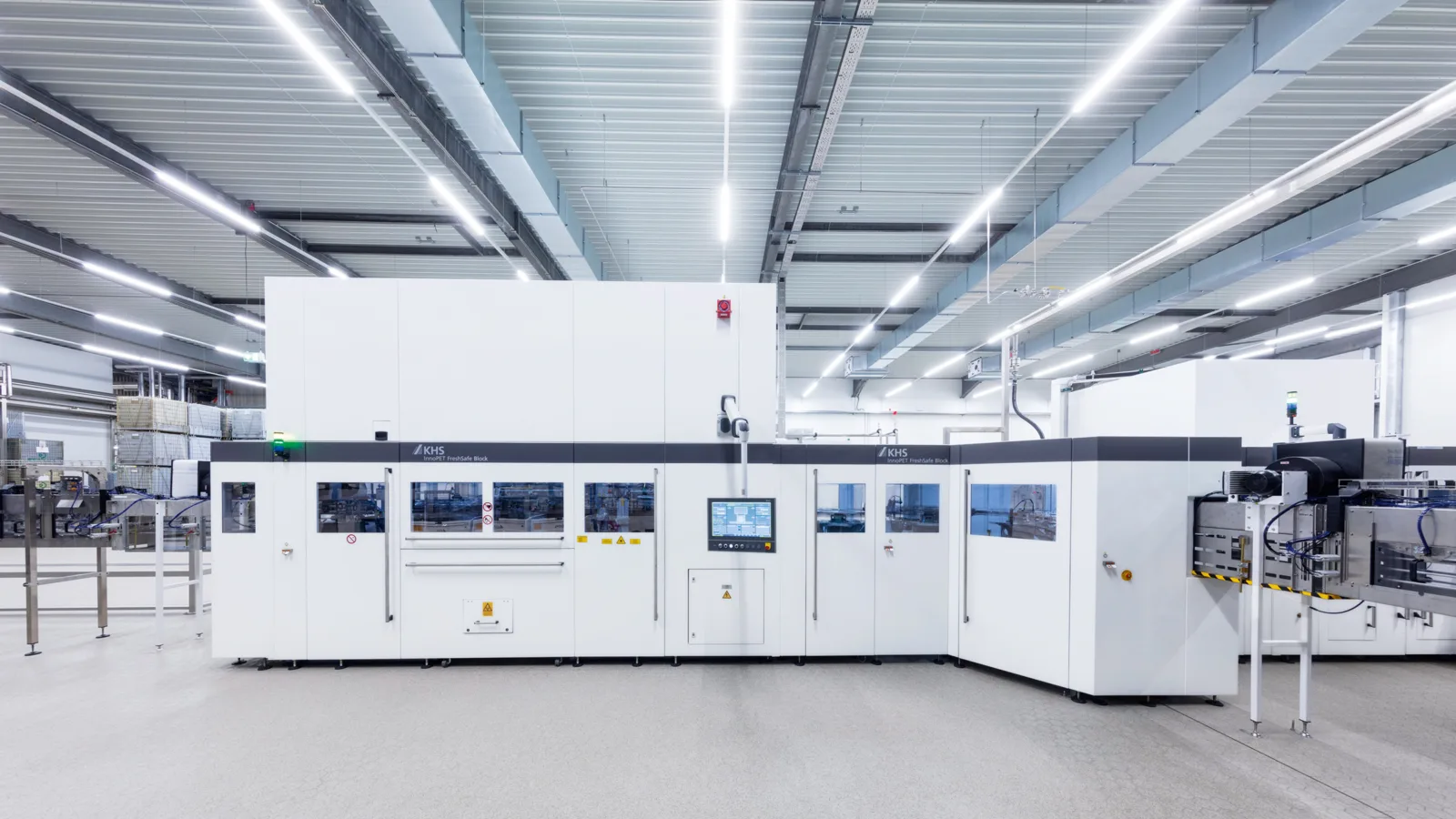
Modelo exitoso
Plasmax, la innovadora tecnología de recubrimiento de KHS continúa su trayectoria de éxito: una nueva generación de máquinas impresiona con un rendimiento superior, una calidad aún mejor, más flexibilidad y eficiencia mejorada.
