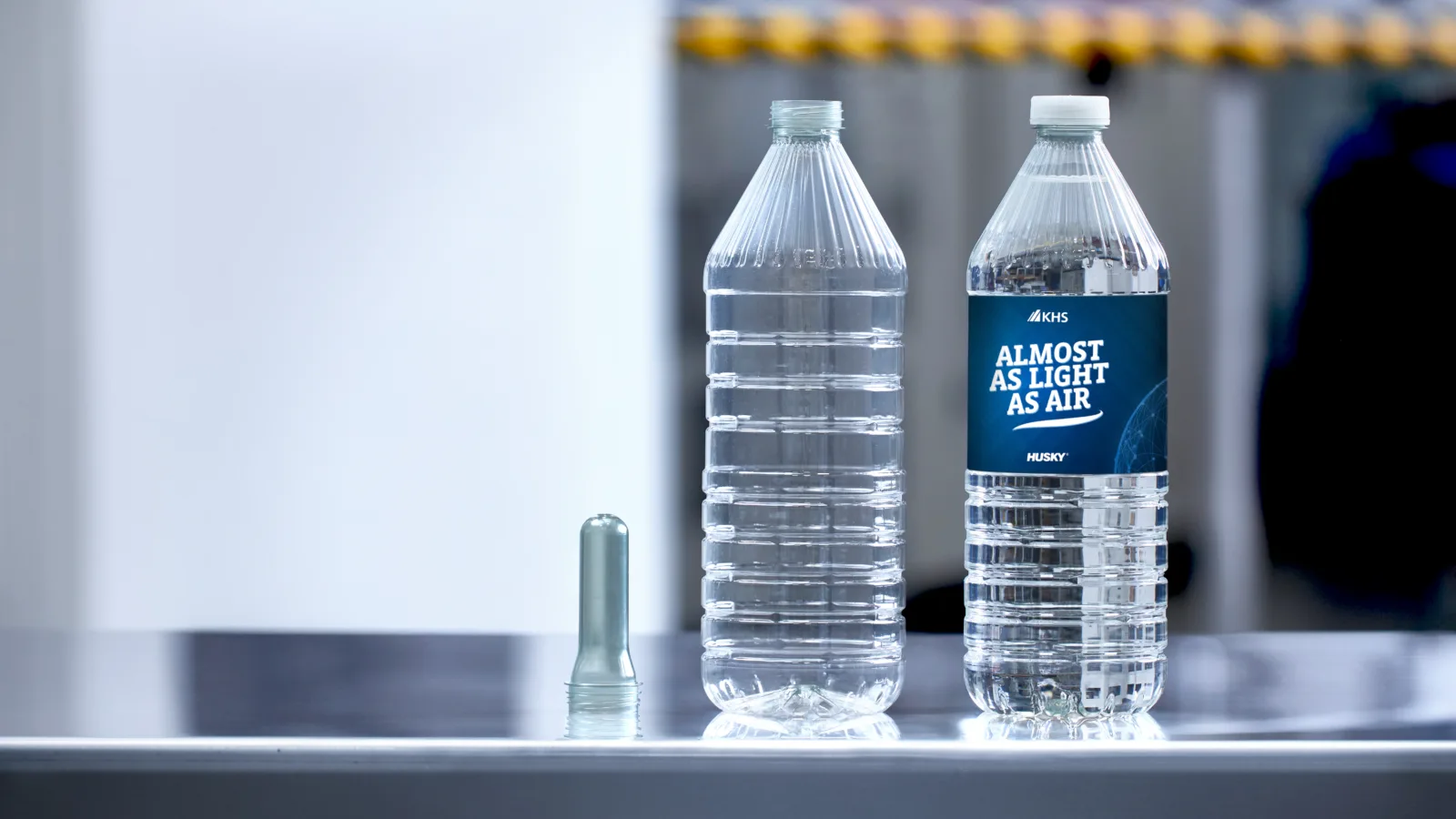
Menos es más
Una de las botellas de PET más ligeras del mundo para bebidas sin gas es fruto de la sinergia entre Husky Technologies, pionero en tecnología de moldeo por inyección y KHS, referente en diseño y fabricación de envases.
KHS está estableciendo nada menos que un nuevo punto de referencia con una de las botellas de PET para bebidas sin gas más ligeras del mundo hasta la fecha. En el marco del proyecto llamado “Faktor 101” y en estrecha colaboración con Husky proveedor y socio tecnológico con sede en Canadá, se ha diseñado un envase que combina un peso de solo 5,89 gramos con un volumen de 591 mililitros, equivalente al tamaño de 20 onzas, comúnmente utilizado en Estados Unidos.
