitive Produkte) liefern im Recyclingprozess 100 Prozent sortenreines PET. Bei Kunststoffflaschen mit Barriereschutz (für sensitive Produkte) lassen sich die Zusätze kaum vom PET trennen – außer bei FreshSafe-PET®. Hier wird die Schutzschicht im Recyclingprozess einfach abgewaschen.
In die Spur gebracht
Parallel zu den wachsenden Leistungen hat sich die KHS-Technologie vor allem hinsichtlich ihrer Block- und Linientauglichkeit weiterentwickelt: „Mit unseren InnoPET FreshSafe Blocklösungen sind wir vollständig in das Gesamtportfolio integriert“, bestätigt Langhammer. „Plasmax ist entweder verblockt mit unserer Streckblasmaschine zum InnoPET FreshSafe Block oder als InnoPET FreshSafe TriBlock zusätzlich mit integriertem Füller verfügbar.“
Um die stark wachsende Nachfrage nach seiner bewährten Barrieretechnologie zu bedienen, hat der Dortmunder Systemanbieter die Kapazität sukzessive hochgefahren, die Bauzeiten reduziert und den Materialfluss optimiert. So ist sichergestellt, dass pro Jahr noch mehr Beschichtungsmaschinen und FreshSafe Blöcke gebaut werden können. „Schließlich wollen wir ja nicht, dass unserer fortgesetzten Erfolgsgeschichte irgendwas im Weg steht“, resümiert Langhammer.