La única botella de plástico hasta ahora que combina una protección de producto altamente efectiva con una reciclabilidad del 100 % de sin mezcla: esto se debe a una tecnología de recubrimiento revolucionaria, que fue desarrollada por KHS hace aproximadamente 20 años y que ahora está lista para el mercado. Hasta que la industria de bebidas se sumó a esta tendencia debido a los crecientes esfuerzos de sostenibilidad y a la demanda de envases reciclables, se necesitó cierta labor de persuasión. El esfuerzo ha valido la pena: ahora, una gran cantidad de empresas envasadoras nacionales e internacionales están adoptando esta tecnología, lo que ha llevado al proveedor del sistema a aumentar su capacidad en su ubicación en Hamburgo para poder satisfacer la creciente demanda.
La idea detrás de esta historia de éxito es recubrir las botellas de PET por dentro con una capa de vidrio extremadamente delgada y químicamente pura, que protege contra la entrada de oxígeno yla pérdida de CO2. De esta manera, se preserva el sabor y se prolonga la vida útil, similar a una botella de vidrio, pero con el peso más ligero y la mayor resistencia de una botella de plástico.
El concepto de la tecnología de barrera no es nuevo. Sin embargo, la competencia utiliza materiales de mezcla o multicapa para ello, lo que dificulta o hace imposible el posterior reciclaje de botella a botella en PET puro. Los materiales