Desarrollo orientado al mercado
Como estudio de viabilidad, KHS ha presentado el concepto Faktor 100 durante la drinktec 2017: una botella de PET con un peso aproximado de 5 gramos y una capacidad de 500 mililitros. Para el desarrollo posterior se realizaron numerosas optimizaciones, como explica Fabian Osterhold, desarrollador de packaging de KHS, en Hamburgo: “En casos de una reducción de peso tan extrema, la llamada resistencia a la carga vertical (topload) es especialmente importante. Este valor indica la resistencia de la botella frente a cargas verticales y determina si el recipiente es apilable y puede soportar el transporte sin sufrir daños“.
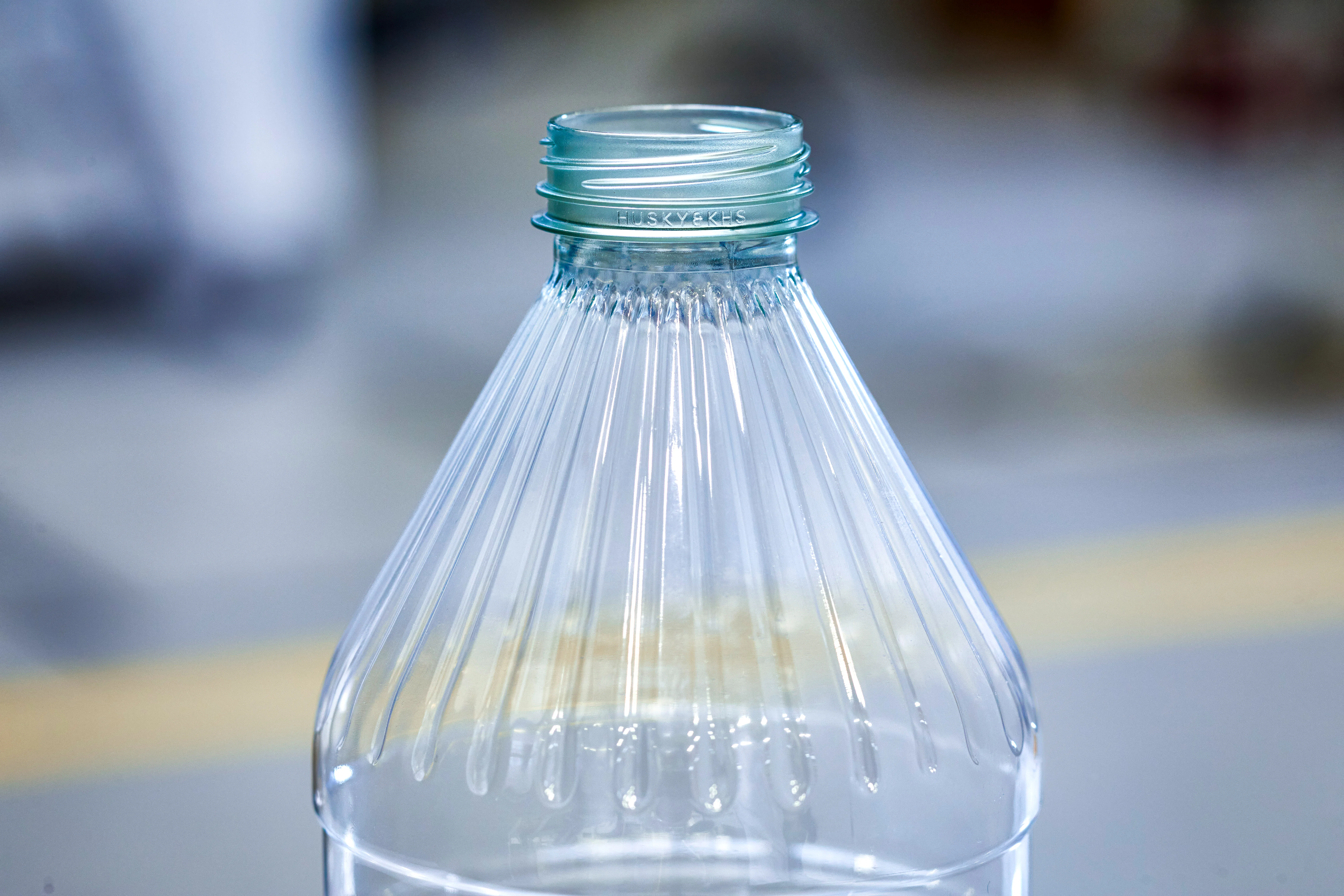
Para estabilizar la botella extremadamente ligera, su hombro se reforzó con nervaduras verticales, entre otras mejoras.