compuestos apenas se pueden separar entre sí y forman una mezcolanza de materiales secundarios y compuestos químicos. Diferente que con el sistema de recubrimiento FreshSafe-PET de KHS: aquí, el recubrimiento interior puede lavarse completamente durante el proceso de reciclaje, lo que permite un reciclado del 100% de botella a botella. Esto lo han confirmado tanto la EPBP (Plataforma Europea de Botellas PET) como la APR (Asociación de Recicladores de Plásticos) de Estados Unidos. Además, la idoneidad de los alimentos ha sido oficialmente confirmada por la FDA (Administración de Alimentos y Medicamentos) de Estados Unidos, entre otros, y más recientemente por la Certificación de Seguridad de la Comisión Nacional de Salud de China.
A lo largo de los años, KHS ha mejorado continuamente la nueva tecnología y ahora la ha llevado al siguiente nivel con un desarrollo posterior actualizado. Los dos objetivos principales fueron aumentar el rendimiento por un lado y la eficiencia por el otro.
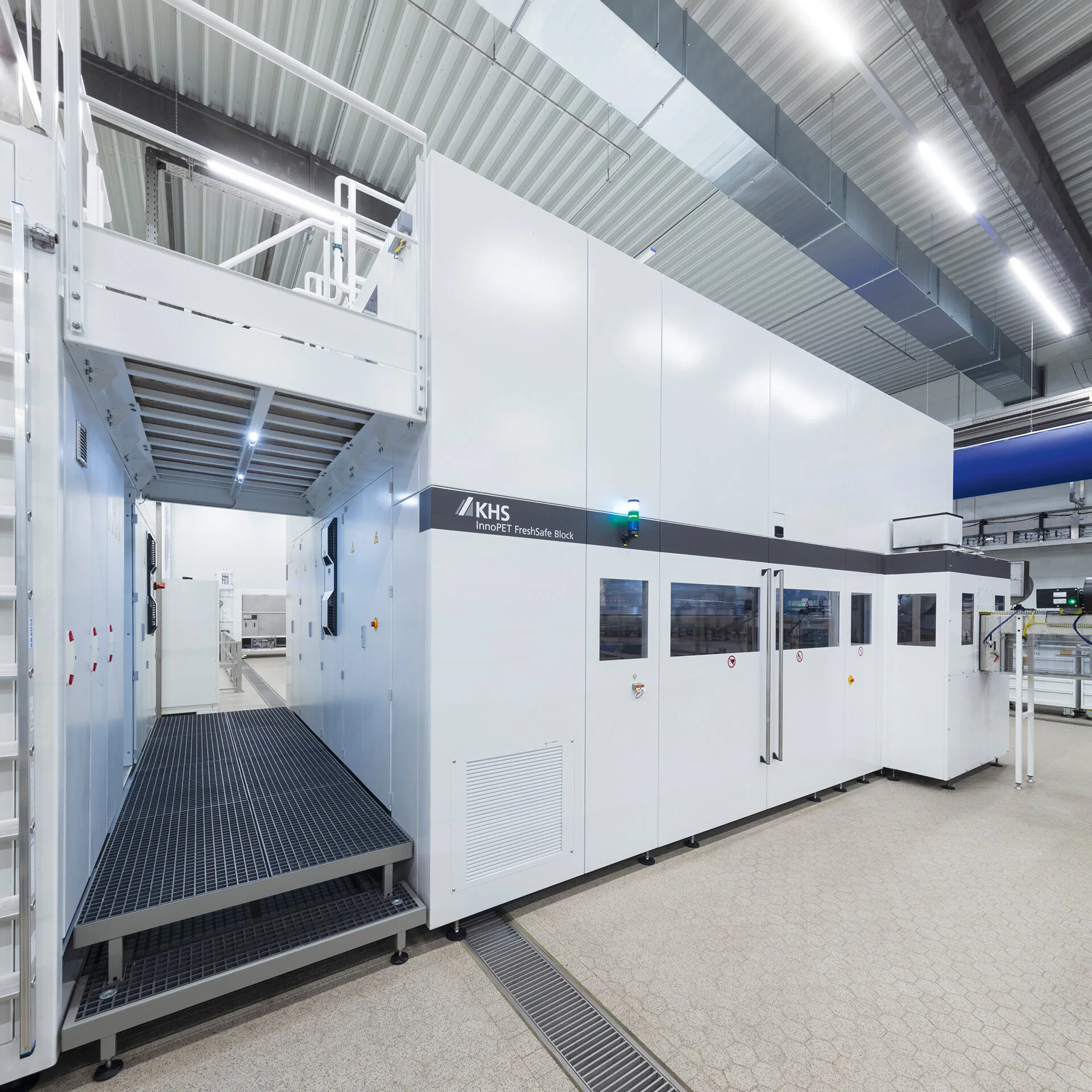
La primera máquina Plasmax de última generación está en la planta de agua mineral alemana VILSA, donde protege su agua premium de influencias externas y preserva su sabor.
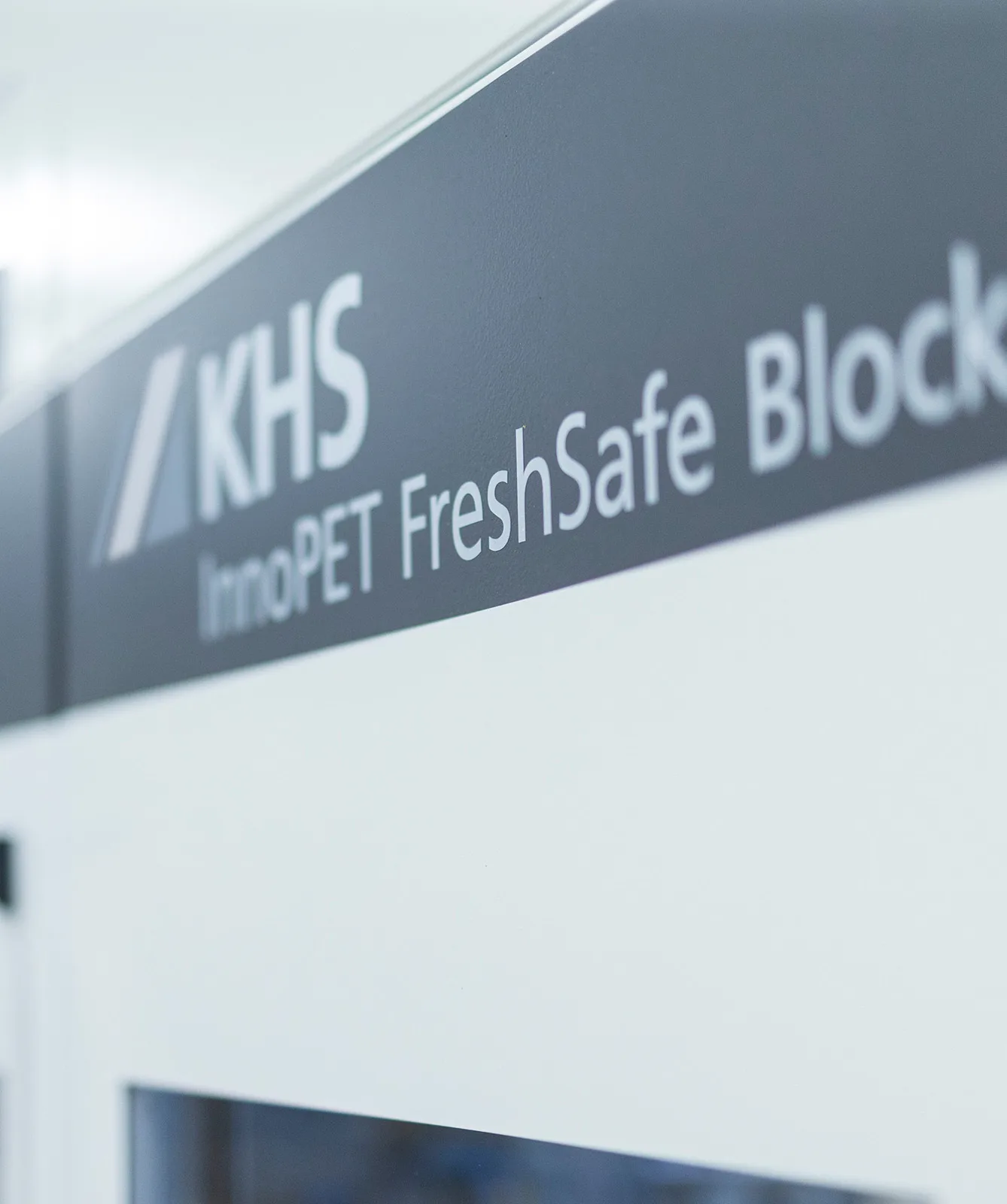
Gracias a una serie de mejoras en el proceso, el bloque InnoPET FreshSafe ahora logra un aumento significativo en el rendimiento.
De un Vistazo
Innopet Plasmax Serie E
InnoPET Plasmax 48ER
Capacidad
Hasta 24.000 botellas por hora
Tamaño de envase
100 ml hasta 1,5 l
InnoPET Plasmax 80ER
Capacidad
Hasta 40.000 botellas por hora
Tamaño de envase
100 ml hasta 1,5 l
InnoPET Plasmax 80ES
Capacidad
Hasta 48.000 botellas por hora
Tamaño de envase
100 ml hasta 600 ml
Clases de rendimiento alternativas
Gracias a la generación de máquinas más desarrollada, que reemplaza a las series anteriores 20Q y 20L, la variante InnoPET Plasmax 80ES ahora puede recubrir botellas PET a una velocidad de hasta 48.000 unidades por hora. La primera máquina Plasmax de última generación está en la envasadora de agua mineral alemana VILSA (ver recuadro “Tres preguntas a...”).
Las mejoras en el rendimiento son atribuibles a las mejoras en el proceso implementadas por los expertos de KHS. Por ejemplo, dentro de la solución en bloque FreshSafe-PET TriBlock, la entrada y salida de la máquina de recubrimiento se han elevado a la misma altura que la de la máquina de moldeo por estirado-soplado y la llenadora. Esto elimina la necesidad de la rueda de elevación, que anteriormente elevaba los envases 30 centímetros hasta el módulo de recubrimiento. Además, la manipulación de las botellas se ha simplificado y reforzado, todo ello como preparación para velocidades aún más altas, según lo anticipa Philipp Langhammer, Gerente de Producto de Tecnología de Barrera en KHS.