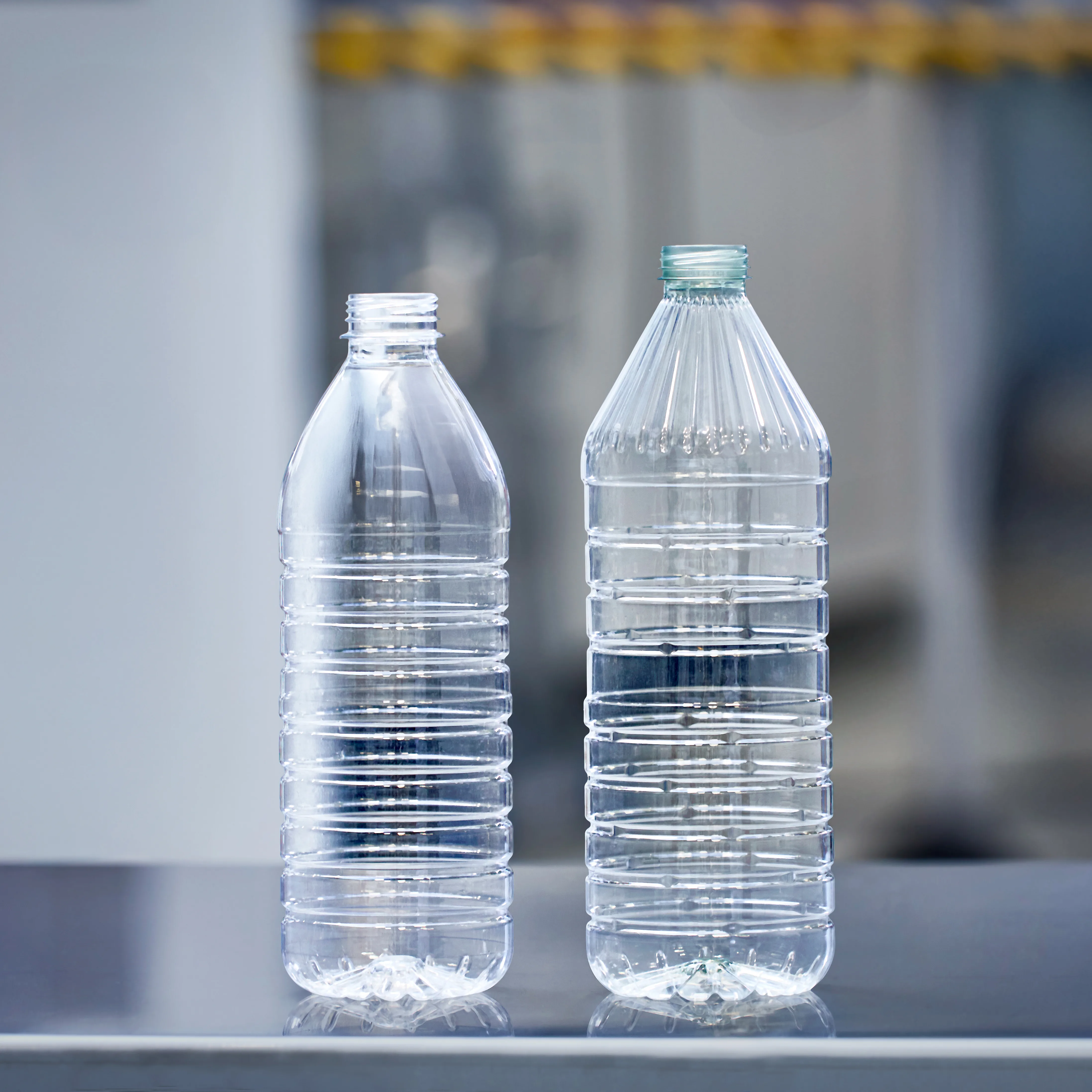
El modelo anterior, Faktor 100 (a la izquierda), lanzado en 2017, ha sido desarrollado con éxito hasta convertirse en el Faktor 101.
Ligereza con gran estabilidad
Para aumentar la estabilidad, se modificó el diseño de los hombros y se dotó al cuerpo de la botella con las nervaduras funcionales. Además, Osterhold y su equipo desarrollaron un diseño del fondo con un efecto de inserción hacia adentro (pop-in effect). Este diseño permite un hundimiento controlado del fondo bajo resistencia a la carga vertical (topload), incrementando así la presión interna y, con ello, la estabilidad de la botella.