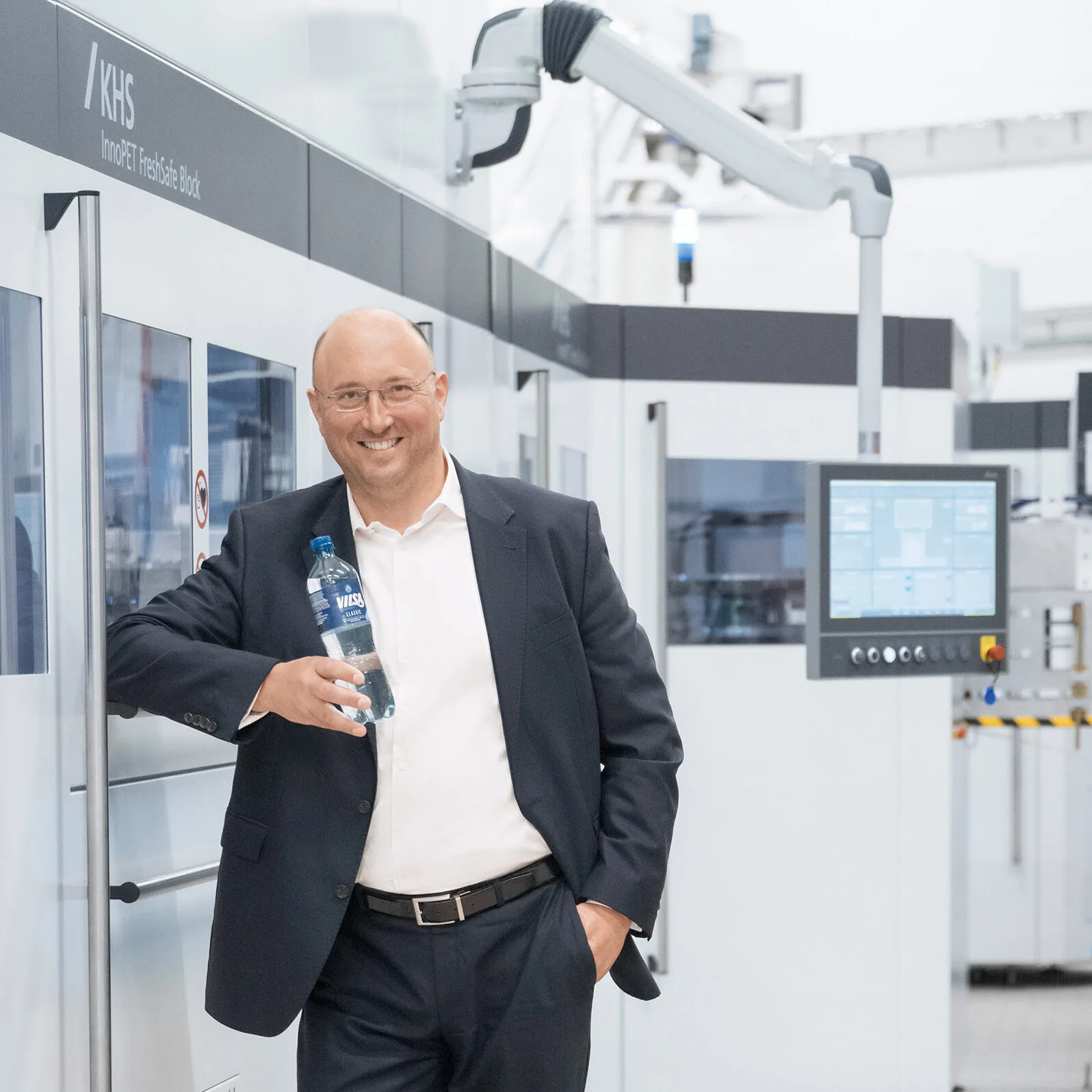
Henning Rodekohr, Socio director del Grupo VILSA, que es la primera fuente de agua mineral alemana que apuesta por la innovadora protección de productos de KHS. El primer bloque InnoPET FreshSafe de última generación Plasmax se encuentra en la planta envasadora de Bruchhausen-Vilsen, Baja Sajonia.
Tres Preguntas a Henning Rodekohr
¿Qué significado tiene la sostenibilidad para VILSA?
Como fuente mineral, le debemos mucho a la naturaleza y nos gustaría devolverle algo. Por lo tanto, la protección sostenible de nuestras fuentes es una preocupación fundamental para nosotros. Nuestra certificación de agua mineral orgánica y nuestro compromiso con el desarrollo de objetivos climáticos basados en la ciencia de acuerdo con el estándar de cero emisiones netas de la Science Based Targets Initiative (SBTi) garantizan que cumplimos con los límites más estrictos y los más altos estándares de sostenibilidad específicos del sector en el mercado alemán.
¿Por qué utiliza la tecnología de barrera Plasmax para su agua mineral?
Nuestros consumidores confían en VILSA para brindarles un producto premium naturalmente puro. Para cumplir esta pretensión, debemos proteger eficazmente nuestro valioso producto de las influencias externas y garantizar su sabor de forma fiable. Por eso empleamos envases que combinen los más altos estándares de sostenibilidad con la mejor protección posible del producto.
¿En qué medida le convence Plasmax en materia de sostenibilidad?
Todas nuestras botellas no retornables están hechas de PET 100 % reciclado y reciclable. Por lo tanto, para la protección de nuestros productos es lógico que confiemos en una tecnología de barrera que no solo ofrezca las mejores propiedades protectoras, sino que también permita un reciclaje 100 % sin mezcla.
“Con nuestra incursión en clases de rendimiento más altas, queremos llegar especialmente a las grandes empresas envasadoras de refrescos gaseosos, que necesitan proteger sus bebidas de la pérdida de CO2, sobre todo en botellas más pequeñas”, dice Langhammer. “Después de todo, la superficie es proporcionalmente mayor cuanto menor es el volumen del recipiente. Y, en consecuencia, aumenta el riesgo de que el dióxido de carbono se escape a través de la pared de plástico o que entre oxígeno”.
De acuerdo con los requisitos individuales de los clientes, la plataforma de máquinas modular se puede configurar para diferentes velocidades. Especialmente para proveedores de nicho, empresas de envasado más pequeñas o convertidores, que están más interesados en un rango de rendimiento bajo a medio, la InnoPET Plasmax 48ER estará disponible a partir de principios de 2025. Podrá recubrir hasta 24.000 botellas por hora.
Además de las diferentes clases de rendimiento, se ha puesto un énfasis especial en una mayor flexibilidad: por ejemplo, KHS ha equipado la solución en bloque con una rueda de bypass para empresas recién llegadas al sector que ofrecen tanto productos sensibles como aquellas que no requieren protección adicional del producto. Esto permite que las botellas correspondientes sean dirigidas directamente desde la máquina de moldeo por estirado-soplado hacia la llenadora, evitando el módulo de recubrimiento.
“Una plataforma modular común y una complejidad reducida de piezas y tareas de mantenimiento garantizan una eficiencia aún mayor”.
![]()
Gerente de Producto de Tecnología de Barrera, KHS
Véase en nuestro vídeo
cómo el grupo VILSA utiliza KHS FreshSafe PET para una protección máxima del producto de agua de primera calidad.
Mayor capacidad de evacuación
En cuanto al proceso de recubrimiento en sí, este desarrollo destaca especialmente por su mayor capacidad de evacuación: reduce el requisito de estabilidad al vacío de los envases. En el contexto del peso ligero, así es posible ahorrar PET: “un cliente que antes necesitaba una botella PET de 22 gramos para un almacenamiento de 100 días, puede reducir el peso a solo 14 gramos gracias a la última tecnología de recubrimiento FreshSafe-PET y, al mismo tiempo, duplicar el plazo de validez”, explica Langhammer. “Para la empresas envasadoras de bebidas que necesitan fabricar productos para la temporada alta con anticipación, esto conlleva dos ventajas: por un lado, pueden ahorrar hasta una tercera parte de plástico, y por otro lado, se desperdician menos bebidas porque su fecha de vencimiento ha caducado”.
Eficiencia aún mayor
También se realizaron importantes optimizaciones en términos de aumento de la eficiencia. “Las principales novedades aquí son la creación de una plataforma modular común y la reducción de la complejidad de piezas, componentes y tareas de mantenimiento”, señala Langhammer. “Por ejemplo, se utilizan la mayor cantidad posible de piezas idénticas para diferentes rangos de rendimiento”.
Un diseño mejorado y más flexible de la nueva generación de máquinas InnoPET-Plasmax permite una integración más sencilla del bloque en el área de producción gracias a un tamaño reducido: por un lado, la profundidad de la máquina se ha reducido en un 25 %, y por otro lado, dependiendo de las condiciones espaciales, la máquina de moldeo por estirado-soplado, el módulo de recubrimiento y la llenadora pueden colocarse en la sala de envasado con un diseño en forma de L, U o V.
Costes de mantenimiento reducidos
Además de mayores rendimientos, una calidad de recubrimiento aún mejor y más flexibilidad, la nueva serie ofrece a los fabricantes de bebidas una ventaja económica sólida en términos de costes operativos: “Hemos logrado reducir los costes de mantenimiento”, explica Langhammer. “Eso es, por supuesto, un criterio importante al tomar la decisión de elegir nuestras máquinas”. Entre las mejoras basadas en la tecnología probada se encuentra un acceso simplificado a todas las válvulas de gas del proceso. El rediseño del sistema de soporte de lanzas ahorra pistones y, por lo tanto, reduce el número de juntas y, consecuentemente, el esfuerzo y los costes de servicio. Finalmente, un nuevo tipo de bomba de vacío ayuda a reducir los costes. “Al mejorar aún más la vida útil de nuestras piezas de mantenimiento, podemos ampliar los intervalos de mantenimiento”, afirma satisfecho Langhammer.