El resultado es una resistencia a la carga vertical de más de 220 newtons, superando el valor estándar de 200 newtons comúnmente aceptado en la industria. Para alcanzar este alto valor de topload de 220 newtons en una botella de PET para agua sin gas, fue necesario más que un simple ajuste en el diseño del recipiente. “También fue necesario optimizar aún más el diseño de la preforma”, subraya Osterhold. Para ello, la empresa se asoció con los especialistas de Husky. Como líder mundial de sistemas y servicios de moldeo por inyección de preformas PET, la empresa dispone de una amplia experiencia y coopera con KHS desde hace muchos años.
“Lo más importante es el perfilado preciso de la preforma, que es posible gracias a la tecnología de KHS”
![]()
Desarrollador de packaging en KHS
Coordinación milimétrica
Desde el punto de vista técnico, el proceso se centra principalmente en los factores de estirado que transforman la preforma en botella, así como en las dimensiones resultantes de la preforma. En el moldeo por inyección, la relación entre la longitud y el grosor de las paredes es particularmente significativa. Mientras que KHS se centra en los requisitos y posibilidades de la máquina de moldeo por estirado-soplado y del diseño de la botella, Husky lleva a cabo las modificaciones necesarias en la preforma. “El elemento clave es el perfilado preciso de la preforma, un logro que solo es posible gracias a la tecnología de KHS”, explica Osterhold. En nuestra serie InnoPET Blomax V, los emisores lineales del horno garantizan una distribución de temperatura muy precisa justo debajo del collarín de la botella. Esto asegura que no quede ningún material sin estirar en esa área crítica. De este modo, se reduce el consumo de plástico de forma considerable”.
30 por ciento menos de material
En comparación con el envase estándar de PET ligero para 500 mililitros de agua sin gas, que en el mercado estadounidense suele pesar alrededor de 7 gramos, la solución desarrollada conjuntamente por KHS y Husky utiliza un 30 por ciento menos de material y puede producirse íntegramente con PET reciclado (rPET).
Sin embargo, entran más elementos en juego además de la geometría de la botella: “El mayor desafío es garantizar la capacidad de la línea en el rango de alta velocidad de hasta 90.000 botellas por hora”, explica Osterhold. “Los aspectos clave son el transporte, el etiquetado y el embalaje secundario. Por ejemplo, en el túnel de termocontracción es esencial prestar especial atención al diseño del hombro de la botella, mientras que, durante el transporte, se debe asegurar que el recipiente mantenga la estabilidad y no vuelque”.
Desarrollado en tiempo récord
“Además del peso, cabe destacar el tiempo en el que se llevó a cabo este proyecto”, señala Osterhold con satisfacción. “Gracias a la perfecta colaboración entre Husky y nosotros, así como al esfuerzo conjunto de las numerosas divisiones de KHS involucradas en el proceso de desarrollo, conseguimos finalizar el proyecto con éxito en tan solo cuatro meses, prácticamente en modo competición”, comenta Osterhold con una sonrisa.
Gran interés en el mercado
En mayo, el proyecto Faktor 101 se presentó por vez primera de manera tangible en la NPE 2024, organizada por Husky en Orlando, Florida. Allí, el diseño ultraligero despertó un gran interés en la industria. “En este formato, la botella es especialmente relevante para las embotelladoras por contrato, que operan bajo una fuerte presión de costes”, señala Osterhold. “Los mercados objetivo son principalmente Estados Unidos, Oriente Medio y Sudamérica.” Los primeros proyectos ya están en fase de preparación.
A NIVEL DE LOS OJOS
Intercambio intensivo
Frank Haesendonckx, Director de PET Tecnología de KHS, y Michael Müller, Director de herramientas PET de posventa en Husky Technologies, hablan sobre la estrecha colaboración entre sus dos empresas.
Haesendonckx: : el proyecto Faktor 101 representa un claro ejemplo de cómo integramos la experiencia de Husky en la fabricación de preformas con nuestra experiencia en el diseño y producción de botellas. El objetivo común es lograr un resultado de alta calidad, más eficiente y más ligero de lo que cualquiera de nosotros podría alcanzar por sí solo. Como suelo decir: 1 más 1 es, en nuestro caso, más que 2.
Müller: estamos convencidos de la ventaja que representa combinar y compartir nuestros conocimientos técnicos y aplicarlos de manera estratégica en futuros proyectos. Faktor 101 sirve de punto de partida para el debate de un programa de reducción de peso y mejora de las soluciones de envasado actuales.
Haesendonckx: nuestro objetivo es combinar una producción de preformas y botellas más rentable con un rendimiento mejorado, incluso más allá del proyecto Faktor 101.
Müller: compartimos una visión común y el propósito de desarrollar envases sostenibles.