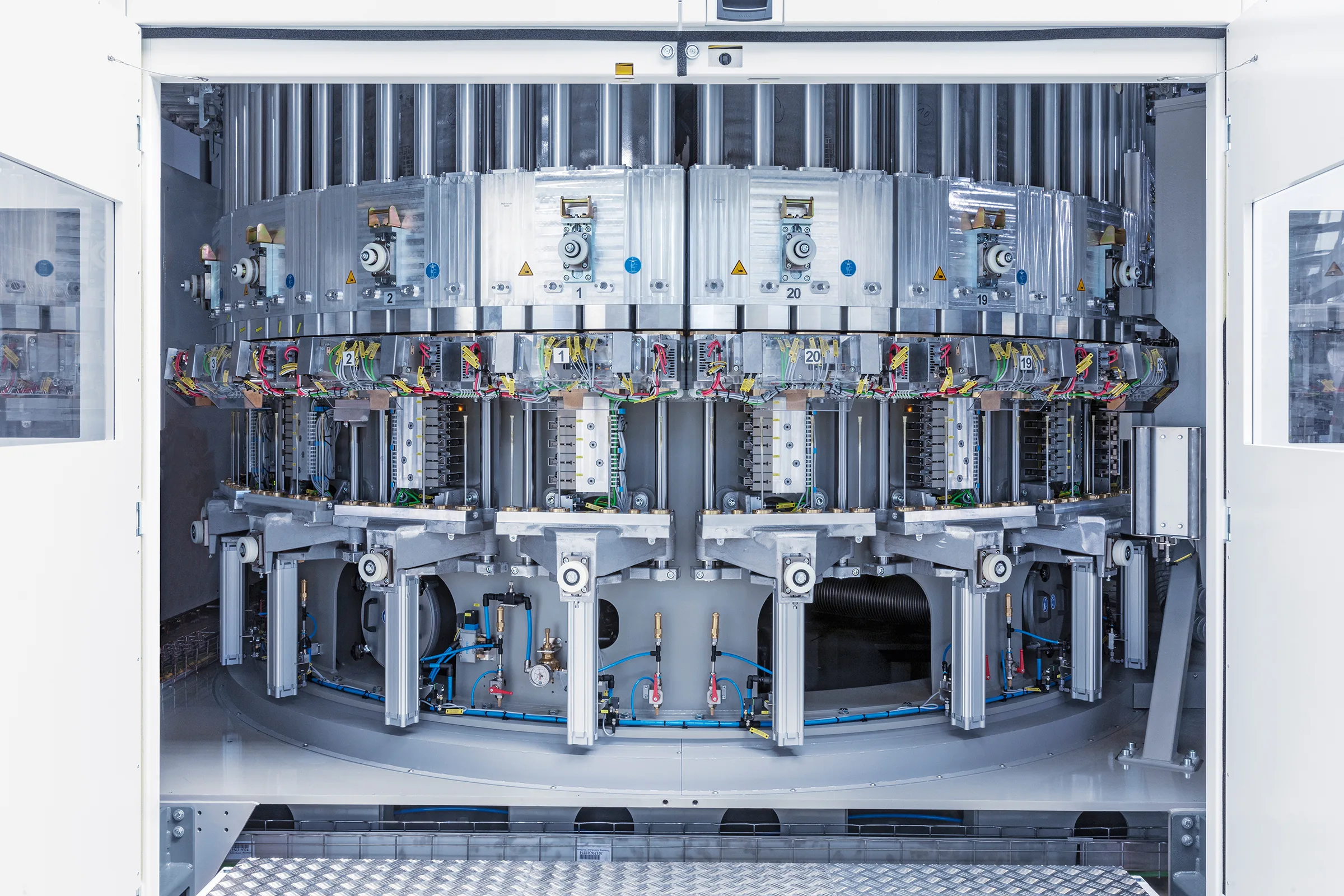
Un número reducido de piezas y una accesibilidad optimizada a los componentes principales de las estaciones de recubrimiento aumentan la disponibilidad y reducen los costes de mantenimiento.